I’ve got some 3/4 inch clear birch kiln dried,T and G in 3,4, and 5 inch widths to lay in a room that’s 24 feet wide x 24 feet long. As I’m trying to allow for expansion at the edge walls, what sort of expansion in terms of inches can I expect from this width of flooring. I’ll be laying to perpendicular to the floor joists, and in the dry, winter season, in an occupied, heated house in western Mass. Hey, thanks for your help. Dennis
Discussion Forum
Discussion Forum
Up Next
Video Shorts
Featured Story
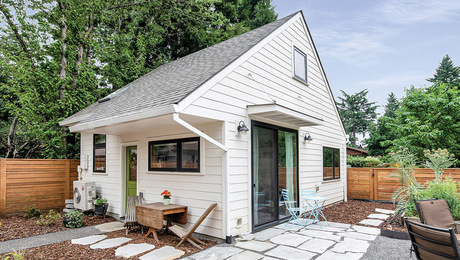
Key proposals for the next edition of the International Residential Code tackle room sizes, stair specs, emergency egress, and deck guards, among other requirements.
Highlights
"I have learned so much thanks to the searchable articles on the FHB website. I can confidently say that I expect to be a life-long subscriber." - M.K.
Fine Homebuilding Magazine
- Home Group
- Antique Trader
- Arts & Crafts Homes
- Bank Note Reporter
- Cabin Life
- Cuisine at Home
- Fine Gardening
- Fine Woodworking
- Green Building Advisor
- Garden Gate
- Horticulture
- Keep Craft Alive
- Log Home Living
- Military Trader/Vehicles
- Numismatic News
- Numismaster
- Old Cars Weekly
- Old House Journal
- Period Homes
- Popular Woodworking
- Script
- ShopNotes
- Sports Collectors Digest
- Threads
- Timber Home Living
- Traditional Building
- Woodsmith
- World Coin News
- Writer's Digest
Replies
I would leave 1/2 inch to 3/4 inch all the way round. I usually cut back the dry wall or plaster close to the floor so as to be sure the base and shoe will cover the gap.
Poetwithahammer,
You need to tell me more information.. that 1/2 to 3/4 inch rule will work maybe.. since you will be using wider boards they will swell and shrink more than a normal 2 1/4 inch wide board will .
(width wise, virtually nothing length wise)
How tight will you be nailing them together? Normal with a flooring nailer? manual or pneumatic?
In the summer when things get really humid is the space air conditioned most of the time? Or do you prefer to open windows for fresh air? I assume it's an old house? what is the subfloor made of? Plywood or carsiding? If it's solid wood what kind of wood and is it laid on the diagonal? Is the basement dry or wet? (summertime)
Finally if you sight down the edge of a strip of wood how close to dead flat straight is it?
Dear Frenchy and BilWil: The house is a ranch built in 1970. I've ripped up the particleboard "upper subfloor" leaving 1/2 in ply. I'll be installing over 15# felt perpendicular to floor joists. In two smaller bedrooms (11x 11 each) I'll be installing parallel to the joists over 1/2 in ply so I'm going to add blocking (2x 10's) 16" o.c. for nailers (this may be a bit overkill) and possibly flat 2x4's screwed between these every 8" and screwed form above for nailering the floor down to since the 1/2 inch ply is minimal for the 2" floor nails.
I'll be using a pneumatic nailer, nailing every 8". The house has no AC in summer but it has a whole house fan which they intend to use properly: exchangeing the air at night when its less humid out. The basement is a bit wet with some standing water in places in spring or after a rain..... and there's a working sump pump. All of the large floor I'll be putting down over the 24' x 24' room will be over a cement floored 4' crawl space which is dry year round. The flooring is clear birch, kiln dried and I checked it with my moisture meter and it's close in moisture content to the subfloor. the flooring seems quite straight when sighted down. the flooring is stored in the living space and unwrapped out of it's plastic bags for several weeks now. It occurs to me from my furniture making days that if I polyu;rethaned the bottom side of the flooring before putting it down it would not expand as much in that large space but this is alot of extra work and seems like the typical overkill. What are your thoughts and thanks again in advance for your time and thoughts. Dennis Pollock
poetwithahammer.
Wow! All the expansion problems I can imagine! Absolutely worst case scenero.
First you'l have to seal the basement from everything. polyurthane the boards ain't gonna be enough..
Cheap solution would be to spread plastic sheets and staple them to the botton of the joists..(even in the crawl space) then tape all the joints and everyplace a staple went into the wood. That will help in preventing the moisture in your basement from making things worse.. But the basement mositure will still come up .. either through heat ducts or doors or whatever access you have to the basement etc..
When you nail down the boards I would leave them a bit loose to allow for the expansion which will happen during the summer months.. loose as in less than a business card thickness. but more than a sheet of paper..
frenchy, I must say you have some pretty uniquie ideas. I guess that is because you are a unique kinda guy ;)
anyhow, my question is....if a 5 1/2" board expands or shrinks twice as much as board half it's width, but a room would consist of twice as many boards using the smaller board. HOw exactly does the overall shrinkage/expanspansion of the floor remain doubled by using the larger board?
As for your statement: "Tar paper makes a lousy vapour barrier that's why they came up with modern house wraps.."
since when is paper ( or wrap ) on the outside of a house vapour barrier?! Paper breathes so well because of all the open seams. 15 lb felt is NOT the same as 30 and 60 minute paper that is used on the exterior of walls. House wraps are specifically designed to allow vapour to esape - it is NOT a vapour barrier.
As for leaving gaps in the floor during install, that is a comlpete waste of time and effort and is ridiculous! We all know that when you nail the floor down as you hit the nailer it knocks the floor boards together. Other than speed, that is what is so great about using a floor nailer. Keeping the boards tight is what keeps your rows straight. You're telling him he's got to maintain a very slight gap on every board?! My partner has layed hundreds of floors, and he would say that to attempt to leave gaps is ridiculous. That is what the perimiter expansion gap is for. It's not going to cup if it is installed properly. Expansion gaps between each board is not part of the equation.
View Image View Image
Edited 2/21/2008 7:19 am by alrightythen
alrightythen,
If you've nailed floors together I'm sure you know the trick of using wide thin putty knives to maintain spacing. You slide them in between the boards just prior to banging them together. Slide them out and the gap is almost invisable. But very useful to preventing buckling when using wide boards.
Why does one wide board tend to buckel more than 2 & 1/2 narrow boards? because even though the two & 1/2 narrow boards are tight together there is a tiny bit of give at each joint. Look at a floor in the dead of winter during the heating season for visable proof of what I'm saying. The finish you use may bridge that gap but the gap is there especially during the dry heating season..
Plastic is used indoors as a vapor barrier on interior walls. He is building over a potential swimming pool so you want to keep the moisture from that water away from the wood.. wood is hydrogyscopic.. it will suck up moisture.. Since you don't use tar paper on the inside for a vapor barrier don't use it under the floor as a vapor barrier.. That's why it's stapled to the bottom of the joists..
Techically he should then cover all that plastic with sheetrock to meet fire code but that's a seperate issue. What he should really do is fix the basement so He doesn't get water in it.. But I've explained all that before..
"If you've nailed floors together I'm sure you know the trick of using wide thin putty knives to maintain spacing. You slide them in between the boards just prior to banging them together."
frenchy, why would I concern myself with a trick that is a watse of time?
"Why does one wide board tend to buckel more than 2 & 1/2 narrow boards?"
I didn't ask why a wide board buckles more than a smaller baord. I know that it can. Which is different than, it will. We are talking the floor as a whole. If a board by itself is going to cup it is going to cup. cuppling of boards and buckling of floors are two different issues. the cupping of the board has to do with how moisture affects the board dependant on the grain on the individual board. floors buckle when they swell and have no expansion around the perimiter.
You told him for the gap to be less than a business card, but you are now saying that you use a putty knife to maintain your gaps. I guess you have pretty skinny putty knives, because most are NOT less than a business card.
As I said before, Waste of time.
"Plastic is used indoors as a vapor barrier on interior walls."
I know that. I also know that VB goes on WARM side. you do not put poly underside of your floor joists of a cold damp crawlspace.
what is he going to do when vapour in the floor system condenses on the cold poly and has no where to go?
5/8 t&g is considered as VB and therefor additional VB is not needed. In an extreme case such as discussed here, were an addional VB upgrade may be desired it should be installed on the WARM side. which puts us to either on top of the floor or the underside of the sheathing, but not the underside of floor joists.
"What he should really do is fix the basement so He doesn't get water in it.."
Right on! Good advice.
View Image View Image
Edited 2/21/2008 8:18 am by alrightythen
alrightythen
If you would be so kind as to go to 86920.13 in the advanced search file over on the left side of the breaktime site page you will see where I used just such a thin putty* knife (s) to set the space between my even wider boards..
If You doubt me, look at Carlise floorings ads. You will note 1/3 inch gap between boards on 8 inch wide flooring and a near 1/2 inch wide gap on 12 inch flooring.. (visual estimate only)
If all the accomidation for expansion could be taken at the edges don't you think they Carlise) would?
When the boards swell as they do they can either buckle up or move is such a way as to accomidate their expansion..
If you come over to my house right now you will find that there is about a paper thickness between the edge of one board and the edge of another.. However, you have to get down on your hands and kness to detect it..
During the humid summer those boards are drum tight.. without those slight gaps buckling/cupping or some other disaster would happen..
Wood shrinks and swells with humidity.. you either accomidate it in the beginning or you deal with the resultant disaster..
As for condensation on the plasatic barrier, THAT WOULD BE A GOOD THING.. BECAUSE IT WOULD BE ON THE ALREADY DAMP SIDE OF THE VAPOR BARRIER NOT THE SIDE WHICH WILL CAUSE WOOD TO SWELL.. Sorry for the shouting....
* I doubt they are actual putty knives they are extremely thin and long perhaps they were originally intended to be used as spatula knives for spreading joint compound?
Edited 2/21/2008 10:20 am ET by frenchy
frenchy....you can use your knives or whatever else you want. But using other precautions it simply is not needed.
whatever kind of wood it is that it requires it to have a 1/3 rd to 1/2" gap to put down is not something I would want to have.
Who knows how many thousands of floors have been installed without using a putty knife to space the boards. Just becuase you do it, and carlise has 1/2" gaps on 12" planks for some reason doesn't mean its right. I find it hard to imagine a 24' x 24' floor would expand a foot! what is way more likely is that their planks have shrunk and you presume to believe that that is how they were installed.
View Image View Image
Edited 2/21/2008 10:37 am by alrightythen
alrightythen
The floor won't expand a foot but each board will expand a ceratin amount. Normal flooring is done at 2 1/4 inches wide because they can accodidate most expansion with the tiny bit of space in the joint when they are nailed together.. as you get woider than that expansion becomes a greater and greater issue..
Go back to a Carlise wide planked floor home in the summer and you'll note the boards are nice and tight without any signs of buckling. I'm certain the reason they show floor with wide gaps like that is so some new home owner doesn't look at the required end gaps and come all unglued..
Finally you've expressed your opinion with regard wide flooring.. and that's fine .. You certainly are entittled to your opinion.. however Instead of injecting my opinion I offered a workable solution given all the factors..
A floor can be installed tight and expand as a whole. That is what you seem to not realize. thinking that expansion MUST be made up with each and every single row. If that is the case you WON'T need large expansion joints along the perimeter. Because you are adressing the issue with every board that you place down.
Your way is another way to "skin a cat". But it is not required to do it that what. It is a slower way to do it. If you keep the floor tight, it will stay tight when it expands. As long as there is proper expansion along the perimiter.
You seem dead set against going with standard practices that work. And that is fine it's your house.
As for wide planks, they are fine. But not if I'm going to be looking at the 1/2" gaps that you are talking about. 24' feet of 12" boards with 1/2" gap per board is a foot of expansion you are talking about. sounds kind of ridiculous doesn't. well if a foot over the whole floor doesn't makes sense, claiming 1/2" spaces needed between board doesn't make sense either. As I said before, those gaps you were looking at were due to shrinkage more than anything. And true they will expand again in the summer. View Image View Image
alrightythen.
Let's keep this simple.. if one 5.5 inch wide plank expands a maximum of 1/8th an inch over 12 feet. and we start expanding in the middle that's 26 times 1/8th of an inch or 3.25 inches the outside one must move..
Now I don't have the sheet here where I look up expansion rates of various woods however I'm sure if you need to know such data is availablle on the web someplace. I'm old fashioned, I look things up in books and I don't have access to my library right now..
As for my floor I will do the calculations at the time I put down those 22 inch wide planks. I'm measuring their change in width as we speak Every month I check on how wide or narrow they are and it would shock you.. the amount required for them.
Just so you know it is possible to put down extremely wide boards if you use a floating system. Several years ago In Fine Homebuilding magazine There was a picture of four boards covering the whole floor of a room something like 50inch wide each but you can bet you last dollar somebody didn't bang them in at the edge..
"if one 5.5 inch wide plank expands a maximum of 1/8th an inch over 12 feet. and we start expanding in the middle that's 26 times 1/8th of an inch or 3.25 inches the outside one must move.."
OK at least now you making a little more sense with 1/8th, instead of talking about 1/2" spacing inbetween boards.
there's room to debate and we could go on forever getting nowhere. And yes different woods will expand contract at different levels as well conditions do affect it as you noted some of the extremes in your original post. So lets leave it at that and carry on banging nails into wood and making beautiful homes.
Have a good day :) View Image View Image
Most deck boards have much less than 1/3 - 1/2" of spacing..
.
A-holes. Hey every group has to have one. And I have been elected to be the one. I should make that my tagline.
Alrightythen,Frenchy may not have the best way of describing what he's saying, but he's largely correct.I work with wide-board floors quite a bit, and each board moves a lot from season to season. It's a common problem for old-house owners. This kind of floor might not be something you are interested in dealing with, but in my neck of the woods, I have to deal with them over and over. And they really are very beautiful floors, in my opinion. Clients love them too, but struggle with the gap issue.Attached are two pix, one showing a 15" pine floorboard in it's entire width, and another close up of the 1/4" gap between it and it's neighbor. In the summer these boards are tight together. When I work on wide pine floors I figure on anywhere between 1/8 to 1/4 of an inch of change in width per 12" of plank width. It varies with the swings in humidity for each particular house of course, a is differnt for different species as well.I struggle with laying anything wider than 2 1/4" strip flooring when I have to lay it in the heating season. I've put down several 3-4-5" random-width cherry and maple floors in the winter, laying them tight, and they all exhibit minor buckling at the edges in the summer. It goes away again in the winter, but I wish I had laid them with a little gap in them. I would rather have a little gap in the winter than buckling in the summer.I'm faced with the same situation agin in a few weeks. need to lay 3-4-5 maple. Still trying to decide whether to butt it up tight or space it out a little. In this instance I may lay it tight, because the house has been largely unheated this winter.One thing I have to disagree with frenchy on is the movement along the grain. That is insignificant. Only movement that is significant is across the grainSteve
That is fine. you are talking 1/4" compared to 1/2" gaps mentioned by frenchy. big difference too me. I've only seen a few "really wide" plank floors myself, and I concur there will be gaps. These floors can be very nice indeed lending to the character of a certain style of house.
I'm putting this topic to rest as far as I'm concerned. View Image View Image
One last post...I bought a 300 dollar moisture meter specifically to help me make decisions about floor laying. I had read--and the guys at the local flooring mill told me--that it doesn't matter what's going on seasonally in the house, if the flooring is at 7% when you put it down, lay it tight and you'll be fine.Well, the last 3-4-5 cherry floor I laid last winter, I did just that. This summer it looked like a pond in a choppy breeze.So now I'm of course I'm in nearly the same situation, and scratching my head about what to do. This is one of those topics that just never seems to die because there never seems to be a right answer.Best to you,Steve
alrightythen,
Please go back and carefully reread what I said about those gaps.. They were visual estimates only! If you look at Carlise's ads you will see what I mean.
frenchy I'm actually done with this thread. You can be right. I no longer care how big the gaps are. I concede there is something to what you say, however there are other methods that you shouldn't have to use a putty knife to lay a floor, along with other scenarios which you simply don't need to.
good day View Image View Image
All I know is I have never run into hardwood flooring spacers at my flooring supplier either.Wallyo
Edited 3/4/2008 1:11 am ET by wallyo
lol View Image View Image
mmoogie,
Oh, we don't disagree one little bit.. I'm sure you've read something wrong (or I wrote it wrong <grin> ) because I know wood doesn't change length wise.
That's why I wrote that width needed to be dealt with but not length..
you can get condensation on both sides if the conditions are right. when I get in my old car I use for booting around I have scrape the windows on the outside and I also have to scrape the inside.
bottom line, inspector told me no poly underside joists. Not that everything they say makes sense. but I'll go along with that. View Image View Image
I`ve lived in hundred year old houses with hardwood floors and rivers in the basement that never had the problems described in this thread. I'm not a big fan of wide boards due to stability problems (they tend to crack in the prairie extremes), but I think if you follow you're local code and put the appropriate underlay between the boards and your subfloor you should be fine. Leave a half inch around the parimeter and cover with nice baseboards. If you can, leave this job to mid to early spring. As far as sealing the basement is concerned, humidity in a house will permeate the house no matter what you do. Your house isn`t that old. Try to fix your water problems.
I think you mean to repspond to the original poster.
But yes I agree, some of the stuff described is incredible. View Image View Image
The 1/2 inch is pretty thin for a sub floor are you sure you got a good measurement and it is not 5/8 or19/32?I am a little confused is the 15# felt parallel and perpendicular to the joists or the H W flooring. In either case I would install the HW floor perpendicular to the joists only.The NWFA recommends 5 inch and wider to acclimate for four weeks.It sounds like you are close to that.I would worry about the water in the basement that occurs in the spring. Is the problem one that could be solved with proper gutters if none are present or draining the gutter run off further from the house or is it ground water coming up through the slab? Or if gutters are present do they leak?A 1/2 expansion joint should be fine. The point of acclimating flooring is to bring it to equilibrium to the conditions present in the house. If properly acclimated the HW floor will expand and contract close to the same rate as the house. Most Problems arise when HW is not acclimated.I would not waste my time nailing poly to the joist bottom that is what the 15# felt is for, and that is why the NWFA recommends felt over rosin paper. As to poly on the slab in the crawl space it sounds like that is not as much an issue since the space remains dry and you may have poly under the slab already, that 24x24 area sounds like an addition?Again I would skip the polyurethane on the under side of the HW that is why you have the 15# felt.The HW should be at 12 -14% moisture with no more then a 4% between it and the subfloor. It sound like you are close to nailing except for the subfloor issue.WallyoEdited 2/17/2008 6:12 pm ET by wallyoEdited 2/17/2008 6:14 pm ET by wallyo
Edited 2/17/2008 9:30 pm ET by wallyo
these are REALLY helpful . thanks.... by the way does a house expand widthwise in the summer? thanks Dennis Pollock What a great web site.
poetwithahammer,
Since most subfloor nowdays is plywood and plywood has layers of alternate directions to minimise the effects of swelling the short answer is no..
IN my case though the answer is yes. (solid wood subflooring)
Wallyo,
The purpose the plastic will serve is the vapor barrier between the subfloor and the swimming pool in basement.. That is why I recommended that he tape it carefully..
Tar paper makes a lousy vapour barrier Every seam is a potential leak/weapage point.. if it was good there wouldn't be the need for housewraps..
Frenchy Frency Frenchy If 15# felt is so terrible why is it recommended by the National wood Flooring Association as their choice.15# felt vs house wrap on the side of a house is a total different application then a floor. The reason house wrap out weighs out felt on the side of a house is a house side may get gale driven rain or moisture at 40-50-60-70-80 mph a floor will not get that.The OP says:
"the basement is a bit wet with some standing water in places in spring or after a rain"He does not say it fills up like a swimming pool just some standing water in places. A dehumidifier may help with that also if needed.That is why I encouraged him to get gutters, or have them checked for leaks, or extend the down spouts away from the house. It has been my experience that a large amount of water in basement is caused by improper gutters. Like everything else on a house gutters need to be maintained. Get rid of the water in the basement a lot of problems solved. My sisters basement leaks after a good rain if they would put gutters up on that side of the house she would have no problem but her husband refuses.If he staples poly up to the rafters it will not do that much good if the furnace is in the basement it is going to cycle up the moisture, also there is no way he is going to seal everything the stair well to the basement will bring up moisture. Also it could leave no out for the moisture and harbor a breathing ground for mold and fungus. I do believe in just about every code written leaving a poly vapor barrier exposed is a no no it must be covered wioth a suitable material ie. dry wall, due to fire concerns. In fact the only place I can think of where it is allowed exposed is a dirt floor crawl space.You say "Every seam is a potential leak/weapage point" referring to the felt, that is why you overlap it as on a roof by 2-3 inches. Have you ever torn up a wood floor that has had tar paper under it for several years the seams are pretty well adhered to each other by the pressure of the flooring.Again on leaving a gap that is why you Let the HW acclimate properly so you have no need to leave a gap.Again I would worry more about the 1/2 subfloor and not laying the HW perpendicular to the joists. Then any other thing on this install.Wallyo
Wallyo,
Well go ask them if they recommend tar paper as a sealant over a swimming pool.
As for sealing, if tar paper was so good they would use it indoors as a vapor barrier instead of plastic.
OK It's not a full time swimming pool but during those times when water enters and stands around how would you deal with that amount of moisture? Take the flooring up and store it someplace drier?
I do agree that this issue should be dealt with and if it were me I would deal with this issue before I put the flooring down.. But that wasn't among the questions or choices offered by the OP.
Maybe by listing the steps needed to put the flooring down and possible ramifications he will reconsider and wait and deal with the moisture issue first .
Maybe not, he may be getting pressure from She-who-must-be-obeyed or just his own preferance.. or he may not have the funds needed to deal with the issue. All of that is conjecture.. I simply gave him my best advice on how to deal with this issue given the circumstances he listed..
(ps I'm a rosin paper guy not a tar paper)..
FrenchyYou go from something that is standard practice (15# felt has been used for a hundred year as an underlayment) and bring it to an extreme, there is no reason to use 15# felt over a swimming pool. The NWFA does not give swimming pool advice. If the basement did not get water I would not object to the OP using rosin paper. By the way most hardwood suppliers here stock only 15# felt and not rosin paper they do it as a convenience, they hardly make money on it.Once again poly on the underside of the joists is a danger, fire, mold and fungus to name a few. I have discussed some simple ways to deal with the water, a simple dehumidifier in the basement may be of help. Again it is some standing water in some places sometimes. He says after a rain which causes me to thing it is run off from the roof. Just because he didn't ask the question originally does not mean it cannot be discussed. It is like getting new tires and being told you need a break job. The two rooms with the basement are only 11x11, expansion contraction is a small issue even with the water.Wallyo
Wallyo.
The OP stated that there was often standing water in the basement.. During those time moisture will come up thru the floor and cause problems..
The best way to secure it is to put a good vapor barrier between the basement and the flooring..
Walls normally have plastic vapor barrier to keep moisture from being forced outside and ruining the insulation..
That is exactly what I recommend. Mold won't want to attach itself to the plastic.. there is nothing for the mold to eat on plastic unlike on sheet rock where mold will make a nice meal of the paper..
The best solution would be to figure out how to dry out the basement permanently then more ordinary techinques can be used.
However you and I will always disagree about tarpaper or rosin paper.. I insist on rosin parer while you are equally adminent about tarpaper..
Frenchy you are correct that the mold will not grow on the plastic. But if the moistue is trapped in the basement because of a plastic barrier on the ceiling and the moisture has no place to go mold can occur in other areas of the basement; wooden posts, cinder block walls,
wooden shelving etc. you get the idea.Wallyo
Wallyo,
I doubt giving it a place to grow on the joists and subflooring will satisfy it's appitite. which is all that will be protected by the plastic. To be completely legal he should cover the plastic with sheetrock. but that would give the mold an additional place to grow.
The correct solution to the problem would be to correct the basement so that is doen't get wet anymore but that is a whole other post..
I suppose you're pretty confused by now! There might be some problems there with the wet basement. I don't know that it's possible to settle for laying a nice hardwood floor and letting the wetness of the basement dictate how you'll lay the floor.Common sense will tell you to lay the floor tight. I can't imagine laying a floor with on purpose cracks in it and then stepping back and saying "Look mom, all the nice cracks. That's just what I was looking for."Lay the floor tight and if the basement area is too damp for too long the HO must utilize a dehumidifier in that damp area. That will also keep the basement area as a more useful place. Wallyo gave you good advise and told you to acclimate your flooring. That's what is important. If the material is at the same MC as the surrounding material it won't move all that much. According to my government handbook on wood your area's average inside home moisture content is 8%. You don't really have to know the percentage but you have to have your material the same as the furniture and the rest of the content of the house.
mesic,
lay the 5 1/2 inch wide boards tight now and in the summer with humidity and the inevitable moisture escaping past whatever barrier he uses and when the wood swells where will it go to? or do you prefer cupping to tiny cracks between boards?
The answer to that is that the floor is upstairs and the floor will take on the MC of that area. The tar paper will be the barrier that will keep the floor thinking it is in the drier area. There is no reason to lay the floor loose. The solution is to lay a floor that has the same moisture content as the rest of the living space. There will be problems with more than the floor if the humidity gets too high and that should be up to the HO to monitor for comfort if not for the furniture. Aim for 40% or less for the living area and 45 for the basement. Good for the floor, good for the furniture and good for the house. And Frenchy, a room full of 5 1/2" wood doesn't shrink or expand anymore than a room full of 2 1/4" wood.
Mesic,
The differance between 2 1/4 inch wood and 5 1/2 inch wood is that there is a tiny amount of yield at every joint between wood so 2 1/4 inch will have twice as much room for movement as 5 1/2 inch will. Well slightly more than twice..
Tar paper makes a lousy vapour barrier that's why they came up with modern house wraps.. the reason for the plastic is to act as a vapor barrier between the floor and the swimming pool below. You do realize that he is installing this over what basically amounts to a shallow swimming pool don't you? Standing water in the basement is a swimming pool,, (OK splashing pool<grin>)
To accomidate all that moisture is why I suggested the tiny gap.. Please note that I said the thickness of a piece of paper not even as thick as a business card.. few eyes will be able to detect that if it's even all across the room..
In addition he's installing it now during the dry season and you don't want him to make any accomidation for the inevitable swelling that will happen during the summer Note* he doesn't intend to aircondition the space which would keep humidity down to near winter levels. So there is going to be a need for large wood movement..
Poet, are you still there? :) C'mon, wake up, the fuedin's a done with.
If you have a 1/2" subfloor where you are laying the floor perpendicular , you will be O.K., if you find you have 5/8" sub floor, all the better.
Assuming 1/2": where you are laying the floor parallel to joists I would add a layer of 1/2" throughout those rooms ( 2 rooms 11' x 11' ea. IRCC ), this will give you needed structure and it will be alot easier than doing all that blocking from underneath or then trying to hit the blocks when nailing the floor.
If adding the 1/2" throughout all the rooms will make for smoother floor transitions then by all means, do so, but at a min. add it in the parallel installation areas.
No need for anything more than 15# felt over the "wet" basement or the "dry" basement areas.
No poly!!
As already said , acclimate, acclimate, acclimate!! that is the key to success.
I suggest a manual nailer using the ribbed style "cut nail" (sorry, brain cramp on the correct name) vs. the staples. pneumatic nailers are O.K. but stick with the "cut nail" style nail.
Geoff
P.S. check to make sure your existing subfloor is soundly fastened, resecure as needed, but don't go overboard either. :)
Thanks Goeffrey.....
Hey, that sounds good. I put 3/4 in CDX up under the floor and did blocking 16 in o.c. and it's going well.... good article from FHB archives was useful.... so it's going well and thanks so much, Dennis Pollock
Here is the FHB Article:
We live in a 100 yr. old house, I don't have a clue when the "new" floor was installed in the bedroom, but it was tight against the baseboards. I removed the flooring - and the baseboards. Discovered the entire exterior wall was bowed. 1-1/2 inch at the center of a 14-ft wall. Actually, I had no idea it would move that much, but that probably was the weakest side of the room. Got really creative with long, tapered strips of the new flooring too :-)
Well, we put some flooring down in two of the bedrooms, I put 30# felt with 6" overlaps on the subfloor(the basement has a moisture problem which I'm working on) and then shot down the 3,4,5" random clear birch.... which looks great. We left about 1 and 1/8 inch expansion room under the baseboard and sheetrock. Funny how 2 inch oak doesn't supposedly expand much propably because of all the nails where wider boards will expand more width wise. Any thoughts on why this might be? Thanks
Dennis Pollock
Well, my problem was a fireplace on the opposite wall and the flooring could only expand in one direction. Consider each board expanding 1/32", then count all the boards across the floor, that's a lot of 32nds. I'm sure the darned stuff is alive :-).
Ray,It depends on the species, but what sometimes happens is you don't get all the movement telegraphing all the way across the floor, rather each board either cups a little bit when they expand, or with softer species like pine, the fibers on the edge of each floorboard actually crush a little bit after cycling through the seasonal expansions a few times, eventually leading to gaps in the dry season.Steve
Edited 3/2/2008 1:44 pm by mmoogie
Since you're installing planks, tongue and grove, I believe the expansion contraction is at each plank's edge and thus "spread" across the number of planks in the floor.
IOW, say that 24 feet of your birch wood will expand, in total, 2". Say there are 100 boards across the room. Each board will thus expand/contract 2/100" (a little more than 1/64" assuming that 2" comes anywhere close to reality) - and each board is held in place along one edge by the flooring nails.
Thus, if I'm right, the edges don't need any "special" treatment for expansion contraction....
Keep in mind ... I was wrong....
Once <G>
View Image
May your whole life become a response to the truth that you've always been loved, you are loved and you always will be loved" Rob Bell, Nooma, "Bullhorn"
"We Live" http://www.youtube.com/watch?v=7kuBgh0VCqI&mode=related&search
And Annie Ross's "Twisted" http://www.youtube.com/watch?v=8lqivrCIRGo&mode=related&search=