*
My small house and furnace are 10 years old. Please excuse me for not knowing the proper terminology but a portion of exhaust duct (the one that vents to the roof) has disintigrated, rusted from the inside out. The section that rusted through is that short section attaching the furnace to the vertical. Is this common? What might have caused this? Should I do more than Just replace that segment of the duct?
Discussion Forum
Discussion Forum
Up Next
Video Shorts
Featured Story
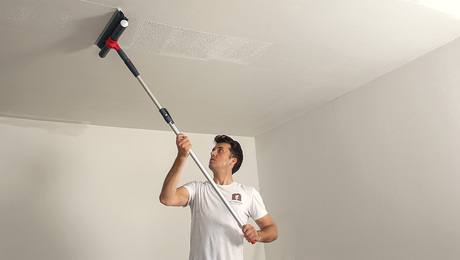
Skim-coating with joint compound covers texture, renews old drywall and plaster, and leaves smooth surfaces ready to paint.
Highlights
"I have learned so much thanks to the searchable articles on the FHB website. I can confidently say that I expect to be a life-long subscriber." - M.K.
Replies
*
Mark,
You have 2 problems. The immediate one is the rust through: you could easily be getting flue gases in the house, and those flue gases can contain carbon monoxide.
Please be aware: high levels of CO can kill you; repeated exposure to low levels can cause serious, long term health problems.
i Just because you aren't dead doesn't mean you don't have a CO problem.
The second problem is with the furnace and/or vent.
Such rust through is
b not
common, and indicates a potentially serious performance problem.
The rust is caused by water vapor (and some acids) in the flue gases condensing before reaching the end of the flue. It may be that the flue is partially blocked, or improperly sized or installed, or that the burners are significantly out of adjustment.
The existence of rust also suggests that the furnace is prodcuing large amounts of CO. (The only way to know for sure is to test the flue gases.)
All of these are potentially serious problems.
Please have it serviced
b immediately.
Not tomorrow; not next week. Today.
Don't use the furnace until it's been serviced.
I recommed that you try to find a service tech who is a Building Performace Institute ("BPI") Carbon Monoxide Analyst. As a general rule, they know more about these issues than many (most) hvac techs without that training.
FWIW, if I were inspecting the house I would probably disable the furnace (depending on the extent of the rust through.)
Bob Walker
Home Inspector
Carbon Monoxide Analyst
*To add to what Bob has said, the entire length of the flue pipe should be under a negative pressure when the furnace is in operation. If that is true, then the small holes, seams, etc will leak house air into the flue pipe instead of flue gases leaking into the house. If you want to play Mr Science (and feel comfortable doing so), you could test for negative pressure in the flue pipe by drilling a small hole and connecting some tubing (flexible copper, 2" of ballpoint pen tube, whatever) to some clear tubing with water in it. Bend the clear tubing into a U and measure the difference between the two water columns. If the one connected to the flue pipe is 1/4" or more above the one open to atmosphere, I won't feel driven to act on it today. Get someone to analyze the flue gas composition (O2, CO2, CO, and smoke) which can be used to calculate furnace efficiency and suggest adjustments. Your gas compnay might do that for free.If the pressure in the flue pipe is not well below that of the room, your flue pipe could be too short (in total height), too narrow (or constricted or plugged) or too big (unlikely). It can not be too tall. And you could then be leaking piosonious flue gases into the house. I'll quote Bob and myself from previous posts:Don't bother with the $39 P.O.S. Carbon Monoxide detectors without digital readout at Home Depot. Slightly better is the Kiddie Nighthawk with readout ($50), better yet is the AIM Safe-Air Products Model 935 Low-Level CO Monitor ($75) which avoids the damnable UL requirement that CO detectors not tell you about low levels of CO. (Fire Departments were getting too many calls back when units were more sensitive). I'd like to know if any detectable CO is there and see the concentration; that is very helpful in tracking down the source and route of CO. The first time I had a CO detector go off, I felt that it had been money very well spent. Here's a link with a lot of info on CO detectors: http://www.avweb.com/articles/codetect/ It has an aviation prespective - pilots are very concerned about CO, because they can't just step outside when the alarm goes off. And here's AIM's website: http://www.aimsafety.thomasregister.com/olc/aimsafety/As to the rust, it is unusual to get rust close to the furnace. On the inside, it is exposed to acidic fumes but that is okay until the water vapor in the flue gases condenses and then you have liquid acid on the metal and it corrodes. Might you be getting drips of water (from upper reaches of the flue pipe or from rain water) falling onto that section of pipe? -David
*One more thought. The corrosion very close to the furnace might be due to the operation of the pilot light. Its flue gases would cool pretty close to the furnace. You could replace that section with stainless flue pipe. -David
*Hi-I just completed an extensive re-think of a client's malfunctioning hydronic system. It consists of a 250k BTU Lochinvar Efficiency+ and Wirsbo manifolds, and tubing.When I got the project the 2 year old system was not running. My first step was to gather as much info. as possible from anyone who was in any way involved from initial installation to those that had attempted repairs and failed. In a nutshell, main problem was controller kept locking out. Last outfit on the system before me was a Wirsbo comfort school graduate. I called him and his mantra was: "system's got too much fire, not enough water, high-temp. shutoff keeps shutting the system down." He was maintaining that the furnace was terribly oversized and needed to be replaced with a new 125k BTU furnace.Seemed immediately apparent to me that there should be some less radical solution by looking at the control end of things. Upon looking at the zone controller it was apparent that some very obvious charring might be a hint. I put a jumper across the thermostat lugs on the Lochinvar and opened manually the 7 Motorized actuators in various combinations. By feathering ball valves at the main distribution manifold I was able to achieve a temperature rise that temporarily appeased whatever was going on in the main control sequence, allowing me to begin troubleshooting. Fan started, combustion air switch made, purge completed, ignitor was energized, gas valves opened, flame took... and then sometimes was almost immediately lost causing the controller to recycle. Sometimes it would fail to reestablish flame after three tries and lock out. To shorten a long story, the system was built without a bypass. Return water was too cool causing condensation that at times was presumably dripping onto the ignitor/flame sensor and tricking it into thinking it had lost flame, causing the control to close the primary gas valve and attempt reignition.The furnace is common-vented with a 75kBTU DHWH. One of my attemts at isolating variables included shutting down the DHWH and disconnecting its 4" vent from the 6" main. I disconnected it at an ell where the 4" riser off the DHWH begins a 4" lateral run to a 6x6x4 tee. The lateral leg was pitched at around 1/4" per'. I duct taped the end closed for the isolated test run. I started the furnace and let it run. After 10 minutes sitting there, I went to lunch. I returned to find copious amts. of water having dripped and dripping from a seam in the taped end. This was a major amount of condensation, I'd say at least a pint after an hour. This was the final clue that, aside from a fried zone-controller and undersized control wiring what this system needed was a bypass. I installed a full-size bypass with balancing valve along with a balancing restrictor downstream on the outlet side. The furnace began immediately to behave predictably. By manually feathering ball valves and mva's the system is now running in a way appropriate to the owner's use pattern off one stat effectively as one large zone.Point is, there can be non-furnace flaws that can cause horrible furnace/other problems. It's a good thing that before all this the furnace never really worked 'cause that heat exchanger is a $1000 part that likely wouldn't have lasted long in that corrosive environment.
*Freelance: An interesting moral: That making a high-efficiency furnace even higher efficiency (by introducing colder water) can leave too little heat in the flue gases to get the water vapor all the way out of the house. I've encountered that in standard efficiency DHWH's when running them to make warm, not hot water (a hot tub in one case, and temporary heat in a radiant floor in the other case). The telltale sign is the sizzling of the water droplets as they drop onto the burner. A slower flow fixed the former. A mixing valve and a higher setpoint fixed the later. David
*David,Good points, although I wonder about the pilot hypothesis (unless its a really huge pilot flame.) Seems to me, (although I don't know for sure) that the flue gases from the pilot would see most condensation long before the flue.BTW, what is the white powder you often see in the heat exchanger above the pilot light (esp. with a really big pilot flame?)Jim Davis (b thecarbon monoxide analysis guru) says its carbon, but I'm not so sure. I've never sen it on gas logs, and I've seen lots of black carbon deposits on those.Also, I've been drawing blanks on some terminology: the name/description of an old, non-draft induced (naturally aspirated) furnace; and the name for a non-tube type (i.e., "standard" boiler.)
*Freelance....Your story is astounding....What a bunch of horrible work and lack of common sense by the owner!I am amazed...250,000btu!?...How big a home!!!!????...We install separate units in bigger homes for zoning purposes and rarely install such a big unit. How many square feet?near the wild and crazy stream,aj
*aj-The plumbing contractor was the owner's brother-in-law. The owner was an absentee that trusted a truly shitty general and a 2nd generation plumbing contractor that saw his job as "goin huntin." The house is 4500Ft of poorly designed butt and pass logs. Standard story: lots of glass, under-insulated roof/ceilings, non-IC recessed cans, uncapped chimneys that needed to be re-flashed and capped after 2 years of caulking, walkout basement with un-damproofed, undrained, uninsulated stemwalls etc., etc.The place uses about $1000 in propane per month in zone 5 for space, water and cooking. Needless to say, it's "on the market." And just as we got the leaks stopped, the septic rebuilt, the hydronics rethought, the drainage retrofitted and the closet storage rebuilt so it would stop falling on the kids. Like $35,000 in repairs on a 2 year old place. The general was totally beyond his ken, and was unable to offer any warranty relief. Owner is kind, successful, un-vindictive. He's been the only one to step up on a project that had truly heinous flaws. He takes responsibility for having mis-placed his trust.
*
My small house and furnace are 10 years old. Please excuse me for not knowing the proper terminology but a portion of exhaust duct (the one that vents to the roof) has disintigrated, rusted from the inside out. The section that rusted through is that short section attaching the furnace to the vertical. Is this common? What might have caused this? Should I do more than Just replace that segment of the duct?