*
ADAM go to a union Fab shop tell them your problem scribble a little drawing. ask nice and they might burn it for you that day
Discussion Forum
Discussion Forum
Up Next
Video Shorts
Featured Story
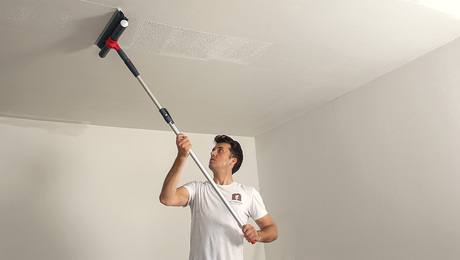
Skim-coating with joint compound covers texture, renews old drywall and plaster, and leaves smooth surfaces ready to paint.
Featured Video
How to Install Cable Rail Around Wood-Post CornersHighlights
"I have learned so much thanks to the searchable articles on the FHB website. I can confidently say that I expect to be a life-long subscriber." - M.K.
Replies
*
I need to remove a load bearing wall in a 2 story.
The owners (actually brother in law and sister in law) want the same look we got in the kitchen, burying a microlam up in the ceiling. (That was only 7 ft span)
Now, in the living room I need to span 14 feet. Problem is the 2nd floor joists are only 2x10. Gives me only 9.5 inches to play with.
Given the loads, I can't find any engineered beams to work. LVLs, etc. need 11.25 inches, miniumum.
So, my question:
Are there any other systems (Steel I beam with integrated wood header?) that will fit in a 9.5 inch space. (Width is not a problem) Barring any neat solution, I'll need an engineered steel ibeam, with holes and cross bolts to hold a 2x wood header which can carry the joist hangers for the floor. Assemble on the floor and then just slip it up between the 20 or so floor joists precisely cut and aligned....Nightmares
I've tried to convince them that sometimes a post can be an attractive esthetic addition to a room. 8-( (They ain't buying)
Help. - Any other ideas?
Thanks,
Adam
PS. Don't worry, unless the solution matches one of the beam span design tables I have, I'll go to an engineer for analysis- I'm just looking for different approaches (if any).
*Adam - Assuming it will take the load, I would take a 9" steel beam and weld a 1/4" steel plate to the bottom that sticks out at least 1-1/2" from the flange of the beam to catch the ends of the floor joists. Then notch the ends of the floor joists to receive the plate. The only problem with this approach is that you need to find a way to stabilize the beams laterally. Good luck.
*That engineered steel I-beam is the right direction to go. I'd get a plate welded to the bottom to catch the joists, solid blocking between joists on both sides of the beam. No nightmares.
*Good suggestions. Although (I learned this here), you might wnat to taper your notches instead of just making square cuts. Tapers will be less likely to split where the notch is.
*Gentlemen - Bearing on a steel wide flange section (I-beam) if not over the top flange, is intended to be on theb webof the beam, not the bottom flange. This sounds like a classic case for a flitch plate beam with hangers if the plate doesn't get too thick.Jeff
*J.C.-please explain
*Flitch Plate or steel beam bearing? I'll assume you mean bearing on the beam. There is a difference between joists bearing on the web of a steel beam (ie, through-bolted blocking with joist hangers)and having joists bear on the bottom flange. Bearing on the bottom flange is not considered good practice. For instance, look at the steel connection details, beam-to-beam on a typical steel frame design. The connection is always plated web-to-web, with considerable effort taken to cope away flanges, etc. to properly make that connection, whether bolted or welded.Undoubtedly there is a PE (structural) posting here that can add to this in a more technical way.PS - IF you meant explain flitch plate please disregard the above, but I assumed that most builders would be familiar with them.Jeffb Been there, done that, still standing ...
*Thanks Jeff. I am familiar with both. My question is really more like can't the inherent weaking of the flange loading be overcome by proper sizing of the beam. Can't the strength of the flange be calculated and used to hang the floor loads from the bottom?14' of load bearing wall makes for a helluva big flitch plate and therefore quite a good bit of weight to toss about- the I-beam would be attractive because tolerances could be more forgiving...
*A simpler solution would be to sandwich a 1/4" steel plate between 2 9 1/4" LVL beams. Fasten with 3/8" through bolts @ 2' centers. I've seen this used before an it works fine. Also; I recently built a laminated beam in place using 2 x 6 glued with polyurethane glue and 8" lag bolts. 6 layers carry a 10' span from a previously bearing wall quite nicely.Just Bob
*Bob, Without some more info, how did you determine that the combination of 2 LVL's and one 1/4"tk plate would do it? What grade of steel, how thick for the LVL's, what was the load per ln ft?, are there anypoint loads?My point of course is, This may work most of the time in most situations (I don't know, I never tried it) but without knowing the details, I'm not ready to give the definative answer.
*ADAM go to a union Fab shop tell them your problem scribble a little drawing. ask nice and they might burn it for you that day
*Adam,I just recently did (just as you described) 14' with a W6X25. With 9.5" you have plenty of room for steel. Find a PE.Good Luck,Jerry
*Based on articles in FHB and JLC by PE's and my own grad school classes in structures a long time ago, flitch plates are not very efficient. Because of the way steel deflects differently from wood, the flitch has to be designed to carry entire load; the wood only supports it lateraly; and there is no benefit of a flange.I believe that a 9" wide flange packed out between the flanges with 2by ripped to fit snug and bolted through the web would be simplest and efficient. Temporarily support and cut all joists; insert bew beam; and install joist hangers.This requires a simple load calc for the beam, a little design for through bolt spacing, and proper selection of joist hangers.
*It's not so much a question of efficiency but rather detailing in tight quarters. With a flitch plate you don't have to be concerned with having to blocking out to the face of the flange.I agree that with LVL's there is less need for flitch plate beams. Just sounded logical in tight quarters. A sandwich of LVL's and 1/4" or 3/8" steel plate would be really strong.PS - The bolt pattern is important - 2 @ each end and 24" o.c., alternating top & bottom is typical.Jeff
*As a matter of principle, you want the loads to be symmetrical with respect to the vertical axis of the beam. It's much more of a concern with heavier loads in steel-framed structure, after all, we are talking about residential loads here. I just meant to make the point that bearing on a bottom flange is generally not considered good practice.Jeff
*Ryan:Obviously you would need to do a structural analysis of the loads to determine the thickness of the plate, the bolt pattern and yes the number of plys of LVL. My assumption was this would be a standard residential loading situation with 40 LL and 20 DL. A 2 ply 9 1/4 LVL will carry 329 lbs/ft under normal conditions on a 14 foot span. I wopuld have to consult my Steel construction manual for the load carry capacity of 1/4" plate as a beam (my assumption was; "it'a big enough, it's strong enough"). The calculations for the carry capacity of plate steel sandwiched between two beams should resemble a downgraded "I" beam (the carry capacity lies in the web and not the flanges which only provide lateral stability).Just Bob
*Thanks everyone.Some great options to try. I'm gonna sketch it out and see what the fab shop suggests. Called one down in Sacramento and they have a PE who will look it over for a nominal fee if they supply the metal.I also liked the LVLs laminated with steel. Might be easier to transport.Again, thanks.
*If a welder/ironworker pounds a nail or two for profit, is he a rat bastard as well?Not meant as any sort of insult or flame, I am genuinely curious.
*Yes RyanWods:And everytime you drive, you take work away from the bus drivers, and everytime you rent a movie, you take work away from the cinema projector guy, and everytime you cook at home, you take work away from the burger flipper, and everytime you say that it's wrong for people to do their own welding because only you and guys like you should be able to, you show that you have a very small, shortsighted, self centered, "sorry I'm on break", "not my job", teamster mentality.Make sure you don't type a reply to my comment, hire a typist to do it!
*If you're hanging on the bottom flange, the I beam probably has stiffeners welded between the top and bottom web or (less likely) was engineered to be oversized enough that the stress on the bottom flange won't cause it to deflect.I'm sure that assembling buildings that someone else designed gives you great engineering knowledge but there are several here that actually went to college for this stuff. And Jeff Clarke isn't talking about "hanging iron" on skyscrapers. He's talking about using a single I-beam in residential framing.How did I get to not like you so fast?
*Bob, I hope you didnt think I was riding you. I just would hate for somebody to follow your advice, get hurt, and go looking for somebody to pay the medical bills.
*Point taken Ryan:Free engineering advice is usually worth what you pay for it.BTW, I would never suggest that someone, somewere; facing a local code issue, take advice from another over the internet without checking it out with a competent local autority (be that an engineer or building code authority). The elegance of the solution I offer is, it can be prefabed in a shop. dissassembeld for installation and reassembled in place making it much easier to put in place. I have seen this used in similar applications and once the load calcs. are complete, the installation is a breeze.Just Bob