I will be installing trim in a few ICF homes…never done that before. Any suggestions for stuff on the outside walls?
Discussion Forum
Discussion Forum
Up Next
Video Shorts
Featured Story
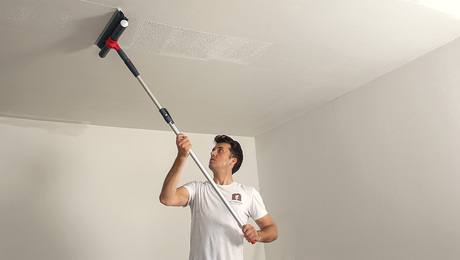
Skim-coating with joint compound covers texture, renews old drywall and plaster, and leaves smooth surfaces ready to paint.
Featured Video
How to Install Cable Rail Around Wood-Post CornersHighlights
"I have learned so much thanks to the searchable articles on the FHB website. I can confidently say that I expect to be a life-long subscriber." - M.K.
Replies
bump
Thanks for the bump...looks like it worked.
no problem.
hope one of those ideas works. The cris cross nails & power grab sounds good, but lots of holes to fill and power grab ain't cheap .......
i've done one and it was a challange. i have heard that some guys hold the sheetrock back 1 or 2" and you can screw on a 1/2 nailer board then your ready to go.
we used a lot of glue and nails into nothing,i wasn't impressed,but it hasn't fell off yet. thats a lot of help, larry
if a man speaks in the forest,and there's not a woman to hear him,is he still wrong?
Larry and ALL,Thanks for the tips...kinda what I suspected. The nailer sounds like the way to go.
Powergrab, and criss cross nails.
For a tall profile base, you may need to cut rock and screw in a 1/2" filler first.
basswood
first you need to figure out what ICF's you are working with. For example on the reward forms I used the screw strips are every 6 inches.. You could either use long trim head screws or screw nailer strips to the ICF's and work off of them..
What I did when I wanted a whole wall of raised hardwood is I went to a local sawmill and bought thins.. any board that is less than 1 inch thick is too thin and usually winds up in the scrap pile I can buy a tailgate dragging load of thins for $20.00 sort them out to a standard thickness and screw those thins into the walland you now have a solid nailing surface for less than $20.00 A lot cheaper than plywood and much easier to keep track of where the screw strips are..
Personally, the most challenging sections are around windows and doors where there is far less material to get a solid hold into. The doors also are a common source of headaches as the pressurre treated buck the door is attached to shrinks. If the buck is bolted to the concrete the buck will loosen in all directions.
Often the trim helps stabilize a questionable door install, but with not much but foam to attach to, there is more of a chance the door will move your trim/window joint. The painter will point fingers at you and you'll have to point fingers at the door installer, who will point fingers at the foundation guy who installed the pt bucks, who won't have to point fingers because everyone has forgotten about his sorry ars by this time.
Don't be bashful about adjusting doors and shimming door bucks so they are solid. Worst case you'll need to reinstall the doors and run additional tapcons through the bucks and into the concrete.
If you have a loose door and really don't/can't get the door off to get to the buck, hammer in something like a 1-1/4" 16g simpson strap between the concrete and buck at the point where it's bolted/screwed. Drill a smallish hole (the bit for tapcons works well) and force as much poly foam into the space as possible. keep the foam gun in place so the stuff will work into the gap and fill as much as possible with liquid rather than just turning to foam. It dries awfully hard when applied this way.
You aren't going to get wide, wavy casing or base to behave and should be careful if your materials are questionable. If you have a stubborn section of paint grade and really need to suck a section in, try some small diameter 4" to 4-1/2" screws, hammered into a drilled hole much like a ringshank. Once in a while that will save the day.
For most sections of base you'll have to be happy with cross nailing or coming up with some method of easily locating the plastic ribs in the block. The ARXX block nylon ribs hold nails or screws fairly well if you can find 'em.
One thing that often surprises trim guys is the quirk of not having stud protectors over pipes and wires. There aren't studs in the normal way and many inspectors allow wires and pipes to sit right under the rock with no protection. If you can get to the house for a quick look before it's rocked you'll sleep better. We have 16 g x 4" plates cut to protect pipes and whatnot that we otherwise wouldn't have a way to avoid.
If you are doing stain grade work and need extra backing for nailing you might have to remove some sheetrock under the trim and tapcon on some plywood.
Hand rails are a bit harder to mount, but not much. Lay out the handrail and blue tape around the rail brackets on the ICF wall. I like to cut a hardwood plug slightly less than the diameter of the rail bracket and deep enough to span from the concrete to the bracket. PL or spray foam and a few tapcons will hold the plug, and provide a solid surface to screw the bracket onto.
Be careful of outside corners, because there is even more foam and less concrete or ribs there to attach to. Most outside corners are molded with a radiused corner. If you are used to a nice solid corner to nail to, it might take some getting used to for there to be nothing but air in that space. If it's important to be able to nail into something you might try a corner block inset into the corner. A triangle is easy to fit since it only requires a straight cut across the corner. Nails from each direction hold it solid so it doesn't even need to be attached to the concrete. I'd fit it, foam it in place and use some construction adhesive when you are ready to install the base. Probably better to simply glue the joint, caulk to the wall and use a lot of nails where you can.
Good luck!
Beer was created so carpenters wouldn't rule the world.
I don't like the sound of the shrinking door bucks.Is is possible to use regular lumber there and create a moisture barrier between the white wood and ICF? Bob's next test date: 12/10/07
It's perfectly okay to separate the bucks from the concrete with something like ice and water shield. However, the bucks are put in place before the pour to hold the concrete back so it takes some work to keep the ice and water on the wood yet not in the way. The ice and water has to be stapled so it doesn't sag or pull off the buck before the concrete.
The next obstacle is feeding all the rebar around the door and window openings without snagging and tearing the ice and water.
Another minor issue will be the poly foam used to seal gaps in the forms and to some extent support the cut ends around openings. The foam won't stick to the ice and water so some areas that normally stay together during the pour with nothing but foam will now need an extra plywood "stich" to prevent a cut end from giving out and leaking concrete.
I first learned to use j bolts to bolt the bucks down and it was just a given that prior to hanging doors the nuts were given an extra twist. J bolts just don't support the buck over a wide area and anyone who suggests 20 J bolts per window will solve that problem don't realize how time consuming/expensive that can be.
Then I started using tapcon screws after the concrete had hardened but before the wood dried out too much and began twisting or separating from the concrete. It provides support to prevent twisting, but is probably more time consuming than need be.
The last year or two I've become a fan of simply running coated deck screws into the buck prior to pouring concrete. It's quick, holds the buck in a predictable and stable way, and has been trouble free so far. Three screws every 16" can be placed quickly by the least experienced person on the crew.
I think we'll see reinforced high density structural foam boards for constructing bucks that don't shrink, insulate the opening and can be bonded to the foam of the icf's. The ARXX vinyl buck material currently available is questionable at best.
Good building!
Beer was created so carpenters wouldn't rule the world.
I used Grace Iceand Water on the backs of my bucks . I wraped three sides and stuck it into the form . Also ripped the 2xs so that they were a tight fit before wraping with I&W. I did not have a problem with that stuff unsticking itself.