*
I am building a new home and would like to know the differences between 2500 psi concrete and 3000 psi. Also, what is the recommended curing time for a slab before framing starts? Current highs are averaging in the upper 80’s, lows in the lower 60’s.
Discussion Forum
Discussion Forum
Up Next
Video Shorts
Featured Story
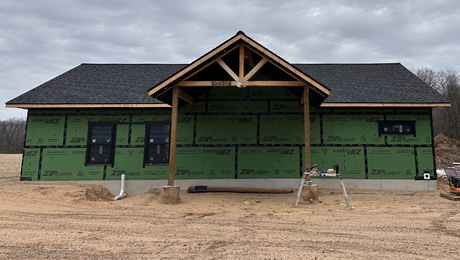
Listeners write in about earning trade-work merit badges and ask questions about radiant cooling, indoor air quality, and radon-control systems.
Featured Video
SawStop's Portable Tablesaw is Bigger and Better Than BeforeRelated Stories
Highlights
"I have learned so much thanks to the searchable articles on the FHB website. I can confidently say that I expect to be a life-long subscriber." - M.K.
Fine Homebuilding Magazine
- Home Group
- Antique Trader
- Arts & Crafts Homes
- Bank Note Reporter
- Cabin Life
- Cuisine at Home
- Fine Gardening
- Fine Woodworking
- Green Building Advisor
- Garden Gate
- Horticulture
- Keep Craft Alive
- Log Home Living
- Military Trader/Vehicles
- Numismatic News
- Numismaster
- Old Cars Weekly
- Old House Journal
- Period Homes
- Popular Woodworking
- Script
- ShopNotes
- Sports Collectors Digest
- Threads
- Timber Home Living
- Traditional Building
- Woodsmith
- World Coin News
- Writer's Digest
Replies
*
Well, Jeff, I'm not in the concrete industry so I can't speak scientifically, but as a contractor it seems the difference is mostly in the amount of cement in the mix (pea-gravel 6-sack mix is 2000 psi, 6-1/2 sack is 2500 psi), but I believe the aggregate size affects strength as well; 1" gravel is what L.A. Public Works requires for sidewalks and curbs.
As for curing time, if it's not an exposed, decorative finish (I'm seeing more of those now days), I always wait until the next day to start framing-- it keeps your boots from getting muddy. Don't tighten anchor bolts for a few days at least....better if you can wait a week or two. Just be careful on any exposed slabs (garage floor, front stoop (why is it called a stoop?)) because the concrete will scratch fairly easily for the first few days.
-Ben
*The strength of concrete is a function of the water-cement ratio (by weight). More pounds of water per pound of cement yields weaker concrete. This is why water can't be added to ready-mix after the initial adding of water at the plant. Water added to flat work to make finishing easier weakens it at the most vulnerable place - the top. A 0.7 water-cement ratio for Type I non-air-entrained cement yields about 3000 psi. It takes about half this amount of water to hydrate with the cement. The rest evaporates leaving holes. The more water added beyond the amount needed for hydration, the more holes. More holes means weaker and less watertight concrete.With ideal curing conditions (always moist) 3000 psi concrete will be about 200 psi after a day of curing, 1000 psi after 3 days, 1700 psi after a week, and 3000 psi after 28 days.
*Jeff,What Terry is saying is correct, but I would like to add some on curing concrete. Moist curing is the best, but you would need to cover the concrete with plastic sheeting for at least 7 days, and this may be a problem if the framer is coming in soon after the foundation is poured. An alternate is to apply a curing compound to the concrete surface immediately after finishing operations. Do not use curing compound in areas where vinyl tile is used. Also. plastic sheeting will cause surface discoloration, so you may not want to use it in the garage area. Irreguardless, do something to cure your concrete.Mike
*This is the first time I have encountered the "evaporates leaving holes" idea. My understanding of the hyrdration process is that each molecule of Portland cement can bond with a VARYING number of molecules of water. The minimum number of molecules of water per molecule of Portland cement yields a mix that is too stiff to pour...but it will harden and be very strong. So, we add a little more water to increase the plasticity of the mix, and each molecule of Portland then bonds with a larger number of molecues of water, weakening the conrete to some degree. Get carried away with a soupy mix and each molecule of Portland bonds with still more molecules of water, weakening the mix still further. In any case, concrete is weird stuff, full of surprises, and unforgiving. After a wee form blow-out on our porch, my wife has forbidden me to ever pour concrete again at our home. Hope she'll mellow, 'cause I really need that new shop.
*What Terry says is not correct. True , strength of concrete is a function of w/c ratio, but it is also a function of lbs of cement, lbs of aggregate, admixtures, addition of pozzolans, moisture content of aggregate, curing temperature, relative humidity, and amount of water. The statement that a 0.7 w/c ratio yields 3000 psi concrete b maybe true for one particular mix design, although I would b neverhave a mix with as high as a .7 w/c ratio (try .45). And the statement that evaporation of water leaving "holes" is not the cause of weak concrete.When you order a "3000 psi" mix from your local ready mix supplier, this means that that supplier has a mix design, based on known batching parameters (lbs of water, aggregate, cement, etc.) which when cast in cylinders, per ASTM methods, and moist room cured for 28 days, will yield statistically valid results within a certain standard deviation, that the strength of cylinders (6" dia, tamped per ASTM specs), when tested against another ASTM standard will be at least 3000 psi in compressive strength. When the truck leaves the yard, the driver should add sufficient water b so as not to exceed the w/c for that mix design.The driver should also knowb how much water he can add ( i.e. "temper")and not exceed the w/c for that mix design.Again, Terry is wrong about not being able to add water after batching at the plant. In fact, water is never added at the plant, it is added in transit from the tank on the truck. Ideally, you add and mix sufficient water so as to provide just the right amount of water for each cement (or pozzolan) particle to hydate fully, and no more. In the real world, we've all seen finishers or drivers who add enough water to to make a soup w/out regard to the carefully designed mix from the plant.Terry is also incorrect in his rules of thumb for strength of concrete vs. time after placement. I've seen 3500 psi mixes achieve 3000 psi after 4 days...better than 5000 psi at 28 days. I've also seen 3000 psi mixes which were lucky to get 2400 psi in situ. And this is the important point: the design strength is based on b controlled curing conditionsvastly different from the in situ conditions we all find in the field (the slab poured at a 8" slump, poorly screeded and consolidated and left uncovered on a hot, dry, windy afternoon). Do you think that slab is really 3000 psi? To get to JW's question, I would rarely use anything less than a 3500 psi mix design. A little extra cement goes along way towards creating a denser, superior product. I have always felt that the true cost of concrete is in the preparation, formwork and finishing. The cost differential between a 2500 psi and a 3500 psi mix is nothing compared tothe labor and preplanning. From your highs and lows, I would guess you are in a similar climate as ours (SAn Diego) and with proper finishing and curing, you'll be at 70% of 3500 psi w/in a week. You'd probably be safe to start seriously working on your slab after 4 days. And if you're concerned about workability, talk to your local plant and ask about High Range Water Reducers (HRWD) as a means to provide plasticity w/out resorting to water. Your finishers will thank you, your mix will cost abit more, but you'll end up with a stronger, denser product.Finally, Mike O'Brian gives good advice. If you can't afford the time to moist cure for 7 days (i.e. plastic sheeting and or "burlene", sprinkled), use a good curing compound and be careful w/ compatibility w/ future floor finishes/uses.
*
I am building a new home and would like to know the differences between 2500 psi concrete and 3000 psi. Also, what is the recommended curing time for a slab before framing starts? Current highs are averaging in the upper 80's, lows in the lower 60's.