Nearly Net-Zero ADU
A low-carbon, all-electric accessory dwelling unit demonstrates the benefits of small-home living.
Synopsis: In this article, Sean Conta describes an ADU his company built for a woman whose daughter was moving back to Seattle and needed a place to live. When the project began, Conta had just learned about the BEAM Estimator, a free tool that evaluates the carbon impact of different material choices. He used it extensively throughout the build and ended up with a 30% reduction in carbon emissions compared to the same house built with his conventional material choices.
Seattle ranks among the top 10 most expensive—and desirable—places to live in the United States, so it’s no wonder the city needs to expand and diversify its housing options. One of many solutions to the housing shortage is the accessory dwelling unit, or ADU. ADUs can be either attached to an existing home (AADU) or detached and located on the same property (DADU). Most of the residential space in Seattle is zoned for single-family homes (now called “neighborhood residential zones” to be more inclusive and accurate), so finding ways to increase density in these areas is imperative to creating more housing.
ADUs also provide a flexible housing option. They are typically compact, under 2000 sq. ft., and thoughtfully designed to optimize space and accommodate small-home living. They can be used as rental units, guest houses, multigenerational family accommodations, or even as for-sale homes, which are allowed in Seattle if the homeowner creates a condo association between the main house and the ADU. There are other aspects of ADUs to like also. They usually fit well into the “fabric” of the city stylistically; often they are designed to match or at least complement the main house, and they generally can’t be higher than two stories tall. Plus, for a first-time home buyer, they are more affordable than many homes on the single-family market. That is certainly true for new construction.
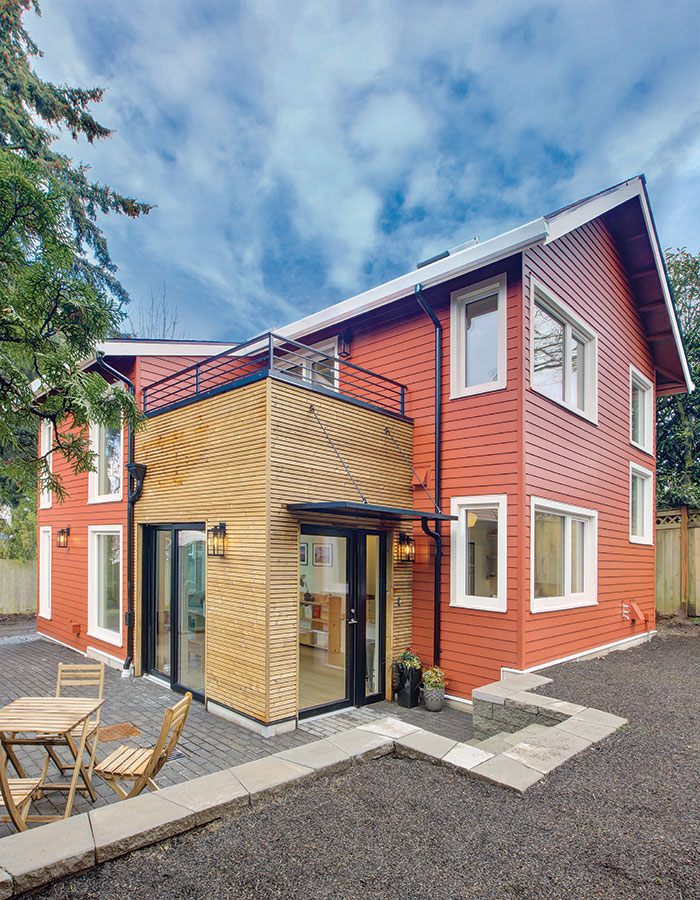
My company, Targa Homes, has focused on building high-performance homes for the past five years. For this reason, in 2022, a homeowner approached us to build a DADU for her daughter, who would soon be relocating to Seattle. My employee Matt Kull and I have a strong background and understanding of building science and sustainability. In my case, that knowledge was gained as a Passive House rater and Built Green verifier (a regional green-building program). A holistic, sustainable approach is intrinsic to every project we do, and this was to be no exception.
Determining the design
The client wanted a space that could one day accommodate an aging occupant, so having a bedroom and bathroom on the ground floor was a requirement. A flexible unit that could serve a variety of uses was also important. This DADU might be used as a work-from-home space; it could house a small family or even multiple generations under the same roof. Generous daylighting to combat Seattle’s gray winters was another requirement, as the client’s daughter was relocating from sunny California. A clean and simple aesthetic was another condition.
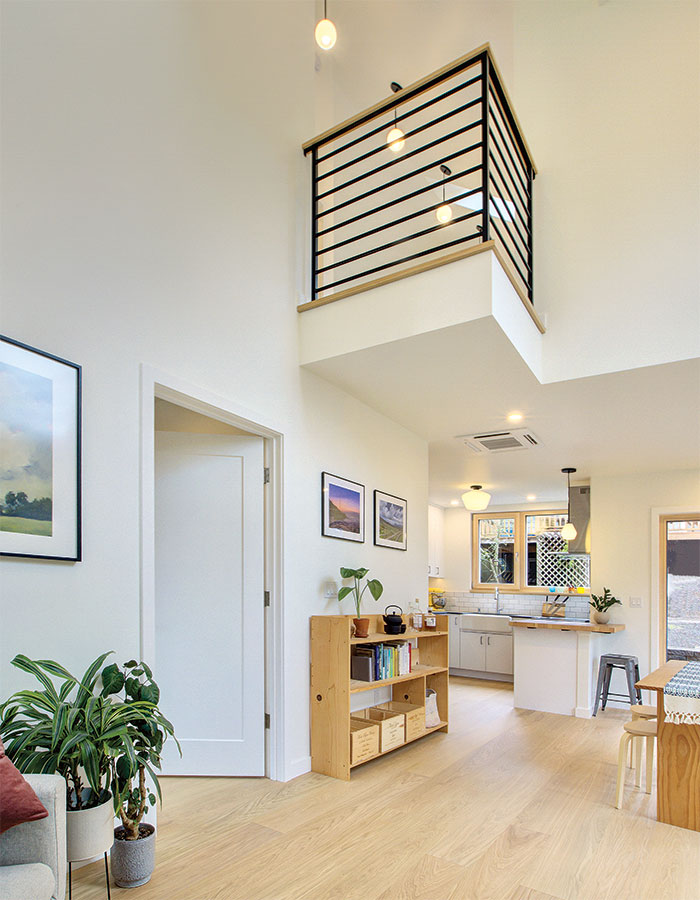
Since Matt and I are solely builders, the first step in this project was referring the client to Freehand Studio Architecture and Design, a firm we have worked with on previous projects. Owners Ben Toda and Alexandra Forin also consider building science and sustainability to inform their work, so we knew we could trust them to collaborate on the right details. They spent time with the client designing a structure that would achieve the project goals.
Small but spacious
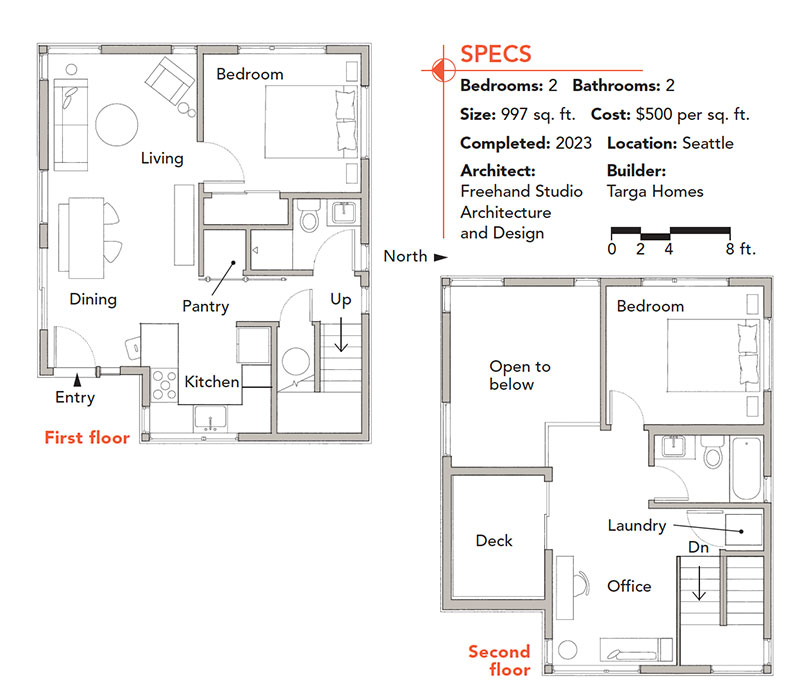
The house was designed for a family, with two bedrooms and two baths. A flex space with an overlook has a small south-facing roof deck. The layout and details consider a variety of occupants over time. For example, the ground floor has stepless entries (both from the outside and to each interior room) to accommodate aging or other mobility-restricted occupants.
Making carbon a priority
Another consideration was the project’s carbon footprint. We are conscientious of both the operational carbon emitted by buildings in use and the embodied carbon inherent in construction. For this reason, we make careful selections when it comes to building materials and products in our assemblies. A major decision on this project was to use reclaimed framing lumber wherever possible. Reusing existing materials avoids the carbon cost of creating virgin material; using local materials also avoids the carbon cost of shipping. Washington State residential code allows the use of ungraded lumber in structural applications where it would otherwise allow the use of #2 grade lumber.
We reached out to our friends at Sledge Seattle, a local deconstruction company, to help put together a framing package. Ultimately, nearly all the common 2×6 studs and plates came from the careful deconstruction of old Seattle homes. Not only is this wood generally of a much higher density than new lumber, but the carbon footprint is extremely low. Plus, it just feels good to put old-growth Douglas fir to work in a home for hopefully another 100-plus years. People often ask if doing this poses challenges for framing. Matt and I framed this home ourselves and found the changes to our process to be minimal. Older wood is often darker, so we used white or red Pica-Dry leads in our pencils. The material is dense, but regular framing nailers worked fine. That said, it can vary in dimension more than new wood, so more attention is required when sorting through studs. To be honest, the main disruption to our routine was the frequent stopping to comment on the incredibly tight grain patterns that our crosscuts exposed.
When this project got underway, I had just learned of the BEAM Estimator. This free tool allows you to enter the characteristics and measurements of a building and compare the carbon impact of different material choices. With it I was able to validate two of the major assembly choices we made: using cork exterior insulation and putting dense-pack cellulose in the wall cavities. Cork is an all-natural product made from the bark of cork trees; it is harvested from the trees and then regrows quickly, making it a highly renewable resource. The bark is ground up and steam-heated, which results in natural binders that glue together the granules and form a rigid board. The ThermaCork insulation we wrapped around the house is vapor-open, R-4 per in., fire-resistant, and carbon-negative, even after having been shipped from Europe. And since the cork insulation is outboard of the sheathing and is continuous, it minimizes thermal bridging.
For wall-cavity insulation, we used blown-in cellulose. In the past we’ve used blown-in fiberglass; here we used cellulose because it is a carbon-negative material that also offers some hygric buffering capacity—meaning it will absorb and release any moisture in the wall cavity.
The last decision we made using the BEAM Estimator was to use an engineered wood siding (LP SmartSide). Although Hardie fiber-cement is the standard in our market, using a wood-based product resulted in a reduction of embodied carbon. Because we always build a fully ventilated rainscreen assembly under siding, we were not worried about long-term durability in our wet climate.
After I entered all the data and selections into BEAM, the result showed a 30% reduction in carbon emissions (presented in kgCO2e, a unit referring to the warming impact of other greenhouse gases that are converted to CO2 equivalents) compared to a baseline version I entered using our conventional material choices, such as fiber-cement siding, fiberglass, and foam. We plan to use the BEAM Estimator on all future builds. We have found there are several low-hanging-fruit substitutions on any project that can really make a difference.
Keeping energy use to a minimum
Our goal is always to build the lowest-load home possible within the budget available. Methods of space heating and cooling will change over the life of a building, but the envelope itself is rarely modified with respect to efficiency. So we like to ensure that a structure doesn’t require much energy to heat and cool.
Airtightness is critical for an energy-efficient, low-load home. It takes time, research, and experience, but knowledge of air-sealing and building science (as well as attention to detail) has resulted in great blower-door test results for all our builds. A key step is performing a preliminary test right before insulation. This is the right time to find out how you’re doing and to correct any weaknesses that may be exposed while “the red door of truth” is running. On this project, we found a few areas to touch up, and our final blower-door score came in at 0.35 ACH50, which translates to 0.02 cfm per sq. ft. Matt and I prefer calibrating to the cfm-per-sq.-ft.-of-envelope-area metric because we find it to be a more accurate measurement of airtightness for any building size.
To ensure airtightness, we used a fully taped vapor barrier under the concrete slab and a belt-and-suspenders approach at the mudsill, with sill-seal foam under the plates and two beads of Contega HF sealant, as well as Siga Fentrim 430 tape from the bottom of the sheathing to the concrete.
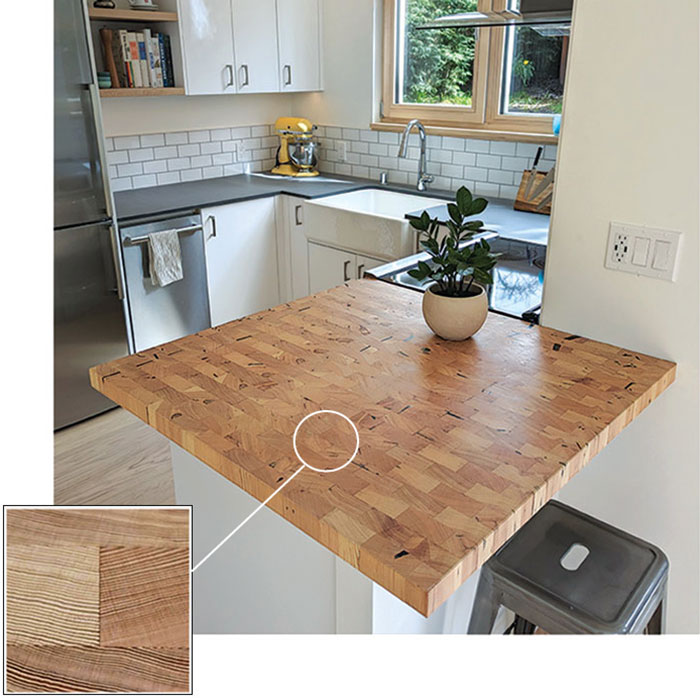
For the walls and roof, our primary air barrier is the taped exterior Zip System sheathing. To make the air barrier continuous from the walls to the roof, we used what’s been called the “monopoly framing” approach. We framed the simple structure without roof overhangs, allowing us to bring the wall sheathing up to meet the bottom edge of the roof sheathing. This also means we have continuity of our water-resistive barrier (WRB), and it allows the exterior insulation to be uninterrupted from the walls to the roof, where we insulated above the structural sheathing with two layers of rigid foam. (Using cork here did not fit in the budget.)
There are several ways to apply roof overhangs; we bolted them on top of the sheathing, filling the space between them with insulation. Over the insulation is another layer of plywood, to which the roofing materials are fastened later. With a combination of exterior insulation and insulation below the roof sheathing, the assembly has a total R-value of 42. The walls are R-25 (R-21 cavity plus R-4 exterior), and the slab is R-16.
We encouraged the client to choose the best windows possible within the budget. She went with Vetta tilt-turn windows, which are made in Poland from FSC-certified wood and aluminum exterior cladding. The triple-pane units are gasketed and highly energy efficient, with a U-factor of 0.16. In addition, they add a beautiful element to the interior aesthetic and will perform for many years.
All-electric mechanicals
In Seattle, it is feasible to build an all-electric home without a gas line, which is what we did here. Not only do we have a relatively clean electrical source (mostly hydroelectric), but options for generating electricity on-site are increasingly available. The house has two ductless-minisplit heads, each of which is paired with its own compressor outside. Unlike a zoned multisplit system, this arrangement allows the minisplits to run at peak efficiency. Our HVAC contractor suggested using Mitsubishi HyperHeat models for this reason; they can modulate down lower than other models. With the two minisplits located in the common areas on both floors, it was necessary to provide backup heating in bedrooms in case of lower temperatures with doors closed. My standard choice here is a ceiling-mounted electric radiant heat panel made by Ducoterra. This simple unit has no moving parts and emits a comfortable radiant heat. Locating the 1⁄2-in.-thick panels on the ceiling allows for flexibility when it comes to furniture layout.
With a very airtight home, proper ventilation is critical, and this combination is especially beneficial during Seattle’s increasingly frequent wildfire-smoke events. This home has a Zehnder ERV with dedicated 5-in. ducts throughout. The unit runs at a high recovery efficiency and low power draw of around 30w, and it operates continuously with a MERV-13 filter.
The hot-water tank was to be located in a closet space under turning stairs. Using a hybrid water heater would have required placing the unit right inside the doorway, effectively blocking off the rest of the storage space. We decided to upgrade to a SANCO2 split-system heat-pump water heater. Although the cost was substantially higher, the short 43-gal. tank could be tucked farther under the stairs, allowing access to an additional 30 sq. ft. of storage. The unit requires no electric-resistance backup but still makes hot water down to –25°F outside, and it has a great first-hour rating due to its fast recovery and the fact that its output water temperature is 145°F. Additionally, the ultraefficient SANCO2 unit uses CO2 refrigerant, which has a much lower global-warming potential than other refrigerants.
As the project moved forward, the owner decided to invest in a 3.6kw roof-mounted PV array. Although the roof is under shade part of the day, production should significantly offset consumption.
Monopoly framing for an airtight roof
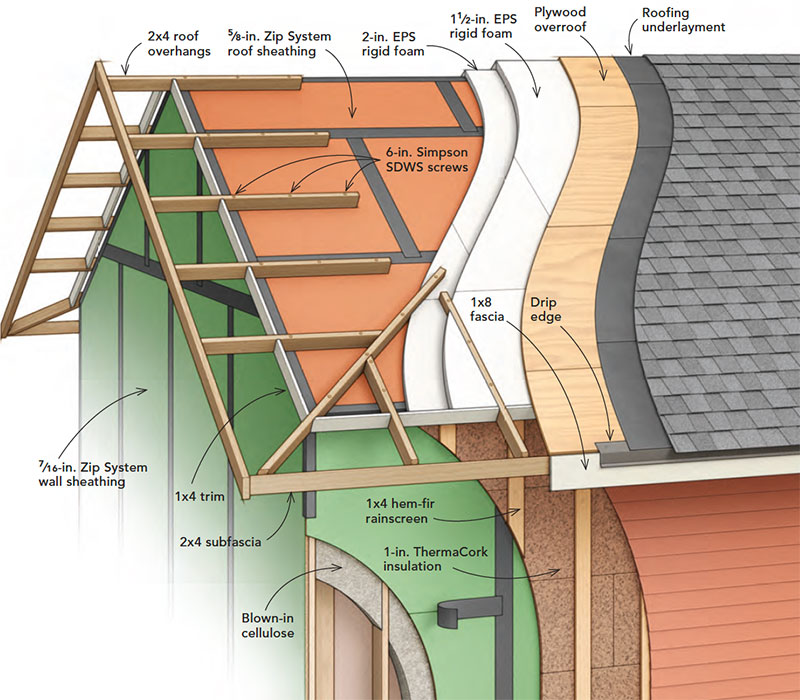
Monopoly framing, which is framing a house without integrated roof overhangs, allows you to keep the air barrier continuous from the wall to the roof sheathing. Roof overhangs are then applied. In this house, the overhangs are installed above the roof sheathing with structural screws. Exterior EPS insulation is fit between the rafter tails and over the entire roof. The insulation keeps the structural sheathing warm enough to reduce the risk of condensation and rot, and relieves the need for venting. It is important to get the correct ratio of R-value above the sheathing to R-value in the rafter cavities; otherwise the sheathing may not stay warm enough. Roofing is fastened to a second layer of plywood that is installed above the foam and screwed through to the rafters.
Tracking for performance
We figured this home would be close to but not quite net-zero. After reading about new smart electrical panels, we decided to install the Leviton Smart Load Center with WiFi-enabled breakers. This system reports circuit-by-circuit energy usage to a smartphone app. The ability to see this data can help occupants understand how they are using energy and potentially change behaviors, if necessary. Also, six OmniSense sheathing temperature and moisture sensors were placed inside the roof and wall cavities to give us visibility into any potential problems. These sensors track and record readings that can be viewed on an online dashboard.
So often we finish a project and immediately move on to the next, mostly unaware of how it performs unless we get called about a problem. With this home, we’re excited to have some insight into electrical usage and sheathing conditions after occupancy. We handed the keys over in late April. During the first month—despite outdoor temperatures ranging from 47° to 88°F—the occupant kept the heat pumps off the entire month, and the OmniSense sensors indicated safe levels of moisture in the wall and roof sheathing. It’s interesting to view this type of data for the first time. We’ve been asked, “What if you see a moisture problem inside the walls?” Correcting it would invariably be complicated and costly, but catching it early will be less so; this is what makes the use of diagnostic sensors a smart move.
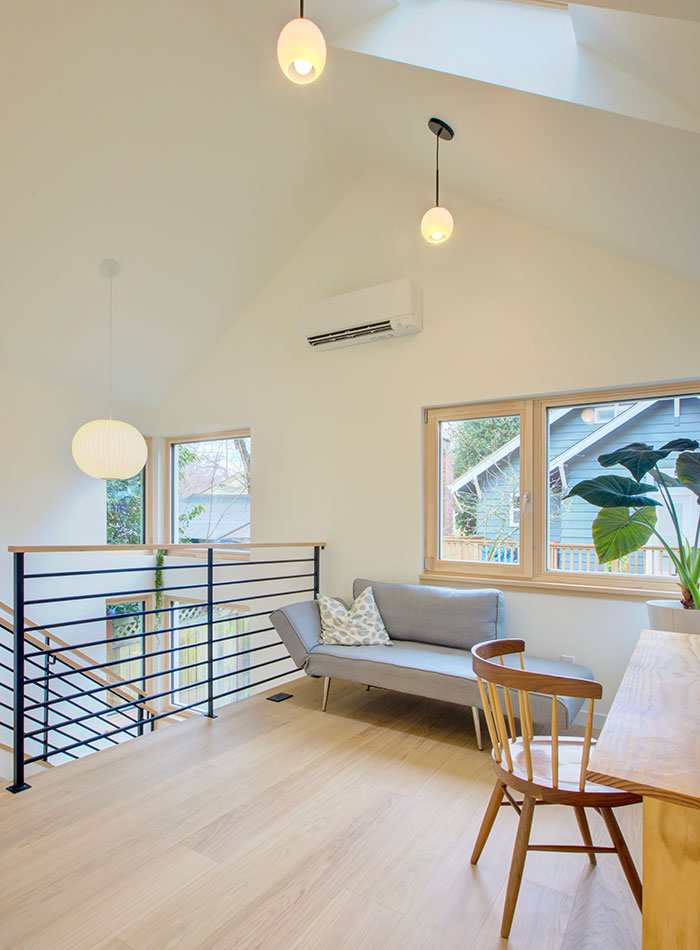
A beautiful, energy-efficient, low-carbon home has failed if it doesn’t last a long time. It’s hard to say what this part of the city will look like in 50, 100, and 150 years, but I’d like to think this home could still be standing long after my time on the planet. Thoughts of this nature provide a deep personal fulfillment in our work. And the client seems pretty pleased too.
—Sean Conta is owner of Targa Homes in Seattle.
Photos by Chuan Xia, Chuan Photography, except where noted.
From Fine Homebuilding #319
RELATED STORIES
- A Flat Roof in a Cold Climate
- HVAC System for a High-Performance Home
- Systems and Products for an All-Electric Small Home
View Article PDF |
Fine Homebuilding Recommended Products
Fine Homebuilding receives a commission for items purchased through links on this site, including Amazon Associates and other affiliate advertising programs.
100-ft. Tape Measure
Smart String Line
Original Speed Square