What is the accepted way to make a cement slab for an outbuilding or shed? What about a landing from deck or porch stairs? Should the thickness be 6″, 8″, or ???? Should piers be used in the process? Should rebar be used to tie the piers to the slab? I live in the southern wisconsin area, so I assume a slab would move if it did not have some way to hold it in place. I have never had a chance to do any concrete work and I have a lot of unanswered questions about how to do it correctly. It seems one guy says to do it this way or that. Who is right? What about under the slab, should it be sand, gravel, both??? Help!
Discussion Forum
Discussion Forum
Up Next
Video Shorts
Featured Story
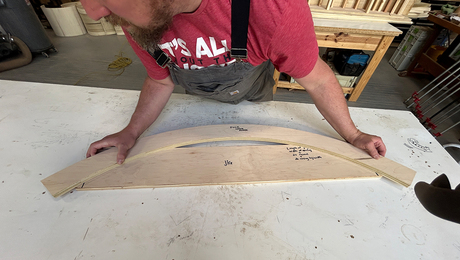
Making mitered head casings is a breeze with this simple system.
Featured Video
Builder’s Advocate: An Interview With ViewrailHighlights
"I have learned so much thanks to the searchable articles on the FHB website. I can confidently say that I expect to be a life-long subscriber." - M.K.
Fine Homebuilding Magazine
- Home Group
- Antique Trader
- Arts & Crafts Homes
- Bank Note Reporter
- Cabin Life
- Cuisine at Home
- Fine Gardening
- Fine Woodworking
- Green Building Advisor
- Garden Gate
- Horticulture
- Keep Craft Alive
- Log Home Living
- Military Trader/Vehicles
- Numismatic News
- Numismaster
- Old Cars Weekly
- Old House Journal
- Period Homes
- Popular Woodworking
- Script
- ShopNotes
- Sports Collectors Digest
- Threads
- Timber Home Living
- Traditional Building
- Woodsmith
- World Coin News
- Writer's Digest
Replies
What you really need is information specific to local practice in your area, and engineering information specific to whatever project(s) you have in mind. Different soil conditions require different ways of building slabs, and if you are trying to support a building, or part of one, you need engineering that takes local conditions into account. A simple landing on grade could probably be a 4" slab on a bed of gravel... but maybe not.
Are you suggesting an engineer is consulted on a project by project basis due to different soil? I do not plan on doing home additions or something so crictical, just maybe an outside storage shed or garage. I see alot of what goes on in the area and it never seems consistant. Also, I think consulting a engineer for small projects can get expensive and decrease my chance of getting the job if other guys do not follow the same practice. I usually do framing and trim work, but I have been asked to do some smaller structures and usually hire someone for the concrete which is getting to be a hassle. Not to mention, as I said before, one guy does it one way and the next another. I guess what I would like to do is be informed enough to either be able to do our own concrete or be informed enough to know the contractor I contract is doing an acceptable job.
I would agree that an engineer (I am one) is overkill on a garden shed project. However, whoever is doing the design and prep work needs to understand frost heave in your area.
If you have water, freeze/thaw temperatures, and fine-grained soils (silt/clay) you can get frost heaves. So you have to eliminate one of more of those three. Typically fine-grained soils are removed and replaced with non-frost suspectible (NSF) soils. Although a RFH building could plan on never freezing. And some buildings in norhern Alaska are refrigerated so to never thaw.
While an outside storage shed is nto very critical, a garage can be. Not only might there be a $40,000 SUV inside, but sometimes people sleep in them. And the storage of fuels and chemicals and power tools make it a common place for a fire to start. Also, the size makes it at risk to settling and/or frost heave.
Like every aspect of construction, concrete work involves skill and knowledge. No reason you can't pick those up and starting small is a good way to do that. Reading up on it and watching/working with a concrete crew would also be a benefit.David Thomas Overlooking Cook Inlet in Kenai, Alaska
Thanks for the info. If you had to recommend good reading material for information on concrete, what would it be?
One of the problems is that you question is way too generic.
An outbuilding can be a 40x60 garage/workshop or it can be an 6x8 storage shed.
A very, very generic answer is that is it is small and does not support much weight an unsupported slab can be used.
If it supports lots of weight, if it is heated, or it has to maintain fixed height because it ties into, one way or another, then you need footings below frost level.
In either case it is good practice to clear the suface and use gravel under the slab so that water will drain away and reduce the possibility of frost forming under the slab.
If your area has building codes contract the building inspecting department. They often have recommend plans for some basic structure that work in your area.
a typical slab is 4 inch with no rebar. a small footing is desired but not needed for like a patio. if weight factor needed just thicken to six inches. anything over six is over kill, wasting money. add some rebar is and only if a weight factor is needed. rebar does not control cracking. I alway use fiber but some people dont like it. welded wire is also used although I myself consider it a waste of money.
It depends what you building, tell us and we will tell you how to do the slab.
The project in hand is a 10' x 12' shed. The building will not be heated and will be used to store a small riding lawn tractor and misc. yard equipment. Not such a heavy load in my opinion.
four inch slab, with fiber 3000 psi mix, turn down footing 8 inch by eight inch. this is no frost area. frost area will be different ,. also place on compacted soil with vapor barrier.
add some anchor bolt. lay copy piece rebar in footing #4
Edited 9/5/2004 7:34 pm ET by BROWNBAGG
What do you mean by " this is no frost area" and how would it be different?
if you in a frost area, you have to dig the footing down below the frost line, some place two three feet. where Im at we have no frost line. By digging below frost it will keep the slab from heaving. people from up north can give you a better idea
I realize the questions are very generic. I am trying to pick up the basics and build on it. Thanks for the help.
I think what brownbagg means is if you're in an area that doesn't have a frost depth, like Arizona, you can build your shed on a four inch slab with 8 inch thickend edges. If your are in Colorado, that design won't work.
I am currently building a 18' x 24' detached garage for someone. In my area of Colorado, we can pour footings below frost line, the stemwalls to grade, and then a 4" slab inside the walls. Or use a monolithic slab, aka frost protected shallow foundation.
A mono slab here is a four inch slab with 12" wide x 12" deep thickened edges and two #4 around the perimeter. This design is for UNHEATED, and DETACHED garages only, otherwise you must get to the frost line. Actually to just heat it, we can line the forms vertical and the trench with 2" blueboard.
Hope this helps
ColeCole Dean
Dean Contracting
Got it! I thought brownbag was refering to my neck of the wood, which is in a frost/freeze area. Thanks for all the help.