*
I’m looking for peoples experinces with insulating concrete forms. These would good or bad experinces, anything that would shed light on this type of construction whether it be from the builders point of view, the home owners point or industries point. If there are products that go along with the ICF concept that would be helpful too.
Discussion Forum
Discussion Forum
Up Next
Video Shorts
Featured Story
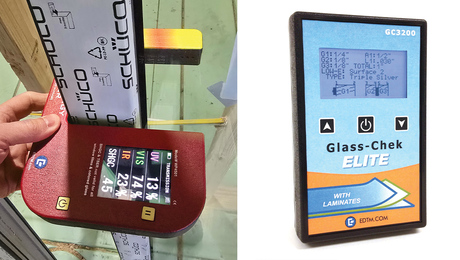
New devices showcased at the Builders' Show make it easy to measure glass performance, u-factor, SHGC, window thickness, and more.
Featured Video
Builder’s Advocate: An Interview With ViewrailHighlights
"I have learned so much thanks to the searchable articles on the FHB website. I can confidently say that I expect to be a life-long subscriber." - M.K.
Fine Homebuilding Magazine
- Home Group
- Antique Trader
- Arts & Crafts Homes
- Bank Note Reporter
- Cabin Life
- Cuisine at Home
- Fine Gardening
- Fine Woodworking
- Green Building Advisor
- Garden Gate
- Horticulture
- Keep Craft Alive
- Log Home Living
- Military Trader/Vehicles
- Numismatic News
- Numismaster
- Old Cars Weekly
- Old House Journal
- Period Homes
- Popular Woodworking
- Script
- ShopNotes
- Sports Collectors Digest
- Threads
- Timber Home Living
- Traditional Building
- Woodsmith
- World Coin News
- Writer's Digest
Replies
*
There have been quite a few discussions about ICF's on this forum, you might want to do a search. My personal opinion about them is that they are ok for a stem wall but are hard to do well as a wall. Also because of the fact that they cannot be vibrated I am a little leary of voids.
*
I have used icf for basement walls 8 and 10 feet high in soils with a lot of expansive clay. the brand we were using could not withstand vibration unless we used 2-3" slump. we had good luck with a 2-3" slump (actual) with superplasticizer added on site. this mixture acts as if it were 6-7" slump within the forms without the same pressure on the forms. the plasticizer leaves the mix within half an hour allowing the concrete to set. we did have problems with voids at the top of the wall forms when we poured a 6" thick wall reduced from the usual 8" thickness to allow for a brick ledge. the reduced thickness and the 2 #4 rebars and the form ties left a pretty tight space for concrete to flow. quick and light vibration would be an easy fix for this problem. On some of out last jobs we used a "grout mix" for the recipe of the concrete-- 2-3" slump with superplasticizer with 50% of the aggregate 3/8" or smaller and an extra sack of concrete. in our area that costs about $84/yd but it sure goes down smooth throughout the 3 lifts for a wall 8ft. high. I like the look of the Blue Max brand of icf it has a tight cast-in form tie that looks like it would have more resistance to head pressure than brands with removable (read loose)form ties
*Rob, I've been involved with ICF's for about 4 years and seen good systems thrashed by users that have no business building. ICFs are an excellent way to build and generally most of the systems are good when the instuctions are followed. 2 systems that i feel are the most versatile; can handle 3/4" agg, solid wall-no post & beam, ship flat not in blocks, are the R-control Diamond Snap Form and the TF System. They're both no -brainers. Check out R-control.com andTFSystem.com.
*Rob,I'm currently building an ICF home. We're using IceBlock forms. We used the 11" in the basement and 9" above grade. The basement walls are 11' as are the walls on the main level. The house has 39 corners.I don't know how the other systems work, but with IceBlock, it's critical to pre-brace each corner with a 2x6 nailed to a 2x4 (or similar brace). A "ladder" built around the top of the wall prevents either side of the block from bulging at the top.We did not use a vibrator because we were told even a pencil vibrator might damage the walls. Instead one of our workers manually prodded the concrete to prevent the pockets.Also, unless you have solid experience pouring these walls, I'd suggest a pumper truck. We poured a 10' retaining wall out of the back of a truck parked on a hill and the basement with a conveyer. The pour straight from the truck was fine. The conveyer pour had several blow outs (possibly from small pieces being used to piece the wall--but I believe it was the force from the conveyer).Good luck.LindaP. S. Portland Cement has many brochures for ICF homes. You might like to check out their site at http://www.concretehomes.com.
*Linda, I had trouble with that web address and did find http://www.portcement.org to work. I built our house from ICE Blocks in 1994 and introduced our local manufactures reps to the use of a ladder form on top of the wall. It served more as a better means of keeping the wall straight and allowed us to walk on top as well. We also glued all the blocks together and were able to pour a continious sloping 8' lift. Good luck with your home. Keith
*
Those that have used ICFs....
What was your final cost and man hours and describe your project....
I like the insulation idea but it seems like one of those overly marketed products as far as other advantages.
Jack : )
*
I have looked at every type of ICF on the market. Last month at World of Concrete in Las Vegas, I saw a couple of new ideas. However I am completely sold on the Ice Block system. I have built a 7500 sq ft commercial flower shop with a large production area using Ice Block from footers to top plate. A two story building. Beautiful system. We developed some innovations during installation. This stuff goes up so fast that you will spent more time scaffolding and bracing than placing the block and grouting them.
On the flower shop we used a pea gravel mix and a stinger. We poured lifts 10' high at a time. We started in a corner and placed about 4' of concrete and went around the perimeter using a pump truck, by the time we got back to the beginning, the mud had set up enough that we went ahead with the final 6' lift. This was all done in the winter. We wet stabbed the verticle re-bar after the cells were filled with concrete.
From our learning experience on the flower shop, we went ahead and built a 42,000 sqft nine screen movie theatre. We again used Ice Block from footers to roof deck. These walls were 38' high!
and are stright as an arrow. We made horizontal "ladders" from metal studs to keep the top course straight. On the cinema job we poured in 6' lifts. using straight 5.5 bag mix (3000PSI) Again we used a pumper. Make sure you use a double elbow at the end of the pump boom. This double elbow slows down the velocity of the aggragate when it shoots out of the hose.
On the Flower shop job we had five blow outs caused by inadequate splicing when we had to cut the last block. Now we scab on a full sheet of plywood over the custom cut block and violia! (there is always a learning curve to any new system or method, make sure you talk to lots of people who have done this to pick up all the tricks of the trade) We've never had a blow out since--Even on the 2400 linel feet of wall 38' tall on the cinema; not one blow out!!
I particularly like the Ice Block over all the others because of the preformed corners and the hefty metal stud screw strip a 1/2" under the foam skin. We have applied EIFS directly onto the block surface. For water proofing we just use a compatable emulsion sprayed on. Very inexpensive.
Don't know about bugs. I've heard termites or other boring type critters like to tunnel up into the foam. Sheetmetal pans may do the trick to keep them at bay.
All in all, I'd use ICE Block again in a heart beat. Wish I had known about it when I build my house, We live in the flight path of an Air force base and the insulated concrete walls would sure keep the figter jet noise out...
My next project will be a getaway mountain cabin up by a ski area. R-35 walls and fire proof is sure a great way to go.
Drop me a line if you have any other questions. Good Luck, [email protected]
*
Elwood,
Are you pouring concrete 38' into holes in the blocks or stacking blocks 5', filling, and repeating?
I definitely need to a see project with my own eyes before I do one of these walls. I've heard here and everywhere that
b the tricks are worth learning first.
Jack : )
*
AJ, In 1993 when I first planned my 1900 sq ft ranch I was going to use 8" poured walls and insulate to R-30 from the outside. Then I was introduced to ICF's at a code officials meeting and was very impressed. I researched what companies I could at the time and went with ICE Blocks. I figured my cost savings to be about $5000.00. I built the house in 94 and am very happy with it. And yes the tricks are always worth learning first. Keith
*
Panelman,
In about another month I'll be buiding a 750sq.ft. addition over a basement. I'm using the 10" Diamond Snap-Form, 9' high for the first time. The material is on-site , I'm just waiting for the weather. I'm convinced this is a good system, but I'm sill nervous about pouring tons of concrete into a fancy coffee cup! Any advice will be appreciated, but I'm especially curious about proper bracing, vibration, concrete mix (using a pump)and pour rate. Also, because of a walk-in bay I have a lot of 1' and 2' pieces. Any cautions as to use or placement of these pieces.
TIA,
Jerry
*
Jerry
Didn't the supplier/manufacturer give you any training?
Are you a contractor using these or just doing it on your own?
Are there installation manuels?
I'm very interested in this please respond.
Rob
*Jerry; The contractors building the 30 foot tanks at my job site do not poor all at once but pour in shorter batches called lifts.These individual lifts use a gasket at the top of the pour to insure that each lift does not leak.This gasket is simply a heavy rubber piece 1 inch thick and 5 inches wide. My thoughts were that you may be able to use this technique on your ICF wall.The gasket would only be insurance in extreme waterproofing cases.But you will avoid handling massive amounts of concrete as these contractors have. Good Luck Don L.
*
Rob,
I have the Snap-Form installation manual and it looks pretty good. I'm sure if I follow it ( and I intend to) everything will go smoothly. On the other hand, there's no substitute for experience and with four years experience, I think Panelman's advice would be invaluable, but thanks for asking.
Jerry
*Thanks for tha advice Don. I plan to pour the wall in three foot lifts, but I won't allow the concrete to harden completely between lifts so I won't need the gasket you mentioned.Jerry
*Rob,As you do your homework on ICFs, look at ease of use, the mechanical properties of the finished wall (they're not all the same), and look at what the mfr. offers for tech support and training. Reward wall systems (402-592-7077) gave us excellent tech support and training materials. I couldn't be happier with the results we got with their product, and this was a fairly unusual job with high equivalent hydraulic pressure design values.I would also check out AAB forms (Blue Maxx brand), I haven't used these yet, but they look good. 1-800-293-3210, http://www.bluemaxxaab.comAs for voids in the wall, this can be a sad story. If you follow mfr. instructions, pour in lifts, working your way around the perimeter at the recommended rate, and use a strong (5 or 6 bag)3/8"-minus mix, you'll probably do fine. The 3/8"-minus mix is important, in my opinion, likewise for rodding it down as you go.Now this is purely speculative, as I have not tried this trick, but one of my concrete subs suggested taking the blade out of a sawzall (important safety tip) and running the sawzall down the outside of the form to vibrate the pour gently. Anybody tried this yet?My strongest advice is if you have any doubts whatsoever about bracing, be safe rather than sorry. These forms are plenty strong, but bowed walls are hard to fix.We use aerosol foam adhesive to glue the forms together as we go. It helps with the assembly and helps keep everything together during the pour. Check with the mfr. for chemical compatability if in doubt.I'd like to hear about what you decide on and how it works out. Thanks.
*
First I want to thank everyone that has replied. The input is appreciated. Next I apologize for not responding sooner, I took short vacation and had my hip replaced.
Bob
I am wandering which forms you can not vibrate?
Why are they hard to do as wall (I'm think you mean above grade?)
What is the difference between the quality of a stem wall and "regular wall"?
Rob
*RonSounds like you have done a few. Where are you locate and which brand do you use? You mention Blue Maxx is that what you have used on all your jobs?Did you have any problems with the super plasticiser?Rob
*panelmanBy the name I assume you do traditional concrete forms. What is the amount of foam forms you do? Are people asking you for it or do you offer it?In your area are ICF's popular?Rob
*LindaHave you used them prior to this project? How was the technical support? Would you use them agian?Rob
*ElwoodI'm interested in hearing more about the movie theater. Reasons why ICF's were chosen over other products.Rob
*Dave It sounds like you have used reward. Why that type rather than say Blue Maxx? Did you use it above or below grade or both? I'd be interested in cost comparision.Rob
*
Initially, we used Reward because it was locally available, the concrete sub/local distributor has a good reputation, and we had an unusual design challenge. This turned out to be good luck for everyone. This particular building had 10 foot high walls, 6' to 8' of which was underground on two sides, with the potential for high soil pressure and sub-grade water. I was impressed with the performance of the product, both structurally and thermally. As the site supervisor and project manager, I had the chance to see this from a few different perspectives, from design, to helping with the installation (couldn't resist), to looking at the budget.
Certainly the ICFs are more expensive than frame construction for above ground applications, but it's also not an even comparison if you only look at SF cost. For below grade living spaces, I wouldn't go any other way. If we had a termite problem here, I might change my tune, but I think the mfr's are looking at this real hard. It just depends upon what you want.
To a great extent, the cost is also going to be a function of how well designed the building is, and how smoothly the construction goes (read that as "experience" -- there is a learning curve, albeit short & steep). We joke about every dollar spent on good, thoughtful design being worth about ten on the site when you're trying new materials or techniques. To some extent, that might be conservative.
The thermal performance and structural integrity of these buildings are unbelievable until you experience it. Some folks have expressed concern on this board about earthquake stability. I'm unqualified to comment on that, but the mfr. would probably have something to say. As for the AAB forms, I just haven't had the opportunity to use them yet. Other builders here speak highly of them.
Weather tightness was an attractive advantage of ICF. This building had over 1,600 SF of T&G ceiling, with a lot of windows. I assumed that this would result in some air leaks despite our best efforts. We did a blower door test, just out of curiousity. As far as I can tell, it was an inconclusive test, because we had to evacuate the building after about two or three minutes. Apparently, the primary source of air (?!) infiltration under these conditions was through the drain/waste lines (yes, the traps were full of water). After the thermal consultant got done drawing what seemed like all the gas in the septic tank back into the building, he said the house was pretty tight. I've been meaning to ask FreddyL if this is normal. :)
*
I'm looking for peoples experinces with insulating concrete forms. These would good or bad experinces, anything that would shed light on this type of construction whether it be from the builders point of view, the home owners point or industries point. If there are products that go along with the ICF concept that would be helpful too.