*
Maybe I’m a little picky about the materials that go into my jobs, but I don’t even leave the culls out in the weather. I also send back shipments that I think are substandard (I set the standard)! As someone aptly pointed out on another message, the contract, usually written by the “contractor”, is interpreted in the clients favor if there is an ambiguity. I wouldn’t pay the man another dime until he replaced those I-joists. Read the manufacturer’s recommended care and feeding of his product. Did you give the contract to the “really” low bidder? Did you check out his previous jobs, clients? Am I being too nosey? Hope you get it resolved (in your favor). Comments?….. Ralph
Discussion Forum
Discussion Forum
Up Next
Video Shorts
Featured Story
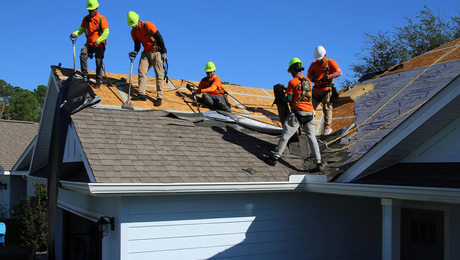
Listeners write in about haunted pipes and building-science tomes, and they ask questions about roof venting and roof leaks.
Featured Video
SawStop's Portable Tablesaw is Bigger and Better Than BeforeHighlights
"I have learned so much thanks to the searchable articles on the FHB website. I can confidently say that I expect to be a life-long subscriber." - M.K.
Replies
*
Seems to me there's an additional question: if the framers are mis-storing the material, letting them bend (which I understand is a major no-no with I-joists, but I don't have any expertise here), what is the quality of their work?
I'd be sure to (i) get some pictures of the I-joists as "stored" (from a distance and close up (get lots - what's the cost of a roll or 2 of film?) (ii) check with the local building inspectors - they _might_ have some concerns here, and (iii) check with the manufacturer of the i-joists.
It is _possible_ that the structural integrity of the joists has been compromised by handling/storage.
BTW, I'm not a regular here, so I can't speak for the community, but it seems to me that your question was entirely appropriate, and that Mr. "oooops" was a bit cranky in his complaints.
Bob
*
I agree with "Mr. oooops".
Chris:
Drive by 10 construction sites that are in the framing stage and make a tally of how many have the lumber covered and properly stored. Let us know what you find out. While I gotta admit that the treatment of the I-joist you described is a little flagrant, the # of folks out there that will treat your lumber like they had paid for it are in the minority. That's the reality of it.
Did you stack and cover it yet? If it were my house, I would have rectified the situation when I first saw it. If it is to be a trussed roof, be prepared for the trusses to be treated badly too!
On the other hand I don't think that this kind of operating practices are representative of the guys on this form.
* Chris,
Joseph Fusco View Image
*Have to agree with all the above. As Blue would say, he put's it up to fast for it to get wet.b have to go with joe about the price issue?????
*Progress update: I talked to the builder and he remedied the situation with tarps and specific directions for the framing subs. The 1st floor joists are in now, the floor is level and all the joists look straight, although I didn't break out anything as precise as a laser beam -- that would probably be overkill. Some cost figures:Living space: 2-story, 2766 SF, with vaulted ceilings in 3 bedrooms and 2-story vaulted family room. Very complex hip roof. 6:12 pitch.12" 600-series BCI joists; 2x4 walls, finger-jointed Doug.Fir; plywood sheathing roof & floors; floors glued & screwed; OSB sheathed siding.Lumber package: $20,437 Framing labor: $10,949Roof Trusses: $4,031
*If I may ask a few questions?1 Why the 2x4 walls? Around here most of the walls now are 2x6.2 You list finger jointed Doug fir, is this the wall studs?3 what OSB/plywood are you using? (ie 1/2" for wall and 3/4 for floor...ect ect) A quick trip on the math and it sounds like your getting a bargin. With the price on the labor less then $4.00) it sounds like you got what you paided with the framing crew. I'm basing that on my area here.
*Chris,Lots of good things said here. Like JJ, I really don't see what complaining to us is going to do about solving your problem. It now seems that you have worked out something with the builder. Good for you. Don't be shy, it won't get you anywhere.I haven't seen a house yet that didn't get soaked with rain at least a few times before it was dried in. I don't see too many houses falling down because of that.I agree with what has been said.......if you see something that you feel needs to be done either do it yourself (like covering the lumber with plastic) or call your builder and raise a ruckus. If something is bothering you......it should bother your builder. If you went with the low bid.....well......you get what you pay for.Good luck, and don't let up. You'll be sorry later if you do.Ed. Williams
*Bill:Just as an FYI, you very rarely see anything but 2x4 walls here in NC - even on upper end houses.
*1. energy code here requires 2x4 walls if nat.gas or better; else 2x6. I live in the very mild climate of Puget Sound. Coldest temperature I remember in 10 years is about 25 deg. F. Typical winter 40-50 deg. Typical summer 70-80 deg.2. Finger jointed wall studs.3. 1/2" wall, 3/4" floor, 5/8 roof.
*Jim;Reading the original question, he was asking if storing materials in the rain was a problem... I think that was a legitimate question.Speaking of which, what is yours?Chris had a perfectly legitimate question in his post. Is my material being damaged or will it straighten out and should I pust it with the builder. To my reading of the posts, you are the one taking out frustrations on Breaktime...but I'll "excuse [your] ignorant ass" as you requested in your post.
*Chris,Around here the track guys are getting about 4.50 a sq. ft. labor for framing. Highend is getting from 7.00 to 10.00. It sounds like you may be getting what you paid for.Rick Tuk
*GACC,I am a lot more careful these days about letting houses get wet. I had to replace about have the subfloor in an existing house that was about 30 years old. All the plywood was delaminating. It was the origional owner. He said that that end of the house had gotten very wet during construction (they didnt have windows in or something). Origional builder had told him it wouldnt hurt it was exterior plywood. Crawlspace was dry and well ventilated. When we pulled up the floor there was mold and fungus under the tarpaper. Plywood was delaminating. Since that his wife who has alergey problems has been so much better it is unbelieveable. A job cant always be dry but I do my best to keep it dry as possible.Rick Tuk
*Chris - I have been working in the Puget Sound region since the late 70s. It has always bothered me, the way lumber is exposed to water here. Most lumber yards don't even have roofs over the framing lumber (and summer sun is just as destructive). Your fears are well founded. Lumber and tjis should not only be kept as dry as possible - just as important is the way it is stacked. One thing you could do to help is once the framing is done and roof is on, open all your windows and get some big fans to get as much water as possible out of the framing before insulating and drywall begin. This is a rough time of year to begin a complicated framing job around here, things are gonna get real wet. Get it dried in as soon as possible, then slow down and allow everything to dry out. It will pay off in the long run. Hey - are those DFir fingerjointed studs kiln dried? - jb
*What's the best way to remove moisture later on?I spec'ed KD lumber, hopefully that's what I'll get. Although I wonder what good kiln drying does if the lumber is going to be thoroughly soaked by our rainy winter?I like the "big fans" idea to remove moisture.Another idea: how about closing up the house completely (windows, doors, etc.) and installing some temporary industrial-strength dehumidifiers? What do those things cost to rent, anyway?
*Adam, I appreciate the fact that there are more readers like you and less readers like Mr. Ooops!My original question was truly from an engineering point of view.
*I've never seen, or used, a dehumidifier, but that might work. I know if you close up the house and crank the heat up, the moisture doesn't leave as fast as with everything open though. Once lumber has been kiln dried, it can take a lot of surface water without moving. But if it never has reached - say 20% - it will move a lot as it dries, that was what used to happen years ago with DFir, and many carpenters argued that KD Hemfir was better framing lumber for that reason. You think discussions get heated here, hooeee, you should have seen those guys go at it over coffee. I believe they HAVE to KD all finger jointed stud material to get the glue to bond right. That is supposed to be one of the benefits of that stuff, that it remains stable. You should be OK, I was just curious as I had a bad first experience with finger jointed studs.
*Chris, I have to agree with "crazy legs". It's going to be to your advantage if you can slow production once the structure is "dried in". Having the heat on for a week before it is insulated will help it dry. You can rent dehumidifiers from 40 rentals, but I don't know if they will be effective before a ceiling is in place. We use them quite often when we have a high moisture content in subfloors prior to a hardwood install. Check with your builder to see if his schedule will allow for a couple of weeks for drying out. Your framing labor if viewed by the sq/ft is the going price for So.King Co., maybe under if the roof is very complicated. I hope your new home turns out to be everything you expected.
*I see the homeowners are still worryingabout things that are almost irrelevant. The joists were obviously stacked tight, prior to the construction process. The framers cracked them open and it started to rain. They went home, and returned the next day and installed the wet joists. Whoopee! The bears have been urinating on that same wood for a hundred years, and it's rained a zillion times on them too!The problem occurs when the wood is saturated, and left to dry in the bent position. Then, it absorbs that form and developes a memory. You can re-instruct the wood by wetting it again, and laying it straight. In this instance, the framers ercted the wood before it had time to dry out. Therefore, no problem!All houses must be dried out to some degree prior to finishing. Each house will require it's own timetable, due to onsite conditions. dehumidifiers are unnecessary. The funace is the best dryer for the job. Turn it on and let it do it's thing.Your house should be alright, even if you are forcing some of the carpenters to work at substandard wages. How do you feel knowing that you live in comfort while the laborers on your house cannot afford health insurance for their kids?blue
*Lots of between the lines stuff here. Like , remember when the builder had his own carpenters and they wern't framing subs. He had more control of the site and the materials. Part of the reduction in cost of construction is subbing the parts out to specialists, but there is a price to be paid for that. Not to be holier than thou, but that's the main reason I haven't built a new house since 1990, could no longer compete when the custom homes went the same way as the tract homes, and don't tell me they are just as good, because we know they arn't.When the framer knows he's the one who's going to be running the interior trim, he 's that much more careful than the framing sub getting paid by the square foot. I would venture to say that if mr. homeowner knew there was a difference between real employees and subcontractors, he might start to be able to compare one contactor's package to another. But they don't have a clue, so it's remodeling and additions for me, where we have a level playing field and I can try to find rewarding work for the talents of my Carpenters.When a Customer asks me about storage of materials, I don't have to say , GEE, I'll make sure to go over that with my sub !b Keep your powder dry, and let's be careful out there.
* Blue,
Joseph Fusco View Image
*Unlike dimensional lumber, wood I and truss-joists are under a waranty since they are engineered/manufactured lumber. If they get wet, are left in the dirt, stored at odd angles or otherwise mishandled, the manufacturer is no longer liable for any future failures -- such as delaminating, splitting, joint separation, swelling and separating at ends, plate cross-over collapse; etc -- that can occure as a result of too much water, too much sun, swelling up and freezing, etc. Trusses are not so vulnerable as wood I's. I don't want to see mud and crap in my attic framing or in my basement joists.Sloppy and disrespectful handling of materials hints at sloppy and disrespectful workmanship. I would definitely check on the framing quality, work arounds and fixes and the nail and joining regines of a contractor who leaves my expensive raw material in the mud and rain. What does a roll of poly cost and how long does it take to stack and cover the materials ? I wouldn't want to put my saw blades through dirty lumber either.
*
Hey, blue. The I guess the "laborers" know what they are worth, too. Sounds like a free market to me. Booger on, blue.
*Hey, blue. I guess the "laborers" know what they are worth, too. Sounds like a free market to me. Booger on, blue.
*
Blue..........thank God your back......where have you been you ole devil.....we thought that back hoe ran over you.....
*
My first lumber shipment arrived onsite a week ago and has been fully exposed to the rain ever since. The framers just began framing today. I drove by the site to look at the progress and noted that the entire stock of 40-foot I-joists were haphazardly scattered about the uneven muddy ground, like a box of spilled toothpicks, getting poured on by a steady rain. Many of the joists are bending and lying in a position they weren't designed for. After that kind of treatment, I fear that the engineered lumber may no longer be perfectly straight as it supposedly was when it was shipped. Are my concerns substantiated? If so, will the joists eventually straighten out, as if they had a "shape memory?"
BTW - all this occurred AFTER I had specifically asked my builder to ensure that the lumber was stored correctly and covered until ready to use. Should I complain to my builder at the risk of being too demanding?
*OOooops!!!!Someone really screwed up!!!Was it your builder or you?Whose responsibility was it to "secure materials" onsite? Yours or the builders? Whose schedule were the materials delivered on, yours or the builders? Does your contract state who will be responsible for "securing materials"?Now is the time to define responsibilities before the windows arrive and you "really have a problem" on your hands.Devil's Advocate, I'm not a builder. I'm only a perp.Jeff
*The construction is performed on the builder's schedule. He procures all material, schedules delivery, performs receipt inspection, and SUPOSEDLY supervises the project, including the subcontractors' handling of the material. The contract does not specify exactly how the material is to be secured. We made a verbal "understanding" about material handling a few days prior to the first shipment. There must be some standard expectancy of material safeguarding in the building industry. That goes hand-in-hand with being a professional.My contract doesn't mention anything about broken window glass being installed in the new home. Does that give the builder the right to install broken windows? Food for thought.
*Maybe I'm a little picky about the materials that go into my jobs, but I don't even leave the culls out in the weather. I also send back shipments that I think are substandard (I set the standard)! As someone aptly pointed out on another message, the contract, usually written by the "contractor", is interpreted in the clients favor if there is an ambiguity. I wouldn't pay the man another dime until he replaced those I-joists. Read the manufacturer's recommended care and feeding of his product. Did you give the contract to the "really" low bidder? Did you check out his previous jobs, clients? Am I being too nosey? Hope you get it resolved (in your favor). Comments?..... Ralph
*OOOooooops!!!As you say your builder:""procures all material, schedules delivery, performs receipt inspection, and SUPOSEDLY supervises the project, including the subcontractors' handling of the material"""Don't come to BreakTime over this problem, go to your builder whom you have by your own admission, contracted to secure your investment in materials.The internet will not satify your claim, restore you to your prior financial position nor remedy a lack of understanding between you, your builder or your lumber.Who in the name of Hell would get on the internet and start bitchin' about lumber/trusses left out in the weather?Excuse my ignorant ass but if it were my home this lumber was destined for, in the situation it was described, the last damn thing I would think about would be to take my frustrations out on BreakTime.Daaahhhhh!!!!!Get your ass out there and cover it up!!!! Yesterday!!!A little of Joe rubbing off on Jeff