*
Hi Don, check Fine Homebuilding July 1992, No. 75 page 100 for an article on bouncy floors by CMHC.
I also asked the same question several months ago, so is probably in archives. I got a copy of the research paper but as of yet have not tried anything.
Way too much to do and so little time.
Discussion Forum
Discussion Forum
Up Next
Video Shorts
Featured Story
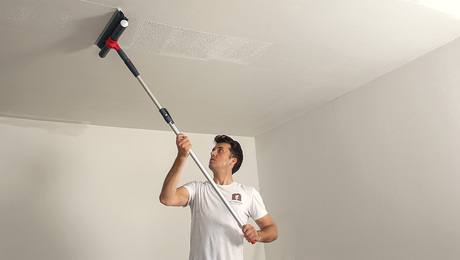
Skim-coating with joint compound covers texture, renews old drywall and plaster, and leaves smooth surfaces ready to paint.
Featured Video
Video: Build a Fireplace, Brick by BrickHighlights
"I have learned so much thanks to the searchable articles on the FHB website. I can confidently say that I expect to be a life-long subscriber." - M.K.
Replies
*
Hi Don, check Fine Homebuilding July 1992, No. 75 page 100 for an article on bouncy floors by CMHC.
I also asked the same question several months ago, so is probably in archives. I got a copy of the research paper but as of yet have not tried anything.
Way too much to do and so little time.
*
Hi Don,
The amount of stiffening that you would get from gluing a 2x4 to the underside of the joist would not be worth the effort. The concept is the gluing of the two would be stronger than the sum of the two.
Instead, for the same amount of work and money, install continuous blocking, the same size as your joists, every 4 ft. The amount of strenght you get will be equal to the quality of the fit of your blocking.
Gabe
*Hello Gabe.I agree with you. I might only add that using PL 400 with the new blocking will further add strength.Hope this helps.alan joseph [email protected]
*Gabe I'd like to agree with you but I think you are oblivious to the humanity involved in this whole blocking thing-wish I could explain but I have forgotten the answers- I'm sure splinter will be along soon and we will both feel better for it.
*
I have a cooky idea, but since I've discovered I'm a second-rate wood butcher, I have no pride.
Don't know the name for the header system (wood butcher), but I've appreciated its function. Two 2x4's transfering the load over the window or door into the king studs, by positioning them in a pyramid with the apex over the center of the opening.
Why couldn't a guy (or even a female, for that matter), use this approach multiple times down the length of the joist, similar to a truss? I imagine there would be some optimum angle for the 2x4 pieces to run in relation to the dimensions of the joist. Nail the shite out of them with a big hammer, and big nails.
Blocking is definitely inhumane. Especially to the guy (or gal,er.. female) who has to look at the results of a wood butcher doing it.
hackin everything I see, except my digits
N
*
i for the same amount of work and money, install continuous blocking, the same size as your joists, every 4 ft. The amount of strenght you get will be equal to the quality of the fit of your blocking.
Sounds like a lot of trips to the basement to me: a person could work her ass off and still not get the floor stiff enough. Or lose her ass bidding it improperly. Or install s.t. ass-backwards. Get her ass drug back to do s.t. else when it didn't work.
The joists are exposed. Sounds like a crawl space or unfinished basement. Why not use strongback/girder and post to ground, get a truly solid floor, if that option is available?
Boys?
*We don't do it your way because, we've done it before and you're an idiot.Gabe
*Hi Doug,I don't know if it's because it seems so easy to block because I've done so much of it or what.It's like the spars on an aircraft wing or the purlins on a steel structure to give it strenght without weight.We all know that wood is much stronger if it can be prevented from torquing. The two ways of doing this is to either sheath both sides or by adding blocking in between. If you sheath both sides, you are dependant on shear to prevent twisting. If you block, you are dependant on compression, which is much stronger.All I do is chalk line across the joists, every 4 feet and install blocks from one end to the other without breaks. I install the blocks alternatively left and right of the line to allow easy nailing. As long as the blocks are cut to close tolerances, the increase in stability will be dramatic.If you have a duct or pipe that interferes with the continuety of the blocking, you simply install a 2x4 on the flat at the top and bottom, leaving an open space for access. This ensures continuety, which is the key to proper installation.Gabe
*Hi Gabe.I am not sure about Splintergroupie's ideas, so maybe your response was appropriate. I dont know.But, it reminded me of a house I worked on. The houses around here are about 80-100 years old. The basement floor is about 2" of concrete over this layer of black cinders (I forget what it is called). And below that is mostly clay.Obviously, to us, this type of floor is not conducive to supporting much.Nonetheless, some crafty thrillseeker decided that, to solve the "bouncy floor" problem, he would just add a 3" steel post just under the joist, and directly on top of the old floor. I am supposing he thought the rust might keep the post to the concrete floor, I dont know.I will never forget looking at that basement, with all these 3" steel posts everywhere, actually holding up nothing, but causing the owner to slither like a snake between them to get anywhere.With some joist hangers I was able to get rid of most of the posts. And the posts that were needed got their own footer.Hope this helps.alan joseph [email protected]
*I forgot about the literal-mindedness here.Post-to-ground is an expression in these parts. (Would the hyphens have helped?) Ground indicates solid footing.Or are yers jus' havin' fun wi' me?
*Actually, the bottom skin on a wing is tensioned in flight- giving it the necessary stiffness....And flexibility with the top being in compression transmitting the whole works through the spars to the fuselage.S.
*And the opposite is true on the tarmack, however, the common denominator is still the spars. And your point would have been..........Gabe
*Hmm. I must be missing something here; If we to lash some plywood to the bottom of the joists wouldn't the plywood then be in tension (with the load on the floor above)? S.
*Sorry Sam,Your idea won't fly unless the top of the floor has more surface area than the underside has.Gabe
*Yes Sam. And the plywood in top would be in compression. They are very stiff assemblies. Its called a stressed skin. The Plywood Association has booklets with all the formulas, details, etc. Generally, having built quite a few stresed skin structures for special uses, I'd not recommend it as appropriate technology for most home building applications.
*You're butting in on a joke, speed.Gabe
*Well, I damn sure won't bother with the landing gear then. Sam
*Sam, don't quit on me now....Conner's not a pilot and tried to get serious.I want to hear about the landing gear connection.Gabe
*Gabe- I'm currently in communication with Simpson working on some special connectors. The only thing is, they're having some trouble with the fasteners I've specified. I told them that Teco nails were out of the question. -Sam
*Sam,very familiar with Simpson hangers etc but naive about Teco nails.I've never used the nails that come with the simpson hangers for Macmillan Bloedel silent floor systems. They were short galvanized nails that had no real holding power.enlighten me on Teco.Gabe
*Gabe- Well hell, you've called my bluff. That's just the term/brand name that I've always heard/used in reference to metal hanger/hardware stuff. And yes, you're right on about the no holding power issue, shear is about it for those things and I'm not so confident about that either- when they pull out. But we digress. Back to the landing gear issue. In order for these special connectors to work with said landing gear, there are going to need to be some big-ass fasteners powered by a big ass nail gun.... Like that one I saw the other day for driving studs/fasteners into structural steel. That thing was manly. -Sam
*Sam,I think the problem can be solved with epoxy embedded anchor bolts. I'd lean towards 1" diameter bolts about 12" long.I know that it would hold the landing gear alright but I don't think the wing can take the weight of the connections.Gabe
*
Here's a few ideas.
Run 1 x 4 strapping across (perpindicular) the joists every 4'. It has the same result as blocking with a h*ll of a lot less effort.
Sister lumber of the same dimention to every other existing joists thus doubling the thickness. Fasten with construction adhesive and screws or nails. Guaranteed to stiffen up any floor. Remember, crown side up!
Do both.
*
Ted,
There's no comparision between blocking and strapping. Two 2 1/2" nails have the shearing resistance of a pinch of coon shit.
Gabe
*I know Gabe buddy- done it more than once. I was poking fun at the antichrist-aka- splintergrouper...live long and prosper even if you are a Canuck...
*...not a good attitude, but his prop-osal might fly if the floor was bare,newly framed!Sorry for buttin in Gabe, I couldn't resist!!
*
isn't blocking every four feet redundant? If you have a 14' span, and block center, then there is 7' left sublject to torsion. I can't imagine at that point that what is happening is not to be overcome by adding more resistance to the joist folding, but adding resistance to the joist bending.
Have installed much fine and golden bridging on floors that had much deflection.
*
ISN'T BLOCKING EVERY FOUR FEET REDUNDANT?
too funny...
*
have personally been in on over400,000 sq ft of frame, and never seen bridging at four feet. Only four feet block detail I've seen is ladder block to tie rim to floor, and shear transfer for shear walls that don't stack. So, where is the joke, pal?
*
Teco nails are the same diameter as a 10D nail, but they're only 1.5" long. They're typically used in hangers where you are nailing into a single 2X member.
*Running a steel beam across, under all the joists, midway, with solid support under both ends of the beam is faster, easier and more humane. It will work as well as, or better than blocking. The biggest detractor is loss of overhead room if in a full basement.
*
The article I mentioned at the top of the discussion uses solid blocking with adhesive and a 26 ga. steel strap nailed across the bottom of the blocking. Something like the airplane wing idea??
*
of course blocking every four feet is redundant. so is blocking at midspan, framing walls. rolling joists, sheating floors, nailing off...EVERYTHING about framing is redundant
*DonSorry for the bit of levity earlier. There are some excellent "practical Engineering" articles on the JLC cd rom. Many years ago I took a mechanics of materials class and was able to calculate deflections, etc of composite beams. As you would guess, the fastening schedule is a critical part of the assembly acting as a unit.
*Gabe- Whoa! Those are some mighty, manly fasteners you're talking about. I agree though, it's a weight issue with those things not so much a strength issue. Now, if we increase the size of the engines, this monster might just fly. Where's the roto-hammer?Sam
*Sam,In 1909 a small group of aviation DIYs led by a fellow by the name of Alexander Graham Bell and financed by his wife, built a small plane of sorts, out of bamboo and wire. In that winter, over a frozen bay in Baddeck, Cape Breton, Nova Scotia, this small plane with a fellow by the name of McMurdy I believe, flew it for the first time in Canadian history. They went on to fly this plane over distances of 20 KMs and did so over 200 times. They flew the plane as a demonstration for the Canadian military and during one of the flights crashed it. Rumor has it that they being young men and full of piss and vinegar, were fooling around giving rides on the wing when it crashed.The military minds of the day, didn't think that the plane would be of any use to the military and approved an increase for the purchase of mules and horses.Gabe
*> In 1909 a small group of aviation DIYs> The military minds of the day, didn't think that the plane would be of any use to the military and approved an increase for the purchase of mules and horses.Of course, what good could come from the efforts of a bunch of DIY's!Rich Beckman
*Gabe- Point well taken. We really do have a future in Aviation, I'm not about to let anyone tell us differently. These naysayers are just green with envy that we'd take the initiative to "get this off the ground". As for those horses and mules, well, putting a stick of dynamite in a strategic location might do it, but otherwise better keep the farrier close at hand. Checkin' the weather patterns, Sam
*
I get it. redundant. I get it.
*
Something that I have wondered about, when you strap, or attach any additional members directly to the bottom of the joists with nails or screws, you are shearing or at least distorting some of the fibers at the bottom of the joist which are under the most tension. At what point do the addition of the fasteners weaken the tensil strength of the joists more than the straps add to the stiffness of the floor assembly?
*Geez Casey,figured out the meaning of life and you still had a little time on your hands?I don't know, a 12 inch spike aught to do it.Gabe
*Have used the strap approach (1/8" x 1-1/2" wide steel, prepunched and countersunk for wood screws) on 1 to 3 members (only) - tacked up strap, jacked slightly, screwed the strap to the joist bottom. Screw holes staggered slightly, 12" o.c. as I recall. Worked well in a small area where a dropped beam/headroom was an issue. Wouldn't want to do it for a whole floor area.Jeff
*Jeff,I've never seen it done but I like the idea. I'm suprised the fastening was only 12"oc though, there A LOT of shear along the bottom edge of that joist.
*
I read somewhere of a method of stiffening floor joists whereby a 2x4 is glued and lagged flat against the bootom edge of existing floor joists, creating an upside down "T" section. Is it necessary for the added 2x4 to have bearing at the ends, or does this added "bottom chord" work like the bottom chord of a floor truss?
Thanx for any input!
Don