*
My partner and I just sheetrock a house that was built by another contaractor. He used metal studs in the house. This had to be one of the worst sheetrocking jobs that we ever had to do. All the walls were 10′ tall and the main hall way almost fifty feet long. Metal stud makes for a nice straight wall but it sucks to sheetrock. And the echoes were unbelievable. Metal studs should stay where they belong. In commercial construction.
Discussion Forum
Discussion Forum
Up Next
Video Shorts
Featured Story
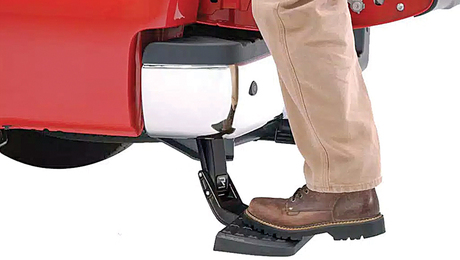
The RealTruck AMP Research Bedsteps give you easy access to your truck-bed storage.
Featured Video
Video: Build a Fireplace, Brick by BrickHighlights
"I have learned so much thanks to the searchable articles on the FHB website. I can confidently say that I expect to be a life-long subscriber." - M.K.
Replies
*
So what was the problem sheetrocking on the metal studs??? I could be wrong but the metal studs would not be responsible for the echo.
*So your partner and you rocked over steel studs and instead of appreciating the fact that you have experienced something different and have expanded your horizons, you post to bitch.I see you will go far in the trade.Gabe
*For all of you guys using steel studs, what have been your experiences with them? I used tham on a small wall in my home just to give them a shot. As with anything, there is a bit of a learning curve and it took me a bit longer to build.Now, about sheetrocking that wall, I used my drywall screwgun and what I think were the right screws (labeled for use as drywall to metal studs). It seemed that if I was hanging a sheet horizontally, I would have to hold the stud flange from twisting as I put in the first crew at the 4 foot mark. Not too difficult, but different. It also took a second for that screw to grab, which again took some getting used to. I was also a bit concerned about screw holding power in that thin gauge metal so i added a few more crews and glud the sheets on as well (Don't know if this glue worthwhile or not).Anyway, that was my experience. Nothing bad, just different. How have your experiences been?BTW, I haven't used metal studs since then. No one uses them in residential construction around here.Eric
*Eric,Steel studs are just another item in our inventory of possibilities. Sometimes they are the answer and sometimes not. For irregular walls or for small renovations, hard to beat. You walk into a clients home with a small bundle of metal studs under your arm and no sawdust to clean.Gabe
*If you place the screws close to the web section, the studs will twist less - leverage and all. I use them regularly, and I love them. However, I do use 20 ga most often, but would like to ease up and use 25 due to cost, etc. They are straight, and I feel give better results. You might try just screwing the edges and gluing the center. There is less to mud, and you get what is essentially a box beam. But, they are the old standard size 3 5/8 which leads to problems at the doors and openings that requires different handling. If you own the building, you will like the fact that they do not shrink and crack drywall. Dennis
*I have built a few steel frame homes (from the floor joists to the roof trusses), and they are not always the easiest thing to work with. The glue definitely helps. The lighter gauge studs (25 & 26 ga.)... also called drywall studs... will tend to resonate. I have switched to 20 ga. studs throughout, on 16" centers. That's overkill in the steel framing world, but the walls are sturdier (even though they may not need to be), and there is no resonating. It also simplifies my materials order, since I design my spec. houses to use mostly 20 ga. studs for load-bearing walls, anyway.The worst part to me is the profile of the panhead screws, especially around openings. The steel may be perfectly straight, but the screw profile sometimes kills that advantage.I will build with wood, too. But face it, guys: Steel framing will slowly grow into the residential market. Learn to deal with it.
*Frank, is there anyway to spot weld these things? It would seem that a small spotwelder would be quicker and avoid the problems you mentioned with panhead screws. I have looked at the steel framing sites, but I have not seen this mentioned. I have read there there are pneumatically drive fasteners (read nails of some sort) that are being tried.Dennnis
*Well, I did learn that the light-gage studs (particularly the 1 5/8" kind) are the pits; but, the heavy-gage 3 5/8" steel studs are fine. With the light gage studs, I kept spinning the screws (I was later told that you're supposed to use "clips" with the light-gage stuff - I've seen the clips, but don't have a clue how to use them). You're supposed to use a gasket along the lower track to stop drumming (flex from the floor above) and rattling - I've only done non-loading bearing walls and followed the instruction and didn't attach the the studs to the track in advance; BUT, did make sure that I put a drywall screw through the convergence of drywall, track, and stud. It was a little strnage to start, but I thought it was actually easier than using wood (light, cut with aircraft snips, straight, easy to find with the stud-finder, very quick with one person, and, no precise measuremenst are required).
*b WBA At Your ServiceDennis, Yes, there is a stud welder out there. The electrodes look like the BIG tongs for Saturday grilling. I have never seen them operate, only renovated jobs and seen the welded connection. They also have a punch that serves a similar purpose. Everyone I have seen around here uses screws. They do hold better than the welded connections I have noticed.
*If you are going to weld, it's hard to do with anything lighter than 18-gauge (burns right through). You also have to re-apply a galvanized coating to the welded areas (sprays are available). And undoing a mistake on a welded connection... well, you can see what that would be like to deal with. Spot-clinching machines are awesome, but just about cost prohibitive in anything but a production/factory environment, at least from what I've seen. They press the stud and track into a "nugget" that's tough to undo and leaves no profile to mess up your drywall and trim. I've used ring-shanked nails (Paslode, in my case) to attach plywood sheathing, but never in steel-to-steel connections. I still prefer to use screws for everything else (including roof decking). Some roll forming machines fix the profile problem by shaping the point of stud-track connection to remain flush and then rivet them together. However, I've chosen to work with what's most commonly available, which is still regular C-channel and track. My costs are already high enough, so more specialized products haven't made sense for me so far.
*screws go from the bottom up,they do take a second longer than wood, but they never pop.welding is for heavier gauge studs only, like stated above, a stud punch works mint but ya cant keep that lil bastard around when ya need it..they have legs i swear,I frame every thing with steel now even cross fur cielings with the sound straps keeps the noise from one floor from getting to another. the echo in a hallway comes from an older gun and thats life .Call me if you need a rocker next time i love steel!!!!!DID I MENTION I FINISH TOO..In 15/8 studs ive had luck with coarse thread screws no spin out maybe im blessed with a gun. The Rock..
*I have a punch, but find it hard to use for other than 25ga studs. The device that dimples sounds neat - anyone know who sells it?Dennis
*
My partner and I just sheetrock a house that was built by another contaractor. He used metal studs in the house. This had to be one of the worst sheetrocking jobs that we ever had to do. All the walls were 10' tall and the main hall way almost fifty feet long. Metal stud makes for a nice straight wall but it sucks to sheetrock. And the echoes were unbelievable. Metal studs should stay where they belong. In commercial construction.