will be doing a 25×30 free standing addition set away from a residence. my client suggested using a slab foundation in order to save money on the time and materials of framing the floor system. what are the pro’s and con’s of going this route & is the cost savings a noticable factor?
Discussion Forum
Discussion Forum
Up Next
Video Shorts
Featured Story
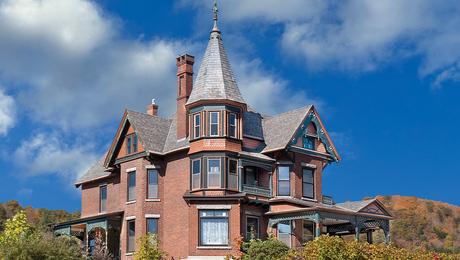
Fine Homebuilding's editorial director has some fun news to share.
Featured Video
Video: Build a Fireplace, Brick by BrickHighlights
"I have learned so much thanks to the searchable articles on the FHB website. I can confidently say that I expect to be a life-long subscriber." - M.K.
Replies
I did a 24x30 for my garage. Its called a monolitic slab. we do it all the time in south. proberly 95% of all slabs are this way
.
BOB thinks I,m an idiot
bb
I'm from Iowa and when garages are unattached they are done the same way. Its not just a southern thing.
Doug
I just know some area must be built below the freeze line,cannot help you there.. BOB thinks I,m an idiot
I'm certainly no expert, or for that matter not even real knowledgeable in the area, but even if there exists a frost line to contend with you don't(cant speak about all areas) have to put walls down to the frost line if its a unattached building, such as a garage or shop.
Just pour a mono slab as you showed. I was just mentioning this becasue you said "here in the south". We do it in the north as well.
Doug
I used to work as an industrial carpenter. We built many floating slab foundations for the various sized "out" buildings we constructed...many were bigger than the mentioned 25 X 30 that was earlier described.
Our foundations were usually 6inch thick minimum...and we always constructed a mat out of no.4 rebar. The rebar was laid 1ft OC and another layer running perpendicular to the first layer was placed on top in the same fashion and both sections were then tied together to form a mat.
We usually tied every other (rebar) cross-over joint. This mat was placed off the ground approx 2 to 3 inches using "chairs" that are made for this purpose. Brick will also work in a pinch but the chair method is better.
The frost line in my area is 3ft. When building slab foundations, we simply built right over the existing ground. It was mostly hard-pan gravel. Never had any problems with ground shifting or foundation heaving.
I placed my own garage (24 X36) on just such a slab. My ground was flat but had a lot of clay, and poor drainage...so I hedged my bet by digging a 3ft deep perimeter foundation ditch, and lining the ditch with heavy sized gravel. This is known as a rubble trench foundation. With french drain piping underneath the gravel, any water that seeps down next to the foundation finds its way into the french drains and the water is carried away from the site.
By eliminating water from the foundation site, there is little chance for the ground to freeze and heave upward. I then proceeded to remove the remaining topsoil inside my planned slab area, and added gravel and sand to this site and then compacted it. Next, I installed heavy mil plastic on top of the ground,and then proceeded to install my rebar mat.
Slab is nearly 8 years old and has remained stable throughout. Conrete was 6 inches thick in the center and closer to 10 inches thick around the perimeter ("turned edge" style floating slab).
As for costs you need to figure how thick you want to make your slab and then compute how many yards of concrete you will need to order and the associated cost. You also need to figure in cost of rebar, cost of backhoe rental, compacter rental, and your associated labor , plus cost of formwork and finishing.
Also, it is better to install a few courses of cement block and then frame your building on top of that; so as to keep framing from rotting due to high snow or rainwater. You will need to compute those associated costs as well.
Figure all this out and then decide which way is cheaper. A few years ago when I last built this slab, it was indeed cheaper for me to go the slab route, but cost of concrete and finishing labor keeps rising steadily, so I am not sure which way will benefit you the most in today's market.
Just my 2 cents.
Davo
Edited 3/27/2006 2:10 am ET by Davo304
If the area is very flat and there isn't much topsoil to remove then it would probably work fine. I considered a mono slab for my 24x32 shop, but the site has an 18" slope corner to corner, and there turned out to be 24" of topsoil, so it was easier to put it footings and walls first and then pour the slab second. I'd do a monopour in a second if the site were appropriate.
Pro: It's required by local code
Con: It's prohibited by local code
Edit follows.
Oops! You didn't say garage, did you.
In your specific area, I'ld have to move there and estimate labor and materials both ways to know how to answer that.
BTW, as long as you allow all those clients to estimate your jobs for you, you will never be able to forecast your cash flow.
Edited 3/26/2006 12:25 pm by SamT