I was wondering if you can get a bi-metal saw blade for a small delta band saw ( I think its a 60″ band). It sure seems like it would work well for iron balisters. Any body got a clue?
Discussion Forum
Discussion Forum
Up Next
Video Shorts
Featured Story
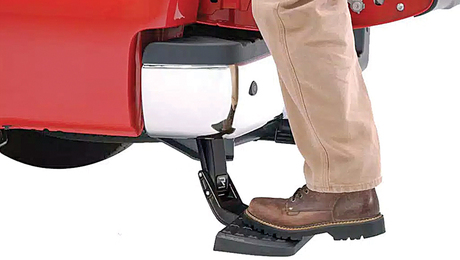
The RealTruck AMP Research Bedsteps give you easy access to your truck-bed storage.
Featured Video
Builder’s Advocate: An Interview With ViewrailHighlights
"I have learned so much thanks to the searchable articles on the FHB website. I can confidently say that I expect to be a life-long subscriber." - M.K.
Replies
The portable bandsaws have bi-metal blades
as a last resort you could have them welded together to make the right size.
Any saw sharpening shop worth it's milkbones should be able to do it for a modest fee.
But you should be able to find a source for bimetal blades for your machine.
Check with a local machine or welding shop to see where they get theirs.
Mr T
Do not try this at home!
I am a trained professional!
MSC ( http://www.mscdirect.com ) sells bandsaw blades ready made, cut to length or by the coil, if you can navigate their web site. Or just order a catalog. They'll send a free catalog to anybody who asks.
If your saw is set up for cutting wood, you'll need to slow it down by about a factor of 10, or it will eat the teeth off your expensive new blades.
Thanks for the tips!
Allen: I have had real good luck just using a sawsall with metal cutting blades. I just clamp the balusters in a vice and cut them off. A typical stairway will only eat up 2-3 blades.
Stan, Have you ever sat down and had a coffee break while you had your epoxy gun going? I found out the hard way just how fast that stuff sets up. I wish they had a system to flush that mixer tip out . Allen
Allen:
.....I never have used epoxy. I take a paddle bit and grind it so it drills a hole slightly smaller that the corners of the 1/2 inch shank. I tap these into the holes...and then screw some square drive srews on all four sides of the baluster. The countersunk head on the screws digs into the baluster...and you can not pull them out. You can adjust them so they are plumb. This makes it handy as the balusters can all be put in and they will hold themselves while you install the railing to their tops.
Good point, and a lot easier to lug around than even a tabletop bandsaw. Another possibility would be a cheapo abrasive chopsaw. I saw some plans somewhere for making one with a circular saw and some plywood and hardware.
timber wolf bandsaw blades,www.suffolkmachinery.com. there a few things to think about- what kind of metal are you cutting? size of the stock? usually when cutting metal stockyou'd like to keep the r.p.m. down because of heat generated will have diffrent physical affect's on the blade and unfortunately a 12" bandsaw dosent have a heck of alot of bandsaw length to it and wont be able to disperse heat as well as lets say a 14"-18" inch band saw. but like i said depends on thestock(thickness,composition). the only coolant/lubricant i would recommend would be pam, any other will affect tires, and blade tracking. the whole key to bandsaw's are tension of the blade, tracking, and the correct blade for the task and material. the address will help with that talk to a guy name art.. goodluck.......bear p.s.1-800-234-7297
Edited 12/1/2002 9:42:09 AM ET by the bear
Allen,
All of my small metal cutting tasks these days are done with a mini grinder with a Zip Cut ( Thin Cutoff Wheel)
Novy, I'm sure that would work great except when they where painted; in that case it might get to hot.