I’m building practice spaces for bands. 2×6 plates w/2×4 studs 16″ oc offset @ 8″. Plans call for two layers 5/8 gb on both sides w/1/2″ ply wainscot. All framed up, lookin at an inspection tues. Planed on insulating wed. w/ rockwool bats in each bay on both sides. Question is: Does any one have an opinion about a blow in cellulose product and its sound dampening qualities vs. rockwool? I’m also trying to gauge time spent insulating. I have about 800 lineal ft. of 10′-12′ walls. Anybody? Thanks.
Discussion Forum
Discussion Forum
Up Next
Video Shorts
Featured Story
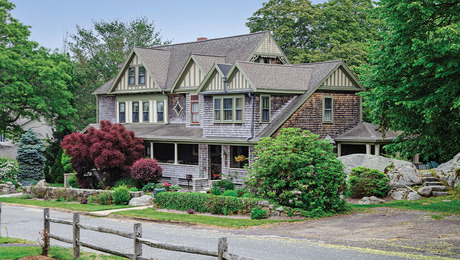
From plumbing failures to environmental near disasters, OHJ staffers dish on our worst and best moments.
Featured Video
Builder’s Advocate: An Interview With ViewrailHighlights
"I have learned so much thanks to the searchable articles on the FHB website. I can confidently say that I expect to be a life-long subscriber." - M.K.
Replies
Your plan for staggered studs is probably more important than the selection of insulation products -- although SOME type of insulation is critical.
You might also want to look into sound deadening panels that can be hung on the finished walls.
Unless you're the lead dog, the view just never changes.
i believe that cork insulation has very good acoustical properties, although i'm not sure if it is still available on the market?
cork insulation? As in rigid boards or loose fill?
I don't have figures, but denser is better, therefore in my opinion blown in cellulose would be better than rock wool.
Hanging the drywall on resilient channels will help, too.
Does this have to be sound-PROOF, or just very sound resistant?
For true sound-proof enclosures at the kind of SPL's a rock band can produce, you need to build a room-within-a-room.
Dinosaur
A day may come when the courage of men fails,when we forsake our friends and break all bonds of fellowship...
But it is not this day.
Staggered 2x4 studs on a 2x6 plate in an adjoining wall is a good idea. But it still leaves two physical connections between both rooms:
- the top and bottom plates, and sometimes,
- the floor and/or ceiling joists.
Better STC (sound transmission class) numbers can be had by building two walls, each with it's own plates and studs. Also remember to kerf the plywood subfloor. This hugely reduces sound transmission as it interrupts the solid pathway through which sounds, esp. base sounds, are transmitted.
Edit: I could have been more specific about the subfloor kerfing, which should be between the parallel bottom plates of the two 2x4 walls. In a kerfing prescription, best practice when laying out would be to place a floor joist under (or right next to) each of the parallel walls, making sure the joists don't touch each other.
'Noise control' calls for a couple beads acoustical sealant under each plate. The detailing is excruciating to say the least, but the manual explains it clearly enough. /Edit
Note that this approach does not help IF the floor and ceiling joists are perpendicular to the adjoining wall, and span both rooms altogether. Sound pressure will cause these joists to vibrate, even where they cross wall plates. A staggered joist layout, each with it's own bearing surfaces, would be helpful though.
It is also important to eliminate openings such as electrical outlets (esp. back to back ones), and shared HVAC ducting, etc. in the adjoining wall cavity.
Edited 6/19/2005 1:46 am ET by Pierre1
Edited 6/19/2005 1:46 am ET by Pierre1
In my work, building condos that are masonry with wood eye floor systems, minimizing sound transfer is a big issue and your advice with the two walls suggestion is right on time. I was really intrigued by your suggestion of kerfing the plywood subfloor. I see your point it seems like it would really help but I can't see how it would be structurally sound. Could you elaborate? We've met with sound engineers and it seems like isolating one area from another, completely, is the answer. We've used a heavy mat product between double layers of 5/8 drywall, and sound clips (I call 'em) an isolator mounted under the joist that holds hat channel (they make duct work isolation for a UL rating a real pain), cork or homosote on the floors between subfloor and hardwood.. Its my understanding that the nails and staples in a traditional wood flooring installation are a big culprit. There's a lot to it. And for us like I said its a big issue. So I'm always eager to learn a new thing when I can.
"but I can't see how it would be structurally sound. Could you elaborate?"
Learning certainly is fun...another reason why I am here.
If the floor joists are blocked where they bear and mid-span at appropriate intervals, and the sub-floor to joist contact is with adhesive and nails, the joist system is structurally stable isn't it? Double joisting on either side of the kerf would address load carrying concerns.
My suggestion comes from "Noise Control", a technical reference part of the Builder's Series published by Canada Mortgage and Housing Corporation. Product code: NHA 6012.
CMHC also publishes "Road and Rail Noise, Effects on Housing" (NHA 5156) and "New Housing and Airport Noise" (NHA 5185).
These technical bulletins are put together by the 'Institute for Research in Construction-National Research Council of Canada' in consultation with the Canadian Home Builder's Association. Very affordable, well illustratedf: great training aids for your crews.
Here are some of the problems identified (and resolved) in 'Noise Control':
poor floorplan layouts
drywall directly attached to wood studs on both sides
drywall screws are too long, short-circuiting the resilient metal furring
resilient metal furring between two layers of drywall (forming a small airspace) and solid connection of inner layer to studs
no acoustical sealant under sole plate
acoustical sealant not effective because of debris under the sole plate
unsealed back-to-back electrical outlets
porous, unfinished concrete blocks
no seal at foot of block wall finished with drywall
drywall too close to concrete blocks
holes or honeycomb penetrations in concrete wall
lightweight floor systems
poor sealing at edges of ceiling
no effective sound barrier in ceiling
topmost floor layer not heavy enough
floor contacting structure at edges
nails or screws penetrating the resilient layer to contact the subfloor or joists
flanking transmission along the top layer of a wood or concrete floor
transmission through floor into common cavity underneath
flanking transmission along single continuous layers of drywall on walls at right angles to party wall or floor
sound being transmitted through hollow core precast concrete slabs
drywall behind baths not extending completely to floor
bathroom cabinets mounted back-to-back on common walls
leaks around pipes; piping rigidly connected to walls
stairs attached to party wall
turbulence caused by high water pressure; excessive number of elbows and bends; water hammer shock waves
waste pipes installed close to quiet areas
bath, shower or toilet attached rigidly to the building structure
leaks around windows and doors
expansion and contraction of forced-air ductwork
Glad to see you are interested in building quality multi-unit structures where people can lead comfortable and stress-free lives, in privacy. Good competitive advantage and markup too, if well executed and your sales people convey the advantages to sales prospects.
Hey thanks a lot. I appreciate the help and reference
No problem.
I could have been more specific about the subfloor kerfing, which should be between the parallel bottom plates of the two 2x4 walls. In a kerfing prescription, best practice when laying out would be to place a floor joist under (or right next to) each of the parallel walls, making sure the joists don't touch each other.
'Noise control' calls for a couple beads acoustical sealant under each plate. The detailing is excruciating to say the least, but the manual explains it clearly enough.
I'll try and add the above to my first post.
Thanks.
Thanks to you too for bringing up additional sound issues as they relate to building structures. Thanks to ALL who chimed in. Stearno
Thanks for the insight. I really appreciate the discussion on this topic. Stearno
> Also remember to kerf the plywood subfloor.
Better still -- and what we did when we built a Foley stage in a crawl space building -- is to demo the entire floor system in the area of the soundproof room, and build the inside room completely independent of the outer structure, using slab on grade. Eliminating the crawl in that area gives you vastly better isolation, and as a bonus, you get more volume in the room, which is better for its acoustics.
-- J.S.
I bookmarked this site last time this topic came up:
http://www.quietsolution.com/index.html
Rebuilding my home in Cypress, CA
Also a CRX fanatic!
The crew starts on Wednesday of this week with the Quietsolutions "Quietrock" product in our remodel; for overkill, we're going to mount critical walls on RC channel as well. I'll be curious to see if it works (and slightly miffed it doesn't---each panel of "Quietrock" will cost me over $100 US dollars!).Our acoustics consultant is non-committal on the product; he thinks the RC channel will contribute more in the long run.We're also using blown in insulation (Icynene).Best of luck to you on your build!NotAClue
No-one's mentioned resilient bar (res-bar). It's a flattened Z-shaped metal strap laid over the first thickness of drywall (which only needs fire-taping) at right-angles to the studs, then the top layer if D/W is attached to that with short screws that don't pentrate the first layer. Normally the res-bar is at 16"o/c, but since you have high walls and all the D/W will be supported on one screw at those centres, I'd suggest dropping to 12"o/c, and perhaps supporting the bottom edge on some kind of foam or resilient material.
cheers
***I'm a contractor - but I'm trying to go straight!***
Resilient bar/channel/furring is also recommended in the 'Noise Control' reference book. However, placing the resilient channel between two dw layers lessens the overall reduction effect.
Best results are obtained when the resilient bar is applied directly to the studs (i.e., in a reno strip the wall down to bare studs). The drywall (preferably two layers back-to-back) is then fastened to the bar - avoiding long screws as you suggested. Doing so in each adjoining room gives better results
The idea is to hold a large dense mass away from direct contact with wall studs, so that this mass can vibrate without transferring the motion to the wall studs, and through them, cause vibration of the adjoining room's dw. The higher/denser the mass, the more sound energy/pressure it takes to set it to vibrating.
The website referenced by xxPaulCPxx (http://www.quietsolution.com/index.html) shows that this particular construction (two adjoining walls surfaced with 2 back-to-back layers dw mounted on resilient channel) yields very high STC numbers.
Edited 6/19/2005 2:11 am ET by Pierre1
Edited 6/19/2005 2:32 am ET by Pierre1
Thankyou Pierre. Ive only had a couple of occsions to do this - wrongly as it transpires, eh.cheers
***I'm a contractor - but I'm trying to go straight!***
a blow in cellulose product and its sound dampening qualities vs. rockwool?
I thought they were the SAME????
EDIT:: I thought the sound was better deflected on the SURFACE of a object.. NOT inside of the wall!
I could be wrong though...
Edited 6/19/2005 2:31 pm ET by Will George
for two layers 5/8 gb on both sides
Better to use 2@5/8 on one side and 2@1/2" on the other, so the two sides have different resonant frequencies.
Another thing might be to set the studs 16"OC on the 5/8' side and 19 1/8"OC on the 1/2" side.
Anything to give the two walls different masses.