*
Bill, try checking with your excavator and/or local trucking companies. We once got several loads of busted up shale for almost nothing. We used it for driveway base in a similar situation. They were tearing it out and needed to lose it somewhere. You might get lucky if you check around.
Discussion Forum
Discussion Forum
Up Next
Video Shorts
Featured Story
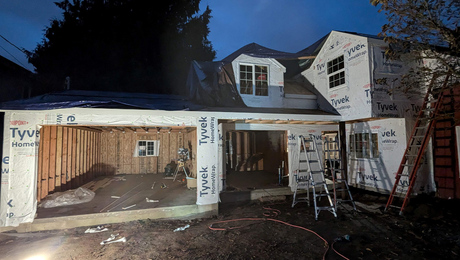
The FHB Podcast crew takes a closer look at an interesting roof.
Featured Video
How to Install Cable Rail Around Wood-Post CornersHighlights
"I have learned so much thanks to the searchable articles on the FHB website. I can confidently say that I expect to be a life-long subscriber." - M.K.
Replies
*
Heres the deal: Lot slopes front to back. 8' fill at front. Mostly clay. Side load. If I allowed for standard entry into 3rd (rear) stall I would be looking at a humongous amount of fill. As the drive entry is currently drawn I am looking as slightly less than humongous amount of fill.
Here's the question - any way to use site fill with an ingenious use of sleeper footings under the driveway and possibly 6" pour? Any other ideas other than trucking in the perfect base?
By the way, I am also looking at loads of fill in the garage, so the same question applies there.
Thanks in advance for the perfect solution that will save me $6 thousand dollars. I might even send you a Hardees sour dough breakfast biscuit.
Be good,
Bill
*Can you send a picture? Maybe if you moved that 8 foot high pile of fill you could get into your driveway. What does side load mean? Is your bank of garage openings perpendicular to the course of the driveway? How wide is the apron area in front of these stalls? Are you restricted by an adjoining property line as to the width of the apron. What part of the country are you in? It makes a difference in how you must (should) put in the base. What do you plan for a watershed area (drainage) for the expanse of hard surface? How many loads of fill in the garage? Why? Did you build on a sink hole? For consultation I get a whole biscuit, up front, a half biscuit down if I start the job and another biscuit and a half upon completion.
*Ralph,Thx for the response. The fill makes the lot roughly flat for the first fifty feet, then it drops off rather rapidly, say 3 feet in ten.Sorry, local terminology. Side load means the entry into the garage is from the side rather than the front. Entry to the garage will be on the south side. The east side faces the street.The apron area will be roughly 30' remember, that 30' runs parallel to the side of the next house to the south. That house is roughly 45' away, it is naturally built 10 feet from the lot line (minimum setback). At the rear of the driveway I'm describing(west) it will be roughly 10' higher than the walkout basement which, after the installation of the side entrance driveway will be about 25 feet directly north of the rear corner of the neighbor's house (have I lost you yet?). We could be looking at a drop of 10' in an area of about 15' if I put in the standard turn which would allow an easy entrance into the third bay. As it will be, the third stall will only be accessable by motorcycle, or Korean auto, and one with a good turning radius at that..The garage is built straddling the rather substantial drop where it goes from 8' fill to none (east to west). The lot allows a nice walkout to a wooded area and a substantial creek, so it may be worth the work.I pay 2/3 biscuit at rough in, the other at final, but I'll throw in some coffee throughout to sweeten the deal.Thanks again,Bill
*Bill, try checking with your excavator and/or local trucking companies. We once got several loads of busted up shale for almost nothing. We used it for driveway base in a similar situation. They were tearing it out and needed to lose it somewhere. You might get lucky if you check around.
*Coffee time, Bill,Two possible solutions come to mind.1. Start filling, use a stepped retaining wall with tiebacks. You can use more of the available area for the apron if you don't have to deal with a natural angle of repose. Then put in a barrier (railing, maybe something fancy) to keep from falling off. Fill for you may be as bearmon suggested.2. Hunt around for precast concrete decking. It's piled up in a least one salvage yard here in Jacksonville. Pour appropriate footers and build supporting beams or walls. Set the decking and pour a cap if you want. Storage now available underneath.Still trying to picture that garage straddling the hillside, four walls, a roof and no floor. The precast deck material would work for that too. More storage underneath.Comments? Ralph
*Bill,Even "perfect" fill can be free if someone has to get rid of it. Look into the different modular retaining walls. (precast blocks with fiberglass pins) Tiebacks are unnecessary with many modular earth walls. Some use geotextile fabric in lieu of tiebacks if wall height requires it. If you're pouring a garage wall you could extend it as a retaining wall. Footing redesign and wall reinforcement would be different though. 10 foot wall shouldn't be too difficult for regular foundation contractor to adapt to.Eric
*Thanks guys,Here's what we did:Lowered the garage floor a foot.Sloped the drive, gained us another foot.Changed the radius of the corner in the drive based on my wife's van cranked all the way. Because of the above we are now down to a drastically more manageable slope. We are using molding sand (remnants from an iron foundry) bounded by the clay soil as fill.We will dig trenches roughly 6" by 6" w/rebar spaced every 4 feet under the drive to be poured at the same time as the drive.I will post in two years to tell you how it worked. hopefully I won't know before then.Thanks again,Bill