*
I have been installing large sheets of laminate in banks for teller booths and sometimes after weeks the edges have sharp corners. I think the laminate gets bigger, or HD press board shrinks. Also, some of the seams open a little. Everything has stablized in building for days before installation. I use real contact cement-stink stuff and Wilson Art. Any suggestions?
Discussion Forum
Discussion Forum
Up Next
Video Shorts
Featured Story
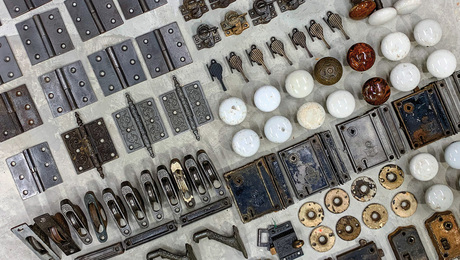
Whether it’s already in your house or picked up at a flea market, vintage hardware almost always needs help.
Featured Video
Video: Build a Fireplace, Brick by BrickHighlights
"I have learned so much thanks to the searchable articles on the FHB website. I can confidently say that I expect to be a life-long subscriber." - M.K.
Fine Homebuilding Magazine
- Home Group
- Antique Trader
- Arts & Crafts Homes
- Bank Note Reporter
- Cabin Life
- Cuisine at Home
- Fine Gardening
- Fine Woodworking
- Green Building Advisor
- Garden Gate
- Horticulture
- Keep Craft Alive
- Log Home Living
- Military Trader/Vehicles
- Numismatic News
- Numismaster
- Old Cars Weekly
- Old House Journal
- Period Homes
- Popular Woodworking
- Script
- ShopNotes
- Sports Collectors Digest
- Threads
- Timber Home Living
- Traditional Building
- Woodsmith
- World Coin News
- Writer's Digest
Replies
*
Dave-I've had the "shrinking" problem with seams opening up. Very disheartening when I put so much time and effort into making the seams perfect. I got very little help from the supplier when I asked for answers to this-it doesn't seem to be brand related. I never considered the substrate to be the problem-maybe your on to something. Hope to hear from someone on this.- John
*Two possible causes to this problem:1)The plastic laminate expanded from exposure to heat--not likely but it does happen--especially dark colors in direct sunlight.2)The core shrank. Contrary to what many people believe, fiberboard (MDF, HDF AND LDF) will move dimensionally with significant changes in humidity. A few days is not enough to stabilize stacked panels. The problem would be exacerbated if the panels were warehoused in a humid environment, then installed in the air-conditioned site with no backer sheets on undersides and backs that didn't show into the room.
*
Bill - if the core shrank, wouldn't it be more likely that the seams would tighten, assuming no professional would put the laminate seams over the core seams.
And actually, if the laminate "grew", again, wouldn't this tend to tighten the seams?
definately confused - yb
*
YB--I think the confusion here is with what seams we're talking about. I was responding to the evidence in the original post--he talks about the edges developing sharp corners. I assumed he meant the seams at 90 deg. corners, where horiz. or vertical surfaces meet an edge, like the 1 1/2-in. built-up front edge of a countertop. In such a case, if the core material shrank a bit, the surface laminate would indeed stick out and separate at the seam. If instead, we were talking about seams along a flat expanse, where you had to butt two pcs. of laminate together, then you're right--a shrinking core would tighten (and probably buckle) the seams.
*
Bill - I agree with what you're saying and that is what is so confusing to me. It makes perfect sense as you explained it except for the fact that he said the edges were "growing" AND the seams were opening. Maybe I read more into it than he intended. The other thing that occupied my mind for awhile was the fact that these are BIG sheets - and so more suseptable to expansion/contraction forces.
Dave - could you clarify the symptoms? Am I misreading? Gotta go South for a few days, but will definately check back later. (or might get a bad jones and rent some time at Kinkos!)
confused but curious - yb
*
Dave,
Did you ever try leaving a small hump near the seem during assembly? After the sheets are glued down you pull out the last thin spacer next to
the seem and roll the hump toward the seem forcing
it together. If you use too big of a spacer and too close to the seem you may never get the bubble out , so be carefull.
John Keller
*The edges where the surface meets the self edge or the laminate edge, the surface gets bigger and creates a sharp edge as it increases in size over the edge. I don't know how to explain other than top surface enlarges over edge and creats a sharp edge. i don't think it is the substrate as this even happened when I installed over existing lamanite. could it be a chemical reaction to contact cement and laminate material?
*John, I didn't use anything at the seam, just a nice routered joint that fit perfect together and was tight after installing. Weeks later it opened up a little and needed seam sealer. Also the edges at the sides of the counter got sharp do to expansion. It has happened over new substrate and over old laminate used as subtrate. I will be gone for a week doing another bank, but will check site tonight.
*Shrinking substrate or expanding laminate--it can be a real conundrum. The situation is capricious and possibly due to a variety of things. The following ideas should help.In my Taunton Press book, "Making Plastic Laminate Countertops" I discuss the "rule of 48," which is the importance of storing the laminate and substrate together in the area where they will be assembled for a MINIMUM of 48 hrs. prior to fabrication. There should be free flow of air around the components. Sticker the sheet goods.Even still, there are occassions when parts of the finished assembly will move. More than once I've had to go back and refile edges that were perfectly flush when the counter was made, and "grew" out a bit. On a couple of occassions I've had the front edge strip of laminate grow past the side edge and someone walking past the corner snagged the laminate and ripped it loose. In one instance, they snagged and broke the edge off. I get the call back, of course.Now, to prevent such problems, I tape off the last inch of laminate and underlay, apply contact cement, remove tape, adhere strip of laminate (I'm talking edge strips here) and before pressing the end in place, I use cryoisocyanurate glue (spelling is undoubtedly wrong-I mean SuperGlue) to stick down that last inch. The ridgid bond does NOT move. At least that has been my experience. There is a bit of a trick to using the super glue but once you learn to deal with it, there is nothing to it.Along these same lines, here is a tip for keeping seams from opening up: Use the masking tape again to tape off about 3/4 in on the sheet and counter, along the seam. After applying the contact adhesive, remove the tape and use a thin even layer of water resistant wood glue to stick down the 3/4 inch width. Don't put too much on or it gets messy. Here again, a rigid bond beats the contact cement any day.I've experimented with clamping laminate to pb substrate using wood glue when making backsplashes and other laminate asemblies and it takes longer (since I'm a small-shop fabricator without big equipment) to do but the bond is awesome.By the way, I hope everyone out there has a copy of my book??????? If I can be of help with questions regarding laminate fabrication (or cabinet refacing-- that's another Taunton book I've written), I can be reached at [email protected]. Consultations are free. But most of the answers are in those books...Herrick Kimball
*
I have been installing large sheets of laminate in banks for teller booths and sometimes after weeks the edges have sharp corners. I think the laminate gets bigger, or HD press board shrinks. Also, some of the seams open a little. Everything has stablized in building for days before installation. I use real contact cement-stink stuff and Wilson Art. Any suggestions?
*
I have used laminate in non-cabinetry applications and believe that laminate will change size by a lot - like 1/4" in 48" from 10% to 90% humidity. Obviously, a typical house won't see this range but it does seem to be a somewhat unstale material. Though, with wood as a substrate - I'm sure its a different issue.