*
Place 2″ of sand on top of 6 mil vapor barrier. Before placing concrete, dampen sand with spray so it will not draw water from the concrete.
Discussion Forum
Discussion Forum
Up Next
Video Shorts
Featured Story
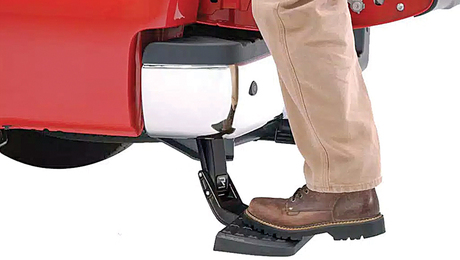
The RealTruck AMP Research Bedsteps give you easy access to your truck-bed storage.
Featured Video
Builder’s Advocate: An Interview With ViewrailHighlights
"I have learned so much thanks to the searchable articles on the FHB website. I can confidently say that I expect to be a life-long subscriber." - M.K.
Replies
*
My sub also advised against an impermeable membrane. The engineer had me put a permeable membrane called mirafi over the soil and a 6 inch compacted rock layer of "one inch cracked rock with no fines" on top of that to provide drainage for water that gets near the slab or foundation wall.
If your slab goes on soil and is in an area with positive water pressure, such as a low area with a high water table, you may want to look at a betonite product. It forms a "skin" that swells when exposed to water. It genrates so much pressure that it moves into and seals cracks. The slab has to be at least 6 inches thick. Its called volclay.
There are also additives that make the concrete more water proof. Make sure the concrete is mixed correctly and that it stays evenly wet while drying. That will help reduce fine cracking. If its a 2 car garage you may want to have expansion joints with volclay in the joint. Your contractor can cut the expansion joint. Then when it cracks it will be in that controlled spot. You can seal it and cover it with neat cement.
The final line of defense is to dig a trench, put a plastic sump pump bucket with an open bottom and lay a pipe at a grade of 1/4 inch per foot to daylight. Cover the trench and pipe with cracked rock. You need to have the top of the sump pump bucket at the level of the top of the slab. Have the contractor check the level before the pour. Then if you ever have problems you can just stick a sump pump in and the slab will be high and dry. Cover hole with something strong enough for a car to park on it.
Ask the engineer who did your plans.
*
Hello Everyone,
Questions like this are very hard to get an accurate answer for because regional differences dictate most of the how and why of any project. Concrete is no exception.
For answers to concrete questions, regardless of region, try this site. If you don't find your answer, e-mail them and they will be happy to answer your questions.
b concretenetwork.com
James DuHamel
*ChrisOne thing I'd like to recommend is to go to 6 inches of concrete. Also recommend that any back fill needed under the slab be compacted. Put in 6 inches at a time, compacted , another 6 inches, compacted, etc. Put poly down, overlapping by 6 - 12 inches, tape the overlaps, minimum of 2 inches of sand and then 6 inches of concrete.Have what you want in the spec sheet and/or blueprint. If the GC or sub wants to put a disclaimer on their estimate/bill, so be it, but do not sign a waiver. As a GC, if a customer (like you) wanted poly under the slab and I felt that it might cause problems down the road and you insisted on having it anyway, I'd put a disclaimer in my estimate or contract to that effect, but I would not require the homeowner / client to sign a waiver. If I did, all it would cause is discontent and then the client would be wondering "What will he be wanting me to sign next?"Vince
*most concrete carries with it the "it will crack" guarantee. controlling where is the trick. i've never heard of the poly under it, it will crack one. i do know it will take more waiting to finish since the water has to go up. wire, fibre additive(hard to finish),control joints, and controlling the rate of cure will do more to help than omitting the plastic. don't forget to isolate the slab from the adjoining foundation. best of luck to ya.
*"I've run this vapor barrier thing by him, and he says that he'll do it if I sign some kind of disclaimer such that he doesn't have to guarantee the garage slab. He say's that in 20 years in the business,he has never seen a vapor barrier installed in a garage slab or ANY slab-on-grade for that matter."Chris, Insist that if you allow him to omit the vapor barrier, he will guarantee the slab in writing against cracking and moisture. Insist on specific recourse in the event of failure. If he declines (and my guess is he will) then you'll see just what he was guaranteing in the first place. Waving a worhless "guarantee" costs you nothing. 2" of sand is fine.
*
I'm having a new house built, currently waiting for the crawlspace foundation to cure. The garage slab will probably be poured in a couple months, and I would like to prevent moisture from penetrating the slab upward in the future. I've spec'ed a 6 mil poly vapor barrier below the slab, but the subcontractor who will pour the slab says that it will crack if poured on top of a vapor barrier, something to do with forcing all the water to leave the concrete in the upward direction as it cures, he says. The slab will be standard 4" with WWM, on top of 6" gravel. Climate: Seattle, 35-50 deg, rainy & damp all winter. What's the solution?
*As you know, a vapor barrier under an interior slab is very helpful as it keeps subterranean moisture from migrating up through the slab and permeating the structure.Some concrete finishers don't like poly under the slab as it makes their job harder and take longer. Since bleed water cannot escape through the substrate, it must escape through the top surface of the slab, which takes hours, may make the concrete cure unevenly, and may even weaken the slab. The uneven curing problem is more prevalent in hot, dry weather. This is compounded by subs who like to water down the concrete to make the pour portion of the job go faster/easier. This is very common. These guys will punch holes in the poly as the concrete is being placed to let the excess water drain out.One way around this to put a layer of aggregate on top of the poly to help absorb bleed water. In my area, this adds about $200+ to the cost of the slab. There was a 6/94 JLC article called "Sub-slab Vapor Barriers". The article's subtitle was "When Placed Correctly, A Vapor Barrier Reduces Slab Cracking, Increases Concrete Strength, and Limits Curling at the Edges. It gives a full explanation to your question. I read the article from JLC CD ROM.Still, slabs are routinely placed directly on poly and do not crack. Personally, I think cracked slabs are more often caused by watering down the concrete, and by unevenly compacted or uncompacted substrate.BTW - damp rainy weather is excellent for curing concrete, although the optimum temperature is around 65 degrees F.
*Chris, There is new additive for concrete which promotes higherstrength/density and results in a product which is virtuallywaterproof.Protecrete.com I intend to try it on my next job; take some cylinders. Regards, Rick
*Rick:I've heard about the stuff you refer to. I think they use it on poured concrete foundations. Got any idea of the cost?And, BTW - I'm still looking for a cheap, effective, curing compound.
*Place 2" of sand on top of 6 mil vapor barrier. Before placing concrete, dampen sand with spray so it will not draw water from the concrete.
*Poly should be covered with sand before the concrete is placed. If much water needs to leave the concrete then the mix is too wet and cracking will occur, poly or no poly. If your concrete guy doesn't know how to place a slab over a vapor barrier, get one who does.
*Exactly how much sand? Jon recommended 2". Is more sand better, or is there a certain thickness of sand layer beyond which any more is unnecessary? BTW, my builder has a certain concrete Sub he uses, and is probably reluctant to switch to another. I've run this vapor barrier thing by him, and he says that he'll do it if I sign some kind of disclaimer such that he doesn't have to guarantee the garage slab. He say's that in 20 years in the business, he has never seen a vapor barrier installed in a garage slab or ANY slab-on-grade for that matter. Is there some kind of industry standard which documents an acceptable installation of a vapor barrier? My goals are to maintain a good relationship with my builder, install a vapor barrier, NOT sign a stupid warranty waiver, and teach my builder something without insulting his intelligence or pride.
*Chris, Your mention of a crawl space indicates a frost line consideration. I will assume the garage is attatched, thusrequiring a foudation of equal depth. Where is the hydrostatic pressure? Seems like a moot point if this is the case. I will absolutely argue against vapor barriers in direct contact with the underside of the slab; based on my own first hand experiences over 25 years and documented studies by the portland cement association. Pouring at a 4-5inch slump will still bleed excessive water to the surface,effectivly reducing the water/cement ratio at the point were it is most critical. Craze cracking and curling area predictable response to the nature of the hydration process which conrete undergoes. Rick