*
Another option is to use aluminum angle.
1. Mortise fluted column to accept one side of angle and edge of rail.
2. Drill 4 holes in angle, 2 on each side, countersink those holes going into the column.
3. You can route the bottom of the rail where the other side of the angle is if you want a “flush” appearance.
4. Spring the rail into the two columns, resting on top of the angle at each end, and attach with SS screws through angles into bottom of rail.
Discussion Forum
Discussion Forum
Up Next
Video Shorts
Featured Story
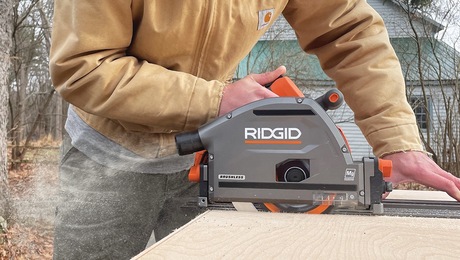
The best tool for straight, splinter-free cuts is made even better without a cord.
Featured Video
Video: Build a Fireplace, Brick by BrickHighlights
"I have learned so much thanks to the searchable articles on the FHB website. I can confidently say that I expect to be a life-long subscriber." - M.K.
Replies
*
Get one of those contour tranferring gizmos with all the wires and cut the column shape into the end of the rail and secure the rail to the column with a couple of small SS brackets and screws.
*
Isn't the mortise itself going to be a rot magnet -- this is where rails always seem to rot through? Will the (lack of) transition from shaped rail to fluted column be aesthetically awkward, would a contoured mounting plate help? Couldn't the railing stop an inch or so short, or does it rely on the column for some strength? Is there some classic" approach to this (I guess it was "no rail at all")?
I know, too many damn questions. But the answers are always so good.
Sending out a rueful chuckle on the no-vent crack...
*How about using the contour gauge to get the profile, (assume the rail is 3in. tall and 4in. high for this exercise) mark the profile on a piece of paper.If the "depth" of the rounded profile is 1in. (draw straight line from tip of profile to tip of profile and measure from line to midpoint of curved profile and include flute if it's deeper), use a 1 1/2in. thick piece of wood that's 3.5 x 4.5 . Draw the profile on the 1 1/2in. edge and cut on the bandsaw. Attach this piece onto the column as a flat mounting surface to attach the rail.Full strengh column and flat mounting.Jeff
*Andrew, the columns are the only thing supporting the railing system other than a small block under the midspan of the bottom rail. As for the rot magnet, the whole thing is pretty well sheltered by the roof overhang from anything but a hard blowing rain. Plus being hollow and relativly thin it could dry from both sides [at least thats my theory] , the columns were also mopped on the inside with an asphalt sealer. Having said that, if anything were to rot thats the first place I would expect it.Jeff, thats a very good idea, I'll probably do some experimenting in the next few days. Plus a good reason to fix my busted bandsaw. Thanks guys, Chuck
*Jeff,That's the best idea I've heard yet. I wasn't very fond of the mortising of the columns because I'm of the same thinking as Andrew on this one, a rot magnet. In fact, I just re-read his post and he mentioned a contoured mounting plate. Probably talking about the same thing, I just missed it. It's funny how one person can miss the seemingly obvious. Sometimes you just need another person's perspective and the answer is simple.Red dog
*It's not just handrail, right? There are runs of balusters beneath? What about mounting 'posts' to the columns (with a v-groove cut into the back to latch onto the cylinder,hopefully landing between the flutes, and a flat face on the other side).The v-groove would allow you to swivel left or right to get the two flat faces in the same plane. Infill the rail sections between the flat faces of these 'posts', and cap the whole thing with the handrail (covering the endgrain of the posts)coped to the column.
*
I have several porch rails to install between 12" fluted columns. The columns are wood hollow stave construction approx 1 1/4" wall thickness with approx 3/8" deep flutes. The rails will be approx 2"x4". My thoughts were to make the rails about 4" longer than the post to post dimension and cut a hole into the side of the column matching the shape of the handrail( with a jigsaw or router)and slide the rails in on one end then back into the holes on the other end centering the whole thing then toe screw from underneath and caulk the rail to the post. My question is will this compromise the structural integrety of the posts much? As for the load on the posts, there only supporting an 8' roof tied to the house on one side, and are on approx 8' centers. I've never ran hand rail between fluted columns before and just wanted something that looks clean and neat. I'm open to suggestions.
Thanks, Chuck
*Hi Chuck, I had to install a balcony handrail once and end it at a wall that was covered with log siding. I cut a mortise into the siding to insert the hand rail which worked out well; although, there was not any question of structural strength involved with the wall there. I just wonder if you could mortise into the column just slightly beyond the depths of the flutes and then cut the rails so that they would have to be slightly sprung to install them between posts. If you are putting in ballisters also, you would then have to build on site which may or may not be a problem. Just a thought. MDM.
*I like MDM's idea of the mortise, instead of matching the profile of the rail. If you do it that way (assuming paint grade) maybe you could put some screws through the column into the mortise to help keep it from wanting to pull outwards, sort of a secondary measure to the idea of putting the spring tension on. Another possibility would be toggle bolts through the end of the rail, maybe above and below the mortise, again assuming paint grade. Good luck Chu
*I've seen it done a few ways that looked nice: 1) Mortise, as MDM wrote; 2) More of a dado than a mortise, just enough to knock off the radius of the column to get to the base of the flutes so the rail could be slid in against something flat, 3) another mortise, this time large enough to accept a backer block to be installed against the column, with the rail being set against the backer block, and 4) scribe the rail to fit against the flutes.I wouldn't advise going completely through the column. Structural may not be an issue, but moisture penetration would be.
*Why couldn't your do as Mongo said "just enough to knock off the radius of the column to get to the base of the flutes so the rail could be slid in against something flat" and this is where it gets tricky - put a 3/8" all thread through to the rails on eaither side of the column. And back (after cutting a slot in the bottom)of the rail, attach with a washer and nut? It'd be clean and firm.
*Excellent advice from everyone so far, thanks alot. I planned to make up the railing in sections complete with balusters in the shop, I forgot to mention that the cross section of the rail isnt rectangular, it will be peaked in the middle on top probably ten degrees or so of slope. So I would have to first mortise in a mounting block like Mongo suggested in order to slide the rail in from the side. One reason for considering going all the way thru the post was I could make a story stick and lay out and assemble the majority of the sections the same size, as the columns are very close to being perfectly uniform on center. The columns are vented from top to bottom so I didnt think moisture would be a problem, but I suppose if [actually when] the caulking failed the end grain exposed inside the hole would tend to wick moisture. Maybe I could just cram the post full of cellulose, to hell with the venting LOL. Thanks for all the ideas everyone keep em comin, a wise man once said on this very board " none of us know as much as all of us" . Chuck
*Another option is to use aluminum angle.1. Mortise fluted column to accept one side of angle and edge of rail.2. Drill 4 holes in angle, 2 on each side, countersink those holes going into the column.3. You can route the bottom of the rail where the other side of the angle is if you want a "flush" appearance.4. Spring the rail into the two columns, resting on top of the angle at each end, and attach with SS screws through angles into bottom of rail.