*
Our wood burning stove sits 36″ from the corner of the two exterior walls in our living room. The insurance co. wants us to install fire protection on those walls. Their specs: floor to 12″ above the top of the stove, UL approved and 1″ air space between the new wall and old wall. They suggest brick. Any ideas? Anyone familiar with FF88 (paintable fire retardant)? What about using non-combustible exterior siding (Hardipanel) in an interior application? TIA.
Discussion Forum
Discussion Forum
Up Next
Video Shorts
Featured Story
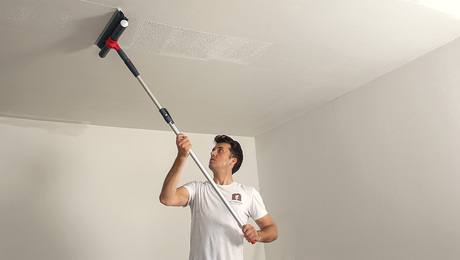
Skim-coating with joint compound covers texture, renews old drywall and plaster, and leaves smooth surfaces ready to paint.
Featured Video
Video: Build a Fireplace, Brick by BrickHighlights
"I have learned so much thanks to the searchable articles on the FHB website. I can confidently say that I expect to be a life-long subscriber." - M.K.
Replies
*
From what I've been told there aren't any paint style substances that do the job over time. If you discover one please let me know.
You didn't mention how much freedom the insurance company would give you. But, have you thought of the 4x4 fibre hearth panels(look like asbestos) wrapped in a sheet of copper?
In remote areas where wood stoves are commonly used and practical fire protection is the rule the only limitation seems to be the owners creativity, esthetics and pocketbook.
*I handled this same problem by laying down a triangular shaped bed of thinset with an overlay of 12x12 marble tiles for the floor. For the two walls, I placed three 2x4 vertically, on each wall, and attached cement backerboard( normal spacing) . Once in position, the backer board was then covered with 12x12 marble tiles. From a distance of 5-10 feet I was surprised to find that the job looked as though the tiles were simply attached to the wall itself. It's been almost 8 years now and it's still looks as good as the day I put it up.The idea of using copper covered "hearth panels" sounds like a good idea too, and would give a very nice "finished" touch to the same type of application.
*Isn't fire rated 5/8" drywall or backer (concrete core?) board set with the required airspace good enough to meet the building code? That should satisfy the insurance co.Copper and brick are probably overkill for a wood stove. Copper is a very good conductor of heat and expensive besides. I'm not sure why Steve suggested it.
*
I have dealt with this exact situation before. What I did was to attatch to each stud a length of steel channel running vertical on the wall. Onto this, attatch tile backerboard using tek screws. Set tile over this. Looks very nice.
I used 1/2" backerboard as this thickness allows for the screwhead to be countersunk slightly.
*Unless the stove is ancient, it shold have a plaque on the back indicating the manufacturer's recommended clearances. Or get the spec sheet from the retailer or manufacturer. The insurance company ought to go for that. If they don't budge (there are lots of other insurance companies), I like the suggested steel channels covered by cement backerboard, covered by tile or marble, or stone. An additional heat reflector and insulating air space with nothing flammable outside of the existing wall (presumably covered with 5/8 drywall).Vermont Castings' recommended clearances for their four models range from 15" to 19" back to unprotected wall and from 15" to 24" side to unprotected wall WITH their optional shields.-David
*
Thanks, everyone,for your ideas. We are currently waiting for the paperwork from the ins. co. telling us their "final" decision on what we have to do. We bought the house in Sep. and the previous owner had coverage with the same ins. co. They are electing not to cover us with the exact same stove in the exact same house--we are trying not to take this personally!
Anyway.....we progressed from being cancelled with no chance of fixing the situation,to weld the stove shut and you can keep it, to clean the stovepipe, remove the carpet, take down the shelves from behind the stove and redo the wall. The stove is 15 years old and we have been unable to find any manufacturer's specs. for it, and the answers the previous owner can provide aren't satisfying the ins. co. So, until we get written instructions, we are exploring our options, trying to come up with a fix that will satisfy the co. and not require rebuilding that end of the living room. Having the stove on the slab looks ugly but it makes Heather, our underwriter, happy. Eventually we will tile that part of the floor. The wall is our major concern for now. Again, thank you for your help.
*
The best reference out there for this topic comes
from the Hearth Products Assoc. at
http://www.hearthassoc.org. or something like that. The
HPA can hook you up with a certified person in you
area that can show you the proper methods. In my
experience, insurance companies are all over the
map on this stuff and will accept the HPA over
their own criteria. There are a lot of factors
involved in woodstove clearances. The simplest
thing to do is get in touch with someone with the
HPA certification and let them help
*If you cannot find the info, call the manufacturer. I bought a 30+ year old stove, with no papers. I searched the web, found the company, and the mailed me a manual (not a reprint either). The bummer was their book said 36" clearance.-Rob
*With a stove that old and all the hoops you are having to jump through, what about a new stove? They cost about $1,000 and you could end up spending a fair bit of that doing the mods to the wall, plus all your time and aggrevation. With a new stove, you could select the approved clearances in advance and get a modern catalytic one. I know several people who cut their wood consumption from 7 cords/years to 4 cords by switching to a catalytic stove - by virtue of burning the smoke that would otherwise go up your chimmey. And the neighbor's yard would smell better and you'd haul and split a lot less wood.-David
*
Our wood burning stove sits 36" from the corner of the two exterior walls in our living room. The insurance co. wants us to install fire protection on those walls. Their specs: floor to 12" above the top of the stove, UL approved and 1" air space between the new wall and old wall. They suggest brick. Any ideas? Anyone familiar with FF88 (paintable fire retardant)? What about using non-combustible exterior siding (Hardipanel) in an interior application? TIA.