Brickmold is available in solid vinyl that never needs painting. How about expansion and contraction with heat and cold? Comes in 17 foot lengths. How much will that length expand and contract?
Discussion Forum
Discussion Forum
Up Next
Video Shorts
Featured Story
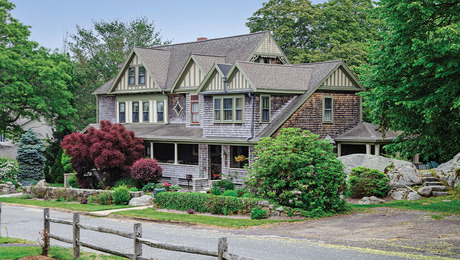
From plumbing failures to environmental near disasters, OHJ staffers dish on our worst and best moments.
Featured Video
Video: Build a Fireplace, Brick by BrickHighlights
"I have learned so much thanks to the searchable articles on the FHB website. I can confidently say that I expect to be a life-long subscriber." - M.K.
Replies
Will the manufacturer tell you?
Excellence is its own reward!
My experience with it is that the thermal expansion won't bother you as much as how it looks where it is fastened. Millwork shops usually t-nail or staple wood brickmold to door and window frames, and the ponderosa pine usually used fastens well using those means, and furthermore, the wood punchholes fill well and look OK when finished. The all-plastic brickmold simply doesn't fasten as well, and there is no way to touch up the nailgun or staplegun holes. Crossnailing at the miters doesn't go as well with solid plastic brickmold, so you might not like the look of the joints over time. Look instead at some of the plastic brickmold alternatives that use a thinwall extruded channel shape, and is fitted as a cladding over a wood substrate, or the rigid substrate-less design which is a rigid hollow section. The one I am downplaying here is the extruded foam plastic WM180 brickmold shape, 1-1/4" thick by about 2" wide, formed in a "U" shape with the hollow channel on the backside. Look close at the cross section and you will see that the material has an integrally extruded skin on the outside, and that the core material is dense but cellular (foamed.)
Thank you for your help with vinyl brickmold.
Let me explain in more detail what I have done with it and now want to do with it.
Last summer I made a cupola for a barn built in the 1800's. I copied the cupola from the Chester County, Pa. courthouse built in 1720 (no longer standing I believe). Shingled roof has 7 1/2 foot radius curved rafters. Made the 13 foot structure in the shop and lifted it up with a crane onto the square base that was prepared. The object was to bolt it on and not require maintenance. For soffit and eave I glued white glasboard onto a wood substrate. Solid vinyl brickmold for window trim. Used the white vinyl garage door jamb, turned backwards which has flutes or grooves for pilaster trim for the corners. Cut vinyl brickmold into 1.25 inch sections and attached under the soffit to make dentil. I tried fastening with stainless steel nails but ended up using a Senco finish nailer and put caulk in the nail holes.
Am satisfied with the appearance and it should be maintaince free. If there is slight expansion and contraction from 5o feet it won't be noticed.
Now working on a house addition with portico, four columns, entablature, dentil. etc. I am making dentil again out of solid vinyl brickmold but this time instead of cutting into small pieces I am doing it by cutting dado's leaving only about .35 inch of solid vinyl left. Making sections currently 17 feet long and attaching with stainless nails. I might be better off making them 3 or 4 feet long and laving a crack to fill with caulk for expansion.
I am glad to get your opinion that expansion will not be a problem around windows if I can be satisfied with the attachment. Have tried a couple around windows using stainless steel screws to cross fasten the corners.
Wood with the cover attached made of metal might have been a more stable material but one dent and it looks bad. Paint here in the midwest is a drag.
Thank you again for sharing your knowledge. Richard
What if you did a little science experiment to determine the expansion of the vinyl?
Put a stick outside overnight, let it get down to about 20 - 30 degrees, and accurately measure the length. Then, bring it back inside and do the same when it's at 65 or 70 degrees. For reference, you could possibly do the same with a 2x2. That should tell you how much the vinyl might misbehave.
I looked in some of my old text books for thermal expansion values, but couldn't find the right table. However, I think the experimental approach would work fine.
Ragnar
Thank you for your suggestion to test the temp. and measure. I brought in a piece of vinyl brickmold at about 40 degrees this morning from the garage. Put it in the freezer at about 10 degrees, then room temp, then to the open oven door to raise it to over 100 degrees, and then back to the freezer to see if it once expanded if it would stay expanded or retract.
at 40 degrees = 60 inches
in the freezer = 59 15/16
open oven = 60 1/8
back to the freezer= 59 15/16
back to room temp = 60 inches
Thank you for your suggestion. I keep two 36" sticks in my shop of end grain and cross grain so I know how much room to leave in cope and stick joinery. This is a similiar idea.
I guess the answer is that in 5 feet I must plan on 3/16 inch of movement. I plan to use this vinyl brickmold on six windows this week that are 5 foot square or larger, but will count on using aluminum or stainless screws to fasten the corners together and then leave 1/8 inch to expand and 1/8 inch to contract with caulk to provide the clearance.
Richard
Richard,
Wow -- I didn't expect that there'd be over an 1/8" of movement on a 5-foot stick!
The only possible alternative I can see to using the caulk approach would be some sort of overlapping trim via a rabbet. That is, hide the expansion gap behind an overlapping trim piece. However, this only seems practical for simple rectilinear cross-sections.
Good luck and let me know if you come up with any improvements.
Ragnar