*
I’m in the process of finishing off a rec-room in a below grade basement space. I would like to panel the walls with a plywood paneling. There is an existing area with the paneling installed over furring strips. Is it absolutely necessary to use furring strips(The walls are block with a thin veneer of cement and they have been painted)or can I use an adhesive and attach the panels right to the wall? If I have to use furring srips how can I attach them to the wall. I’m not crazy about putting anchors into concrete. For what it’s worth the basement is relatively dry. Thanks
Discussion Forum
Discussion Forum
Up Next
Video Shorts
Featured Story
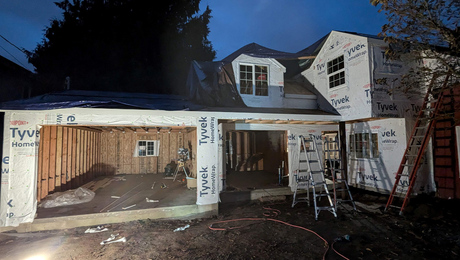
The FHB Podcast crew takes a closer look at an interesting roof.
Featured Video
Video: Build a Fireplace, Brick by BrickHighlights
"I have learned so much thanks to the searchable articles on the FHB website. I can confidently say that I expect to be a life-long subscriber." - M.K.
Replies
*
Where is this? Weather can make a difference in your need for insulation.
Anyway, a recent experience of mine:
1. Basement walls of block. Not always exactly even surface.
2. Previous owner had spot glued foil covered foam to walls. Hadn't gotten around to finishing. When I pulled at the foam, its glue adhered tenaciously to the previous paint on the blocks. The paint, however, didn't adhere to the blocks. Easy removal.
3. I wanted a moisture barrier between the block and the finishing products, so hung plastic from above ground level and under sole plate (added).
4. Attached furring strips, 16" O.C., to wall with 2-1/4 inch Phillips head Tapcons. Easy to do with a half-inch hammer drill and cordless driver drill. Could have done 24" O.C., if desired, but I wanted more nailing points. Had the strips ripped exactly 1-1/4 inch thick from two by lumber, as stock one-by is too thin for 3/4 inch foam, and two-by is too thick for what I wanted.
5. Used 3/4 inch foil faced foam (R-5.4) between the strips, covered with half inch gypsum. Tile board over that in the laundry area.
6. Furring strips, gypsum, and tile board provided sufficient thickness for electrical boxes and covered wiring.
Note the salient points:
Wall isn't exactly flat.
Moisture pushed off the paint under the glue.
No external wiring necessary.
Insulation added for climate (western Wisconsin).
I don't think your idea is any good, not only from the points I've made, but it's also a pretty chintzy approach to finishing a basement.
*One man's chintzy is another man's affordable.
*
I too am in the process of finishing a below grade rec room. I agree with everything Barry said. Tapcon anchors are great! Also, you may need drywall underneath the paneling to meet code (for fire protection).
Good luck!
*
Yes, but why waste your time and the material to do a half-assed job. The savings will be in his labor. Do it right, or don't do it at all. No offense intended. Best of luck.
*Luka,Actually, my solution may be more affordable, considering what's being paid for Don's plywood, how bad it'll probably look, and what will likely be a shorter life span.I think chintzy is about right, though calvin's "half-assed" has appeal.Maybe we should call this "So-So Homebuilding?"
*Sorry guys, I didn't mean to step on anyone's toes. It is not my intention to debate who is 'right' and who is 'wrong'. In my opinion there is no need for that particular distinction in this matter. I am merely trying to say that maybe we should be more careful about how we say things.It WAS my intention to point out that everyone has a budget. There are people here who can afford to build a replica of the Taj Mahal, and there are people here who can only afford to live in a tin can. Just because someone cannot afford the materials you might be able to, should they not try at all to better thier lot ? If I cannot afford to buy all the materials needed and instead use scavanged/recycled materials for much of my supply, does that give you the right to make fun of me, or to insult me ? I have turned out some pretty 'fine' work using 2/3 'found' materials. In Don's place I would first put up two layers of 6 mil plastic. I would then cruise construction site dumpsters for firring strip materials. Stuff that could be quickly run through a tablesaw to dimension. Failing that, I would gather all the pallets I could find. Tear them up and dimension the boards into my firring strips. I would then drill pilot holes in the wood, and use my Hilti tool to fasten the strips to the wall. If I could find it dirt cheap I would then lay foam insulation between the firring strips. As a cover.... If I were forced to choose between buying drywall and buying plywood paneling, I would go with the drywall. As an alternative, I would check out all the local lumberyards and HD's etc for dirt cheap OLD paneling. I would lay this up backwards if it was several different 'patterns'.When I am finished, I can guarantee you that what I have done can look as 'fine' as what you have done. And MY money was in hilti nails, plastic, insulation, etc. Probably half of what I use will cost me nothing.Fine does not always equate with expensive, nor is cheap always crap. So far this forum has not taken a hint from television and changed it's focus to become 'This Old Forum'. When/if it does, it will probably lose some of it's better posting persons. Finaly... Most of what you guys all said was good, comon sense advice, there was no need to debase that advice with the addition of aspersion. No matter how far out the side of the mouth the affront came from. If I come in here and ask for advice/opinions on how best to make a garage using old barn wood and straw bales, I do not expect, nor would I appreciate being insulted by being called chintzy.
*Luka, In case you misunderstood, here is a little more. The backer is a necessity as 1/4 in ply needs it. The furring is needed to get a chance at a flat surface and decent looking seams, nailing base, the poss. of insulation and maybe juice if it'll fit. The man is going to save $ in labor but not time. No need me thinks to use his time and limit his chance at a good looking job. I wholeheartedly agree on the benefits of the scavage approach to material. Spent alot of time many moons ago dismantling barns for the siding and beams. Took apart many a rice burner motorcycle crate for the mahogany. There is nothing wrong with reusing material. In fact, those folks should be commended for beating it to the landfill. I find homes for any worthwhile usable salvage before I think of throwing it away (ask my wife).The only point I wanted to make is that a job should be done right with whatever material you might use. Sorry if I may have offended or confused you.And Don, best of luck on that basement.
*I agree with everything Luca has to say. I wonder how chintzy stainless steel kitchens will look when they fall out of favour with next wave of design trends.But before anyone goes jumping to conclusions, no where in Don's post is there any mention of his financial means. In fact it reads to me that he wants to cover up some ugly basement wall in a style which is in keeping with previous work and he's a little unsure about the work effort and his abilities.I'm a little curious about how to attach furring to block walls myself. Usually deal with solid concrete and rely on my trusty powder nailer. Can you powder nail block walls or are they too thin?
*One other low-cost wall covering if you are just trying to clean up the appearance of a block wall, is paintable wall paper. there are several brands out there, but I've only used the Borden version.For a rough wall they have a type of high-adhesive bridging paper to apply first, then put the finish paper up ( it comes in a number of textures ),Then paint it. I've used this on two different basements and one old plaster wall that was getting quite loose but the customer couldn't afford to replace.I would imagine that you would have to be sure that it is a dry area.
*Another frugality point, besides finding cheap furring material. The half inch drywall I bought to put over the foam insulation had been damaged. Dings here and there that made it unsuitable for finished wall but okay for below the tile board glued over it. Even then, okay for a basement if I wished to plaster the dings. I got it almost free. Pristine half inch sheets were about seven bucks each. The damaged stuff was a buck a sheet and I had to forage for it myself from the back yard. A half hour's work sorting sheets saved sixty bucks or so. I don't earn that much at my job. It can be done cheaply.Calvin has it right about using furring to get a smooth surface. I had to undercut some of my furring strips to retain plumb given the somewhat extra and offset mortar joints and blocks the 1930's masons left in my basement. Folks back then didn't think of basements as living areas, so there wasn't much concern in that area.Luka's thoughts are also in the right direction, as far as old materials goes, though two layers of 6 mil plastic may be excessive. Usually 6 mil is only found in the contractor's quantities -- the big boxes of hundreds of feet. A cheap roll of 8'x25' 4 mil plastic is available at most home centers for about five bucks and is sufficiently waterproof and at the right dimension (8') for basement walls. Luka could have avoided what she thought to be a disparagement by initially writing what she did at 5.0 instead of at 1.1. Seven word quick shots aren't appreciated nor the standard on this board. Claiming to have been "insulted" on this board doesn't make it -- we aren't into feelings and sensitivities. Try HGTV if this is too rough.Tapcons work equally well in solid concrete, Scott, for this application, and powder nailing is probably excessive for concrete block. A carbide masonry bit in a hammer drill will penetrate much faster than you'd expect, be it block or solid. Just need ear protection so that you can still hear "Rewind" afterward. Okay, so what do you listen to....?TLE, as to the paper, it still boils down to an adhesive surface and what, if any, insulation one wants. Painted basement block in most areas that have basements isn't sufficiently adhesive for anything, as the paint will inevitably be forced off by intrusive moisture. I once visited a house for sale and noted that the basement wallpaper was the only thing holding the wall together. Everything under it was loose powder. Looks good or works -- take your pick.
*Shoot the mortar, not the block.Some concrete/cinder block will just blow out. Jeff
*Gentlemen, (and I use that term loosely. LOL)I made a mistake. I made an assumption. And we all know what happens when you make an assumption.Further to that, due to some sort of brain fart, I felt some compelling need to defend that assumption. Rather than continuing to argue who said what, etc, I will render my apologies. Please excuse my rambling reparté dé la white knight.The next round is on me.View Image
*fugedaboutit.
*
Many thanks to all.(I didn't realize I'd open such a can of worms). I'm going to go with furring strips and the tapcon screws. I plan to use 1x3 furring; what size screws, what size pilot (I assume pilot holes are needed)and at what spacing do you chaps recommend. Thanks
*
Chaps? Where you from Don?
The pilot is determined by the size tapcon. Most brands will have a bit included in the box. I usually use the hex head and countersink the head. The phillips and I don't have any luck in a hard drive situation. If you go for the mortar joints you shouldn't have a hard drive ahead. Might try phillips and skip the countersink. Get a couple of each and try it. Go for the 3/16 and at least but not much more than 2 1/4 long. Or.......... check out drive in anchors. Still require the hole but they hold well in softer material like brick and soft mortar. Read their required length/for furring info and choose the proper one. Gauge or thickness again shouldn't be to hefty. One that requires a 1/4" hole. Spot glue the strips also if you feel they'll stick. It'll bridge the uneven gaps. Hey, good luck.
*Don...Calvin... hi , Barry... Luka , buddy!..when we do basements, we usually stud the walls, drop yur 6 mil poly, lap it onto the floor, shoot your 2x3 or 2x4 shoe right into the floor, start with your lightest load until you get good shots,,,.. you can hold the face of your studs to any depth you want for the equivelent insulation value..wire you wall conventionaly, and then sheetrock it (3/8 if backer for paneling) or 1/2 if that is going to be your finish....we only furr our walls if we are squeezed for space..now you have a conventional stud wall, easy to build, easy to get professional results on.. and you can do some niice things wit the window treatments..if you want to furr the walls, try nailing up the furring with old fashioned cut nails or concrete nails and a two pound hammer... only into the joints alot faster and cheaper than the tapcons, and the strength of the tapcons will only be as strong as the mortar joints anyway.. so ?block walls were furred for a long time before there were tapcons (just a little observation of mine)hey how bout those Red Sox?1918 was a great year but 2000 is gonna be even better, sorry bout that ohio...Calvin, BGSU gave the greatest concert of the 3 I've heard so far..they had the whole audience rapt.....and then they had them rolling in the aisles with their finale....and that fiddler, De Pue, whoo hah.they done ya proud Calvin..
*Glad to hear it Mike. We turned around on the way to Howards Club H. Snow that night and for the first time, the van headed for the ditch. Straightened it out and decided to forego the music. U-turn and home for the nite. Ah well, next year.Cut nails, yup.Didn't know about a fiddler. Will have to catch a show. Thanks.
*Mike: Good info thanks, but there is h/w baseboard heat running around the walls, and the blocks are covered with a veneer of mortar and paint. I think Calvin's adhesive/tapcon is my best approach. If you hear a bunch of expletives deleted Saturday you'll know I'm not having a good time.
*If you've got hw basebd on the wall at the floor, make sure you cap the furring at the bottom so that heat doesn't go be hind the paneling. Keep it in the basement room where it belongs. Best of luck.
*Mike,Very good post at number 12. I said half inch drywall 'cause that's what inspectors want to see over foam -- probably 'cause that's code in many places for fire reasons. I think 3/8 is probably okay if another layer of tile board is applied, but I'm not into going to court over it.The rule of thumb is that Tapcons should penetrate at least an inch into the masonry anchor, so choose your length based upon that. Whether it's 3/16 or 1/4 inch Tapcon depends on the holding strength. 3/16 is fine for furring. The drill bit that comes with a box of 100 Tapcons is probably good for a third or less of them. Get a couple more. There's a difference between "masonry bits" and those designed for use with a hammer drill. I buy Milwaukee 'cause I don't know better, and I get a discount where I buy. I woudn't ever drill into the mortar joint of block, just because that's the wall's weakest area and the area most likely to leak moisture afterward. There's no problem sinking a Tapcon into block or poured concrete if you use a hammer drill and the proper bit. Don't try this with your old $35 Skil 3/8 drill. Go out and get a proper half inch hammer drill. This, plus your cordless driver, are all you'll ever need for 95% of your home projects. You can rent the big guy for the other 5%, like anchoring iron railings, or such.The problem with concrete nails is that they aren't removable. And the pounding must have an effect on the block's strength around them. Tapcons were invented to replace nails, and they do so very well. I've handled more than one goof (I admit to them) by unscrewing the Tapcon, sealing the hole, and drilling where I should have in the first place.By the way, a recently renovated theatre in our town use Tapcons five years ago to anchor the new seats into seventy-year-old (read very hard) concrete, and none have come loose yet.
*Steve,Went out and bought 150 tapcon 3/16 by 2 1/4 as suggested. Put the drill bit in my 1/2" Milwaukee switched to hammer and noticed the bit looked a little big but I drilled the hole 1/4" longer than the screw as recommended in instructions. After I tried to screw in the tapcon with my cordless it didn't seem to bight. I was right, I was able to easily pull out the wood with the screw.(Expletive deleted). I'm a weekend warrior (as if you couldn't tell)and I had a few 2 1/2" cut nails. Using a 5lb hand sledge it went into the pilot hole just great.Off to Home "Despot" to return tapcons, buy cut nails and a 2lb hammer. I saw Tapcon drill bits sold seperately and realized I was right the 3/16 bit that came with the screws was too big because the separate bit was 5/32 for 3/16 screws. Tried the new bit, same results, but the new bit is handy for drilling pilot holes for the cut nails. Since the block is skinned over with a coat of concrete (or mortar) and painted I can't tell where the mortar and block are. The area is 80% furred, and I think I have the hang of it. Thanks.
*Don,The result is what matters. I haven't had the same problem as you when drilling pilot holes for Tapcons, so I don't know what happened in your case. The only time I've had a Tapcon pull free like that was when if didn't penetrate deep enough into the block. That's why they should be sized for at least an inch's penetration. I believe that the 2 1/4 inch Tapcons mentioned earlier were for 1 1/4 inch furring. If you used dimensional 2 by 2 furring, you'd have added another quarter inch to the material , which could be enough to prevent the Tapcon from getting a strong grip. 2 3/4 inch would then be appropriate Also, the drill bit can't be rocked or wriggled when drilling, as this would enlarge the hole.
*Steve,Thanks, I don't think I rocked, but maybe the threads weren't deep enough (even with the 5/16 bit)or the block wasn't hard enough and crumbled. The house was built in the 50's I think, but it appears that quality material and workmanship were used. Anyway, the results turned out OK>
*Steve,Thanks, I don't think I rocked the drill, and I used 1x3 furring, but regardless the end result was OK.
*Glad to hear it Don. Now remember what you learned and keep it handy for next time.For your info., the bits in the box should be sized right. Masonry might be soft and then it'll strip out. Was the bit in the box or did they give you one? Their associate might have not helped you.Good luck on the finish. I'm sure you'll do well.
*Calvin,Good point. I've had "sales associates" at one place see 3/16 on the box and reach for a 3/16 bit.Hard to say why the Tapcons didn't hold. My own block wall is 25 years older than Don's and had been subject to negative slopes at the foundation, big shrubs at the walls, and no down spout extensions for years before I bought the house. I had no problem with Tapcons. Have to be there, I guess.Well, King, this case is closed.
*Calvin,Not to beat this to death but the box of 3/16 x 2 1/4 Tapcons had a 3/16 bit in it.
*Don boy. The 3/16 tap con takes a smaller than 3/16 bit. The qtr. inch, a little bit smaller also. The 3/16 tap con bit is 5/32. It should have a cut out at the base of the bit. Don't wanta beat it either, but just a little more info for you.
*
I'm in the process of finishing off a rec-room in a below grade basement space. I would like to panel the walls with a plywood paneling. There is an existing area with the paneling installed over furring strips. Is it absolutely necessary to use furring strips(The walls are block with a thin veneer of cement and they have been painted)or can I use an adhesive and attach the panels right to the wall? If I have to use furring srips how can I attach them to the wall. I'm not crazy about putting anchors into concrete. For what it's worth the basement is relatively dry. Thanks