I just got a huge compressor for my home shop (boat building and woodwooking). It’s 7.5HP, 2 stage, 80 gal vert tank, 175psi, 25 cfm @ 90, yadda, yadda. I’m using it primarily for sanding and grinding. As I’m setting it up, are there any things you all can think of that I may not have to make my life easier?
Discussion Forum
Discussion Forum
Up Next
Video Shorts
Featured Story
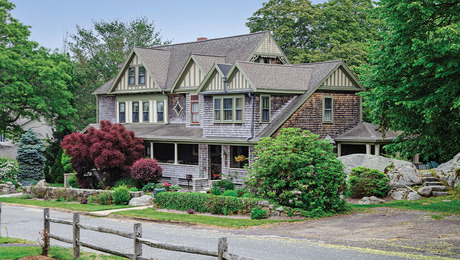
From plumbing failures to environmental near disasters, OHJ staffers dish on our worst and best moments.
Featured Video
SawStop's Portable Tablesaw is Bigger and Better Than BeforeHighlights
"I have learned so much thanks to the searchable articles on the FHB website. I can confidently say that I expect to be a life-long subscriber." - M.K.
Replies
-filter/regulator/lubricator combo unit at compressor exit - takes out water, junk, etc and lets you add lubrication if you need it. You can leave out the lubricator if you are just using it to spray paint. Make sure to check the filter often to remove water in the bowl.
- pick one size of quick connect fittings and get lots of them for all your air tools. put male fittings on the tools, female on the hose ends. You can buy an accessory kit for the compressor which will have enough fittings to get you started, as well as some other useful things like a blow gun and tire chuck.
Hope this helps. Rich.
Automatic water drain, I have been an expert witness on 3 tanks bursting all caused by failure to drain.
Edited 6/7/2002 11:05:32 PM ET by JANATION
"automatic water drain" Where are these available?
You can get them at http://www.mcmaster.com/ and I'm sure other places. They are called "condensate drain valves". There are several types, some need electricity and cycle on regular intervals, while others use a float which opens a valve when water in them reaches a certain point.
Hope this helps. Rich.
I would manifold air lines overhead so you won't be tripping over air lines. I used 3/4 inch air hose with hanging lines ending just slightly over your head.
and if you run steel pipe manifold, be sure to slope all runs away from the compressor, take off all tees UP and then down (so water won't run toward your tools, and put a drain at the end (ball valve) to let the water out every day of compressor use.
You may want to isolate the compressor from the hard piping with a short section of hose. This will prevent the vibration from the compressor going to your pipes . Chip
too noisy, put it in a closet, with soundproofing,do you really want to listen to that thing? Then again, you're probably hard of hearing anyway.
no turn left unstoned
Oil drain fitting is probably 1/8 NPT - make up a short fitting (nipple, elbow, plug) to make oil changes less messy. Ditto for condensation drain at bottom of tank. Ditto on previous good suggestion to use short flex hose from compressor to your main air pipe run - however be sure to use high quality, properly rated hose here.
The Tauton book "Setting up Shop" has a pretty good section on setting up a compressed air system.