Hey All, I`ve enjoyed reading your threads over the last couple of weeks and have learned alot. I`m trying to figure costs of a septic system for a new home. Any ball park guestimates out there? I`m in the Northeast. House is 36’x24′. 2 bath and laundry. Also, cost for a Well? Thanks for all responses.
Discussion Forum
Discussion Forum
Up Next
Video Shorts
Featured Story
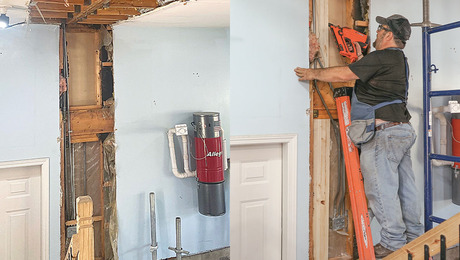
Don't buy in to the TV show nightmares—when you uncover something unforeseen on a remodeling project, take these steps to keep the process moving and fix the issue.
Featured Video
Video: Build a Fireplace, Brick by BrickHighlights
"I have learned so much thanks to the searchable articles on the FHB website. I can confidently say that I expect to be a life-long subscriber." - M.K.
Replies
There's a thread going about cost for a garage slab that has brought in estimates from five to ten thousand and up.
Yours will have an even wider range but the discussion will be enlightening! The type of soil you are on now and the system the designer employs will have a lot to do with cost as will the cost of washed stone in your area.
I live on an island where all gravel (we don't have anything but clay and ledge) needs to come by ferry so it costs more than three times aas much as on the mainland and since we have nothing but clay to build on, it takes more gravel to build a system than other places. Additionally, we have a sole source aquifer, meaning that nobody wants anybody to pollute the groundwater so many systems get overdesigned.
If you were here, it would be around twenty thousand for the waste water system.
The well would be twelve dollars a foot to drill and another twelve for the casing plus sometimes a setup charge for ferry fees etc.
Depth of well is anywhere from fourty feet to four hundred.
Good idea to get a dowser to wander around.
Excellence is its own reward!
Thanks for the input. What do you mean "dowser"?
To dowse for water is to use an age old method whereby a gifted person lets a willow branch or alder branch in his hands tell him where the water lies. Some consider it mystical, some hogwash, others find scientific validity in the theories.
Our tanks run about a thousand, Washed gravel is 28 to 40 bucks a yard, excavators at $55 to 85, depending who....
Excellence is its own reward!
I`ve heard of that before. Interesting, But my vote would be for hogwash....At what point in the costruction process does the well need to be drilled? Can it wait untill after the shell is built or does it make sense to drill before construction?
Find the water first. Unless you want to move the shell to where the waters after you find it 4 miles from the site.
You might want to find out if land can handle a septic system also if it drains to fast the state may require you replace all the ground with enough clay and dirt to fill a small gravel pit.
the water table you will also need to know how high that is. You may find you have to the septic system above that also.
Edited 1/22/2003 5:05:36 PM ET by fredsmart
MINE WAS $1200
I doused my well, and several others, and I am hardly gifted and use any old wire. Everybody I've shown could do it too. When I showed our well driller where I wanted ours, he liked the spot and hit 20 gallons a min. at 185'. Some people go 500' around here and don't even get a gallon a min. Anyway, the well cost $1900 three years ago. $8' drilling, 42' of casing @$7'.
Septic was different story. $6200 for a special pump up the hill infiltration system. No gravel in the drain lines, 1200 gal septic tank, 1200 gal pump tank, poop pump w/ control floats and control box, 200' of 2" trenched pvc supply to a 5 line manifold w/ valves, to 360' of special infiltrator drain line. A traditional gravity system would have cost $2400. Central high priced North Carolina. But then again, maybe it's not so high priced here... EliphIno!
Like fres said, it's a pretty good idea to know where things are going to be before you get too far along. You need the raod/driveway base for the drillers rig to get in on. You need a septic designed and permitted at whatever distance your loical ordinances require away from the well, etc.
I get the waste water design first because we have limited locations where that is possible. Some places, you can put it almost anywhere on the lot. It depends on your soils. So get the soils guy to design that first.
Then keep in mind where you would like your house to be and find a place for the well that is convenient to it and the right distance from the waste system.
"my vote would be for hogwash."
Well, I have done it. I ignorantly drilled my own home without dowsing and got a meager three gallons a minute at 177 feet. After that, a guy showed me how. I'm not all that gifted but I can find underground water lines more accurately then instruments can. I have dowsed water that cam in at over 80 GPM at 140' depth, it was a river of good stuff. The twitches were unmistakable!
.
Excellence is its own reward!
drill the well first.... around here about $10 /ft...then $1500 or so for the pump system
septic can go $30 K to $40K for even two bedroom.... course that's cause all the good lots are gone and only the problem ones remain....
the last really good lot was sold by the indians to a bunch of guys from newport that wanted to graze sheep on the island...... at that price, they bought the whole thingMike Smith Rhode Island : Design / Build / Repair / Restore
I don't know how you dowser dudes do it. I watched a plumber pace around a house with some wire in his hands to try to find water pipes in the joist spaces, man , that dude couldn't find doodly squat.
Eastern PA
Septic systems are designed by # of bedrooms. I had a sand mound system designed for a 4 bedroom home that was $10,500. Pretty typical for this area, from my discussions with others. A friend just put in a spray irrigation system that he designed and assisted install. This system would cost you and me about 25,000. His limiting zones were less than 18". My system design missed being a standard system, instead of the sand mound, by one test hole and 12". Bummer. A standard system would run $3000 to $4000 less.
carpenter in transition
mine was quoted at 4200 that is a 1500 gallon tank with a 90 by 110 field, well was 3200 figured on 70 foot i think that includes pump , pipe , wiring , well grout or something like that. mine is also around 2500-2800 sq ft with 3 beds two and a half bath. northwest ohio area.
Around here (western MI) sandy, well drained soil, typical septics I've seen are two 1000 gal. tanks, 600 sq. ft. drain field, dug out, stoned, installed and covered for $2300 - 02500. Add $500 - $600 if using precast coffins instead of drain field. The dowser I know can tell how deep to drill and how wide the vein runs. He's not usually off the mark by more than a few feet.
Edited 1/22/2003 9:55:54 PM ET by SCAMPERNATRA
I'd doubt that you could do it over open space like that, but I'll have to try it sometime.
As I understand one theory of how it works, The water, especially flowing water, is a conductor for fields of the earth's magnetic aura, the same thing that creates the Northern Lights in the winter sky. Iron deposits do the same.
So it is logical that an instrument or a person who is sensitive to these energy fields could read them. Watches invariably quit working on me. I sleep better with an east-west orientation then north-south, and small compasses have been known to swing with my body movements. The only thing about me that's not magnetic is my personality.
;)
Anyway, you search for ground water by taking a forked branch from a willow or alder - trees that like water and know where to find it, even to growing into septic fields for a drink - and holding it out from your body like this....
As you walk along the ground, your feet are in contact with the earth, picking up the energy patterns. You don't think about it or try to DO anmything. It just happens, like a compass needle swings. You have no control over where or when.
For dowsing a water line ( or a buried power line - don't try this disclaimer) you take a stiff #10 0r 8 Copper wire about 18" long and bend it about five inches from the end to a right angle. Do it again to make two. Cup your paws loosely around the short legs of the 'L' wire so they can swing freely. Then walk along and let them swing.
When you cross a water line, especially if it is a metal line and not plastic, the two wires will swing towards one another. Feels creepy.
But then - maybe it is all hogwash, who knows?.
Excellence is its own reward!
No, it isn't hogwash, it works.
1. At our previous house, we drilled a new well but we wanted to locate the water lines because we knew they had been redone in the last few years and were below frost line. We took two metal hangers and bent them as described into wires in the shape of an "L" The wires would cross every time we crossed the water line and then uncross when we came back. The water line was plastic by the way. It worked for me, my husband, and my sister.
2. We hired a dowser for our new place and hit water at 200 ft. Our neighbors all went twice that far. Actually, our one neighbor drilled a 900 ft hole and hit NOTHING! Ouch. Then he hired our dowser and found water. We drilled where he said two underground streams crossed. We figure if we need more water, we should be able to go deeper and hit the second stream.
To the original poster: I would never consider getting too far into the building process without drilling the well around here. Water depths can vary significantly from property to property in this area (colo mountains) as evidenced by my example above. Our well was around 5K by the time it was all said and done. That would be drilling, casing, 120 ft water line 10 ft deep (oops, guess that 5K didn't include the blasting for the water line but I doubt most people live on a big rock like we do), and pressure tank. If we had drilled a 900 ft hole that was dry, kiss another 10 grand away for nothing. That would hurt, especially if you were at the end of the process and out of cash.
Our septic was about 12K, but we actually did a lot of it ourselves because we had a backhoe on site. Again, our lines had to be blasted, so that added to the cost. Also, our engineer designed it wrong and then told my husband that when we were installing it according to the drawing supplied that we should have KNOWN it was wrong and corrected his (the professional engineer's) mistake. Huh? Isn't that why HE has the stamp that we paid so much money for on our plans? DIY homebuilding, not just a stupid thing to do, but an adventure. LOL!
A number of years ago (cannot remember the issue) there was a FHB "Great Moments" article about some Air Force guys did 'witching' to find buried MM cables near new building on a farm - the article shows the fallacies of believing in that stuff.
Where I am, wiching always works - you can point a stick down anywhere within a few miles and hit > 30 gal/min from 4" well right above the glacial blue clay layer at 60 feet.
Spent around $4K for my sand filter system and just under $2K pound down 174' for my well. I have about 2' of dirt on top of rock here...all the way down (at least 174'). Well is over 20g/min. Was pretty dry down until around 110' and then hit a vein.
Paid $400 I think for the septic "design" and stamp, included in the $4K.
Junkhound, your ambition and DIYness amaze me. Why not melt down some scrap and mold your own well casing?
Oh yea, my casing goes about 17' down...they couldn't pound it any further in the rock.
Don't forget the other $1K for the pump and installation and bringign the water to the house.
Well has to be a minimum of 100' from your septic system.
My well in Southern Utah was $10K. When everyone is busy wells are expensive, when they're all standing around wondering how to make the payments it's cheaper. 360' of 6" casing, top 20' is 12" steel with bentonite seal. Hit water 3 times going down to 360', but right now while my neighbors shallow (150') well is dry I've still got plenty.
Well must be 100' from closest building.
And yup, witched by local Witcher.
Don't be picking a well driller out of the Yellowpages.
Joe H
That's a good thing. Around here I think the well can be closer to a building...but what the well drillers told me...put it someplace it won't be in the way...and someplace they can get to in 20 years if need be. Then I heard all the stories of how people built buildings around their well and it couldn't be drilled deeper/reopened when the gravel/rocks fell in.
As is always the case....lot's of planning helps big time.
A 'bout 12 years ago this state (WA) 'outlawed' burning old motor oil in furnaces - only really 'free' way to melt scrap - broke my heart <G>
Art, years ago there was an backpage article in FWW about making your own tools.
It was pretty much a "Start with ten tons of iron ore and a couple tons of coal." Make some coke and smelt some iron, you may have written it?
Joe H
After I posted, I wondered just what fuel you'd use for free....LOL.
No, not me. My great-grandfather did dig his won coal mine in So. IL 'cause he thought he was getting ripped off buying coal. <G>
"an even wider range but the discussion will be enlightening"
ya betcha, Piffin, good comment!!!
Septic:
Around here (king co WA) if you don't have 4 ft of good soil, it's gonna cost you $5K to $10K even if you DIY . You can't both design and build both in this county without the 4 ft of good soil. Only way out cheap ($400+200) is to find someone you can team with, still costs $200 for each license (simple test, but intimidates most). After that, only about $400 in materials, assuming you both design and pour your own tank and have your own backhoe <G> .
Well:
$100 up front to the state here for recording fees. Each 21 ft of 8" steel pipe runs $130 (nearly unobtainium surplus at that size except in oil country-betcha David T in Alaska or the guys in Tx and OK could find some good deals?), so that's close to $7 ft right off even if you build your own drill rig and DIY.
My neck septic costs break down as follows:
1250 gallon concrete septic tank, set in final placement by concrete contractor: $600
Distribution box connecting to septic tank and providing opening for finger system, thin (2") and small concrete structure placed by hand: $150
Clean out lid (cast iron 22 3/4" heavy duty traffic-rated) and frame: $200
500' perforated 4" tile (plastic, sdr35 etc) prox .35/foot
#8 stone, biggest cost - here about $10 / ton delivered, conversion is 1.5 tons/cy, our spec is 12" side 24" deep on finger pipe
probably 200' sch-40 pipe and misc fittings to get from house to tank and run fingers out, here 5-100' fingers. Maybe $1.10/ft
machine time/labor to trench and dig in.
remodeler
Holy Moly! and I thought the garage slab thing was all over the universe. You guys must all live in McMansions if the infrastructure costs that much.
Here's an idea. Find a septic guy and a well-driller who work the area. Here they love to talk and are generally so knowledgable that they can give you a pretty good quote right over the phone...as long as you position the lot for them. Least that's what I experience. "Yeah, little lady, water's at blah, you've got clay down to blah, then sand. Gonna cost you blah. Suppose it depends upon your geology, tho. Even if you've got rock or iffy water they still should be able to give you good info about wells in the area, perc tests and what problems they've encountered.
BTW, I can witch too!
Shelley in NM
Thanks for the insight everyone. Will let you know what the end result cost ends up being. By the way, 1 degree F. this morning in Maine. Fricken freezin.
This is Doug in Alaska. I recently paid $5,000 for a new state-approved spectic system that serves a three bedroom home. The septic tank was 1,000 gallons and the leachfield was about 40 feet long, two feet wide, and extended 14 feet below frostline. The leach trench was filled with
approved leach rock and covered with a sediment barrier and five feet of top soil to grade.