I’m as green as the grass! And, I am general contracting the construction of our home. We are just about to install radiant heat pipes into the basement floor AS WELL AS on the main floor. On the main floor, we will cover the 1/2 oxy pex with 1 1/2″ of concrete. I want to finish the concrete on the main floor as my final surface in the entry, kitchen, dining room and perimeter of the living room. But one sub-contractor is saying it can be done if care and the proper additives are employed and another is saying it will be a disaster. Can anyone with experience please advise if this can be accomplished successfully and, if so, what are the requirements to do so.
Discussion Forum
Discussion Forum
Up Next
Video Shorts
Featured Story
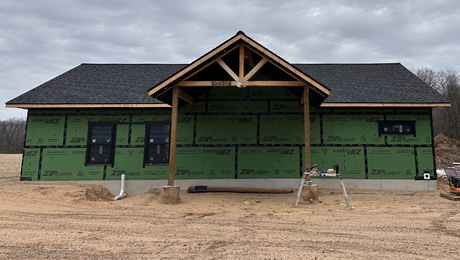
Listeners write in about earning trade-work merit badges and ask questions about radiant cooling, indoor air quality, and radon-control systems.
Featured Video
Builder’s Advocate: An Interview With ViewrailRelated Stories
Highlights
"I have learned so much thanks to the searchable articles on the FHB website. I can confidently say that I expect to be a life-long subscriber." - M.K.
Fine Homebuilding Magazine
- Home Group
- Antique Trader
- Arts & Crafts Homes
- Bank Note Reporter
- Cabin Life
- Cuisine at Home
- Fine Gardening
- Fine Woodworking
- Green Building Advisor
- Garden Gate
- Horticulture
- Keep Craft Alive
- Log Home Living
- Military Trader/Vehicles
- Numismatic News
- Numismaster
- Old Cars Weekly
- Old House Journal
- Period Homes
- Popular Woodworking
- Script
- ShopNotes
- Sports Collectors Digest
- Threads
- Timber Home Living
- Traditional Building
- Woodsmith
- World Coin News
- Writer's Digest
Replies
We use a 3000 or 3500 psi "small rock" concrete mix with super-plasticizer for
fast , high slump placement. And fibre mesh re-inforcement.
A thin overlay such as this is prone to random hairline cracking, as it
will dry out rapidly. Don't count on it remaining pretty.
"Wet" concrete contains many gallons of water, per cubic yard, and the concrete
will shink as it dries. That's the nature of the beast.
This will not affect its ability to become a radiator for you, however, and is a cheaper
medium than gypsum overlays, and readily available.
Apply ceramic tile, slate, vinyl, clic, or thin carpet for maximum heat transmission,
and enjoy warm toes.
A thinset colored and stamped overlay may be possible.
View contractors previous similar works, before you commit.
Edited 3/13/2007 12:23 am ET by ericicf
Sarah,
Yes, it can be done.
First you will need a really string floor, something on the order of L/720 or better.
Next, you'll have to have a good relationship with the Mix Master at your local batch plant. He's the one who will be engineering your concrete mix and he is the one who knows it the best.
I would want visqueen under the Pex so the 'crete doesn't dry out from the bottom and because you will have to be putting water on the floor for at least two weeks after it takes on its' initial set, and 4 weeks is best.
Keeping the 'crete wet/damp for that time frame is so that it will cure in a manner to minimise shrinkage and cracks. It will also give you much stronger concrete. You can use wet burlap, and wet it twice a day, or just mist it several times daily. Like every four hours, 24/14.
IMO, this should all be done before DW. A month or so before, so the structural lumber can dry out again. That means pouring the floors at least two months before drywalling. Buy a lumber humidity tester.
If you want good concrete, you must make concrete the master of your time.
I would suggest that you and the sub who sayshe can do it both meet at the batch plant and talk to them at the same time so you are all on the same page.
SamT
Anyone who doesn't take truth seriously in small matters cannot be trusted in large ones either. [Einstein] Tks, BossHogg.
consider gypcrete as an alternative to concrete..
http://www.maxxon.com/
http://www.durexcoverings.com/gypcrete.htm
Life is not a journey to the grave with the intention of arriving safely in a pretty and well preserved body, but rather to skid in broadside, thoroughly used up, totally worn out, and loudly proclaiming
WOW!!! What a Ride!
Forget the primal scream, just ROAR!!!
Sarah,
Eric and Sam T have it right. The advice to keep it wet is the best advice so far. Cover the concrete with plastic sheets, tarps, anything you can find and pour water onto it daily. Don't let anything dry out.
The concrete will still crack, so you want to make it crack where you want it to, rather than in some random location. Make shallow saw cuts across doorways, for instance. That will encourage the concrete to crack beneath the cut rather than halfway across your dining room. In theory, there should be no uncut area of concrete larger than 10' x 10', but you can increase that a great deal by puring the floor with a dry-ish mix, using the superplasticizer, fly ash, and by curing it as wet as possible as long as possible.
If you intend to acid stain it, keep it clean for the duration of the job or stain it and seal it before the rest of the job happens. Especially, keep drywall mud off it. It's hard to clean completely off concrete and intereferes with a good acid stain. Paint is even less fun.
When I did my own, I left the finishers late at night with lights and coffee and a mass of wet mud on the floor. When I came back in the morning, they had finished and gone. They had gotten on the floor too soon with the power trowel and left it with swirly marks and tiny curved ridges everywhere. I was very angry as I wanted a smooth hard finish. (And I had already paid them.)
I stained it anyway having nothing to lose at that point but a bit of time and it turned out far better than a smooth floor might have. The little bit of texture in combination with the random blotchiness of the stain is quite beautiful and now, I recommend a rough finish for acid staining. When I say rough, I only mean something less than mirror smooth; you can't feel these ridges.
Ron
Don't expect any guarantees from your concrete guy. This is a risky business at best. You may have perfect results and you may have random cracking based on a multitude of variables.
I'd pour and tile if it were my house.
Thank you all very much! It is so good to have such informed responses, especially considering that I live in a small Town and the ability to discuss these issues with contractors is significantly constrained by their amazingly busy schedules. Can someone, actually I think it was Sam T, advise what L/720 means? I live in Canada and we have a 5/8" plywood floor on 2 x 10 on 16" centre floor joists. I understand you to be saying that if our floor isn't strong enough to let go of our plan entirely. We are now thinking, after reading your advice, that we will meet with our contractor to review the practicality of our plan and, only if the contractor comes on board, will we then go to the batch plant to ensure their cooperation. Finally, we will accept that if the concrete doesn't cooperate in our plan (and cracks horribly) we will have a fall back plan of placing tile, lino etc on it. We are just realizing that, if we go ahead this will be a labour of love and we are OK with that but we are going to have to be pretty creative to figure out a way to keep this 900 square feet of floor wet for 4 weeks. Thanks again.
what L/720 means?
It's simple enough to explain, harder to do.
What that means is that the combination of subfloor, joists, etc. does not deflect more than 1/720th of the span. If you had a 720 inch span (60'), the most it could "flex" would be 1" (typically at the center).
The are some old construction terms/values, such as l/240 or l/360. The former being the maximum deflection before wood paneling cracks, the latter where plaster begins cracking.
SamT is recommenting a significantly stiffer floor assembly with radiant heat in a cementitious subfloor for several good reasons. One is the need for more stiffness with the additional material. Another is that RFH works best with complete contact of the radiant "mass" as possible. Yet another is that, if the "mass" material cracks in the future, it can make annoying and very hard to quite fix right noises.
Is your floor that stiff? Dunno. I'm a voice on the internet about 7-8000km south of you, and not at all an engineer. Your best bet is to ask a local professional to assess your floor.Occupational hazard of my occupation not being around (sorry Bubba)
Sarah,
What's the span of the joists? If they are under 12 feet long and have either solid blocking or daigonal bracing across them, you are fine.
That isn't a big floor to keep wet. With tarps to limit the evaporation loss, six or seven 20L buckets a day will do the trick. The first week is the most important period.
Where in Canada?
Ron
We are in South East British Columbia, 7 miles North of the border with the US.
Sarah,
I'm in NS, just outside Halifax
Ron
If your going to go with tile over the concrete, and are willing to wait a year before tiling, I would think that a L/360 is enough. Otherwise, shoot for L/480.
The year wait is to let the floor sag to near whereever it's going to before putting delicate tile down.
The reason for such a stiff floor (L/720) under exposed 'crete is to prevent any sagging/cracking.SamT
Anyone who doesn't take truth seriously in small matters cannot be trusted in large ones either. [Einstein] Tks, BossHogg.
The company I work for builds low rise apartment buildings and all the 2nd and 3rd floors are poured with gypcrete. This is for sound control and to ensure a level surface to install finished flooring on. They do not have radiant heat though.