It’s always been my assumption that a bed of crushed rock should be placed before pouring a foundation. I’ve been seeing some instances where it hasn’t. Can any of you tell me whether it’s necessary. I’d hate to be wasting money on unnecessary steps, although I’d hate to leave something out that would make for a good solid foundation. By the way I live in Washington state.
Discussion Forum
Discussion Forum
Up Next
Video Shorts
Featured Story
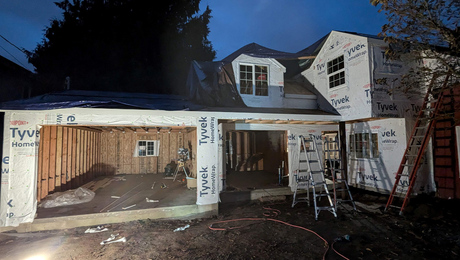
The FHB Podcast crew takes a closer look at an interesting roof.
Highlights
"I have learned so much thanks to the searchable articles on the FHB website. I can confidently say that I expect to be a life-long subscriber." - M.K.
Replies
lydensden,
I don't believe it is neccessary at all times and all places.
I live in Oregon, during the summer months we often poured footings on bare ground (undisturbed subsoil), but during the winter rains the ground becomes so soupy with the clay here that we almost always had a lift of 3/4 crushed spread out immediatly after cutting the lot to provide some drainage and keep things out of the mud.
Engineers usually design foundations for dwelling spaces and most other structures. When in doubt they use soil technicians as consultants to determine bearing capacity. Often undisturbed soils need no treatment - dig trench, set form, place footing and strip. If there is fill material in the soil then often a bed of granular material such as you describe will be called for.
So you decide: have it engineered and remove the guesswork, or give your own skills, experience and insurance cover a workout.
Engineers usually design foundations for dwelling spaces and most other structures
I would disagree with that--I don't recall ever working on a house that had an engineered foundation. Around here it's whatever the architect drew and local practice.
"This is a process, not an event."--Sphere
And I'm a legitimate certifiable Tool Whore.--Dieselpig
Heh... you need to come over to my house then. After the previous foundation was demolished through neglect, frost heaving, and water damage, we lifted the old girl, blew out the rubble / brick walls and started over.I never wanted to deal with this sort of problem again... so an engineered foundation it was. Commercial-spec, 12" thick, with #4-60 rebar on 14" and 16" centers... I wired some of it myself. Running footings on the inside, radon mitigation, etc. Now the clay outside can heave, it can misbehave, but the foundation and the footings (also re-inforced and tied into the foundation walls) will hopefully just laugh.
Sounds like you have quite a foundation!
I wasn't saying engineered foundations aren't a good idea, just disagreeing with the statement that MOST foundations are engineered.
Agreed.However, I would wager that the SOP for most foundations is to follow a plan that has worked elsewhere in the region... some might go as far as saying that the minimums set out in a building code (if it exists) represent some sort of "engineered" standard.The bottom line for me is that the requirements are quite site-specific. Deep foundations in clay soil in a cold climate will experience very different "living" conditions than shallow ones in sandy, warm soils, etc. We have exterior insulation, waterproofing, etc. plus 12" of gravel under the slab to address the myriad of local problematic conditions. In areas with better drainage, warmer conditions, and no radon, this would perhaps not be necessary.
I've always understood that compaction is the important measure of suitability. Although local building inspectors seldom perform tests, they are usually pretty knowledgeable about soil condition and how that effects the stability of the substrate. What is often called for and usually advisable is a motorized compactor, a skid plate with a lawnmower motor on it. One person fine grades the excavation with a shovel and rake while another drags the compactor over the graded fill. This operation provides a precisely graded and equally compacted surface for the footing form.
It's only when rain has turned the excavation to muck or when a mistake has been made in digging the footings too deep, that gravel is required and then it's also graded and compacted before the footing forms go in.
Vibrating compactors are available at most equipment rental places.
There may be cases in poorer bearing soils where engineered footings call for fairly deep coarsly crushed rock, to create an effectively wider footprint.
So convenient a thing it is to be a reasonable Creature, since it enables one to find or make a Reason for everything one has a mind to do. --Benjamin Franklin
Vibrating compactors are available at most equipment rental places.they are not worth the money you spend, the vibration compactor does not put out enough energy to work.
<<they are not worth the money you spend, the vibration compactor does not put out enough energy to work.>>
While I've never operated one myself, I've built footing forms on many large federal and state government projects where they are approved of and used in just the manner I described. In fact, they are the only type of compacting machine I've ever seen in footing excavations. I don't believe they are meant to take the place of other, more powerful compacting devices. They are just a means to give uniform compaction to a few inches of loose fill.
BTW, the laborers always made a number of slow passes with them, over the same area.
I'm glad you didn't build anything I manage or own with a statement like that.
I'm glad you didn't build anything I manage or own with a statement like that.why, you afraid of doing a job right for once.
I think he understood you to be saaying not to compact at all is as good as using a vibrator.I know you meant that it would be better to use the jumping jack machine, but you did't compleete your statement to include that.
Welcome to the Taunton University of Knowledge FHB Campus at Breaktime. where ... Excellence is its own reward!
Plate compactors, which have a plate 2 or 3 feet square, aren't what you generally need here -- they're for compacting the fill under a slab, etc. A "jumping jack", though, or a narrow plate compactor (about halfway between the jumping jack and the regular plate compactor) will do a pretty decent job, producing several inches of compaction in most cases.
So convenient a thing it is to be a reasonable Creature, since it enables one to find or make a Reason for everything one has a mind to do. --Benjamin Franklin
I have used them on previously compacted engineered fill for tamping down the grains loosened by rake and shovel.SamT
Anyone who doesn't take truth seriously in small matters cannot be trusted in large ones either. [Einstein] Tks, BossHogg.
depends on specific soil and drainage conditions
here.. with our 40" of rain and lot's of clay in the soil.. i can get excellent bearing with no compaction.. just dig to undisturbed eart and pour
but with a crawl space or basement.. i always put 8" to 12 " of 3/4 stone under my footings and , with the basement, under the slab too
i know there WILL be groundwater.. so the stone allows me to control what happens to the groundwater
Only required in special circumstances. Otherwise, it's best to set the footing on compacted soil.
Footing drains must be near the bottom of any gravel, but you do not want drains below the bottom of the footing.
SamT
Anyone who doesn't take truth seriously in small matters cannot be trusted in large ones either. [Einstein] Tks, BossHogg.
Thanks all for your input.