I have a long gravel circle driveway. After 7 years, I am finally ready to have it paved with asphalt. I am getting bids on the job, but I am not sure of what makes for a good asphalt job. My main questions are: 1) how thick should it be 2) how can I judge the quality of the asphalt itself? My fear is that the lowest bid may be an inferior mix, etc.
Discussion Forum
Discussion Forum
Up Next
Video Shorts
Featured Story
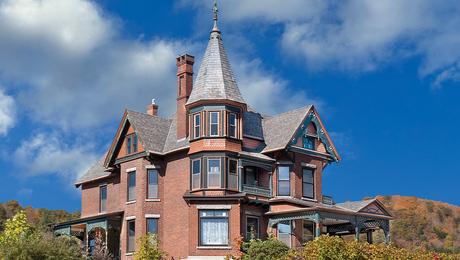
Fine Homebuilding's editorial director has some fun news to share.
Featured Video
Video: Build a Fireplace, Brick by BrickHighlights
"I have learned so much thanks to the searchable articles on the FHB website. I can confidently say that I expect to be a life-long subscriber." - M.K.
Replies
Like anything else, the quality of what you see on top is directly related to what is underneith.
Asphalt, as opposed to concrete, directly transfers the load straight down to the under layers (concrete spreads it around). It is very important to have a good foundation of compacted gravel as the foundation for the top layer of asphalt.
Rebuilding my home in Cypress, CA
Also a CRX fanatic!
Parenting has always been a mix of sage life advice and inexcusable laziness.
Thanks...very good advice. So asking about their grading and base prep is as important (or more important) than the actual materials.
1) how thick should it be
1 1/2" minimum inclusive of all coats. I like 2" for commercial applications, but I'm also in a climate that softens asphalt every afternoon for about three months of the year.
2) how can I judge the quality of the asphalt itself? My fear is that the lowest bid may be an inferior mix, etc.
Ah, from the happy references the contractor gives you from previous customers. If the contractor cannot give you references, you probably want a different one. Asphalt is all about the subgrade. There are some issues in the quality of the bithumen, and in the aggregate the bithumen coats--but the best "tar" and the best "gravel" won't fill in a wobbly pothole.
Since you have a long-standing gravel driveway, it's kind of a hard call (even beyond I'm just some words on a screen on the net <g>) to say whether it would be better if the contractor wants to tear out the existing drive to grade up "properly" or not. It may come down to how level, and how stable the existing drive is.
I don't usually butt into two way question/answer posts...I'm not Joemilw but I do have some experience in asphalt (on the consumer end, getting my driveway "paved") and a close friend who's been in freeway construction for 25 years.
For what it's worth: Asphalt is priced with the price of oil, the more oil costs the more asphalt is going to cost. With that said, the average cost(two estimates) for our driveway eight years ago was $134,000. Our drive was about 22 feet X 610 feet in size and after getting the estimates we opted for coating it with brine mix(Bittern) and grading it smooth. Since then, prices have gone up as you know. Expect to pay a minimum of about $14 to $18 a square foot, maybe more, for prep and asphalt placement (4 inch thick).
Lots and I do mean lots, of people around us opted for what's called "chip seal," it's completed in a day or two but it's cheap. The basic steps in this process are: grading the whole drive then a few truck loads of base are brought in and spread, graded and rolled/compacted. A layer of heavy bituminous oil is sprayed on top the rolled surface, another truck brings in a second layer of base material(small gravel like rock mixed with fines)and it's rolled a second time. Final coat is another sprayed on layer of heavy bituminous oil. The oil is allowed to dry for approximately two to three hours and the whole thing is rolled a final time. End product looks and feels like asphalt but believe me, it isn't. As you can imagine, this "chip seal" is only about 1/2 inch to 3/4 inch in thickness. Drive on it for three weeks or so and it begins to show wear and tear. One hot day and one car or truck turning it's wheels, without moving forward simultaneously, and you have the beginnings of serious deterioration. After four to five years of average use, the drive looked much as it did prior to paving, lots of plain ol dirt and gravel. Some sections looked in fair shape but other sections were nothing but gavel base with some significant holes. Re-oiling on a yearly basis certainly may have helped maintain the driveway but then some other alternative repair should have been attempted originally.
If you go for asphalt, get the true four or five inch thick hot mix application just as is done on our streets and highways. This is the only "asphalt" that truly holds up under driving conditions for a long period of time. The "chip seal" job uses a water base oil slurry of some sort that looks and feels like heavy oil but it is water soluble. Don't how that's possible, maybe it's a mixture of latex or similar material and water. Once it's dry however, it doesn't seem to breakdown with added water or heavy rain, just breakdown when when you drive on it.
your driveway cost over 100K?
Ha! Not in the final method that I chose, but yes it would have if I'd taken up the contractor's estimate. When I saw that it was going to cost over $100 K, I decided to pursue other options. In my view, the biggest problem is dust in the summer so I had the driveway graded, rolled/compacted and then sprayed with brine solution. The solution, known in the trade as Bittern, is the salt solution(brine) residue left behind from solar evaporative salt production. The cost was about $8,000 for grading and compaction then application of the brine solution. The brine solution is cheap and keeps the dust to a very minimum and seems to be effective for quite a long time. I've considered renting a small road grader, if there is one available, and practicing with it to cut cost potential in the future.
For $18/SF you could get stamped concrete. On a job as large as your driveway I could probably get the grading and concrete work done for about $40k, that's a turn key job.
Jon Blakemore RappahannockINC.com Fredericksburg, VA
The drive is 22 X 610 feet in length. That's 13,420 sq feet and at $18/ft2 that's $241,560. Even without stamping, just plain ol concrete 4" stuff, would require 163 yd2 of concrete. That works out to be about $32 K, minimum, before you factor in labor and placement. You must be making the concrete for free, how do you stay in business?
I'm not trying to say your price was off, I was just observing that I would be able to do a lot more than asphalt in my area for that kind of money.Concrete is $118/yd so 170 SY would be $20k, stone would be $4,800 for a 4" base, figure $4k for forms, stakes, wire mesh, and misc. items and you're still only at ~$28k.I would not expect a concrete sub to be on the job more than a week so that would be a gross profit of $2,400/day. Maybe it would be a little more expensive in this area than I am thinking, but I doubt it.The last driveway we paved was $4,800. I don't know the exact SF but it was at least 12' wide and 250' long. This comes to ~1.60/SF. If paving was as expensive here as you have to pay, I'm guessing everything would be concrete (unless that was much more as well).
Jon Blakemore RappahannockINC.com Fredericksburg, VA
Here in California, concrete delivered to the site is at least $200 / yrd. last I checked, about four years ago. I could be off but I'd bet it's at least that now or more. Wow, your costs are significantly lower. I think concrete was around $120 / yrd locally maybe 10 years ago at least. I'll bet with gas prices the way they are here, they must have tacked on at least an additional 5 to 10 dollars per yard just to transport so I'm thinking a ball park figure of around $225 to $250 a yard. Now I'm curious, I should give the concrete guys a call and see what concrete is these days. I let you know in the morning what I find.Here we pave our highways with combinations of concrete and asphalt. I'm sure they consider which is cheaper before choosing which one to use. Way back in the 40's and 50's they did a lot of highways in concrete sections about 20 feet X 20 feet. Today they are cupped so you get this constant thump thump as you travel down the road. About 15 years ago, they paved huge sections of highways with continuous pour concrete. Smooth as glass for the first few years then our earthquakes make it a bit less smooth. Lately though they've gone back to asphalt for highways which seem to hold up fairly well for 15 to 20 years of hard use, then they start to go south. I can't imagine what the cost is but many of our new sections of highway are 5 to 6 lanes wide and cover maybe ten mile sections at a clip and with oil at nearly $70 a barrel, we're talking some serious money.
More reasons for the "I'm glad I don't live in CA" file.
Jon Blakemore RappahannockINC.com Fredericksburg, VA
woodway,
Wow!
I get 5000 PSI pumpable concrete for around $130 a yard 3000 PSI would be less than $110 probably around $105. I'm in Minnesota right near the twin cities so It's not exactly the sticks..
Something people here have started using for a better surface is a Re-claim - old paving reground and mixed with ground up old tires reycled.
Welcome to the Taunton University of Knowledge FHB Campus at Breaktime. where ... Excellence is its own reward!
Yea, I've heard that's being done around here too. Seems like a good use for old tires if it works. Used tires are a big problem and their disposal is something we need to figure out. Huge pile of old tires caught fire here a couple years ago and it created a lot of pollution, both air and ground. It took a couple months to extinguish.
>> Expect to pay a minimum of about $14 to $18 a square foot, maybe more, for prep and asphalt placement (4 inch thick). <<
Not sure of the cost of asphalt but here I get turn key concrete for around $3 a sq ft. Like overbudget said, maybe add in 1$ for grading and gravel. BTW - 3000 PSI concrete is $101 a yard here (current price).
Based on the cost of living you have to deal with, I hope you make at least $1/2 mil a year... or maybe you live a remote area where certain things are very expensive?
Edited 7/4/2007 9:53 am ET by Matt
Cost of living here is a significant factor, without question. There are two main groups, those who bought property 15 or more years ago and those trying to buy in within the last two to three years. I'm in the born-in-the-area crowd, thank god otherwise I couldn't live here either. With property taxes and living costs locally, the ones buying in the metro areas around SF are primarily techies or two income families for sure. Quite a few Google employees for instance, who started with the company when it was founded back in 1998-1999 or so, are now retired. All others need not apply, or even consider it, which is a big problem the way I see it. Mega-loads of people are doing the commute to work thing with one way trips as far as 50 to 75 miles, just so they can buy a first home.
I had an existing drive way that had 3-4 inches added - 5+ in a couple of spots -- 4000 sf and it cost 13,800 and another 1500 to seal after 30 days -- what as said earlier about a proper base is the most important -- have the base as thick as you can go - 6-8 inches and then top off with 3-4 inches of asphalt
learningmore,
A driveways durability is determined by the density of the pack and it's preperation..
Do not accept less than 4 inches of subsurface preperation.. that is 4 inches finished.. do it in two lifts.. (a lift is when they compact things) the size of the compactor and it's vibration frequency and impact force determine the quailty of compaction.. Most driveway guys have little tiny compactors, they do a poor job. a lot never even ballast the drums on site..
Use crushed rock or class 5 as a base. pack it in two lifts (not one the way most driveway guys want to) .. then decide on the heaviest load you'll have on the driveway. light little cars and if you're willing to redo it every decade a couple of inches is enough. (that's after compaction) 4 inches will allow an occasional bigger delivery truck onto it as long as the ground underneath isn't wet clay
Speaking of clay if that is present you need to increase the base even more unless you like frost heaving things around. and finally where you are located in the country will determine exactly what a proper driveway calls for..
Like most things a low bid gets the cheapest level of work but the high bid doesn't mean you'll get the best.. details.. it's the details that count!
In some areas tiling under the drive may be necessary to keep it dry.The size of the crushed rock used under the drive is major factor in determining the weight it can carry -- large pieces distribute the weight more broadly.
So convenient a thing it is to be a reasonable Creature, since it enables one to find or make a Reason for everything one has a mind to do. --Benjamin Franklin
Hi DanH
What is tiling under a drive?
Mike D
Installing drainage tile to give the water someplace to go.
Welcome to the Taunton University of Knowledge FHB Campus at Breaktime. where ... Excellence is its own reward!
Drain tile, run to daylight.
So convenient a thing it is to be a reasonable Creature, since it enables one to find or make a Reason for everything one has a mind to do. --Benjamin Franklin
as is being discuss in this thread,also check on concrete,lay it and forget it for 30 years. here for a driveway you could figure a 1.00 a foot to grade and 3.00 a foot for concrte and labor on a driveway with no power trowel. larry
hand me the chainsaw, i need to trim the casing just a hair.
alot of good information already given.... beware alot of jackleg asphalt guys out there...ALOT.... seems to attract them mostly gypsies around here... new trucks... small f350 type dumps small 1ton rollers and usually use a dragbox spreader if they even have that...
base is way important.... sometimes very cost effective to use a barrier type material that helps spread the load and bind the under surface... (looks alot like the fabric that keeps weeds out of your garden)
edges on a drive need to be contained... steel.. concrete something besides asphalt... asphalt edges will not hold up...
asphalt is really better for a well used road than it is for a private drive... the constant compacting helps...
2 1.5" lifts on a private drive is a good job (1.5 before compacting) the contractor should have a spreader box as wide as the drive so you'll have no seams...
the more they compact the better... not only for looks but keeps moisture out... smooth tight compaction is good... "if it looks porious it is" (thats bad)
pretty sure the trade mag for paving has a website "paving today" you might find some info there... i never looked but I'm sure there is an asphalt forum... might be worth a visit...
the good asphalt guys out there hate nothing more than the bad guys out there... find a good one...
good luck
p
I am suprised that so faar nobody has asked you the most important questions:
What part of the country are you in? You might have noticed that the responces from down south mention up to two inches thick, while thoise from up north mention four inches as a minimum.
Highways in the south are far cheaper to maintain. of course, there is no plowing in their budgets, but allso, no frost heaving.
The other Q has to do with your existing base. Somehow, I am getting the impression that you are thinking you can just pave over what you have now. That is certainly possible, but depends...and so does the life of the end product depend on the prep work, as with painting.
I don't know if your existing is a decent base with sound mineral fill, well compacted from years of use and well drained - or if it turns to mud and ruts every spring.
If the latter, you really need to build the base up first, ideally about 18" with geotextile worked in. once you have a decent base that is drained and compacted and will not move around and squirt out from under the paving under a load, then you might get buy with 2" of paving in the south.
Up here, I would be looking for a good base first as mentioned, then a two ply spread. 2" first, then 1" finish.
Welcome to the
Taunton University of Knowledge FHB Campus at Breaktime.
where ...
Excellence is its own reward!
Asphalt in my area is usually about 2" thick. The key however is in the base. 18" of base is ideal. After the dig out and stone brought in a waiting period of about a week to allow the stone to compact naturally is preferred. Otherwise you end up with sinking. I have seen longer periods up to three weeks because the right compaction hadn't been achieved.
There are also different grades of asphalt. Typically it is the cheapest stuff that is offered to customers in an effort to be competitive with other paving companies. If you want a better grade of asphalt ask for pricing and examples of were it was used so that you can go have a look.
My best friend owns a paving company. That is the only reason I know any of this stuff.
Dave
Just how does compaction happen naturally in a week? You got magnetic stone up there?. Usually takes machinery to compact fill
Welcome to the Taunton University of Knowledge FHB Campus at Breaktime. where ... Excellence is its own reward!
Piffin, Piffin, Piffin.You invite all your friends who have heavy vehicles over for a barbecue and agree to feed them all for a week if they'll just drive up and down your driveway (for a week).That's how we did ours. :)Mike D
gravity i guess. It's alot of stone. A little water helps too. before paving they will go over it with the compactor. I guess this will let them know if there is any soft spots in the driveway.
"before paving they will go over it with the compactor. "There ya go! All gravity does is help transfer the load from the truck to the ground.;)
Welcome to the Taunton University of Knowledge FHB Campus at Breaktime. where ... Excellence is its own reward!
If you were going to ask for a higher grade asphalt, what would you ask for? I.e., if there are grades of asphalt, what are they?
Mike D
Hey Mike,
I gave my buddy a call regarding the asphalt paving grades for you. He was happy to help. They are as follows.
1. DM (Drivway mix) - This is your most commonly asphalt used for driveways. It has a very fine stone and has a more sandier consistancy. It gives a much smoother more esthetically pleasing finish but doesn't have alot of strength. Over time ruts may form from the wieght of vehicals. On hot days a bicycle kick stand will sink into it.
2. HL3-Fine - This has a coarser stone and is much stronger than the DM. It doesn't have as smooth a finish. It's good if the home owner is parking a large truck in the driveway.
3. HL3 - A bigger stone again used in this mix. Very strong. A bit on the ugly side.
4. HL8 (Base Coat) - This mix has a large stone, very strong, looks like crap. (his words) This mix is primarily used on roads/highways.
His suggestion to you is go with the HL3-Fine at 2 1/2" thick. After 2 1/2 years seal it. Not before. The sealant will fill all the little nooks and cranny's.
Hope that helps.
Dave
Thanks Dave,
That's such a good summary, I've printed it out and saved it.
Mike D
What people call various mixes vary by locality.
Worry about gradation and asphalt content, not the name.
My first look would be the city/county engineer's office and see what specs they use. Many areas have area standard specifications for roadway improvements. See if they have a standard section for local, low traffic, roadways.
In closing, roadway prism, and pavement design is kind of a black art. I had a professor when I was in college who had published several papers on asphalt pavement mix designs and durability. I once referred to him as an expert on pavements. He gave me a horrified look, and said that there are no experts, on pavements. Only someone who is young and inexperienced would ever claim to be an expert.
Wow, a lot of good information, some misunderstandings, a few assumptions with a few huhs thrown in!
Please pull up a chair, grab a cold beer, and enjoy. And this isn't even the Tavern!
Lets start off with the basics. The structural design of asphalt is based upon the subgrade. If the subgrade is silt and/or clay, it is recommended that this material be removed and replaced with structural backfill. The backfill is then compacted ideally in 6" lifts to 95% Proctor density*. If you are in a bog or similar conditions with clay or silt, geotextiles would be required. There are ways to test these conditions, but this would require soils borings and a geotechical report. Which is a little overkill for a residential driveway.
For base course on a residential driveway, 4" of 5/8 minus crushed gravel will suffice. For the base course, you want to maintain the drainage around it so that water doesn't get into it and cause frost heave. That is the biggest issue with base course material. And make sure you compact the heck out the the base. Again, 95% Proctor is the way to go.
For the wearing surface, 1-1/2" of a 3/4" minus gradation asphalt will provide you with the greatest structural capacity for a road, although 5/8" or 1/2" will make the the road tighter in appearance. With the smaller size of aggregate, rutting becomes possible, but it would be a rather long time. I mean over 10+ years. The size of asphalt aggregate really depends on what the local asphalt plants have as their standard mixes. These mixes usually follow what the states specify which the counties and cities follow generally, <rant on> unless you are the moronic COE. Long story, but idiots all the same. <rant of> The mixes are based on Marshall testing with 5 specific test taken to measure density, stability, air voids, flow and volume of voids. From these five test, the optimum value for asphalt content is selected. in a nutshell, if you have too much rutting, the asphalt content is too high, especially during high temps. If you have aggregate raveling, the content is too low. Edges are special or not depending on your pocketbook. If you just place asphalt over base course, you have what is called an unconstrained edge, which means that the density of the asphalt lessens as you go out to the edge. In other words, when the compactor rolls over the asphalt, the asphalt material is squished out towards the edge. If you had a ways, such as a concrete curb or a hot joint (another lane of hot asphalt) to contain the asphalt, you would have full compaction. Now the ways to test compaction of the asphalt is usually to either core drill a section (old way) or use a nuclear gauge to test density. But we are back at the residential driveway..... Best way to do this is to make sure the asphalt material is delivered to the site from 325-350 degrees and is well compacted.
Side note: As long as you don't have over 10,000 18,000 pound axle loading on your road, the Asphalt Handbook actually recommends 1". Trust me, go with 1-1/2".
Now for the issue about asphalt concrete(AC) versus Portland concrete cement (PCC). AC virtue is that it is flexible, whereas PCC is rather stiff, thus on a moving subgrade, the PCC is not ideal But then again, PCC has longevity versus AC. When it comes down to installation, AC is quicker to install, and you can have traffic on it in 2-4 hours. With PCC, you have form work, doweling, etc, as well as a curing period. With AC, over time, the asphalt will degrade, but this is dependent on variables such as the freeze/thaw cycles and vehicle loading. And with PCC, over time, concrete can spawl, joints can get damaged, and the aggregate can ravel. There are trades offs with each material. What the local DOTs really determine is what is ideal for the situation such as availability, cost, labor availability, material availability, and yes, the price of oil.
What LearningMore needs to do is decide what he wants in a final product as far as look, cost, and maintenance. And yes, it would be nice to get location specifics.
*Proctor test determines the optimum water content for which the soil can be compacted optimally. Too much or too little water leaves too many voids in the soil, which can affect performance of structural/base material.
Leland... PE
Will someone kick Piffin, me thinks he fell asleep. :DConcentrated power has always been the enemy of liberty. -- Ronald Reagan
" kick Piffin, me thinks he fell asleep. :D"Hey, I said what I had to say! Then I shut up.Glad you put in about compaction in lifts. Skipping that is the most rediculous mistake made to create ruts
Welcome to the Taunton University of Knowledge FHB Campus at Breaktime. where ... Excellence is its own reward!
Ya better be careful. If people realize you actually know what you're talkin' about, they will come to expect it from you all the time.
LOL
Dave
what is compaction again?
LOL
Hummm. After that expert explanation, I almost fear to ask the following question.First, some background.....
When our asphalt drive was being re-done .. oh, yes ...Location .... Louisville, KY, 60 year old sub-division, minimal backfill 60 years ago, primarily clay soil - old potato fields according to the old timers here.Anyway, the contractor dug up the old asphalt driveway and 8 inches of old gravel and dirt and filled it with 8 inches of new, compacted crushed stone (I park a vehicle with a 12,000 lb axle on it). But, as he compacted it (in about 2 inch lifts), the surface began to move ahead of the rolling, vibrating compacting machine in waves - a good two inch vertical deflection - occurring over about half the length of an 80 foot driveway - very impressive to see. As they continued to compact the stone, the surface became down right fluid in places - you could actually cause it to swell up around your boot just by walking on it (darn!).The contractor called it "clay pumping", and said that it isn't that unusual around Louisville. He solved the problem in two steps.1. He stopped, and waited for two weeks for the "soil to stabilize" before continuing (I think that another job was calling, but hey, that's just me). I drove on it for the 2 weeks, marking out the scarier parts with a spray can so that I could observe them more easily. One didn't actually sink into the spots - they just moved under wheel or foot. That actually did improve over the two weeks, until only the marked "holes" moved when disturbed with a wheel.2. After two weeks, he came back, dug out the semi-fluid spots I'd marked (some now showing clay discoloration) with a backhoe and filled them with more crushed stone, compacted that, and then paved the whole shebang with 2-3 inches of asphalt. I was inconveniently out of town that day, so I didn't see if the movement ahead of the compactor improved or not. However, he did a great looking job, and it doesn't move ahead of my big vehicle, so I guess it's ok.That was 3 months ago, and is holding up fine - - no rutting, potholing, no move wave motion in front of the wheels, etc.FINALLY, my question.
What would cause formerly solid ground, that has shown no previous swamp-like tendencies, to go semi-fluid like that under the load of the vibrating, rolling compacting machine? And, (now that it's way too late to do anything about it, but for future reference), should I have revised my spec, mid job, and required geotextile stabilization under the gravel? (Not that I knew about geotextile at that point.).Mike D
Vibration will "fluidize" certain soils. A major problem in some earthquake areas. Left undisturbed the soils will eventually "set" again, but such soil is clearly unstable/unrerliable.
So convenient a thing it is to be a reasonable Creature, since it enables one to find or make a Reason for everything one has a mind to do. --Benjamin Franklin
Warning - thread digression ahead:
I believe the technical term for that effect is "Liquifaction".
(Saw some show on engineering bridge uprights. The guy did an example on the beach at low tide by driving in some rebar about a foot and leaveing 3' above. he then danced around it on his bare feet and you could see the water rising up around the rebar until it fell over. Who says that TV watching is bad for you?)
Yeah, you're right -- "fluidize" is a slightly different concept.
So convenient a thing it is to be a reasonable Creature, since it enables one to find or make a Reason for everything one has a mind to do. --Benjamin Franklin
Don't start dancing around your TV now!;)
Welcome to the Taunton University of Knowledge FHB Campus at Breaktime. where ... Excellence is its own reward!
That is one of the reasons for the geotextile.We get something similar in the spring. The top 12" or 18" is thawed while the ice lens in still solid down under so the water in the clay is floating things. You can jump on a spot and it will sink an inch while five or six feet around you it swells up.Clays hold water , some of them for a long time. He was right to just hold off and let it dry and stabilize for awhile. Vibrations bring water up towards the surface. More vibrating might have just meant that he would have had to keep bringing more stone to pound in two feet deep.
Welcome to the Taunton University of Knowledge FHB Campus at Breaktime. where ... Excellence is its own reward!
Mike-D,
As other have said, "Liquefying " of the soil. Think "Quick Sand" It occurs from water table being high and having soils that don't drain. The phenomena occurs here where I live quite frequently. Using drain matting, subsurface drainage to lead the water away from the driveway will cure the problem unless you have "seeps" or "springs" directly under the roadway. If the water problem is bad enough no amount of rock , placed however deep you want will help in the long run. The aggregate will always sink into the soils as it "liquefies" and eventually disappear from under the roadbed.The fabric prevents the aggregate from settling further and further down. I have seen roadways where the fabric was damaged either upon install or as a result of trenching after the roadway was finished and the area that has the damaged fabric will always cause problems.
"Poor is not the person who has too little, but the person who craves more."...Seneca
the "liquidation" is also known as pumping. It is when the moisture content starts replacing the soil particles. The soil cannot handle the excess moisture and the moisture act like a lubricate and the particle starts moving under loads. This is a non compacted area and need to either be dried out or replace with lower moisture soil. It can also be replace with a material that can handle the excess moisture as in rock, gravel, or sand.Clays have very low moisture temperaments, some clays will swell with excess moisture.When a material starts pumping your compaction is usually around 70%, that mean when the soil finally dries out, you will have close to 25% voids. Settlement will happen.
Thanks for all the replies. Verry educational.I am pleased with the job that I got - the contractor and his guys have a good reputation in the area, were on time, pleasant to work with, didn't stick me with a cost overrun, answered all my (sometimes stupid) questions, and completed a very nice, professional looking job that does, in fact, support my light and heavy vehicles. Even better, my wife likes the way it looks.Mike D :)
Mike D, make sure you have a drainage ditch adjacent to the roadway to keep the base course (gravel) well drained. This will increase the longevity of the road.
That is one heavy vehicle you have. And that is just one axle?
If you have time, check out the Kentucky DOT site. Here is their design guide if you want some interesting reading: http://transportation.ky.gov/design/pavedesign/docs/DesignGuideUpdate2-2007.pdf
Okay.... it is interesting to me to see how each DOT sets guidelines for their specific conditions. :)
Government exists to protect us from each other. Where government has gone beyond its limits is in deciding to protect us from ourselves. -- Ronald Reagan
Yep, a drainage ditch would be a good thing. The problem is that the grading of the property takes the natural flow onto my neighbor's yard instead of onto a public drainage. I like the neighbor, so I'd better not do that - he also has a full basement about where the storm drainage would come out. The vehicle is heavy - the front axle is rated for 12,000 pounds and the rear axle is rated for 20,000. I don't load it that heavily, but the potential for is there. That is an interesting site that you referred me to, although it includes more technical detail than I'll carefully read, now that my immediate project is completed. However, if the drive gets in trouble down the road (so to speak), it'll be a good starting point for defining effective remedial action.Thanks for taking the time to educate me.Best Regards,Mike D
No, quick sand is fluidization, not liquefaction -- the suspension of solid particles in a fluid so that they take on the aspects of a fluid. Requires that water (or other fluid) be driven up through the particles, and the effect stops as soon as the water flow stops.Liquefaction, OTOH, is the temporary breaking of bonds that bind a solid, so that it becomes more liquid. Generally the presence of water is a factor, but the action comes from some mechanical effect that breaks the bonds.You see the effect when you stir premixed drywall mud -- it gets less stiff/more fluid.
So convenient a thing it is to be a reasonable Creature, since it enables one to find or make a Reason for everything one has a mind to do. --Benjamin Franklin
(But in either case draining away the water helps.)
So convenient a thing it is to be a reasonable Creature, since it enables one to find or make a Reason for everything one has a mind to do. --Benjamin Franklin