A client has a house with a huge deck constructed using 2 x 12 doug fir joists. There appears to be fungus/mold on the joists and some of the (painted) decking boards are rotting. I haven’t yet determined the extent of the damage to the joists but it may only be on the surface. Obviously the deck shouldn’t have been built using untreated doug fir but I’m wondering if, rather than removing all the joists and replacing them is there an easier solution? i.e. could I scrape the fungus off and saturate the joists with, say, a 2 part epoxy sealer or something similar? Since this approach is used for ensuring previously rotted wood won’t spread or return. I would obviously replace those joists were the structural integrity has been undermined.
Thanks
Discussion Forum
Discussion Forum
Up Next
Video Shorts
Featured Story
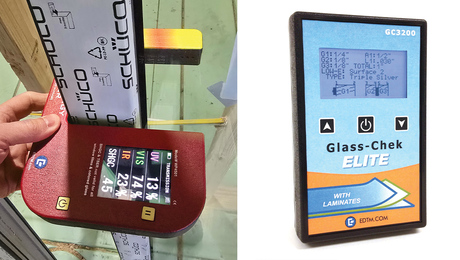
New devices showcased at the Builders' Show make it easy to measure glass performance, u-factor, SHGC, window thickness, and more.
Featured Video
How to Install Cable Rail Around Wood-Post CornersHighlights
"I have learned so much thanks to the searchable articles on the FHB website. I can confidently say that I expect to be a life-long subscriber." - M.K.
Fine Homebuilding Magazine
- Home Group
- Antique Trader
- Arts & Crafts Homes
- Bank Note Reporter
- Cabin Life
- Cuisine at Home
- Fine Gardening
- Fine Woodworking
- Green Building Advisor
- Garden Gate
- Horticulture
- Keep Craft Alive
- Log Home Living
- Military Trader/Vehicles
- Numismatic News
- Numismaster
- Old Cars Weekly
- Old House Journal
- Period Homes
- Popular Woodworking
- Script
- ShopNotes
- Sports Collectors Digest
- Threads
- Timber Home Living
- Traditional Building
- Woodsmith
- World Coin News
- Writer's Digest
Replies
if you fix one spot now, what keeps the adjacent areas from not rotting? and how do you limit your liability on the repairs?
I'd say new deck.
As I said, it may only be on the surface in which case if there's anyway to clean the affected joists up and protect them then that may be a significantly cheaper alternative. But if the joists are beginning to rot then they should obviously be replaced.
replace the joists?
where you are going to have the most problems is where the decking is nailed to the joists and where the ledger is fastened to the house. theres no way to replace the joists without removing the decking. then the posts for the railing are fastened to the joists also
a new deck is inevitable
"a new deck is inevitable"
That would make a great rubber stamp builders could use on the foreheads of enquiring clients.
the deck is toast.... the more you replace, the more you'll findMike Hussein Smith Rhode Island : Design / Build / Repair / Restore
I used the epoxy (I think it was Rot Doctor?) on interior framing to cover over the damaged floor joists in a leaky toilet situation. The leak was fixed, rotted joists cut out, replacements dropped in and the "not-so-bad" joists got a coat of epoxy and a new sister.
As a practicing organic chemist, let me tell you, that's a potent blend of solvents! I switched to a full respirator about 30 seconds into the operation, and I had to swap cartridges less than 30 minutes later! I could smell it in the basement for weeks later.
More to the point, the actual solids load in the epoxy seemed pretty low, which makes sense: too much solids and you don't get good wood penetration (there's a dirty joke in there somewhere...). Because of that, I can't imagine it would do real well without multiple coats or soaking outdoors, but maybe I'm wrong.
Seems to me that once you've spent the labor to lift the old decking, sort out the good from the bad, scrape the old joists, fix/replace rotted joists, epoxied semi-rotted boards, and rebuilt, you'd still end up with an old, fungus-prone deck to show for it?
No matter how bad it looks on top, it's always worse underneath...
-t
"No matter how bad it looks on top, it's always worse underneath..."Can't agree.When built right, a deck frame can see 3-4 surface replacements in it's lifetime.I don't have any idea what the condition of his deck frame is, and nobody else does either until he takes up the surface.
Welcome to the Taunton University of Knowledge FHB Campus at Breaktime. where ... Excellence is its own reward!
Obviously the deck shouldn't have been built using untreated doug fir
That is not obvious, but I'll respond to that second.
First, you should determine how extensive the mould and rot are. It may indeed be that the deck is toast, but if it's just surface mould on the frame with a few rotted deck boards, you can save the frame.
As pointed out, the place you will likely find the most rot is at the wall ledger. (In bad cases, the rot eats right thru the sheathing and attacks the sole plates of the wall.) You need to pop enough deck boards to see what the ledger looks like, and if you see that it is badly rotted, you need to yank the whole deck off the house.
Surface mould can be addressed by scraping it off and then treating the wood with Pentox or any one of a number of similar wood preservatives which are copper-based. That will kill any spores you missed with the scraper and discourage new air-borne ones from surviving.
Spot rot in joists that does not go deeper than 1" in a 2x12 can be dug out and plugged with epoxy wood filler putty (Abatron makes a good one). This type of putty can be hand-faired flush with the joist surfaces, and it hardens to a nailable, sandable, paintable substance. Do make sure you dig out all the rot before you plug the void.
As to the second question, whether or not the deck should have been built with untreated doug fir, that is not really the question to ask. The deck should have been built so that it drained properly. If it had been, there would be no rot or mould as the lumber it was built from (whatever species) would have dried after wetting and not provided a good medium for mould or rot spores to grow upon.
Things you can do when rebuilding this deck to avoid a repeat performance are:
Dinosaur
How now, Mighty Sauron, that thou art not brought
low by this? For thine evil pales before that which
foolish men call Justice....
D wrote:
Make sure all the decking boards are nailed down with the heart upwards so that the planks crown towards the weather rather than cup.I remember my grandfather (who was a pilot not a carpenter) telling me this when I was a kid. I don't remember why he told me, but I remember it.However I have found it to be not very helpful advice, because other factors - knots, wany areas, other aesthetics - very very often trump this objective.
I have found it to be not very helpful advice, because other factors - knots, wany areas, other aesthetics - very very often trump this objective.
Nothing's perfect, but that doesn't excuse ignoring basic technique. Bad knots should be cut out; wane as well. Slant-grained boards where the heart moves from one side of the centerline to the other over the length of the plank should be cut at the transition point and flipped so the heart is always up.
You should listen to your grandpappy, bud. He knew what he was talking about. If you ignore his advice and nail 'em down 'best side up', you'll wind up with a bunch of gutter boards scattered all over your deck. They'll not only hold water and rot, the sharp, upcurled edges of a cupped board can put a nasty slice or splinter in the bare feet of the unwary.
Dinosaur
How now, Mighty Sauron, that thou art not broughtlow by this? For thine evil pales before that whichfoolish men call Justice....
First a disclaimer - I realize that PT 2x6s aren't prime deck material.
Anyway, I built a small deck for myself recently, 16x16, out of said PT boards, and out of approximately 35 deck boards, I can say that the the pretty side was in 90% of cases the 'cup-up' side, and was pretty darn ugly. The ugly side (cup-down) was really really ugly. I'd rather take my chances with them cupping up, than with the cavernous knot holes and deep canyons due to wany edges on the bad sides.
Had I chosen to cut out this bad material, I would have had no full length boards, and would have had to buy easily 30% more material.FWIW this is from a reputable and good local lumberyard catering to contractors, not Home Despot or Lowes.
"I realize that PT 2x6s aren't prime deck material."
Prime or not, when I built my own deck last summer every scrap of material in it was PT. It's all very well creating a beautiful high maintenance deck for some other sap, but I'm not spending my whole life fussing with materials that nature here wants to re-absorb into its primordial soup as quickly as it can.
I realize that PT 2x6s aren't prime deck material.
That is an understatement worthy of some kind of award, LOL.
I don't know exactly why, but PT lumber is generally the scrappiest lumber on the market. If I received untreated framing lumber as bad as the best PT my local yards sell, I'd turn the whole delivery back without letting the trucker unload it. And change suppliers....
Had I chosen to cut out this bad material, I would have had no full length boards, and would have had to buy easily 30% more material.
That, I'm sorry to have to point out, is the right way to do the job.
There is no requirement to have 'full length boards' on a deck job; it's convenient if you've got a deck under 16' to do it that way, but you have to order as much material as necessary to make certain you get enough good boards to work with. Then you simply return the bad ones for credit. I don't know of many yards which won't accept returns of culls from a contractor. (Yes, they will sometimes try to charge DIYers a 15% restocking charge, but contractors won't put up with that noise and they know it.)
I routinely order 15% over my calculated needs for framing or decking; if I know the stock is going to be poor, I'll order even more. When the job is completed, I haul the culls back to the yard, and they credit my account. Done.
But what do you do if the deck is 20 or 30 feet long? Special-order long lengths from the mill and wait two months to get them? And then be stuck with left-overs and culls because special-orders are not returnable...? I don't think so.
Joints are part of life when decking anything. There is absolutely no problem having joints in a deck as long as they are properly staggered and don't land on the same joist with less than three boards separating them. A good carp does all this automatically--cullling, cutting out bad spots, staggering joints, etc.; a poor one just takes the next board off the pile and nails it down any way it falls.
Dinosaur
How now, Mighty Sauron, that thou art not broughtlow by this? For thine evil pales before that whichfoolish men call Justice....
>>would have had to buy easily 30% more material
You will eventually purchase that much or more in replacement material.
If you bought from a big box and hauled all the material yourself, you hand picked it and loaded it for about the same price that a lumber yard would have sold it to you and delivered.
I buy packages from the lumber yard I've used for 19 years. That 30% cull is stacked to the side and the yard get called for more material and pick up of the culls.
Saving a client money most often means saving my time, not scimping on material.
Home owners generally don't put a value on thier own time, so they only see a huge savings over what a contractor would do the job for. Then they end up investing much more of thier free time than they ever expected. That is when you hear them say "I'll never do that agian."
I'm not saying big box store serve up any lesser quality limber than anywhere else, but you do have to be slective when you pick it ot. Then you have to load,haul and unload everything yourself. All that equals nonproductive time.
You get a lot of arguments on heart up vs bark up. I prefer heart up as well, but as you say there are enough variables that it's not a sure bet.
As I stood before the gates I realized that I never want to be as certain about anything as were the people who built this place. --Rabbi Sheila Peltz, on her visit to Auschwitz
There is no wall ledger, it is a free standing deck. There are glulam beams supporting doug fir joists with painted deck boards. Not all of the deck boards need replacing, if they did I'd suggest replacing the frame as well. It is hard to justify going the drastic route of replacing all the framing if there is a solution that will add years to the existing structure. It is easy to say 'the deck is toast, replace it' when it's somebody elses money (even though I'd welcome the extra work) especially without seeing it.
I disagree that just by sloping the joists the water would drain and wouldn't rot the joists. If that were the case unpainted doug fir siding would be okay since the water would just drain off. Joists would absorb moisture and then cycle between wet and dry which would eventually cause them to rot.
I guess I was trying to find a solution like Abatron (which I haven't used) to see it makes sense.
the deck is toast, replace it
every contact point will have rot, every joint
go underneath and probe with an awl or a penknifeMike Hussein Smith Rhode Island : Design / Build / Repair / Restore
epoxy is good for non-structural trim & sash repairs..... not for deck structural members
I'd probably consider just spraying the thing with whatever anti-fungal/preservative one can find that won't make you go blind or kill too many fish downstream -- just try to get another year or two or three out of it.
i've seen decks last 80 years with DF framing in this wet climate.
The tops of the joists are lined with 30# tarpaper - nowdays with Vycor. no other chemical or paint treatment needed.
Welcome to the
Taunton University of Knowledge FHB Campus at Breaktime.
where ...
Excellence is its own reward!