*
We have a steep hillside lot with difficult access, and we need to
add a 2- or 3-car garage, so we were thinking of building a
sturdy shop-addition on the lower level and then putting the
garage on the roof of the shop. Anybody know if this is possible,
and what the engineering/cost issues might be? Thank
Discussion Forum
Discussion Forum
Up Next
Video Shorts
Featured Story
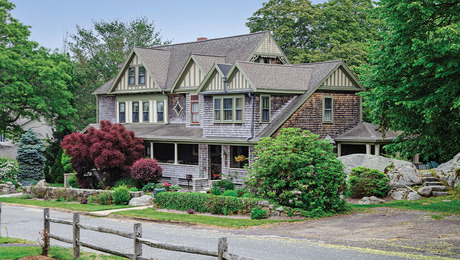
From plumbing failures to environmental near disasters, OHJ staffers dish on our worst and best moments.
Featured Video
Video: Build a Fireplace, Brick by BrickHighlights
"I have learned so much thanks to the searchable articles on the FHB website. I can confidently say that I expect to be a life-long subscriber." - M.K.
Replies
*
This is not really a problem, but you will need to have it engineered. Once that is done there should be nothing unusual about the construction other than the framing being beefed up.
*Over the past 15 years, I've quoted several garage floors with wood floor trusses. But I've never sold one - they're pretty expensive. I'd suggest finding a supplier for spancrete. That seems to be the way everybody ends up going that I've dealt with.
*
Ron's idea of Spancrete is an excellent idea. At any rate, as a PE, you will need to have it engineered and
b properly detailed.
As with any construction, its sucess is dependent on good design, detailing and execution. The three can be expensive to achieve, but there are sure to be reputable engineers who will tackle the job for you. I would assume approx. 5% of the construction cost as a reasonable design fee, assuming soil conditions are readily attainable and suitable. Unknown soil conditions is a whole new ballgame...could mean big bucks in site survey, analysis and engineering. It is all dependent on your site. Hire a consultant to go over your plans and site for a couple of hours,
*I know a guy who is using TJI's for this situation. He has put them on 12" centers instead of 19.2 but is this really safe. I have my doubts. Can anyone give me some suggestions. I would hate to see someone killed over this.As far as I know it is not an enginered job. I know that is the first mistake on his part. But I need more info. Thanks
*
Hollow-core concrete plank. Here in western PA the manufacturer is William S. Long Inc. We used them on a project and they have a lot of potential for freespanning. The bottoms are real smooth, and they have a slight camber to them so you have to pour a peagravel mix over them to level them out. Another neat thing about them is you can run mechanicals inside the cores (including using them for ductwork) my thought personally though they lend themselfs to radiant heating the most. They make two sizes 8" and 10" the later will span 43 feet
*Corq,One of our jobs here in Dallas has this very same thing. The floor to the garage is made up of very hefty steel "I" beams that were enginered to carry the weight of two cars. On top of the steel they welded corrigated metal and then poured the slab on top of that. Don't do this yourself. Hire an engineer and do it right or don't do it at all.My opinion,Ed. Williams
*
We build these types of structures quite often. Most people think that Texas is flat, and most Texans believe that they have to build on flat lots. We just quoted and are about to start a building that sounds similar to what you are doing. We build with Insulating Concrete Forms (ICF's). This particular two story building will be at the end of an existing driveway that turns into an existing house (with a rear foundation wall that is close to 15' tall that probably could have been a basement for less $$) We will be putting up solid concrete walls, 12', then install "S" deck (a large corrugated steel panel like that on some steel buildings), pour a floor, then build the walls up one more story. The building is 24x36. The floor system will have access for a stairwell to the basement level. The upper level will be for this guy's toy cars. There are lots of ways to build like this, about six years ago, we framed a garage on stilts on a steep hillside, decked it and poured concrete inside. The city of Seattle required the concrete mainly for fire resistance. There are a lot of manufacturers of the corrugated steel, you will be able to find them on the web. Most of these are free spanning up to 12 feet or so, without any shoring, some only require a temporary stud wall underneath until the concrete has cured for a couple weeks. British Steel and their subsidiary , CSM Canadian Steel Manufacturing, have plants in Vancouver, Edmonton, Toronto, and Montreal. We can buy "local" at significantly less $$ You may be able to also.
*
We have a steep hillside lot with difficult access, and we need to
add a 2- or 3-car garage, so we were thinking of building a
sturdy shop-addition on the lower level and then putting the
garage on the roof of the shop. Anybody know if this is possible,
and what the engineering/cost issues might be? Thank