Discussion Forum
I am constructing a 30 x 60 shop. I am getting conflicting advice from well meaning friends about the prevention cracks in the slab. One dude tells me to go with fiber re-enforced cement. Another tells me to use lots of rebar. What is the best way? How thick should it be. I will be driving on it.
Discussion Forum
Up Next
Video Shorts
Featured Story
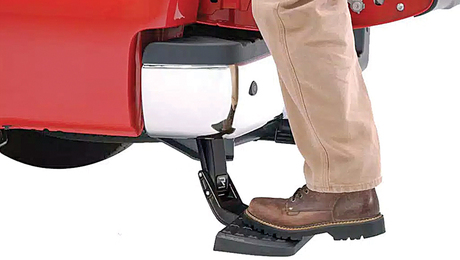
The RealTruck AMP Research Bedsteps give you easy access to your truck-bed storage.
Featured Video
Builder’s Advocate: An Interview With ViewrailHighlights
"I have learned so much thanks to the searchable articles on the FHB website. I can confidently say that I expect to be a life-long subscriber." - M.K.
Replies
Get a concrete person who does hocket rinks and tennis courts and prepare to pay really big bucks for no cracks. Those guys claimn they can do it but charge accordingly.
For realistic $, you don't avoid cracks, you control them.
Thanks for the info. Are you saying I should divide the floor into smaller pieces? How big? How thick? How do most shops or warehouses or whatever done come up with floors that don't have bunches of cracks?
dont overlook the substrate. Rebar or fibre or mesh. it helps prevent the cracks, not stop them. Make sure your substrate is well packed, and drainage is solved underneath. Its the underslab erosion, improper backfilling and water redirection that improve your cracking chances. Have someone who knows what they are doing and order your crete with the right moisture. More water in the mix will probably be an invitation to cracking later.
But as one person said earlier, its crack control over anything else. But if youre dead set on not having one crack, block or pour a perimeter and get some joists....
Edited 7/28/2002 12:59:33 PM ET by BILL_1010
rebar is used for the bending of concrete, its purpose is to control weight. Fiber is used for stress cracks due to shrinkage and drying, the same purpose as wire mesh. fiber cannot replace rebar and rebar cannot replace fiber/welded wire mesh. I am a firm believer of fiber. The slab need to be a minimum of four inches poured on a slump of about four. watch out for heat of day and time. Do not let a truck set for over 90 minute from time of batch. Very important, Curing and control cutting. After placement, hose slab down and cover with plastic. keep wet for three to seven days. cut slab for control cracking no more than ten feet in length and at all corners.
Soil compaction; MAKE SURE SOIL IS VERY WELL COMPACTED, I know you think its tight but compact again. Cannot afford a packer, use your truck. Make sure gradeing is perfect flat. The different in slab thickness will created a stress plane for the crack to appear.
I couldn't have said it better myself, BrownBagg. The only difference is that I use both rebar AND fiber mesh. I still get a few hairline cracks, but after a good cure and a good sealing product, they are invisible to the naked eye.
On my next project I am going to use a massive four inch layer of washed sand over compacted soil, then a moisture barrier of 6 mil plastic, a two inch layer of two inch rock, rebar (supported by rock, not wire) and then pour using twice the fibermesh recommended for your area. This will be an expensive pour and you couldn't do it in the real world, however, this project is small addition to my shop and I have one goal in mind: no cracks. Let you know how it turns out.
Both of those are good ideas but the more important things are to have bearing, compacted, well drained soil under it, say 12" to 18" of inch minus or it's equivalent, and to not mix and pour it too wet. most of us like a wet pour for flat work because it's easier to push and pull but the more water in the mix, the more shrinkage cracks you'll have as the excess water leaves during the first year. For a job that big, you might want control joints.