*
I am planning to build a cabin on property I own in south central Missouri. The cabin will measure 28’x28′ with kitchen and bath down and loft up. Heat will be wood stove, air will be window unit. Which would be the least expensive way to go, slab or crawlspace foundation and any drawbacks I should be aware of since I will be doing all the work myself except for the concrete? Thanks.
Discussion Forum
Discussion Forum
Up Next
Video Shorts
Featured Story
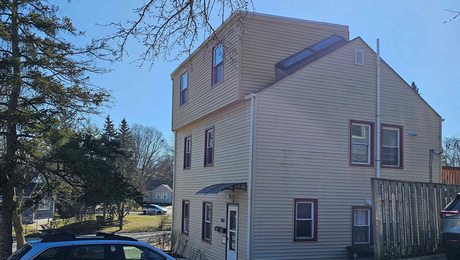
Listeners write in about greedy dormers and shop class and ask questions about steamy storm doors, fireplaces, and insulating a basement.
Featured Video
How to Install Cable Rail Around Wood-Post CornersHighlights
"I have learned so much thanks to the searchable articles on the FHB website. I can confidently say that I expect to be a life-long subscriber." - M.K.
Fine Homebuilding Magazine
- Home Group
- Antique Trader
- Arts & Crafts Homes
- Bank Note Reporter
- Cabin Life
- Cuisine at Home
- Fine Gardening
- Fine Woodworking
- Green Building Advisor
- Garden Gate
- Horticulture
- Keep Craft Alive
- Log Home Living
- Military Trader/Vehicles
- Numismatic News
- Numismaster
- Old Cars Weekly
- Old House Journal
- Period Homes
- Popular Woodworking
- Script
- ShopNotes
- Sports Collectors Digest
- Threads
- Timber Home Living
- Traditional Building
- Woodsmith
- World Coin News
- Writer's Digest
Replies
*
Bill,
Looks like we will be neighbors of sorts. I have a 26 x 28 concrete block hunting cabin outside Ash Flat in North Central Akansas.
I recommend a concrete slab. Typical construction method in the area is a conventional footing with one or more often two courses of block and one course of cut-away "L" blocks (which form for the slab). The area inside the block foundation is filled with sand and compacted. Plumbing is roughed in, plastic vapor barrior is put down, and the slab is placed. Some folks use metal mesh in the slab and some use fiber.
A slab can be cold. Particularly after the place has been unused for a Winter month or two. Can take some time to heat up. On the plus side, you will not have to worry about a colony of skunks taking up residence under your cabin (not a joke).
You should be able to get all of your plumbing in one wall which make the rough supply and DWV easy to lay out. I did my own and it all came out OK.
Some thoughts on wood heat. Sounds romantic. It can be a bitch, particularly when you arrive on a cold rainy night, the tarp has blown off the wood supply, and you forgot to bring matches. Include a $250 vent free propane heater in your plans. You can buy a 100# cylinder at Tractor Supply Company (like a BBQ tank but 5 times bigger) and any propane dealer can provide you with a regulator. I ran a short 3/8" nipple through the wall and hook up with a hose my propane dealer made up for me. In ten minutes I have heat. A 20# tank and BBQ regulator will also work and give you a weekend's worth of heat.
I was living in the St Louis area when I built my cabin. Took about a year of weekends. It was a real enjoyable experience. I made some mistakes but I also learned a lot. Cleared, had a well drilled, brought in electricity, etc. Willing to pass the lore on. E-mail me if think I can help.
Steve
*If you guys put it up on the board, instead of e mailin', we can all enjoy it. - jb
*
Steve,
Thanks for your reply. I agree with you about the wood heat and I like your idea about the propane heater. Although I probably won't use the cabin in the winter, there are some pretty chilly fall nights where some instant heat would be appreciated. I already have electricity and water at the cabin site. Will have to have septic system installed.
Since I live and work 90 miles from where the cabin will be built, my idea was to build the walls in manageable sections to as near completion as possible in the evenings at home, then trailer them to the site and install them on weekends. Seems this would be the quickest way to get it under roof. I realize this approach would require some very careful planning and foreward thinking so as not to get to the job site and have something not fit. Any thoughts?
*
Hi Bill,
I'm in the middle of a similar, but quite a bit larger, cabin project. Some things I have learned are: Build your walls on-site, they go up very fast. If you want to build at home, build your door and window headers ahead of time. Use 92 5/8" precut studs. Sheath your walls on the deck and stand them up. If you're working alone, or with your wife, use wall jacks.
I would get a propane direct-vent (not ventless) stove or small furnace, you will be glad you provided a backup for your wood heat as Steve said...
Regards, Jim
*Hello Bill.I have to agree with Bill. Build your walls on site. They go up too quick to fool around with doing them in sections and hauling them 90 miles. If you want to build things during the week at home, maybe you could tackle the cabinets and vanity.
*
Appreciate your input guys. Have done a few remodeling jobs in the past but never built a house from the ground up. You guys have more experience at this than I do so site-built walls it shall be. That's why I'm glad I found this discussion board. Anybody else have any suggestions on the slab vs. crawlspace issue? Keep in mind I'm after the more inexpensive option. Thanks.
Bill
*
How are you at flatwork? I've seen some slabs that were pretty rough. It's pretty hard to screw up a framed deck. Just a thought. - jb
*Bill,I agree with the others. There is no need to pre-cut or pre-fabricate framing if you have power on-site.To revisit your foundation question, if cost is your only consideration, then building on block, wood, or concrete piers is the most economical. It eliminates the need for a cement finisher. If you use tubular concrete forms you can eliminate the block layer too. However, you will end up with a floor that requires insulation and will be open on all sides to skunks and other vermin. Rustic to be sure. When I offered you the benefit of my Ozark cabin building experiences by e-mail I was thinking you might have another question or two along the way. Well, Jim wants the lore here and now. Not knowing anything about your situation I really can not be very specific but the following should apply.First, have a plan. Not as detailed as the one for D-Day but one that addresses where you want to be at the end and how you will get there. Time and money in particular. Be realistic.In selecting the actual building site ask yourself this question - Is the cabin the ultimate best use of the property or will you or someone else want to build a residence, a shop building, or some other structure at a later date? It may be smart to build on a less desirable spot and reserve the best building site for the future. In my case, I build my dream "shop" and immediately converted it into a temporary "cabin." The hilltop with the views is avalable should I or a future owner opt to build a residence.Spend some time on your property when the leaves are down and you can clearly see the lay of the land. I have 21 acres. After my cabin was up I found a more desireable spot on the other side of the hill.If your site is wooded you are most likely going to need a dozer man. Forget any notion of clearing with a chain saw. A dozer is quick and it gets the stumps out. You will also need a back hoe operator (for footings, septic, water lines, and stumps the dozer guy could not push). Ask around. Local lumber yard may know about good people. My real estate agent put me on to a couple of good guys. You will find that your back hoe operator will know a block layer and the block layer will know a cement finisher, and the cement finisher will know a carpenter, and .... Get the names and numbers and make contact with them. Tell them about what you are doing and find out if they are interested in working with you. Since you will be coming in from outside it is important to get people who will be available to work when you are on-site. My first back hoe operator also dug graves. Every time I was available someone died. Eventually I had to find someone else. I will say the guys in the country are more reliable, in general, than the subs I use in town. Remember, word travels fast in the hills. Pay for work when it is done with green or good checks. If you screw someone everyone will know including the waitress at the cafe. Coffee? With tip, that will be a buck up front. They say eggs are the only things that are cheaper in the country. This is certainly true when it comes to most building materials. Plumbing, electrical, and hardware items for sure. You may be able to find competitive pricing on lumber. Ask around. I purchased my lumber and, of course, redi-mix locally and carried just about everything else in.Don't build anything until you have a favorable perk test. In my area at the time I did not need one (because I had 10 or more acres). Check with your county health department to see what you need to do. Don't rely on coffee shop advice or what you realator told you. Chiggers and ticks are endemic in the Ozarks. In the Summer, use a lot of insect repellent. In addition, I like to put out a granular insecticide around the cabin and wherever people park their cars or walk. It also helps to keep the grass mowed and underbrush cleared as does burning off just before green up in the Spring. If you are not used to the rigors of the construction site take it easy at first. Summer heat can kill you. Most important asset in the country is a good neighbor. Make friends with yours. Tell them about your plans and consider any advice they may give. There is a building materials salvage yard on Hwy 63 in Koshkonong (South of West Plains). The have incredible prices on stuff no one wants and very good prices on every thing else. Not worth a special trip but well worth a stop if you are in the area.Again, feel free to e-mail me if you have something specific (or, for Jim's sake, put up a post). Good luck,Steve
*Steve - I didn't mean to stick my nose into your business. I just get e mail from folks discussing things that seem like they could be on the board, where they would get wider attention and varied perspectives. I've always thought that was the great thing about this medium, you can monitor conversations and jump in to ask about or share ideas at any time. Sorry if I spoke out of line there. (did you ever find a source for that Hardi cuttin' blade?) - jb
*Bilt a hunting camp ,24'x32', in '74 , me, my wife and father-in-law. On weekends, 125 miles each way, so the first summer, we laid the block for a full cellar, framed the floor and put the plywood deck on and covered it with rolled roofing. Well, when it rained during hunting season you had to make sure your cot was between the joints of the plywood.Any how, by the following Winter we had our camp done.Everything was site built. execpt the doors and cabinets. My father-in-law built those in my garage during the winter, since he was retired.Site bilt the trusses too, 2x6 top & bottom, plywood gussets. Things would be easier and better now, we've got giant blue plastic tarps, pressure treated wood, lots of truss mfrs. deliver anywhere. Site build, borrow / rent some Proctor wall jacks. Get some help to set trusses(you can swing them up from the deck). And find a good restaurant halfway between your home and the camp.
*I would suggest making the cabin a tight as possible for less energy to heat and cool AND to keep the bugs out. Insulate it well because as you get older (like me) you may want to use it more in the colder times of the year. That area is beautifull in the "off season" (I grew up in Fayetteville AR). If you can, use cellulose insulation at least in the attic to keep down the radiant heat from the roof in the summer. Try to keep all of your plumbing on one wall and pitch it to be eazy to drain in the winter. An inside wall is best. Supply pipes in a slab in a house not heated year round is just asking for trouble.
*Bill:Re your thoughts about prefab walls, etc, I have to agree with everyone else that site built is the way to go. The Habitat for Humanity homes I have worked on are relatively simple and somewhat "cookie cutter" in style. Possibly, similar to what you want to build. What we have found is that, as someone mentioned above, precut framing parts save limited site time. In addition to purchasing the precut studs (93" in our area), we precut all headers, jacks, cripples, and windowsills using a cutsheet. The headers are pre-assembled. Sometimes, the jacks are nailed up to king studs ahead of time, wall Ts can be pre-assembled, and sometimes window framing assemblies are built ahead of time. For simplicity, all door and window jacks are the same size and we only use a few sizes of windows. These things make the walls go up as fast as possible, especially if you have access to a nail gun. It is always a race to get the house under roof (with tarpaper). It sounds like you may have decided to go with a slab floor, but if not, consider using one of the newer floor sheathing products. Although possibly not appropriate for FHB, on the HFH houses we use something called Advantek floor sheathing. It is basically water resistant 3/4" T&G OSB - they guarantee it not to deteriorate during the framing process (extended exposure). IMO, floor sheathing delaminating is one of the main problems associated with a prolonged framing process. Also, lumber that is left out in the elements twists up quickly. With respect to your post title " Concrete slab vs. crawlspace foundation?", one minor consideration is that you may need something to "shoot" the wall sole plates down to concrete slab. This isn't necessary if the concrete is fairly green, but the task gets tougher as the slab cures over time (say over 6 weeks). Framed is more of a DIY project, but (around here, at least) non FHB grade concrete work can be had for - well let's see - 28 x 28 *.333 / 27 * $35 = ~ $340 for labor only and maybe about $800 for the concrete @ $80 a yard; I'd say that $1140 for a floor is pretty cheap. Of coarse radiant floor heat could raise the price considerably.Although, in your case cost is of utmost concern, you may want to look into getting roof trusses, as it really speeds roof framing. I'd say that a 28' span is right on the edge of needing a crane - they can be hauled up by hand if you have about 6 people, but either way you can have the roof framed in a day or 2. Giving my rathers, I'd go with 2 or 3 other good guys and a crane. Storage or cottage and scissors trusses could give you the loft you spoke of. Roof trusses also eliminate the need for interior load bearing walls which, lends itself to a more open floor plan, and, in the case of a framed floor system, will reduce the need for midfloor piers/girders.We also use 30# felt on the roof as it lasts much longer than standard 15# during prolonged "shingleless" periods. For the same reason, we use "button cap" nails for the felt, which prevents blow off. While at the lumberyard last week, I saw a brochure for a new type of 15# felt that was supposed to be much more durable and was about the same cost per square as 30# felt. Either way, it's still cheaper to put 30# on once than 15# twice.As far as your concerns about cost, a " 28'x28' with kitchen and bath down and loft up" cabin = about 1000 sq ft which is a little more than a "shack in the woods" so you might as well face it that you can't build it for $10,000. Heck, for that matter, I don't know if they have Lowes in your area, but around here they sell house kits that include all the framing, sheathing, roofing, exterior finishes windows and doors and I bet the price is hard to beat. Of coarse, you'd have to be somewhat flexible on your floor plan. OK, I'll stop rambling...Good Luck with your project,Matt
*You might want to use ice and water shield for the whole roof instead of tar paper. It goes on quick and will last for many months without shingles. Check the prices, HD was less than half the price of any where else.
*
I don't have any questions this time, just a few comments about the responses I received to my original posting on this topic.
I must admit that I had reservations about asking for any advice about my project on a bulletin board such as this. The majority of you guys are probably professionals. You do this type of work for a living and have been doing it for a long time. I am but a novice carpenter which a pro would immediately detect by the questions I asked. There was a preconceived notion on my part that if anybody would respond, the answers I received would be short, cute, so vague as to be useless, so technical that I wouldn't understand them, or that I would be passed off as somebody who had no idea what I was getting into and had no business even picking up a hammer.
Nothing could have been further from the truth. Every one of you offered very helpful advice, some much more detailed than others. You all tried to cover every scenario I might encounter. I was given much food for thought and I percieved a genuine desire on your part that I succeed on my project with a minimum of mistakes, waste, heartache, or disappointment. Thank you all for being so helpful in sharing your experience with a novice.
I plan to break ground this spring and I'll keep you posted on how things are going.
Bill Lowther.
*If one of your goals is to really learn a lot about carpentry, forget the trusses and design/cut/build your roof yourself. It will take longer, to be sure, but maybe you'd get a lot out of the experience. It would save some money too. So now, how about a hip roof with multiple dormers, hmmmmm...MD
*
Jim,
Don't think you put your nose in my business. There are others here who have raised that to an art form.
I agree with posting over e-mail in general but I also think that it is nice to know there are folks who will respond to a direct question or two when asked.
As to the HardiBoard blade, I finally went to a tool supply and purchased the diamond blade recommended by several Breaktime posters. I have since received a package of information from Tamlyn which included a flyer on a "Diamond Blabe for all Fiber-Cement Siding" sold by Power Diamond Tools. No price. 888-968-5990.
Steve
*Bill,I know nothing about the construction trade but I enjoy learning. With that in mind, I can tell you that three of my friends, who live in slab foundation home have discovered water leaks caused by settling of the house. They all had to have the water pipes reroute. There insurance picked up most of the cost but you can imagine the inconvinience. The soil in my area is adobe. That may have something to do with the problem. Most of the GC's in my area build with slab because I am told it saves the buyer money. Good luck Jerry
*
Just have to provide a good base, drainage, and get a good
cement guy, one who knows how to pour a good floor. Slabs
don't have to leak.
MD
xx
*Personally, if given the choice I'll take a crawlspace over a slab, but I'd prefer a basement over both. The advantage of the crawlspace vs concrete: More resiliency to floor, easier to walk and stand on, access underneath, ability to place some utilities (air handlers, low boy water heaters, etc ) underhouse, access for same. Also, adding things like extra outlets and running wire for alarm systems, home theaters, plumbing for water softeners, etc is easier for the first floor.Disadvantages of crawlspace vs concrete: Potential moisture issues if not sloped properly (I don't have any problem, and it is fairly flat under house), others?? Not aware of any.
*Hello, I've been reading some of the above and would suggest to Bill that if he goes with a slab foundation to be sure and put a 6 mil plastic sheet down before he pours, and wrap it up the sides of the slab and tuck it under the wall plates.I am starting work on my own house, myself. I will do all the work. Have some previous framing experience and quite a bit of concrete experience. I don't have any experience with CMU, though. My foundation wall will be 2 blocks high. Local code requires #4 rebar around the top of the wall. How do I put vent blocks in the top course and rebar too? I understand how bond beam blocks work, but do I just let the rebar run past the backside of the vent block?Thanks in advance. Greg
*
RE poly under slab, this is standard practice however search the Breaktime archives for a discussion of installation techniques. Use "6 mil poly garage" as your keyword search. Read all responses as the conversation "wanders" a bit.
Greg:
You say you are building a crawl space? If so, check code requirements with respect to a 2 block high foundation.
*Slab would be easier and cheaper. However, I'd worry alittle about a slab in a small unheated cabin in the winter.I know a slab installed correctly shouldn't heave but if it does, what a pain to fix it inside a finished cabin.
*
I am planning to build a cabin on property I own in south central Missouri. The cabin will measure 28'x28' with kitchen and bath down and loft up. Heat will be wood stove, air will be window unit. Which would be the least expensive way to go, slab or crawlspace foundation and any drawbacks I should be aware of since I will be doing all the work myself except for the concrete? Thanks.