*
I’m a woodworker and I have a chance to put a shop on where I live. I don’t know where to start.All I know so far is I want a slab foundation. And that is about it. I live around San Fransico Ca. so I know I will need to earth Quake prove it. Are ther anjy good books out there that can help. I olan on doing all the work my self. Except for the foundation. Any help will be greatfull. Thanks Tim
Discussion Forum
Discussion Forum
Up Next
Video Shorts
Featured Story
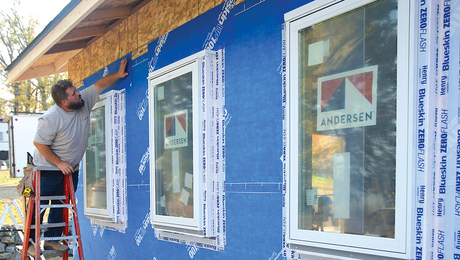
Getting the details right for a wall assembly with the control layers to the exterior and lots of drying potential.
Highlights
"I have learned so much thanks to the searchable articles on the FHB website. I can confidently say that I expect to be a life-long subscriber." - M.K.
Fine Homebuilding Magazine
- Home Group
- Antique Trader
- Arts & Crafts Homes
- Bank Note Reporter
- Cabin Life
- Cuisine at Home
- Fine Gardening
- Fine Woodworking
- Green Building Advisor
- Garden Gate
- Horticulture
- Keep Craft Alive
- Log Home Living
- Military Trader/Vehicles
- Numismatic News
- Numismaster
- Old Cars Weekly
- Old House Journal
- Period Homes
- Popular Woodworking
- Script
- ShopNotes
- Sports Collectors Digest
- Threads
- Timber Home Living
- Traditional Building
- Woodsmith
- World Coin News
- Writer's Digest
Replies
*
Tim,
Some thoughts:
Build as big as you can afford. It will still be too small.
Dust collection. Lay out your shop on paper and identify the location of every major/stationary power tool. Run your dust collection ducts under your slab. Provide connections at every tool location. Also provide extra connections at logical locations, i.e., every 5 or 6 feet along the walls. You can cap them until you need them. Locate the dust collector itself in a seperate room accessable from the outside (to mitigate noise and make it easier to dispose of the dust).
Electrical. Include floor recepticles for tools, like table saws, that will be sited away from walls. You can not have too many recepticles. Consider wiring in conduit so you can upgrade to 220 at any location if you need to. Dont skimp on electrical service. If you are going to do commercial work consider a seperate meter (so you can write off the cost of power without dispute).
Building features: Ceiling heighth should be no less than 9'(so you can stand/flip a sheet of plywood the long way). Make sure you have at least one door that is tall enough and wide enough to pass the projects you will be building. If you are going to spend a lot of time out there include a cold water 1/2 bath.
Material Storage: Plan for shelves and racks. Over time you will accrue a lot of stuff that is just too good to trash but not pegged for anything just yet. Consider an attic or loft.
Hope this helps.
Steve
*Tim Fine woodworking had an article about this 8 or 9 years ago. There are also several good books on shop lay out. Look in the ad section of fine woodworking. If I find out some names I will let you know.Rick Tuk
*Tim - I work somewheres around 6 months a year in my shop and here are some things I'd like to do if I ever build another;Like Steve says - "It will still be too small". If not right away, later. So one thing I would do is plan for easy addition by framing with headers running the length on bearing walls. At any time in the future you could cut the siding, remove a few studs, and add on.After 18 years in my present shop I am reroofing it this fall. I plan to add a few skylights. Nothing better than a naturally light workspace. Plan a few strategically placed skylights. The single biggest thing I would like to have is sections of the walls in my shop mounted on some type of rolling hardware (like real heavy duty barn door track) so that I could roll large sections open in good weather. I get feeling a little "cooped up" in my shop, especially when good weather comes in spring. Opening the walls would be a nice way to feel less "confined". Your climate (I used to go down to The Bay Area a few times a year, always beautiful weather, I'm jealous) should allow the sliding walls and skylights, no problem.Lastly, and most importantly, even if you ignore the other things I said, please consider a wood floor. Very forgiving on dropped tools, material edges, and most of all, your spinal column and legs. - jb
*I also am starting to build my shop. In running the dust collection ducts under the slab, do you recommend PVC or is there something else? If PVC, how do you handle the static electricity build up? Simply fish a grounded copper wire through the duct and hope that crud doesn't get hung up on it? Is anyone aware of an outlet for the duct that can be cast in the slab but that has a cover that won't trip everyone when the tools are rolled out of the way for some large project or the inevitable change from the original layout occurs? For electrical in the center of the slabe, I had figured on dropping power from the ceiling to stationary tools, realizing that the cords would get in the way occasionally (frequently?). Has anyone come up with an electrical outlet for the center of the slab that won't get filled with crud or create a impediment or a hazard. Most that I am familiar with are used in gymnasiums or large conference rooms and that have an outlet just below the floor level covered with about a 2" to 4" round brass cover with threads around the periphery and a slot on top to screw the cover in place. (Inevitably these outlets are either broken or filled with crud when I try to use them...not to mention the covers getting lost) I haven't researched NEC to see what restrictions there might be on creating my own outlet box in the slab, to be covered with a steel plate when not in use. Any interpretations of NEC regarding in-slab electrical outlets would be appreciated.
*Casey, Maybe someone more knowlegable on the subject of static elec. could correct me, but wouldn't a duct system in the slab be self grounding?John
*If the dust duct was PVC, I would guess that it would not be self grounding - PVC is a pretty fair insulating material. I was thinking that perhaps I could place copper rivets through the PVC at close intervals to allow the static charge to bleed off to ground, but I would be afraid that this would also allow an entry for ground water to infiltrate into the duct. Galvanized or stainless steel duct would allow the static charge to bleed to ground, but I would wonder how long galvanized would last and the last time I priced stainless steel duct, it was fairly pricey. However, even metal duct, particularly if it is in a fairly dry layer of gravel, should probably be attached to a ground that meets the standards for an electrical ground.
*
only if it's made of metal.
*
Casey,
I do not know what kind of stationary tools you have but if we are talking about a Delta Unisaw, or something like that, I would not mess around with recepticles in the floor - I would hard wire. To do this in a slab takes some planning but overall, it is the best way to go. You will need to know the exact location of the tool and even more specifically, the location of the power control box (the one with the on and off buttons). Before you place your concrete, rough in a pvc conduit from the edge of the slab to the power box location. Size the conduit to carry the number and size wires your tool requires. If you think you may upgrade to a larger machine at some point, oversize your conduit. Use pre-bent 90 degree turns - one to take the line under the slab and one to bring it up. The turn-up at the edge can be stubed up above the finished level of the concrete slab - the finishers should be able to keep the floor level along the form. However, the story is different in the field. You want a flat surface for your tool but it is almost impossible for finishers to avoid some rise anytime they work around projections. To avoid this, set your conduit so that it is flush or slightly lower than the finish level of the concrete. You need to end the conduit with a female fitting. Put a dowel in the bell and secure it with duct tape. Mark the location of the bell with intersecting string lines. Remove the strings before you place your concrete. The idea here is to be able to locate your conduit if it does not "show" through the finished concrete. Secure the conduit in place so that it does not move. Use rebar hairpins and stakes as necessary. After the concrete is placed and your shop is up you can position your tool, open up the conduit, extend the tube into your control box and hard wire all the way back to your panel. As I stated earlier, this is one of those detail things. Takes a lot of planning because you can not change your mind after the mud turns to stone. It is, however, no different or more exacting than any other under slab plumbing job.
Good luck!
Steve
*
Given the chance to build a shop, I would give serious consideration to installing 2x4 or 2x6 PT sleepers on edge on the slab and then screwing a sufficiently strong plywood floor to the sleepers. This would allow you to run the dust collection ductwork under the finished floor where you could use self grounding metal ducts. You could also run your electrical service under the floor and could make changes and/or additions at a later date by just unscrewing the finished floor. You would also be standing on a wooden floor for which your feet and back will be eternally grateful. Good luck. Wish I were in your shoes.
*You may want to post this on Knots over at FineWoodworking, if you haven't already. The combination of builders/woodworkers should be a good mix of ideas on your project.Good LuckM
*
One thing I'll do on my next shop: since the table saw eats
so much floor space, I'll center it in front of, but close
to, a non-load wall, and make a wide enough slot for any
conceivable plywood rip. Then have a little lean-to shed
outside, with a "workbench" that will carry the ripped
material. A hinged flap would keep out weather/varmits.
Probably--haven't thought this completely through--would
leave just enough space between table saw table and wall so
I could have a long shelf for chop saw and drill press.
Speaking of which: has anyone ever counter-weighted their
drill press, and attached its table to a shelf, so that
cranking moves the head, rather than the table, up and down?
*Casey-Instead of PVC for your dust collection, you should look into PCD - polyvinyl coated ductwork. It is rated for almost anything, including underslab. It is basically metal duct with a plastic coating, which can be either inside, outside, or both. A HVAC supply should have info on it, I have a packet from Foremost Duct, Inc. , 1-800-521-9316,who manufactures it. I'm sure it is more expensive than PVC, but could eliminate static problems. Just a suggestion.
*
I'm a woodworker and I have a chance to put a shop on where I live. I don't know where to start.All I know so far is I want a slab foundation. And that is about it. I live around San Fransico Ca. so I know I will need to earth Quake prove it. Are ther anjy good books out there that can help. I olan on doing all the work my self. Except for the foundation. Any help will be greatfull. Thanks Tim