*
I am building a garage for someone soon.
The mason has informed me that since it is
not tied into the house there is no need to dig down to the frost depth of 42″and lay block. An 18″ rat wall is all that is required. There is a large maple tree about 8′ away from where we are building and we would probably hit less roots going shallow.I don’t know if the slab would crack too much without a solid foundation or not.
John Keller
Discussion Forum
Discussion Forum
Up Next
Video Shorts
Featured Story
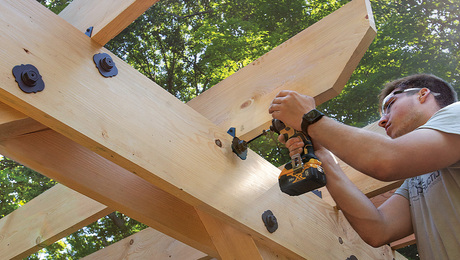
Built from locally sawn hemlock, this functional outdoor feature uses structural screws and metal connectors for fast, sturdy construction.
Highlights
"I have learned so much thanks to the searchable articles on the FHB website. I can confidently say that I expect to be a life-long subscriber." - M.K.
Fine Homebuilding Magazine
- Home Group
- Antique Trader
- Arts & Crafts Homes
- Bank Note Reporter
- Cabin Life
- Cuisine at Home
- Fine Gardening
- Fine Woodworking
- Green Building Advisor
- Garden Gate
- Horticulture
- Keep Craft Alive
- Log Home Living
- Military Trader/Vehicles
- Numismatic News
- Numismaster
- Old Cars Weekly
- Old House Journal
- Period Homes
- Popular Woodworking
- Script
- ShopNotes
- Sports Collectors Digest
- Threads
- Timber Home Living
- Traditional Building
- Woodsmith
- World Coin News
- Writer's Digest
Replies
*
I'm not framiliar with exactly what the rat wall you mentioned entails, however, your mason is correct when he says the garage need not be placed on a frost wall. Up here in the north lands of Wisconsin we usually use what we call a floating slab on grade. Prepare the site by removing the topsoil, and then place a sand pad. We try to put done 8-12" depending on the site and drainage. If the site is prone to wetness, we may put down 6-8" of breaker rock for drainage under the sand. Make sure the sand is well compacted and the final grade slopes away from the building footprint.
We form the slab with 2x12's, maintaining a trench of that depth to a width of 18" in towards the center all away around the perimeter. From that point we taper a slope up over about a foot of distance so that we end up with a slab thickness of 4" in the middle. Then we lay a grid of 5/8" rebar in at 2'o.c. in both direction with the ends bent into a 90 on the ends so they turn down into the trench. Then we lay two rows ofrebar around the perimeter. Everything gets tied together with wire ties. You get the best results when all the rebar sits on chairs or large pieces of aggregate to keep it up off the bottom of the pour. We also lift the rod in the center during the pour. It's common practice to cut control joints into the concrete so what cracking that does and will take place does so in the control joints. The rod keeps the slab from separating and the floor stays looking nice. This method allows the slab to "float" as a unit. Frost action can be minimized further by placing 2" rigid foam around the perimeter to a distance of 4' at the depth of the bottom of the slab before you do the final grade. It keeps the frost from penetrating under the slab at the edges.
As far as the large maple tree goes, I would be temped to remove the tree or cut the roots and trim the canopy back to shorten the drip line. Maples have a wide spread root systen that spreads out to or beyond the drip line of the branches above. Their root systems can cause havoc with slabs and foundations. Sewer lines and drain fields too.
Hope that helps. Anybody else have any suggestion?
*
Hi Wayne,
You covered it pretty good.
Gabe
*Great discription Wayne, you can come and do my garage slabs anytime!! And Im just down the road in Iowa. The only thing I would add is putting down a "moisture barrier" ( unless you use the insulation board) under the slab prior to the pour. This will help the cure by keeping the moisture in the concrete instead of being wicked up by the sand. Not necessary, just something to consider.Dave
*
Thanks Dave,
I didn't mention the use of a moisture barrier because I got the impression that it was going to be used strickly as a garage. If I know the structure will be used as a shop or something along those lines, we usually pour over the top of 2" rigid foam. Then we also oversize the forms and place 2" foam on the perimeter also. That makes for a pretty good thermal break and keeps the floor from getting too cold. It also helps stop the slab from sweating when we get the high humidity hot days that we are famous for up here. I don't usually have a moisture problem if the sub grade is well drained and the grade is pitched away from the slab.
Wayne
*
Wayne,
I agree that you have posted great specs....So my questions area about money!!!!
26' x30' slab for combo workshop garage. What would be your labor man hours, labor costs, material costs and finally what do you charge the client in this case?
Near the stream thinkin your building for the stars...
J
*
very very interesting about adding the extra foam insulation for usng the garage as a shop.
what about if going to use it for an indoor basketball court? (we'll have very high ceilings! and a garage door with glass panels instead of wood panels. it will also be a bit larger than most garages). any considerations in this instance?
*
Lou,
Wayne's specs are perfect for your "Michael Jordan" lifestyle...
Near the stream and singin my lobsters to sleep,
J
*Hi Lou Ann,THe 2" foam is used as Wayne describes, as a thermal break from the frost in cold weather climates. The building is classified as for human habitation or use, (not lobsters Jack) that means it's going to be heated and people are going to work or play there.Whether it's used for a workshop or a basketball court is not relevant. The use of 2"SM would be highly recommended.The only difference in methods would be that here we only install 2"SM around the perimeter of the foundation or slab and then on the flat for the first 4 ft. only. The center area is covered in poly VB anyways so moisture is not a problem.Gabe
*Todays garage is tomorrows workshop and next years guest cottage. For what it costs, I would use a vapor barrier regardless of initial use. I know it depends on soil conditions, but here in the glacial till of THE GREAT NORTHWEST we use rebar in the thickened edge and 4" mesh to reinforce the slab. - yb
*
Thank you for all the great and free advice.
The estimates came in $1200.00 cheaper with a
floating slab than a full 42" deep foundation.
The mason bid at $2200.00 including slab, drain,
block and foundation bolts. That is the going rate for Central Michigan.
I am confident about using this method.
I can dig the trench myself by hand.
John Keller
*John You never gave any dimensions for the slab, so it's hard to know whether or not the estimate you recieved is in the ballpark or not. The method I described does not require digging any trenches, that's the idea behind the method of construction. It minimizes site disruption. The thickened edge is created by using the sand base, filling the center area with more sand to create the concave shape on the bottom of the slab. The top soil gets stripped to be reused over the fill to finish the grade and provide good soil for the lawn that will undoubtedly be planted around the structure. The whole process can be accomplished with equipment no larger then a skid steer. Strip the topsoil and spread the base. One question remains. What's the block for?Wayne
*Jack Not building for the stars...just building a floating slab the correct way. If I have a client that wants a floating slab, I bid it according to the method of construction that we use. I'm not bidding to get the work. If they think it's too high, I move on and don't loose any sleep over it. If they want it done cheaper, then someone else can do it for them. I won't cut corners to reduce the bid. Do it right or don't do it at all. The low bidder can have the headaches when the finished product doesn't preform as expected. The bitterness of poor quality remains long after the sweetness of price is gone.Wayne
*yb I have to agree with you on the use of a vapor barrier if you think as far down the road as you do....i.e. guest cottage. If you use foam under the entire slab, a poly vapor barrier is redundant. We quit using wire mesh around here about ten years ago. In floating slab construction, mesh won't/can't hold the slab together like rebar does. You don't get the kind of frost action in the ground in "The Great Northwest" like we do here.Wayne
*Wayne, I agree with your assessment on proper construction of the slab (commomly referred to as "slab on grade construction" in my area." My only additional comments would be availability of Fiber Mesh Reinforcement for the concrete which further reduces the chances of cracking and heaving, possibly using several inches of 3/4" aggrgate rather than sand, and to be sure and get a high quality mix that will produce 2500 to 3000 psi when cured.
*Wayne, The dimensions of the garage will be 20'x 28'I thought one course of block would be goodto raise the wood structure 10" off the ground.I think it will hold up better.John
*
Wayne - have to agree with you on all points. Really like your approach regarding "this is what it will cost to do it the way we do it, THE RIGHT WAY". Spoken like a true pro.
Hey, not only do we not have to deal with frost here, the missus and I have our sights set on even gentler (read sunnier) climate in about 10 years when we sell out and call it a career! - yb
*Lou Ann,I would choose between EITHER the indoor basketball court OR the glass paneled doors. Personally, I would opt for the indoor hockey rink. A bowling lane off to the side might be nice.If crime is a problem in your area, you might use translucent glass.Dan
*
Deemark
Not mentioning the psi strength for the concrete was an oversite on my part...I agree with you.
As far as using sand as a base...once again...it depends on existing soil conditions. If I think drainage will be a problem....we put aggregate( breaker, stone, gravel) down first and put a sand base over it. The sand makes it easier to form the thickened edge and the slope to the center.
Wayne
*John, A good flat worker can form a raised curb right into the slab. All he has to do is use a slightly deeper form on the outside and tie/suspend an additional form(usually a 2 x 4) to the inside of the slab. Works well for a 4" wide raised curb. Don't know how well it would work for a 6" wide curb. I've never seen anyone do that. If you decide to use block, make sure your anchor bolts stick up high enough so that the project above the block. That way you anchor the wall to the slab, not just the block.WayneWayne
*
I am building a garage for someone soon.
The mason has informed me that since it is
not tied into the house there is no need to dig down to the frost depth of 42"and lay block. An 18" rat wall is all that is required. There is a large maple tree about 8' away from where we are building and we would probably hit less roots going shallow.I don't know if the slab would crack too much without a solid foundation or not.
John Keller