*
I stopped by the site of our home under construction today, found the footings poured, and noticed the forms seem to overlap and appear destined to leave jagged sides on the footings (rather than smooth courses from corner to corner). I can see how it wouldn’t matter, but I am curious as to whether it is standard procedure.
Discussion Forum
Discussion Forum
Up Next
Video Shorts
Featured Story
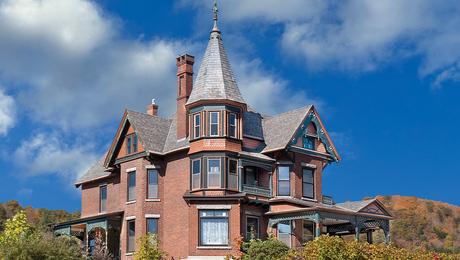
Fine Homebuilding's editorial director has some fun news to share.
Highlights
"I have learned so much thanks to the searchable articles on the FHB website. I can confidently say that I expect to be a life-long subscriber." - M.K.
Replies
*
Anything worth doing is worth doring right and with a little pride. If a foundation drain is to go around the footing it may be helpful for the side edge to be smooth and even.
We often dig a trench for footings here in VA. If the excavation is rough and uneven or rocky or has limited drive up access for concrete truck, I like this method best. We must add 8" to the height of the foundation for 8' basements. Also we can back a concrete truck right in accross the footing while pouring. No wheeling necessessary.
*Not a big deal, as long as the minimum width for the footing is met. Most crews overlap the boards to prevent having to cut and scab pieces together for that "perfect" fit.
*Mongo,Is it standard practice to form your footings as against trenching and pouring, if so why?RegardsMark
*Once-upon-a-time, in a town near here, a certain sub used to trench his footings. A few years later one foundation had severe problems, crew came in to dig out and secure below the footings. Lo and bold, the footings were about 4" thick. In came the lawyers, out flew the lawsuits. Building Inspector was sued as well. Town paid dearly to back him up. Guess what? Since then, the inspector isn't fond of trenched footings. I believe that the town's insurance policy may not even alolow them, thought not sure on that. This happened a few years before I moved here, but I've heard it through several people, including the inspector.So...yes, always formed footings. To be honest with you, even if given the option, I'd probably still have the foundation guys form vs trench them. I install under-slab drainage and radon tubing, this goes inside the footings. With less poured wall height lost to the pipe and slab, it also affords a few more inches of basement headroom using standard forms. For me, it's simply not an option due to local restrictions.
*A well built footing is level, straight, and square and has the right amount of rebar in it, sometimes they are "keyed" to help resist lateral forces. When the wall is poured on top of it, the wall pretty much "centers" on the footing. Putting steel to the surface to get a decent finish, or putting an edge on it is busy work, money better invested at the other end of the job. If I saw a set of footings with a nice edge or smooth finish, I would wonder more about that than what you describe.
*It seems that your codes are a little different to ours or maybe the overall inspection side of things is. Here our footings are designed and inspected by the Engineer and then inspected again by the Building Inspector ( or building surveyor as they now refer to themselves ) in any case as we have to warrant our work for 6 years any problems with the foundations has usually shown up by then and we have to fix it at our cost or our license is pulled.What do you do with a slab on ground? Do you still box footings?
*
Trenched footings around here have to have the grade chalked during "form" inspection. I can see the advantage of trenched footings in that the pour is keyed into undisturbed soil on either side and is not dependent on a compacted backfill to prevent lateral footing movement in the event of an unusual side load. Footing contractors who form their work in this competitive world may not be too keen on cutting up their multi pour oiled formwork for YOUR footing just to make the edges
of the footing look pretty with no overlapping 1 1/2 inch jumps.
*
I'm sure the codes are fairly similar, more on the inspection side where the variances arise. Mr. Inspector is a decent guy with a few quirks that need to be worked around.
I'm all residential, all full basements. Footings are required 42" deep.
*Eric,Jagged edges no problem. Most important thing is overall level and good bearing on bottom hard-pan with hard pan to forms being square not rounded from loose fill getting under forms. Also, re-bar top and bottom, not in middle. Question for trenchers. What do you pound grade nails into if you use no forms?
*
I stopped by the site of our home under construction today, found the footings poured, and noticed the forms seem to overlap and appear destined to leave jagged sides on the footings (rather than smooth courses from corner to corner). I can see how it wouldn't matter, but I am curious as to whether it is standard procedure.