*
Someone address the real-world issues of proper installation of welded-wire-fabric. Thank you.
Discussion Forum
Discussion Forum
Up Next
Video Shorts
Featured Story
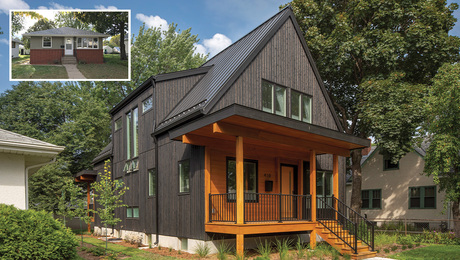
A small and dated house lends its foundation to a stylish new home with more than twice the space.
Featured Video
Builder’s Advocate: An Interview With ViewrailHighlights
"I have learned so much thanks to the searchable articles on the FHB website. I can confidently say that I expect to be a life-long subscriber." - M.K.
Fine Homebuilding Magazine
- Home Group
- Antique Trader
- Arts & Crafts Homes
- Bank Note Reporter
- Cabin Life
- Cuisine at Home
- Fine Gardening
- Fine Woodworking
- Green Building Advisor
- Garden Gate
- Horticulture
- Keep Craft Alive
- Log Home Living
- Military Trader/Vehicles
- Numismatic News
- Numismaster
- Old Cars Weekly
- Old House Journal
- Period Homes
- Popular Woodworking
- Script
- ShopNotes
- Sports Collectors Digest
- Threads
- Timber Home Living
- Traditional Building
- Woodsmith
- World Coin News
- Writer's Digest
Replies
*
if your going to install weld wire install it during the pour. this will allow you to push it down instead of walking it down. If on the other hand you have a concrete "come along" you can install it(the wire ) first. The pointy thing on the reverse side is to pull up the wire during the pour.
*Lary and Bill. In the real world Welded Wire Fabric (now called welded wire reinforcing) is installed incorrectly 99 percent of the time.See page 27 Welded-Wire Fabric in my book, Complete Building Construction, 4th Edition published by Macmillan Publishing Company. Pushing it down or pulling it up is wrong. It must be set on chairs so that it remains within 2 inches of the top of the slab. To do differently is to waste money. And if you use it because you think it stops cracking you are again wasting money. See explanation in my book. GeneL
*
Bill and Gene, thanks for the reply.
Gene, I call for W.W.R. to hold the concrete together when it does crack, and call for control joints to regulate the cracking. Is this the explation in your book? Thanks.
*LarrySee my question in this discussion: Cracking of new concrete slab for a thread on my daughter's problem with her contractor.He used 'Fibermesh' in lieu of welded woven wire mesh. One of his reasons was that "The concrete masons push down the wire when they walk on it during the pour and leveling operation."I'm stilling trying to determine if fiber mesh is a valid substitute for wire. When I asked the contractor for a copy of the local Building Code, which permits the fiber mesh, he confessed that it was not in the code.
*John, thanks for the reply. I read the thread on your daughters'house.Structural engineers tell me fiber reinforcing is not a substitute for wire.Fiber reinforcing is good for eliminating surface crazing. For serious cracking, the kind you describe on your daughters'house you need wire to hold the concrete in the same plain.If you use fiber it should be used with wire reinforcing.
*
Larry. Yes. I do go into detail as to why using 6x6-W1.4xW1.4 for reinforcing does not work. I also show different types of chairs and bolsters.
I also explain when WWR is necessary and when it is not necessary. When I was code Enforcement Officer I would not allow the use of WWR unles it was installed on chairs. Told them to get a mesh with wide enough openings to allow a foot to enter, and thus keep men off the mesh. the problems were always in residential construction. Never had these problems in commericial construction. GeneL.
*
Gene,
Your book,the publisher is out of stock and our library don't have a copy. Anyway I can download the info about WWR. Thanks.
*
Larry. By the bye. The WWI gang and the Portlanmd Cement Association disagree--even thought hey use the same formulas--about WWR. And unless they have kissed and made up since my book was published they still disagree.
Some of the things I did not discuss in my book were vapor diffusion retarders (VDR) where under the slab they go, the warning not to use sand under slabs and so on. Although there are some savvy people on this web page, most builders know next to nothing about concrete. I was just readoing about the horrorstoris of improperly placed slabs-on-ground in Florida. Any buildr dealing with concrete must subscribe to Concrete Construction.GeneL.
*Gene,What do you think of ....several inches of 2" stone and drains to daylight, poly, then 1" of foam board, then, 1-2" sand, then 4" 3000psi concrete with wire tossed in as you go into hlf layer pour.Jack
*Gene,What do you think of ....several inches of 2" stone and drains to daylight, poly, then 1" of foam board, then, 1-2" sand, then 4" 3000psi concrete with wire tossed in as you go into half layer pour...break with joints every 12'...Jack
*
Gene and Jack,
What do you think of 2" of sand, 6 mil poly, 4" to 6" of grandular fill on virgin soil, 1 1/2" x 2'-0" perimeter foam under 5", 3500psi concrete w/ #3s at 18" o.c. with control joints 30' max?
Hey, I learn a lot from you guys. Thanks.
*
Larry,
I like it...My 12' for control joints came from measuring the local Lowes floor....Smaller is better...
J
*Larry. why do you need 3 capillary breaks: poly, RFBI and gravel? Why both sand and stone? Are the rebars on chairs or bolsters? GeneL.
*Jack. Stone, poly, foam, sand, concrete is the order you listed. Oh yes, I forgot you are tossing in some wire. Problems. Why are you using 3 capillary breaks and two diffusaion retarders (VDR)?No matter how common is sand usage it is a NO-NO. Some say the sand layer protects the VDR, and also acts as a sponge to absorb excess mix water.It is argued that the sand allows bleed water to exit from the top and bottom of the slab and reduces the stresses that would exists if the slab were poured directly on the VDR.I agree with this, but disagree with the use of sand as the permeable layer.Sand is easily displaced by workers as floor is being poured. The displacement causes a non-uniform slab thickness. Heavy vehicles, say in a garage, cause the sand to shift beneath the joints. Dense graded crushed stone 4 -inches thick is a better choice.But what about the sungrade drag friction? The crushed stone can be ckoked off with stone screenings which fill the voids between the stones. This reduces the permeability but still allows the mix water to bleed off from the bottom of the slab. With such a subase there is no displament and hard and soft spots are eliminated.GeneL.
*Gene,I am looking for the "Golden Floor System" for basements and garages that are also used for a warm workshop occasionally in the winter...If you think you know what that would be, please help me out...Here's what I want...Soft floor for my feat, warm floor for my comfort, strong floor in strips for where the vehicle tracks in and out, a pit possibly for under vehicle work (a real extra), very easy to heat up and or not heat..very low use of fuel, sun energy is free...
*
Someone address the real-world issues of proper installation of welded-wire-fabric. Thank you.