*
I NEED TO INSTALL A GREEN MARBLE AND TILE BORDER TO THE FACE OF A GAS FIREPLACE AND I WOULD LIKE TO KNOW IF THERE IS A HIGH-HEAT TYPE OF EPOXY THAT IS USED FOR THIS TYPE OF INSTALLATION. I HAVE USED THE TRADITIONAL EPOXY (MIX 2 LIQUIDS & ADD THE WHITE POWDER) FOR BATHROOM MARBLE JOBS, BUT THIS FIREPLACE JOB HAS GOT ME STUMPED. MY SUPPLIER SAYS THE TRADITIONAL STUFF WILL WORK, BUT I’M NOT SURE. IF ANYBODY HAS SOME IDEAS (OR SOME ADVICE) I WOULD BE MUCH ABLIGED. THANKS! – RICO
Discussion Forum
Discussion Forum
Up Next
Video Shorts
Featured Story
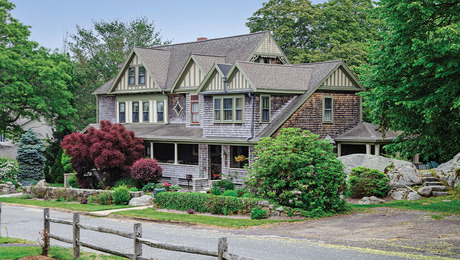
From plumbing failures to environmental near disasters, OHJ staffers dish on our worst and best moments.
Highlights
"I have learned so much thanks to the searchable articles on the FHB website. I can confidently say that I expect to be a life-long subscriber." - M.K.
Replies
*
Test the proposed epoxy mix on some marble scraps by putting it near a fireplace, at least as close as you are going to install it. If nasty horrible fumes & smoke result, try something else. A call to the manufacturer of the epoxy would probably be in order. Also try the manufacturer of the fireplace...I'm sure they see similar situations occasionally.
*They make a high temperature silicone for automotive work. Red in color. Might consider that. There might also be some kind of stove cement that might work. I'm just guessing, you'll need to do further research.Also consider having slabs of marble cut into three pieces, so that they form a column on either side and a header or beam across the top. Drill pin connections between the column and beam and insert a steel pin so that even if the adhesive fails, the beam won't fall. If you are just using a marble tile rather than the custom cut 1" thick stuff, this obviously won't work.
*I'm wondering to what extent recrystallization of the stone will take place due to temp. Yes, yes; I know this is consequent to temp and pressure, but would you be agreeable to changes in the color of the stone?
*
I installed green marble in my surround and about 1/2 way into the firebox. I used an epoxy mastic (that I picked up at a local tile supply store) and green colored grouting. The mastic wasn't specially designed for this "hot" application. The project turned out great with no heat related issues whatsoever. I've used the fireplace alot with no problem.
One warning. Make sure you give the epoxy alot of time to set up before moving any supports. I removed one support too soon so that I could clean up and had some overnight slipage. This was very dificult to correct without destroying much of the work.
Good luck!
*I've always used liquid nails and never had a problem.
*Don't use any organic adhesive!Thinset is the right way to adhere the marble to the fireplace. Mix it a bit stiff so that it doesn't run. Make sure that it is evenly applied - especially around the edges of the hearth piece. The marble requires sturdy support from below - or it may crack when you step on it. You can apply it rather thick so that the marble seats well - try and keep it under 1/2" thick.Make certain to fill in gaps and voids between the marble and the firebox with the thinset. You may have this issue if you are installing returns within the firebox.Make certain that you let it dry adequately (at least 12 hours) before using, touching, or stepping on. This is a "permanent" solution - removal means breaking the marble off.This is the way my fireplace was done. The marble was applied to an existing brick (not as pretty) fireplace.Thinset does not burn, smoke, etc. and it is readily available in the flooring department of your home improvement store.
*
Thinset will NOT stick to metal for very long. Will not, will not, will not.
*Often times our installers overlap the metal with cement board fastened with screws etc. Tile or marble goes on a substrate that thinset will definitely adhere to. We trim out the inside edge with extruded aluminum trim (tile edging or Al picture frame ordered with reverse miters).
*
I've done several identical applications. The oldest has been up for 12 years - still looks great!
My supplier has always reccomended a special high temp adhesive made by GE. Could not be any easier to use, does not bleed though the marble, and after 12 years of almost continous use during the Connecticut winters, still holding on strong.
*Chris T. et al. : The problem with thin set is that it is water based. Green marble absorbs water and it slowly falls apart, unlike most other marbles, thus in applications using green marble another method must be used. I still think that the epoxy based adheasive is the best answer.
*
Nine years ago, I tiled the inside of my pre-fab fireplace with 3X3 AO quarry pavers. I lathed the metal and then muded to a thickness of 1/2" with light wall mix. I set the pavers with flexible thinset mortar and used sanded grout. Still strong, no cracks, looks great. The area that surrounds the firebox was also muded. The face was done with stone, thinset over DUROCK. I've noticed that black soot doesn't stick to the tile very long. Once the fireplace heats up, the soot burns off and the tile and grout look like new.
*The answer to your querry is scattered in little points in most of the answers given.The metal expanded mesh is a must, use metal self-drilling screws with washers and make damn sure that it is secure. Every 6 to 8 inches max.The use of a good quality thinset is the best with additive to ensure that extra adhesion.Remember the weight of the marble.Install a good scratch coat, let it really dry and then apply final coat.Place your marble sections carefully, plumb & square.Install pressure bracing to hold the marble tight against the fireplace, leave for a day.Let dry a couple of days, start a small fire and warm up the firebox on the first day.Then you can use and enjoy your fireplace with the new marble surround.As with most projects, patience should be followed with more patience.
*
Gabe (and all you other guys who took time to help me out): Thanks very much for your advice!
OK, so let me get this straight. I should NOT use epoxy or adhesive, but instead I should attach metal expanded mesh and then use thinset (with additive)to attach the marble & tile.
That sounds like the best alternative yet, but I have always been told that you need to use epoxy to set green marble, because green marble tends to "curl up" after a while - and epoxy prevents this. Have you had any experience with this.
Also, can you recommend a "good quality thinset and additive" for this application?
Thanks!
*
I NEED TO INSTALL A GREEN MARBLE AND TILE BORDER TO THE FACE OF A GAS FIREPLACE AND I WOULD LIKE TO KNOW IF THERE IS A HIGH-HEAT TYPE OF EPOXY THAT IS USED FOR THIS TYPE OF INSTALLATION. I HAVE USED THE TRADITIONAL EPOXY (MIX 2 LIQUIDS & ADD THE WHITE POWDER) FOR BATHROOM MARBLE JOBS, BUT THIS FIREPLACE JOB HAS GOT ME STUMPED. MY SUPPLIER SAYS THE TRADITIONAL STUFF WILL WORK, BUT I'M NOT SURE. IF ANYBODY HAS SOME IDEAS (OR SOME ADVICE) I WOULD BE MUCH ABLIGED. THANKS! - RICO
*
Rico, the warning comes from the propensity of certain types of green marble to warp after installation. Moisture is the cause of the warpage and Hulian Green is notorious for it. This warning applies to floor installations especially over a concrete slab. Concrete slabs contain a certain amount of moisrure that will vary throughout the year with changes in temp and humidity. I would suspect that on a vertical interior wall installation, where temperature and humidity remain somewhat constant, your chances for warping would be greatly reduced. Since your application will be the face of a gas fireplace, you may want to test the stone's resistance to dry heat. Sounds crazy, but I would heat several randomly selected 12X12 squares of your particular green marble (Vermont Green?) in the oven at say, 300 degrees for a couple of hours. Let the pieces cool, and check with a square and straightedge for warpage. If you note any, use epoxy. No warpage, use thinset.