I was on site last week, and was running my cords out. Heavier gauge at the panel, smaller ones as I got to the work area. This was a straight run, no multiple outlets being fed.
The painter stopped by and said that it didn’t matter what order the cords go, unlike air hoses or plumbing. His reasoning:
The current has to go through each conductor, to the tool and back again.
So it makes no difference whether the 12 gauge cord is at the saw or the outlet, likewise with a 14 or even a 16. If the cord is sufficient for the amp load, you can put it anywhere on the line.
This goes contrary to what I was taught, but there’s a logic there that I can’t refute.
Is he wrong, pulling my leg, or is it truly unimportant??
Discussion Forum
Discussion Forum
Up Next
Video Shorts
Featured Story
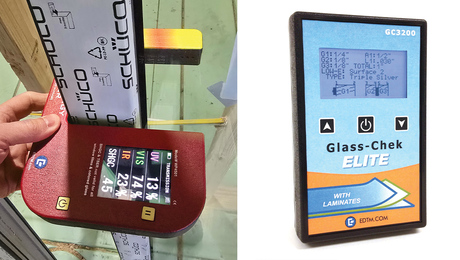
New devices showcased at the Builders' Show make it easy to measure glass performance, u-factor, SHGC, window thickness, and more.
Featured Video
Video: Build a Fireplace, Brick by BrickHighlights
"I have learned so much thanks to the searchable articles on the FHB website. I can confidently say that I expect to be a life-long subscriber." - M.K.
Fine Homebuilding Magazine
- Home Group
- Antique Trader
- Arts & Crafts Homes
- Bank Note Reporter
- Cabin Life
- Cuisine at Home
- Fine Gardening
- Fine Woodworking
- Green Building Advisor
- Garden Gate
- Horticulture
- Keep Craft Alive
- Log Home Living
- Military Trader/Vehicles
- Numismatic News
- Numismaster
- Old Cars Weekly
- Old House Journal
- Period Homes
- Popular Woodworking
- Script
- ShopNotes
- Sports Collectors Digest
- Threads
- Timber Home Living
- Traditional Building
- Woodsmith
- World Coin News
- Writer's Digest
Replies
Unless you're doing branch runs, he is correct.
Mike
So would the 'run' of cords only be as strong as it's weakest link? What I mean is if our temp pole is very far from the site, we will often run a 50' 10ga to a 50' 12ga junction box and then run more 50 12ga cords from there out to the tools. Are you saying that I'd accomplish the same thing by running 100' of 12ga right to the junction?
Electricity is like a foreign language to me..... go easy. ;)View Image
The max current capacity of the circuit depends on the smallest (highest number) wire -- it's what will melt first. But the voltage drop you get at the end is the sum of the voltage drops of the various cables, so if a 12 gives you 2V drop and a 10 of the same length gives you only 1V drop (not real numbers, but for example), it's obviously better to have the 10 instead of the 12, since more power makes it to your tool.
So convenient a thing it is to be a reasonable Creature, since it enables one to find or make a Reason for everything one has a mind to do. --Benjamin Franklin
No. In your examples, in one case you've got 50 ft 10ga and 50 ft 12 ga, in your other case you've got 100 ft 12 ga. There's a difference in the other 50 ft of wire size.
The OP is saying that it doesn't matter if you put your 10 ga first or the 12 ga first - in essence your 50 ft 10 ga + 50 ft 12 ga is the same as 50 ft 12 ga + 50 ft 10 ga.
Cool, I get it.View Image
No. It's the length times the resistance per foot of each cord. So if you have 50 ft of 14 ga you are going to lose twice the voltage as another run with only 25 ft of 14 ga. Bottom line is: make your long cords the heaviest gage you can work with like 10 ga. and then branch off with your 50 footers of 12 ga. Makes a big difference whe you are running compressors and those Big Foot saws.
Well, if you run one cord from the panel and then split into two, you obviously want the heaviest cord first. For a single run, though, you'll get the same current capacity either way.
But there's another practical reason for having the heaviest cord first: It's heavy and hard to move. Have the lighter cord closer to you since you have to move it around more.
Re the air hoses, you actually want the larger diameter closer to you. That way it serves as a "pig" to supply bursts of pressure.
Interesting. It made sense, but was a little counterintuitive, and went against everything the old-timers taught me.
If I'm any great distance from my compressor, I'll sometimes hook up a small air tank just before the last run of hose. Doesn't seem to reduce the cycling, but I don't outrun the air supply as often.