*
I am re-creating architect and author (and Fine Homebuilder column writer) Sarah Susanka’s “Not So Big House.” In the dining nook corner, the plans call for a threesome of casement windows at each corner elevation, tightly packed into the corner. The casements are separately-framed, not factory-mulled. Wall framing is 2×6. The prints show the first rough opening 6 inches off the outside stud wall corner in each direction, then each rough opening separated by 3-1/2″ (three and one half inches). I have got creative framers, but how does one construct a stud corner and get trimmer studs supporting a header, with a six-inch corner dimension? Email addresses in responses would be appreciated, thus we can trade sketches.
Discussion Forum
Discussion Forum
Up Next
Video Shorts
Featured Story
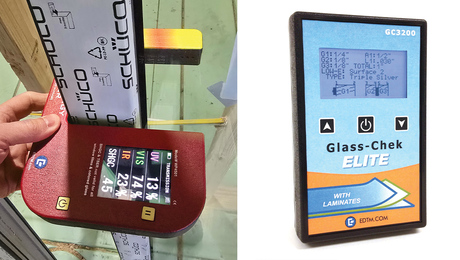
New devices showcased at the Builders' Show make it easy to measure glass performance, u-factor, SHGC, window thickness, and more.
Featured Video
Video: Build a Fireplace, Brick by BrickHighlights
"I have learned so much thanks to the searchable articles on the FHB website. I can confidently say that I expect to be a life-long subscriber." - M.K.
Fine Homebuilding Magazine
- Home Group
- Antique Trader
- Arts & Crafts Homes
- Bank Note Reporter
- Cabin Life
- Cuisine at Home
- Fine Gardening
- Fine Woodworking
- Green Building Advisor
- Garden Gate
- Horticulture
- Keep Craft Alive
- Log Home Living
- Military Trader/Vehicles
- Numismatic News
- Numismaster
- Old Cars Weekly
- Old House Journal
- Period Homes
- Popular Woodworking
- Script
- ShopNotes
- Sports Collectors Digest
- Threads
- Timber Home Living
- Traditional Building
- Woodsmith
- World Coin News
- Writer's Digest
Replies
*
I think I figured it out myself. How does this look to all you veteran framers?
*How about this?
*How about it? What's a .tcw file?
*My first thought would be to frame the corner in place, that is, frame the walls lying down normally but only to the first window from the corner, stand up the walls and then build the corner. I'd make the corner solid, laminating it up out of a 2 x 6, a 2 x 6, a piece of 5 1/2" 5/4 decking and a final 2 x 6. The final 2 x 6 would be the jack for the window on one wall. The header for the window on the other wall could be notched in in a matter of minutes. Ron
*I'd lace the two headers at the corner and put a 3 1/2" steel column under it. That's what we've done before, and it works great.Ed. Williams
*The corner is a built up trimmer. Four 2x6 (6 inches), faced on one side with 1/2 to make 6" the other side. Trimmer (corner post) height is stud height less header width. Assuming a double 2x header, this bears on the post 3" from f.o. framing, leaving 3" bearing for the other header coming in 90 degrees the other way. Frame down for window height. This allows the header to be faced nailed from the top plate. The first wall can be framed down with header installed, then the other wall will need the header installed after standing. Set the double plates so the second wall will lap over the first at the corner. You will leave at least the first four feet of this plate off before standing. After standing, install the second header. Then face nail the top plate into the second header. Then install the double plate, lapped over the first corner.I usually add two 24" c.s. straps on the outside of the headers (don't fall), tieing (sp?) the corners together at the headers.
*Gene, It sounds like you are attempting to set the windows tight together at the interior jamb, without leaving any space for casing? It sounds odd, but since I'm not privvy to the overall interior trim scheme, I'll just go along with the program.Your 2x6 stud, with a half inch sheathing will give you the six inch setback from corner. That means that all your header bearing will have to be buried in the corner. Since you are using casements, seperately framed, I'm assuming that you will have a header under 48"...probably around 30". That is usually a very small load to consider.I'd simply run two 2x's tight all the way to the corner on the first wall. That will automatically leave a 2 1/2" pocket to bury the intersecting header into. I'd install three 2x6 studs under as "trimmers", but really they'd all be buried in the corner. If you are serious about energy, then install only two with insulation filling the void.bluePs. i just reread Nathan's post. I think we are thinking along the same wave length. The only difference is i like to save studs.
*Psst Gene, If you want to simplfy the corner post, just purchase a 6x6!blue
*Sorry, I was figuring from the inside corner.
*Blue, it sounds like you were able to see my sketch. My windows have rough openings 29 inches wide. In the concept I hallucinated, the header (twin 2x6s???) bears on only the 1/2-inch "trimmers." Is this too risky, bearing only that little? If it is, we (I mean me, I will do it in my shop so as not to aggravate the framers) can cut mortise notches in the post faces for the headers to gain some more bearing. The inside face headers will be mitered if we do this. And yes, we are trimming without casing at that corner. One jamb extension will lap over the other.
*Think I got the idea of what you're doing. Wouldn't the easiest way be to take Blues suggestion and set a 6x6 post under a continues mitered header? Add 1/2 ply to the sides of the post and you should have your numbers. BY 45ing the header you should have plenty of bearing.
*Forget about supporting the headers at all.We often built corner windows in New Zealand without any mullions..just glass meeting glass and silicone joint.We would cantilever our headers from both directions, ( obviously the unsupported end of the header is shorter than the supported end. To assist combating uplift and tie down we ran 1/2 inch booker rods plate to plate through the headers.This will allow you to bring both windows tight together. ( just how creative are your framers?)kind regardsmark
*My second thought is I'd do it Ed Williams' way.Ron
*(reply to #13)Way to go Digger!!!I forgot all about that. We built a Frank Lloyd Wright School designed house about eight years ago, (framing, trim and cabinets) and that's exactly what we did. Boy, I seem to forget more than I learn. Good show.Ed.
*marcwhat are booker rods run plate to plate?if they are all-thread, ready rod, through the header at the corner, how is rod to the floor above adding any resistance to settling and deflection? if they are at the other end of the beam, what could they be adding to the rotation equation that is not already overcome by installation to floor or wall?Would you feel confident framing a decent-size hip on one of your corners?Just poking for more info on your technique. A large condo had many corner windows like you describe, and we lost corners due to eventual sagging, some cracking of glass...6x12 was in the floor, reverse crowned. These were 3-0,4-0,5-0, and glazed after stucco. We thought we were bullet-proof.I bet a creative framer could find a way to install this header, and then tension it in some creative fashion, after the load is on it.I recently framed some corners like the title post called out. I thought they looked good when finished. Framed them the blue and me too way. nice and clean. Need to have a framer who cares build them. But you definitely don't i needto have routers and shop time involved. Do this in the field.
*Hello NathanMy scanner's karked it at the moment or I could send a pic of one in particular...it had corner glass one end of the wall, and curved glass brick wall the other end...this meant the header was continuous the length of the wall. ( bit of a pig to stand as the thing was almost balancing on the studs as we could only toenail them )booker rod = threaded rod yes..we use it all the time here for our cyclone codes.. ( average home would have between 60 and 100 in it.)In the case of a cantilever the rods aren't for at the corner..rather at the support ends of the header...helps to combat the see-saw effect...the job mentioned above had a hip falling on each corner and it was a concrete tile roof, if your're worried about weight.All said and done though if you're flighty about sag or don't want to pay an engineer to crunch the numbers go for the steel post and be done with.latermark
*Mark,since yours' is down, how about enlightening me on how to attach one of my scans to a post as a link. Mac os9
*Mate..I'm a bit of a ninny...but scan it and save as a JPEG..you should then be able to upload it by clicking on the Attachments Browse button at the bottom of the Reply box.
*
I am re-creating architect and author (and Fine Homebuilder column writer) Sarah Susanka's "Not So Big House." In the dining nook corner, the plans call for a threesome of casement windows at each corner elevation, tightly packed into the corner. The casements are separately-framed, not factory-mulled. Wall framing is 2x6. The prints show the first rough opening 6 inches off the outside stud wall corner in each direction, then each rough opening separated by 3-1/2" (three and one half inches). I have got creative framers, but how does one construct a stud corner and get trimmer studs supporting a header, with a six-inch corner dimension? Email addresses in responses would be appreciated, thus we can trade sketches.