*
Young Acchhitect want stairs on deck to be 14″ wide using 1×2 clear cedar on edge glue and nailed to each other like a butcher block deck has 7′ ,5′ ,14′ Radius. on 3 dif. levels. Anyone have a opinion whould be helpful.
Discussion Forum
Discussion Forum
Up Next
Video Shorts
Featured Story
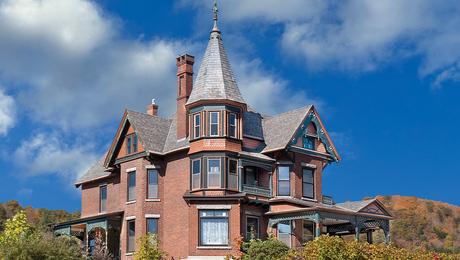
Fine Homebuilding's editorial director has some fun news to share.
Featured Video
SawStop's Portable Tablesaw is Bigger and Better Than BeforeHighlights
"I have learned so much thanks to the searchable articles on the FHB website. I can confidently say that I expect to be a life-long subscriber." - M.K.
Replies
*
Now, I realize this might not be helpful, but your young arch badly needs a clout on the side of his/her head.
*
just shoot the ***hole and be done with it. Have you priced this already? if not jack it up to cover any thing you can think of 'cause you know it STILL won't be enough to cover you in the end, guys that do designs like this usually change their minds several times in the course of construction so watch out! good luck,
Geoff
*Step 1...see cautionary notes above. Step 2 ...a cuff in the ear for you...just in case you have already priced this one, and underbid. Step 3 ...If I am right about step 2 run away, ask for more money(with tail planted firmly between your legs), or bite the bullet and work for free to try to save your rep. Step 4 ...get out the clamps and glue these treads up just like a butcher block. West system epoxy is your only option for adhesive, and the lumber should be clear and kiln dried. I quote..."has to be kiln dried". step 5 ...any fasteners should be stainless or ceramic coated zinc treated screws.I would reccomend gluing up with the west system and forget the fasteners. Step 6 ...seal all 4 sides of each step to prevent water penetration. West System Epoxy is availiable at any boatbuilding or fibreglass supplier. You can probably buy it on the net.Good luck! L
*Amen.....West system .......amen to everything Lawrence saidbuild your self a mold form so you can duplicate the curve for each tread, if you want to save timebuild half as many forms as you have treads so you can lay up several at oncebuy a lot of boxes of waxed paper, and a lot of rolls of Scotch 3"tape with a dispenser...buy the system that will give you about a half hour working life and get the dispensers, don't even think about measuring this stuff, you won't have time...tape some waxed paper to your concave mold form and clamp your 1st piece to the form, then screw it from the back,now lay up your second pc. and screw that to the first, you can go for broke and try for a 3d pc. or switch to the next form and start your 2d tread and then just keep at it, figure a day per tread, you got 18 pieces per tread, make your mold back square to the horizontal supports that the pieces will rest on until the epoxy kicks....Start with the small stairs and work your way uptell him you'll lay up the first treads T&M and make sure you get your best rate and mark up the matls to the max. then use the same production rate for the next two sets and give him a fixed price...if you get better, you'll make some money, if you don't at least you won't lose your shirt.You have to do this indoors (unless you're in Florida)because you want to control the temp/humidity so it will be easier working the epoxy.After you have your treads laid up, take a belt sander and clean them up....the cedar is going to want to split and check and the treads may warp (they're 14" wide)so make them thicker than your finish depth so you can dress them front and top after they stabilize...I don't think I'd leave these in place unfinished, because the cedar is going to soak up every drop of water, and oil, and bubble gum and gin & tonics, so figure some kind of durable non-skid finish.If you don't have a Marine Supply store , try the web at Jamestown DistributorsThey ship all over the world and can tell you all about West system....tell 'em I sent ya and their check is in the mail
*Randy,First write a letter to the architech and tell him you think this is going to be horribly expensive and an uncomfortable step. Can you get to code using a 14 inch tread and the rise you have? Make him give you about 20 drawings from every angle so there are no mistakes about what he wants. I love curved stairs, but these strike me as monumental stairs that look nice but wont be a comfortable step. You may also need to fabricate a steam bender. Or just make some templates and have a local millwork shop biuld the treads.Rick Tuk
*Best stain I have ever usedhttp://www.weatherbos.comAmmonia and water based, goes right into the wood.Bio degradable, and will not harm plants.L
*
'b' UPDATE ON CURVED STAIRS WITH 1X2 CEDAR 1. I did not quote a price to customer , Young Arch. did before asking me $30,000 for deck. I just laughed . We live in Canada , the ground is frozen 12" down , I used a jackhammer to dig 23 holes for footings . Put tent over work area ,1100 sq. ft. deck plus heater. Arch. added planter 7x9' beside deck had to dig 1 pick up box of frozen dirt for footing. The customer has deep pockets and was told project should take 3-4 weeks . I laughed so hard I pissed myself. We our in the 5th week on Mon. I,m working by the hour and the customer is paying for the labor and materials . I really enjoyed reading all your notes , it was great to see some people who think the same way. I'll update as project goes,framing is up and decking started. Will post pics. Thanks
*I used to build movie sets, a lot of sci fi stuff where they were very fond of curves. My impression is that every time someone picks up a compass its going to cost them a minimum of $10,000 per swipe regardless of what they are drawing. That said the stuff can look great and is fun to build, so what the hell as long as they are paying for it.
*
Young Acchhitect want stairs on deck to be 14" wide using 1x2 clear cedar on edge glue and nailed to each other like a butcher block deck has 7' ,5' ,14' Radius. on 3 dif. levels. Anyone have a opinion whould be helpful.