What is the likelihood of asbestos content in the insulation board used in a built up roof, done on a light commercial project, back in about 1982?
Discussion Forum
Discussion Forum
Up Next
Video Shorts
Featured Story
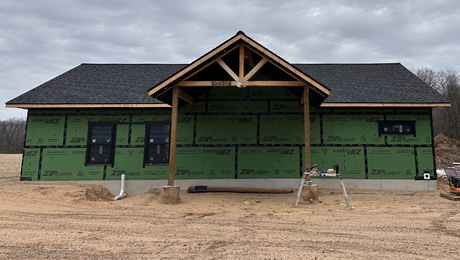
Listeners write in about earning trade-work merit badges and ask questions about radiant cooling, indoor air quality, and radon-control systems.
Featured Video
How to Install Cable Rail Around Wood-Post CornersRelated Stories
Highlights
"I have learned so much thanks to the searchable articles on the FHB website. I can confidently say that I expect to be a life-long subscriber." - M.K.
Fine Homebuilding Magazine
- Home Group
- Antique Trader
- Arts & Crafts Homes
- Bank Note Reporter
- Cabin Life
- Cuisine at Home
- Fine Gardening
- Fine Woodworking
- Green Building Advisor
- Garden Gate
- Horticulture
- Keep Craft Alive
- Log Home Living
- Military Trader/Vehicles
- Numismatic News
- Numismaster
- Old Cars Weekly
- Old House Journal
- Period Homes
- Popular Woodworking
- Script
- ShopNotes
- Sports Collectors Digest
- Threads
- Timber Home Living
- Traditional Building
- Woodsmith
- World Coin News
- Writer's Digest
Replies
It is possible, unlikely though. Asbestos was still allowed to be sold then.
I can't say about the insulation board, but we commonly used asbestos based tarpapre for the BUR roofing back then, esp in commercial work.
Welcome to the
Taunton University of Knowledge FHB Campus at Breaktime.
where ...
Excellence is its own reward!
Unlikely that asbestos is in the insulation board. It's probably brown fiberboard, maybe with some pearlite, or polyisocyanate foam. The built-up roof may contain asbestos, and the flashings at the perimeter and penetrations are very likely to be ACM.
In NY, an asbestos inspection is REQUIRED before any work that could disturb suspect ACM is done.
Edited 5/21/2009 10:14 pm ET by Southbay
Who must perform the inspection?
This question of mine stems from a re-roof scope for a building, our local arts center, which needs to have its circa 1982 BUR replaced.
What is there now is a relatively thin layer of board atop the steel decking, then the BUR, and that has been repaired and patched over the years.
We can get a full manufacturer's warranty for the Carlisle or other membrane roof system we are considering, but only if we strip to the deck. We want to put rigid foam board down to achieve R30.
Our question was whether we could save money as regards asbestos abatement by leaving the existing board down, and going up from there. What we would lose is the full warranty from the membrane system maker.
We can go up there ourselves and cut sections to sample every type of potential ACM, then send them to an approved lab. Is this legit?
View Image
"A stripe is just as real as a dadgummed flower."
Gene Davis 1920-1985
We can go up there ourselves and cut sections to sample every type of potential ACM, then send them to an approved lab. Is this legit?
It is here.
Our question was whether we could save money as regards asbestos abatement by leaving the existing board down, and going up from there. What we would lose is the full warranty from the membrane system maker.
Check for another manufacturer. You're probably getting prices on Carlisle and rebranded Carlisle. What you're proposing is allowable under some warranties, but the membrane must be vented. Not the roof, but the membrane only to release any build up of bituminous outgassing that might deteriorate the membrane from below.
All that being said, get a sample checked before moving ahead. You'll have a better system if it's stripped and there may not be any asbestos in the roof system.
edit: I'm assuming you're looking at EPDM. I'm not sure how TPO and PVC react to the bituminous outgassing. Might be worthwhile to look into those products.
http://www.quittintime.com/ View Image
Edited 5/22/2009 10:49 am ET by seeyou
"We can go up there ourselves and cut sections to sample every type of potential ACM, then send them to an approved lab. Is this legit?"No. Unfortunately, for you, a certified NYS Asbestos Inspector must collect the samples, even for non-friable roofing. The samples must then be analyzed by a NYS ELAP approved laboratory. You want to leave the board down, but remove the existing built-up? You need the inspection if in any way you could disturb the existing materials. So, basically you must have the inspection done. I would do it right. Remove everything, add the R30, and get your warranty.How far upstate are you? I'm on LI.
The initial thought was that the board may be the only component in the existing roof that was ACM, thus the thought to strip all else, leave the board (which is thin), then go R30, membrane, flash, curbs, etc.
We would not get the full from-the-manufacturer warranty, but we would avoid the costs of abatement.
That was the thought.
Now, it's sure sounding as if the board is a non-issue, or very likely a non-issue, as far as being ACM.
The demo component in our quotes includes removal and disposal of the board, but no asbestos abatement. We've guesstimated a contingency for the abatement, if needed.
From what you have advised, asbestos, if we've any, is going to be in other components of the roof, and we are best advised to get a certified NYS inspector to do the sampling.
Furthermore, if it goes as you are thinking, the board removal is a no-brainer, it will get demo'd, so our new roof will begin from the steel deck, and we'll get the full Carlisle (or other) warranty.
View Image
"A stripe is just as real as a dadgummed flower."
Gene Davis 1920-1985
Yes, you are required by NYS regulations (12 NYCRR Part 56) to have all materials tested.
http://www.labor.state.ny.us/workerprotection/safetyhealth/sh56.shtmDown here, a lot of the asbestos contractors also do regular (non-asbestos) roof rips. Asbestos in roofing doesn't add too much more to the cost of a regular roof removal. As per what Pedro said about going over everything; certainly this has been done, but there are several concerns: trapped moisture in the existing, the additional weight, the warranty...
Edited 5/22/2009 2:27 pm ET by Southbay
Hi Southbay,
As per what Pedro said about going over everything; certainly this has been done, but there are several concerns: trapped moisture in the existing, the additional weight, the warranty...
Oooops.....should have mentioned.....the roof support was more than adequate for the 1/2" backer board......that particular building of mine has steel painted trusses and galvanized panels so any minimal moisture that was trapped should not cause a problem....we also had the advantage of doing this during our drought a couple of summers back so I suspect is was pretty dry by the time we sealed it.
Got a full warranty contract on it with no exclusions.
Pedro the Mule - Still dry inside
"so any minimal moisture that was trapped should not cause a problem...."One of the biggest problems for new roof membranes is minimal moisture that is trapped under it from opld leaks.Hot weather and sun turns it into vapour, and the resulting vapour pressure can lift a bubble as large as a VW Beetle in a roof. Then the wind catches it.in gene's case. CU explained the venting of vapours and gasses from an old roof
Welcome to the Taunton University of Knowledge FHB Campus at Breaktime. where ... Excellence is its own reward!
Hi Piffin,
Hot weather and sun turns it into vapour, and the resulting vapour pressure can lift a bubble as large as a VW Beetle in a roof. Then the wind catches it.
in gene's case. CU explained the venting of vapours and gasses from an old roof
Ahh makes good sense........well I guess I got lucky.......haven't had a bit of trouble with mine.......this will be the third summer but I will keep that in mind.....got three guys wanting me to go in with them and buy an old vacated wally world.....that's about half of the building and the whole thing is vacant....enough age that I'm sure it'll need a new roof.
Hey I saw a message from you a couple of days back but everything after about message 45 has continuously been deleted.......sorry I missed it.....
Take Care,
Pedro the Mule - Luvin' the new company next door
Pedro, oh no doubt you did the right thing for your situation. Just pointing out common pitfalls of going over an old roof, particullary if the roof contains asbestos.I also see a lot of carpet installed over asbestos floor tile, and even new tile over asbestos floor tile. Later, when you pull the carpet, you pull up the ACM floor tile. The old tile often telegraps through the new tile. So when you look down a hall or classroom, you see the old tile pattern under the new tile. Then when the new tile needs to be replaced, you have more asbestos waste. Because you can't separate non-asbestos tile from the old. Many times, budgets mandate options.In my opinion, it's best to do the job right. That said, money spent for asbestos removal is often viewed as just a huge expense that doesn't add value to the finished project.Unlike you guys who offer a finished product, my services don't "show". It isn't easy.
Hi Southbay,
In my opinion, it's best to do the job right. That said, money spent for asbestos removal is often viewed as just a huge expense that doesn't add value to the finished project.
I completely agree.....we had a walkout basement in an old commercial building that housed all of the ancient boiler equipment. When it came time to replace the heating plant, I went with an outside unit, self contained. All of the pipes within the boiler area were covered in asbestos as well as the boiler unit itself. The way the guys removed the stuff and contained it was fantastic......triple doorways with air showers, wet showers and disposal area's etc. When they finished I would have eaten off the floor. I converted the space into usable offices and rented the space out, recovering all of my original expenses and later selling the building making a healthy profit. It was the right thing to do for all.<!----><!----><!---->
However, for the roof on another office building, I didn't want to give up any of the existing R-Value if possible. I don't know if that roof had any asbestos in it or not. Considering the general use of material, probably not but can't be certain without proper testing. But, it is completely encapsulated and works flawlessly. No blow offs, no telegraphing, full warranty so the best choice for me with the re-roof over existing was the right thing to do in this case.<!----><!---->
Yeah, I've seen some of the flooring that's been gone over....cheap vinyl over nice asbestos containing linoleum....the cheap vinyl takes on a nice pattern haha. That is also a nice point that you make about extra landfill due to unnecessary doubling of disposal once the job has been done right....sort of the green effect to do it right the first time.<!----><!---->
<!----> <!---->Pedro the Mule - Safety must always be considered a priority
Hi Gene_Davis,Our question was whether we could save money as regards asbestos abatement by leaving the existing board down, and going up from there. What we would lose is the full warranty from the membrane system maker.
One of my commercial buildings had a roof that was beginning to leak and already had polyiso panels of R26 in place.....I didn't want to give up what I already owned.....used 6" screws through 1/2" backer board then 4" new polyiso foam in place with membrane over that (as opposed to the 7 1/2" they normally use in this area). There's not likely to be any trapped moisture or condensation as the top layer is foamed in place sealing off everything.
The cost of extra materials and labor for the add on makeshift decking was about equal to what I saved in new extra foam but the savings came in by not having to remove and dispose of what was already in place.
Pedro the Mule - I was green before green was cool
It's my understanding that most asbestos was removed from building products in 1978I believe that technically, it was never banned, but levels were set incredibly low.wait a minute - it's way more complex than I'd learned.... http://www.epa.gov/asbestos/pubs/asbbans2.pdf
Weirdly, all the EPA etc real estate disclosure laws/brochures use '78 - but it sems that was just for sprayed on asbestos stuff...
"Ask not what the world needs. Ask what makes you come alive... then go do it. Because what the world needs is people who have come alive."
Howard Thurman
http://rjw-progressive.blogspot.com/