*
Had a discussion with an architect regarding 2×4 exterior wall framing vs. 2×6 framing. The energy “saving” (really an energy use avoidance) is obviously better with the 2×6 walls. The cost of the 2×6 (studs, windows/jambextensions and additional labor) is higher than 2×4 exterior. His almost immediate response to the issue of 2×4 walls was …. “turn the heat up and avoid the additional cost of 2×6’s” Does anybody have any real data/experience to show where energy savings of 2×6 walls surpass the cost/construction of 2×4 walls???? His point was that costs can be recouped but probably not until 2098 or sometime close to that! Thanks!!!
Discussion Forum
Discussion Forum
Up Next
Video Shorts
Featured Story
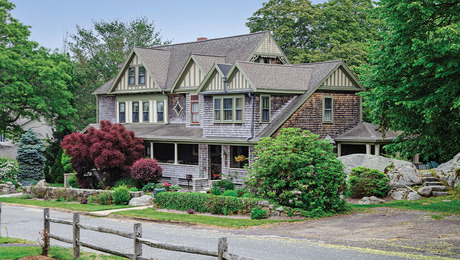
From plumbing failures to environmental near disasters, OHJ staffers dish on our worst and best moments.
Featured Video
How to Install Cable Rail Around Wood-Post CornersHighlights
"I have learned so much thanks to the searchable articles on the FHB website. I can confidently say that I expect to be a life-long subscriber." - M.K.
Replies
*
I'm guessing, here, but there's probably a web site from an independent organization which lists such things. Something like the US Department of Energy, or an energy saving advocacy group. I'm sure it's been accurately measured by many testing organizations.
The cost difference is not that great, because often with 2x6's you can space studs at 24" vs. 16" with 2x4's, so the material cost is close. Your architect or contractor would know for sure for your particular circumstances. Labor would actually be less if you use fewer studs. With many windows you buy jamb extensions no matter what, you just buy wider ones with thicker walls.
I hope you are able to find a site with actual data.
*Have your architect do two HVAC sizing computations for the different wall options.I built my house with 2x6 walls. I plan on building my shop with 2x4 walls. You can get the same R value with either size you just need some aditional sheathing.My house has 6 computers running full time now and the heating bill is non existant and I open the windows in the summer.
*Dear Jim,Your artichoke may be right. There is absolutely no way to calculate accurate payback rates from individual thermal measure. Here are the extremes:You build a great ranch house in a 10,000 HDD Vermont climate, R-60 attic insulation, tight to 1000 CFM50, with high $ electric heat. In this case, you'd better do a great job with the walls.On the other hand, you build a Cape in Maui with a 90%+ heater and no windows. Thicker walls are not appropriate here.Trying to make some sense of this, Fred
*Jim,The thermal resistance qualities/performance of a 4 inch wall compared to a 6 inch wall is indeed disproportional to the cost.A properly build 4 inch wall will of course outperform a poorly built 6 inch wall, but you already knew that.A lot of discussion centers around a particular insulation. Whether FG batts, Dense packed cellulose, blown FG and the usual group of semi and rigid insulations. Some will swear by one and swear at the others. Truth be known, none will do it all.Any will do reasonably well or better IF the house is properly sealed with a good plastic vb/ab.
*If I remember the literature, mostly from 70s and 80s, from the DoE(Department of Energy) and FPL(Forest Products Laberatory) the economics of the 2by6 system were boosted by the 2by6s being placed 24"OC.The energy comparisons were made with increased insulation and supperior placement. Some of this advantage is due to significant amounts of insulation that can be placed behind any exterior wall plumbing and electrical boxes. In 2by4 usage electrical boxes and the areas behind plumbing are largely uninsulated. They commonly have as little as 1/2" of space for insulation if they are insulated at all. Many calculations for heat/cooling loads don't take this into account. While plumbing can be planed so as to not be placed on exterior walls electrical box placements are not as flexable. With what amounts to a 2 by 3 inch uninsulated window every 12' the heat/cooling losses can be substantial.
*I think FredL is right - depends mostly on where you live. (Is it PC these days to agree with FredL???)Build in Alaska, and 2X6 walls probably look pretty good. Build in Kentucky, and it may be a waste of money. George Robert's point about doing HVAC sizing computations would also be helpful. And some utility companies will do cost/benefit analysis on things like ground source heat pumps that might shed some light on the subject.
*In case you haven't been around for a while, this is the year 2002.We have progressed beyond the 70s and 80s.The amount of space available behind or around any electrical outlet is the same whether you use cellulose or FG batts or foam or sawdust.A 2 by 3inch uninsulated window would not be significant enough to calculate the overall effect on a 12' by 8' wall. About.000434027% of the total wall area with a gap in the insulation. Using the complete wall system approach, an R20 wall system would suffer by .000260416%Sorry 4Lorn but your ship just sunk.
*LFredHi. Just trying to duplicate your numbers. I get something different and wondered why. For a 8'x12' (96 sqft) wall with whole wall R-value of 20 and a single 2"x3" (0.0416666 sqft) penetration with R=0.5 (essentially an uninsulated), I get a new whole wall R-Value of 19.67 ( = 1/(0.05*0.99956597 + 2*0.00043403)). So unless I'm mistaken, the wall suffers by 1.7%, a small but not insignificant amount. Perhaps the ship sails after all :)BTW, Jim Darr, you might check out the following links. One of them has a online calulator for wall assemblies and another compares different walls with different levels quality control.http://www.ornl.gov/roofs+walls/whole_wall/index.htmlhttp://hem.dis.anl.gov/eehem/99/991110.htmlhttp://www.homeenergy.org/archive/hem.dis.anl.gov/eehem/97/970308.htmlRegards,Steve
*The 2"x3" penetration is incomplete so your calculations are inaccurate. The outside finish, sheating, 1" of insulation and vb are still intact.The ship sunk, big time.
*Sorry, just using an interpretation of your 2"x3" "uninsulated window" statement as the model you used for calculations. So the wall assembly is more typical, and we have cummulative R values of 0.5 outside air film, 0.5 sheathing, a generous 3.0 for insulation and 0.5 for inside air film. I suppose if you had air tight outlet covers you might gain a bit from airspace inside the box. We can use plastic boxes and ignore conductivity throught them. This gives R=19.97 or 0.15% smaller. A number different than yours, but nonetheless too small to worry about. The ship sinks.
*gurgle gurgle.......
*But how about the increased chances of condensation at that 2x3 "window" and trhe portential attendent problems from condensation?Just asking, not trying to win a debate or nothing.OTOH, if you want to play battleship; my first 4 shots are at A7; B9; F8 and Z26!
*$49 a year savings in Seattle area for 3300 sq ft 2 story per this model. PS: $49 delta only changed the north wall from R14 to R36, more for other walls also thicker.Haven't pasted a excel ss for awhile, hope this works. Go to sheet 2 and enter you numbers for your size house, sheet 1 for your climate and energy rates, to get rough comparisons. e-mail me if it doesn't come thru for you, but might not get back to you till Monday. All disclaimers as to accuracy, etc. apply
*Look at the whole picture - you can also use 2 x 4's with 3 1/2" R-15 and save the cost of extension jambs for all the windows, not to mention 2" of interior space all around.Jeff
*The vb negates any increase in probability.
*Back when we were building "super insulated " houses we were taught that it didn't make since to add more insulation to a house until you controlled the biggest source of heat loss in a house and that is air infiltration. We would air seal the house and control the air in the house with an air exchanger.Controled air quality instead of having good air on a windy day and bad air on a calm day, as well as reducing your heat bill. After that was addressed,than heat loss through the envelope became a bigger percentage and was worth going after.We would build walls that were 12" thick. To reduce costs I went to a 2 x 6 wall with the air sealing and air exchange. The anual heating costs went up a little but still about 1/2 of a conventional house. My point is that maybe we should look at the project as a whole and not individual things. Don't get lost in tiny town.Rick
*Imagine buying a piece of property that has unlimited electrical power. Oak trees and pine trees are neutral and line.....whatever. The typical thinking on building a house would go like this. Since I have unlimited energy, I'll just build with 2x4 framing, no insulation, cheap aluminum framed single pane windows, and no sealing. I'd just run my heater and AC as much as I like. While this would seem like the logical choice, the house would be horrible to live in. All surfaces would be cold in the winter and you would have hot dry air blowing around just about all of the time to keep you warm. Imagine sitting in you living room with hot air blowing on you to keep warm but you body is radiating it's heat away to the cold surfaces. In the summer, the opposite would be true. Very uncomfortable. I know this is an extreme case but it's not a bad way to look at problems. Now just imagine the opposite, it's cold outside but in you well insulated and sealed house, the hydronic heat is keeping the slab and your feet around 90 degrees. The walls and windows are warm also, and the air temperature is a cool 68 degrees. Very nice and comfortable. So adding insulation and good windows isn't just to save money in 12.7 years, it's also done for comfortable living conditions that start the moment you move in.
*I like that thinking.
*The stuff put out by the folks in the really cold areas like Alaska and Western Canada seems to be the best practical advise. That stuff says that you must build a structure as a whole to be healthy, comfortable and energy efficient. And that is the priority their stuff gives.If we are talking about new construction as opposed to remodels then you first address controlled air exchange. You want enough air exchange between outside and inside to maintain a healthy and comfortable inside environment. This generally means a HRV system and extensive poly and sealing.Then you look at the entire outside structure as an insulator. Here there is a lot of bias and snake oil. In my humble opinion, ok maybe not so humble, 2x4 vs 2x6 isn't the question. The question is: Given the building's architecture, siting and local custom what is the best combination of materials for energy savings? In one place that may be 2x4's with something else layered over it. In another you absolutely must use 2x6's.Oh yes, why local custom? You are going to sell that house sooner or later. So, the ability to market that house is very important. In some areas it doesn't matter whether a 2x4 wall is just as efficient as a 2x6 one. Buyers want 2x6. So, without a 2x6 wall your house is at a competitive disadvantage in the marketplace. That may mean a longer sale time or a lower price.