*
Ron- I’m a P.E. and your advice is right on the money. I couldn’t have said it better myself.
Fred
Discussion Forum
Discussion Forum
Up Next
Video Shorts
Featured Story
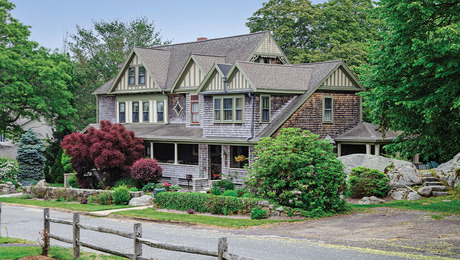
From plumbing failures to environmental near disasters, OHJ staffers dish on our worst and best moments.
Highlights
"I have learned so much thanks to the searchable articles on the FHB website. I can confidently say that I expect to be a life-long subscriber." - M.K.
Replies
*
"WARNING TO ALL BUILDING OFFICIALS" Never ever, never ever,ever,ever accept any truss plans unless drawn by a qualified design professional. You WILL share the liability and WILL be held accountable for your actions. I hope you get the message here "B", everyone here so far is giving you sound advise. It seems you fear the permit process and rightfully you should. I hope you were really apolgizing for being persistent rather than arrogant. Persistence is for a reasonable person with determination and a goal. Arrogance is usually just a by-product of stupidity. Think this one through. Keith
*Sorry-but if you can't size the gussets, you certainly can't size the members. Again- this is best left to an engineer. I'm not trying to be arrogant either.
*
Gee folks, I'm getting some real negative feelings from you all regarding truss building....and, quite frankly, it's registering. But,trusses are such beautiful devices....the picnic tables I build use trusses as supports, and, I know you won't believe me, the members are made from 5/4 X 6 PT ripped in half....yes, that's 1 x 2 5/8. And they sit ten people....would do twelve but mid-span of the bench suffers. Things are really beautiful, too....singlehandedly, I can load one onto the bed of my pickup. Perhaps, I get a friend and perform some destructive testing by pushing one off of said truck at highway speed...haha. I know, I know, "That's a picnic table," you say, and you're correct...but trusses are trusses are trusses....the same principles apply.....members are in either tension or compression and all vector forces add up to zero at the intersections (joints). Keith is quite coorect, that I fear the permit/inspection process and it is because of that that your objections register. It is a real disappointment that so much of the building process has become so regulated, so homogenized, but I do accept that safety is a reality. Are any of you saddened to see a 2 X 12 rafter employed....gee, 20 feet of 2 X 12 , when maybe only two of those twenty feet actually require such a large section modulus....always seemed like a misuse of materials. I say this as someone with an civil engineering background, not as a builder, nor as someone who is overly concerned with my time or making money on my time, Dave.
Again, I do appreciate all of your comments. Keith, I guess it is, indeed, persistence that describes me, but then again, I said, "Sorry if I SOUND, arrogant." Perhaps, I can discuss this more later...but, it's some school lunches that demand attention right now.
Brian
*
Brian,
Assuming you are in an area that uses standard building codes, there is a 99% chance that it won't fly without engineering specs and won't be worth the trouble. But to satisfy your curiosity, why not build one and test it? Given your practical experience, I'll bet it would be just fine. My totally non-professional gut feeling is that 1/4 plywood is too plyable to work well. I'd use 1/2" or more, and the cost increase is only about 20%. Use a liquid-nails type adhesive and, assuming you have a nail gun, use a TON of nails.
I definitely support you philosophically. In this age of lawsuits and people wanting life to be 100% safe, things do get over-engineered. Here, a 24' 4/12 truss costs about $40 and has about $20 worth of 2x4, 2x3, and mending plates in it.
-RandyR (the guy with the Room-in-attic question)
*
Randy - I like your encouraging tone but "liquid-nails type adhesive and....a TON of nails" is exactly the wrong answer. Plywood plates need an epoxy or at least a polyurethane type adhesive - all the strength will be from the adhesive - and as few as fasteners - all carefully located - as possible. Check out Am. Plywood Assoc. for glueing/fastening info.
But to go to a heavier roof rafter and figure out the tension joint through the "kneewall" plane (or any number of other solutions) would have to require less material cost and less time. Plus the trusses would have to be built flat on the deck and they still need lifting up.
But I admire the spirit and courage!
*B, I agree with the others you need a structural engineer to design and stamp, and that a truss manufacturer is the easiest route. But,the book Carpentry and Building Construction, Feirer Hutchings copywright 1976 does disscuss building trusses on site.Very basic info that refers to APA that Bill mentions above.Various plywood gussetsizes 3/8" being the minimum mentioned and very specific regarding grades, moisture, and glue etc..Not an all inclusive article but a starting point of information.
*A friend has a 15-yr old house that has a load-bearing wall running the same direction as the peak of the roof separating the living room from the kitchen. In the summertime the ceiling is connected to the wall, but in the winter there is a half inch gap between the wall and the ceiling. Truss design at fault?
*
B,
I don't know which manual has the specs you require. But I do have experience building trusses on site. The finished trusses spanned 32', with a roof slope of 6:12 and a ceiling slope of 3:12 or 4:12. We just built them against a temporery stud wall so we could nail gussets from both sides. The 1/2" plywood gussets were nailed in a specific pattern. The top chords were 2"x6". All other chords and web pieces were 2"x4". Everything was specified by an engineer at a cost of <$200.00. It was a fun challenge which I would do again. The warnings alluding to liability and catastrophic failure shouldn't be ignored. But, I don't see how the metal toothed connectors pressed into place by the operator at the manufacturing plant are any more reliable than plywood gussets carefully installed by a skillful carpenter. In fact I have seen many loose metal toothed connectors in manufactured trusses. If you can be sure of the engineering, build them and enjoy it. Steve
*
It really isn't the fault of the truss, but it is common. Check out http://www.trussnet.com/ for more info about this.
*
I wanna make some trusses using plywood (1/4 inch) for gussetting but fear that building permit will hinge upon an engineering review stamp. I feel my design/sizing of members is adequate, but can't independently substantiate the gussets. Is this subject covered in any of the manuals?
Thanx.
*As an old truss guy, I've never recommended that someone build their own trusses. There are just too many issues to try to deal with, that it's not worth it. What kind of lumber are you going to use ? What size ? What grade ? (Lumber for trusses is different than what you get at the lumberyard, at least in the midwest)Who decided on the size of the plywood gussets ? Who said 1/4" plywood is adequate ? (I've never seen it used)How many nails do you need to use in each member in each joint ? What size nails ? I've been flamed before on similar boards suggesting that People shouldn't build their own trusses. I don't know why, but it seems to be a pretty emotional subject. Best of luck with your project.
*B,The only thing worse than a professionally designed truss is one that isn't. In VA, we can design and build trusses for ag buildings and the like, but we dare not do this for a residence. Your best bet is to have a truss company do your work, or go with joists and rafters ( to code). This will ensure a good and sound roof system. I have had my share of problems with trusses, but never a catastrophic falure.
*Ron- I'm a P.E. and your advice is right on the money. I couldn't have said it better myself.Fred
*Thanx to everyone for the input, BUT, I do believe I asked ONE question which I will repeat..."Is the subject of gusseting covered in any manuals?" Sorry if I sound arrogant.Brian
*You might be able to find something in a wood design manual. Guessing it would be in a chapter on connections. But, if you feel your time is worth anything, why not leave it to the truss guys to do it. By the time you reasearch it, design it, find an engineer to check it, then get the building inspector to approve it, I think it will be money and time well spent going to the truss manufacturer first. Ron, I dont know why anyone would give you trouble....your advice is good advice.Dave
*To "B". Yes, it is covered in a manual.......sort of If you can find the latest edition of NDS, you can wade through all that stuff to figure out nail values. But it will probably take a P.E. to intrepet it for you. You'll also need a copy of TPI95, and some more time with an engineer to sort out the lumber design issues. You'll spend more time trying to sort out all this info than it could possibly be worth. My point in all this is that there is no simple "manual" for truss design. It's incredibly complicated. But let's assume for a minute that I'm full of it, and you find a way to get by the building inspector. You build your trusses, and do a pretty decent job. But maybe you make one mistake. Trusses are like a chain, in that they are only as strong as their weakest link. Maybe you have a big snow, and your roof collapses. How much money would you have saved then ?Or what if your roof only sags, and causes drywall cracking, etc. Again, how much money will you have saved in the long run ?
*
Maybe it depends on what type of building you
want to make trusses for. I wanted to do all the
work myself on a workshop I built. So I built the
trusses also. I went to a place in town that makes trusses and made them with the materials they use. They sold me the materials ( #1 yellow
pine,1/4" plywood for gussets and a powdered glue
that you mix with water. Built 21 of them with
my dad. Lot of fun. Gave radial arm saw a work-out. Downside was only saved about 200 dollars.
Simple way to build Trusses.
I have built a dozen or so buildings using engineer trusses. Last time I build a 30 foot by 60 foot garage I desided to call my truss builder and order one truss. He delivered it and I used it as template to build the rest.
I used the 2x6 material along with 3/4 plywood cut up into appropriate angles and squares to fit the need. I used 3 inch ring shank nails in symmetrical patterns. I nailed them on both sides of each truss.
My trusses were stronger feeling when installing the decking for the roof. No give no bounce.