*
We are building a home and have a loft type room that overhangs the main living room. The floor of the loft has a pretty large arc to it. We are brainstorming on ways to build the bent handrail for the overhang. I’ve seen the pre-fab products for doing this (one on cover of recent FHB) but they appear to be very expensive (but maybe worth it). I am looking for any advice from anyone that has made their own bent handrail and recommendations on how to do so. Tricks for laminating, how to clamp, etc. Thanks for the time.
Discussion Forum
Discussion Forum
Up Next
Video Shorts
Featured Story
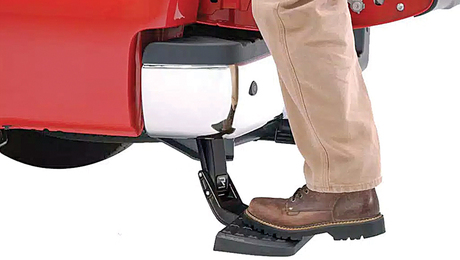
The RealTruck AMP Research Bedsteps give you easy access to your truck-bed storage.
Featured Video
How to Install Cable Rail Around Wood-Post CornersHighlights
"I have learned so much thanks to the searchable articles on the FHB website. I can confidently say that I expect to be a life-long subscriber." - M.K.
Replies
*
No experience with it, but everything I've seen shows gluing up thin(er) strips of pre-curved wood wider or 'higher' than needed. Once it's all to thickness, plane/joint/etc. the ragged edges to get the finished 'height' of the rail. Then pass along router to shape sides of rail. May be necessary/logical to do this in small length portions, assembled in place. Can even add balusters between sections, incorporating them into a design, maybe.
I hope the crude sketch gives you a better idea...
*Hi Matt,ASSUMING that your floor is unfinished, lay out the arc on the floor and screw down blocks on the outside line every foot or so.Take your handrail and run it on the bandsaw and cut it into 1/2 inch strips and glue them together, clamping them together against the blocks on the floor with c clamps.Next day, remove, sand and install.Gabe
*When curved stair railings are made, there are alot of strips and ALOT of clamps. I bet I've seen 30 or more clamps on a 12' section of rail.Once the glue is dry, sand, sand, sand, and finish.
*when we made these oak handrails .. the core is 3/4 ply.. nailed to the top of the balusters..then we laid up the oak... the center is cut to fit...and trued..then the filler blocks between the balusters then the half round sides were glued on ... then the ogee quarter fillers ( the ""quirk"" bead)... the clamps were many innertube strips , wrapped and tucked.... the inertube strips develop unbelievable clamping force... we just kept wrapping until everything closed up... the glue was 5 minute epoxy..this rail is 15 years old....
*Good looking rail, Mike.Rich Beckman
*Matt,I priced this a while back to do my curved staircase.If I'm not mistaken, the bending rail was about three or four hundred bucks for both handrails, with bending mold (temp pieces to use on the sides to clamp to) This may be more affordable than you think.Call Superior Stair Systems in Bend,Or. 541.318.8040Bill SmithP.S. I haven't bought yet, stairs still unfinished and on the back burner.
*Matt, I have to think you would want to use bending rail & mold>>> HereYou will need a ton of clamps and slow setting glue. You might price out having a stair shop make the rail for you, you could supply the template or have them come to the site and make it. Ya the cost is not pretty, but what is your time worth and are you sure you are not going to spork it? You only have one chance to get this right.
*
...I'd be easier if I could draw this...
You can accomplish precisely the same thing as the pre-fab products by slicing up stock handrail on a table saw. What works the best is to slice up two lengths of handrail into strips of equal thickness--one with the saw kerfs to the left side of your division marks, the other with the saw kerfs to the right.
Then you just sort of collate the strips--by selecting alternating pieces from one set of strips to the other, you can cancel out the saw kerfs and end up with the complete profile of the handrail.
Then you can bend and glue away. And yes, you will need a lot of clamps.
*
Matt,
The March FHB (#129) has an article on using bending rail as some have suggested, and March '99 (#121) has an article on a porch that uses a laminated crown molding that's cut up using the method suggested by Anthony. If you can get hold of them, they illustrate each method pretty well.
I haven't used bending rail, but if you have an unusual rail section, you might have to go with the second method. Either way, stock up on clamps.
Froed
*here's another handrail.. this is on a 14 foot rdius wall..the rail is teak ripped into 1/4 inch x 2 strips..we covered the shingles with poly and screwed 1.5 inch blocks to the shingle wall so we would get teh right stand-off..then we built up our laminations.. with epoxy..the only clamps were the inner tube strips.. when we ran out of inner tubes we cut strips from .060 rubber roofing.. worked even better..when it was finished we took it off the wall and shaped it to the final profile with our router bits...
*BEE-YOO-TEE-FULL! Not just this, but everything I've seen from you.If you were in Philly, I think I'd like you as my contractor.
*I'm not a big fan of bending rail at all. One of the first railing projects I ever did was with bending rail and over the course of the next three to five years I kept on having to go back to re-plump the newel at the base of the staircase. You see the bending rail was trying to return to it's straight rail former self. I haven't used it now for at least fifteen years. One my other complaints with it is it comes in a limited number of profiles and making your own is not as just as simple as bandsaw-bend-glue-sand-install . Certain profiles (and species) don't lend themselves well at all to that technique. In certain wood species too I think it would be a waste of wood "design-wise" too. While bending rail doesn't look that bad in oak I would think cherry bending rail wouldn't look anything at all like it was cherry. I prefer stacked ( or as we call them "blanked" up) rail or rail made from solid stock. The photographs below show project we just completed this past spring. All the railing is fabricated (cut and shaped) from solid stock. The level S-shaped section in the first section was cut from a 3" thick piece of cherry about 14" wide by about 9' long and the curves in the second photo were cut from pieces that were maybe 10" or 12" wide by about 14' long. The very last part of the curve in the second photo where it returns to the wall is short curved piece that I added on otherwise to make that whole section out of one piece we would have had to had a 3" thick piece of cherry about 18" wide by 15 or 16 feet. You should (if I've written the HTML code correctly) be able to click on the thumbnails here and open up a larger photograph in it's own window. View Image View Image The way the whole job went I first templated the whole balcony and gave the templates to the iron workers (Bedford Ironworks, Bedford NY). They then fabricated the balustrade sections and installed them. Then working from the templates we then fabricated the bullnosed base pieces that "clam-shelled" around the balustrade on the floor level (the next photo below). The carpeting that would be intalled at a later date would run up to and butt with the bullnosed flooring pieces we were installing. While the straight sections of the floor pieces weren't that difficult getting the two curved floor pieces to mate perfectly with each other while tightly encasing the balusters was actually the toughest part of the project. As it turned out you could fabricate and fit only about four or five linear feet of curved flooring a day. I figured (estimated) the curved floor sections would be four or five times as difficult as the straight sections. As it turns out they were more like twenty times the difficulty . The sections were biscutted and joined with polyurethane glue together. I found a great new tool in a a Metabo 3" Random Orbit Sander to clean up the joints along with the trusty old Fien finishing sander too. View Image To fabricate the railing we actually placed the stock (after surface planning it to thickness) on top of the installed balustrade and scribed/traced both side of the 1" wide strap iron that held the top of the balustrade together. The stock was then flipped and the plough for the strap iron routed out. We then took the pieces out to the garage with had a perfectly level tile floor and set them up on a high set of saw horses. We then scribed the rail pattern using the plough as a guide. The stock was then cut along those lines with a band saw I had mounted on wheels. In other words the bandsaw moved while the stock stayed in one place. I tried it the other way at first but the pieces were way too cumbersome to handle and kept binding because they didn't move laterally side to side across the saw horses. I could have use ball bearing type rollers I guess but I found this was just as easy to set up. The rough curved railing shape was then "faired" sanding it with a belt sander. I found this was real important to do before shaping because any bump or hump in the band saw cut will transfer itself to the shaped cut and it a lot easier to "fair" the surface while it's flat than after it has a complex curved shape cut in to it. You can ask the guys who sanded the shapes I did with out that "fairing" step. The profile was shaped using a 3HP DeWalt router with a 1" round over on the top and a "railing" bit I I picked up from Rockler ( why they are the only ones who make that shape in a router bit puzzles me) Before installing the rail back on the balustrade we took 1/4" thick cherry stock and clamped it to the strap iron and then using a trimmer bit trimmed it off in place for use as fillets in the ploughs and then installed the railing on the balustrade. The tricky part of the job and what turned away a lot of other stairbuilders was the wreath turn on the stair (photos below). As you can see from the photo below both the bottom section which we referred to as the parapet cap and the rail had to make a 180 degree turn while decending approximately 30" on a very tight radius. I think the railing centerline turned on a 4-1/2 radius. That made the inside radius of the parapet cap wreath's turn a 1/2 in radius. You can see from the second photo there that it almost turns "under itself". The way I made the turns was after plotting them out in my head and then checking my thinking a couple of times with drawings in VectorWorks I glued up a blank for the parapet cap wreath stacking a 3" blocks of cherry and then roughed out the rail according to my calculating from one of the 4"plus thick x 12" blocks I had around. You can't use 3" since the base plane of the rail distorts itself as it makes the helical turn so you need enough extra stock to accommodate the distortion. Distortion is actually the wrong word since it's geometrically doing what it is supposed to be doing but the word helps explain what's happening. The shaping of the railing was pretty much sculpting with a carbide bur chucked in a Roto Zip tool and then touched up and finished with sanding drums in a dremel and that 3" Metabo I mentioned earlier. The parapet wreath was roughed with a Porter-Cable Tiger Saw and 40 60 and 80 grit sanding disks in on a DeWalt Grinder and then finished with the Metabo as well as a 6" Porter Cable Random Orbit Sander. View Image View Image To look at pictures of the whole project you can click on http://www.paradigmprojects.com/brookfield/brookfield.html for a page of thumbnails. I know this is a lot to write about how this project was done but it's actually going to be I know this is a lot to write about how this project was done but it's actually going to be an article for another site I'm working on and this seemed like as good a reason to start the writing process as any. I interested in hearing anybody's comments and advice regarding what we did here and how they might have done it because as usual as I was doing certain processes I could hear myself thinking " Geez I never do it this, this way again". Think about it and then I'll tell you what I would do differently the next time too.
*Jerrald Hayes,
View Image © 1999-2000"The first step towards vice is to shroud innocent actions in mystery, and whoever likes to conceal something sooner or later has reason to conceal it." Aristotle
*Jerrald, WOW!!Very nice, can I go to work for you?Chuck
*Thanks fellas, Interestingly I bought a digital Olympus C-2020 Zoom camera just as I was finishing that job and I now consider it to be the most important tool that I've purchased in years. I was amazed at just how good the pictures it shot were. I actually now wear it on belt along with a Palm Pilot and a Construction Master calculator.And yes Chuck we're hiring. I was thinking that the greatest limit to growth I face today is "aquiring talent". I think the Skilled labour shortage? discussion is interesting for those very reasons
*
We are building a home and have a loft type room that overhangs the main living room. The floor of the loft has a pretty large arc to it. We are brainstorming on ways to build the bent handrail for the overhang. I've seen the pre-fab products for doing this (one on cover of recent FHB) but they appear to be very expensive (but maybe worth it). I am looking for any advice from anyone that has made their own bent handrail and recommendations on how to do so. Tricks for laminating, how to clamp, etc. Thanks for the time.