A market share of 5% may not sound like a lot, but to Sam Rashkin, getting the Department of Energy’s “Zero Energy Ready Home” label on that many houses each year could be the tipping point for high-efficiency building in the U.S.
Rashkin, chief architect in the Building Technologies Office of DOE’s Office of Energy Efficiency and Renewable Energy, says the Zero-Energy-Ready (ZER) Home program is now entering its third year with improved prospects of turning small numbers into much bigger ones.
Like the Challenge Home program that preceded it, the ZER Home project is designed to move building innovations developed through research in the Building America program into houses that actually get built.
To date, about 270 builders have signed on to become “partners” in ZER, with 350 houses meeting zero-energy-ready certification requirements. But new interest from production builders–including those in Denver’s huge Stapleton development and from Meritage Homes–could extend the program to a much broader audience, Rashkin said.
“It’s kind of like gold mining,” he said in a telephone interview. “You’re finding little cracks and crevices and opening them up to be very productive.”
Finding the “sweet spot” in home construction
ZER homes are a step up from those built under DOE’s well-known Energy Star program, with requirements stringent enough to make them energy self-reliant, or nearly so, with the addition of renewable-energy systems. Certified houses would typically have a HERS index in the low- to mid-50s.
Builders can use either a prescriptive or performance path to meet the requirements. In addition, houses have to meet a number of other benchmarks aimed at water and energy conservation and maintaining health indoor-air quality.
The government’s target audience are builders already capable of producing Energy Star-rated homes who are ready to move up.
Jumping from Energy Star performance to something as rigorous as the Passivhaus standard is just too big a leap for most mainstream builders, Rashkin said. The ZER program offers a sort of middle ground–tougher than Energy Star with much better energy-conservation numbers but not so daunting as to become essentially unattainable.
“That’s the sweet spot for us,” Rashkin said.
Several advantages for builders
There are a number of ways builders benefit from participation, Rashkin says, but probably none as important as risk reduction.
Even builders whose houses simply meet current codes face risks they didn’t five or six years ago because the houses are better insulated and better air-sealed. With less thermal flow through roof and wall assemblies, Rashkin said, houses can’t dry out should they become wet. And tighter houses require carefully designed HVAC systems to keep indoor air healthy.
Participating builders have access to well researched “best practices” that minimize moisture and air-quality concerns, and they also pick up an important “market differentiator” that can be helpful in attracting buyers, he said.
It’s the country’s builders, not the buying public, who hold the key to making high-performance houses more common, Rashkin said.
“We believe the innovation comes from the providers who are the experts in their technologies and products,” he said, “so we believe that we”re working with the builders to take the proven innovations from the hub of innovations like Building America and showcase to consumers how much better an experience they will have living in the home of the future.”
Challenges for builders remain
Houses in the U.S. are largely built one 2×4 at a time on site by workers with varying degrees of knowledge and skill, but the industry has moved far beyond that model elsewhere. In Scandinavia, for example, highly insulated and air-sealed components are built in factories with virtually no waste, and assembled rapidly on site.
That’s the rule rather than the exception, but change hasn’t come quickly to the U.S. home-building industry.
“The housing industry is perfectly suited to actually miss innovation,” Rashkin said. “It’s about 80,000 builders working independently and you don’t have the primordial soup of engagement and interaction and sharing and working together that you get in industries that are much more consolidated.”
Builders who do make the transition to much more rigorous building practices–“admittedly a heavy lift for a lot of builders”–face marketing and sales challenges that rival those on the technical side of construction because they don’t know how to sell homebuyers on features that aren’t obvious.
“If you can show off the granite counters and the large master suites and the three-car garage, you’re kind of getting it done,” he said. “It’s much more difficult to sell what you can’t see, and add clarity to something that is admittedly a little bit complicated. Health, durability, comfort, quality–those are all things you can’t see.”
On the construction side, there also are hurdles to cross: how to increase the R-values of wall and roof assemblies, how to save water with hot-water distribution systems, how to get air ducts inside the conditioned space.
All of that makes the collaborative nature of the ZER program, including online access to the DOE’s Solution Center so important, Rashkin said.
Getting houses built correctly in the first place is more important than installing renewables that would make them truly net-zero-energy performers.
“You can always add on a solar-electric system,” Rashkin said, “but I can’t change the wall construction and the wall tightness and insulation. I can’t change the windows. I can’t change the comfort system. I can’t change the plumbing system. What you want to do from our perspective with the [ZER] labels is nail down those 200-year opportunities.”
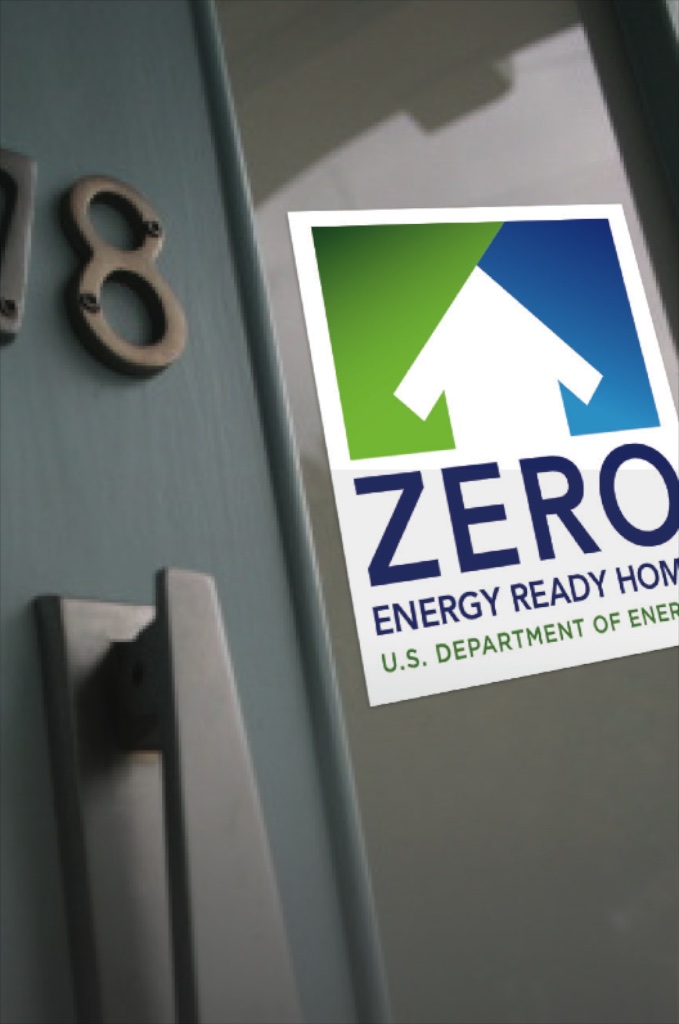
The Department of Energy's Zero-Energy-Ready Home program is designed to encourage more high-performance building. Program leaders are shooting for 50,000 homes a year by 2020.