Insulating staple-up RFH with plates
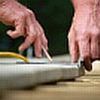
Have a friend who wants to add Radiant Floor Heat (RFH) with floor over crawl space, joists on 16″ centers, has exterior door threshhold hieght to maintain.
Rest of house is heated with new high temp boiler and cast iron radiators. We discussed a valve that will mix return flow with out-going to give proper temp to water in tubes…that part and tubing layout will be handled by local contractor.
We discussed aluminum plates, and he understands they are a good way to go for either staple down or staple up schemes, wants to DIY staple up plate/pex, and then insulate the joist spaces.
Read somewhere, I think here, that if you use plates and staple up, you should insulate right up to the tubing…no air space…because you don’t need to heat the AIR in the space, that the plates serve to transfer BTUs directly to subfloor and on up. As opposed to the somewhat dated (IMHO) method of just hanging the tubing in the joist space, insulating while providing air space, and running 180 degree water through there, counting mostly on the air heating the subfloor>.
In his case, I’m recommending he #1 put in a 6mil vapor barrier on the dirt (not one there yet), and #2 after installing plates and tubing, pressure fit 2″ rigid foam between the joists tight against the tubing-plate sandwich.
Am I giving the correct advice IYO? Or is this total malarkey?
Replies
I prefer rigid foil-faced polyisocyanate insulation. Rip the sheets into required widths on a table saw and friction-fit them into the upper parts of the joist bays.
When using TJIs I tuck them up against the upper flange. If regular 2x joist, tuck them against the bottoms of the staples. You can do the same if using plates. A 1.5" space between the subfloor and the insulation is the max you want.
The foil face stays clean and does a nice job as a radiant surface. A good VB as well.
It's easy to friction fit thinner insulation. Getting up to 2" thick (R14.4) makes it tough to get a tight friction fit. In that case they can be ripped narrower than the joist bay then foamed tight with canned foam.
With the HO DIYing the plates and PEX, have hime sign off against future plate noises...expansion/contraction, etc...as well as against plate edges chaffing the PEX causing tubing damage. Not normally a problem, but...just in case.
You're correct in that simply hanging the PEX in the bay and heating the entire depth of the joist bay is not an option. Not a valid one, anyway.
You're correct in that simply hanging the PEX in the bay and heating the entire depth of the joist bay is not an option. Not a valid one, anyway.
In my opinion you are blindly discounting a very viable method of providing RFH. Now if you would say that this method is vastly inferior to plates I would agree in a heartbeat. But to claim this method is not a viable option is flat out incorrect.
It is true that it takes a lot better designer to do it this way. You have to know what you are doing and what the limits are.
Why deny a huge segment of the market the chance to enjoy RFH just because to do it this way is not the most efficient use of energy, etc? There are many jobs where the owner would not be able to enjoy RFH if they couldn't do staple up. I refuse to make that decision for them. Neither should you.
Having said all that... when I get back into the business (just quit 2 weeks ago) I will most likely refuse to do staple up. I will be positioning myself as a high end ONLY contractor. If they can't afford to do it in the best manner possible then they will have to use someone else. It is niche marketing and nothing more.
Would love to hear your thoughts back.
WHW
WHW,
Don't take my comments as not endorsing staple-up. I wasn't discounting staple-up. I wasn't even discounting staple-up without plates.
What I was discounting was the idea of hanging the PEX in the bay...either from the subfloor or the sides of the joists...and then capping the BOTTOM of the joists with rigid insulation, resulting in the entire jost bay (all 9.25" or whatever) being heated. That, to me, is not a viable solution. Essentially the same materials and labor for both options, but with the 1.5" airspace being more efficient than the 9" airspace...as well as leaving useable room in the bays for mechanicals.
Comparing that to a "standard staple-up" which only uses the upper 2-3" of a joist bay for heating and allows the rest of the bay to be used for mechanicals.
I do think that insulation is required under a staple-up. If you're going to insulate, you may as well tuck it up tight and only have a 1.5" airspace instead of a full joist depth air space.
Does that make sense, or did I mis-read your post by thinking you mis-read mine.<g>
Radiantly,
Mongo
Oops! I misread your post. Sorry 'bout that. We agree.
<g>
I like the foil faced application. About the same $/R, added reflective, and same or less labor time.
What do you do to insure tight fitting plates-to-subfloor and plates-to-pex?
As opposed to the somewhat dated (IMHO) method of just hanging the tubing in the joist space, insulating while providing air space, and running 180 degree water through there, counting mostly on the air heating the subfloor>.
This is no the preferred method of doing RFH. But is is not outdated. Nor do you need to use 180 degree water. Just for your info.
I know you don't need to use 180 degree water, but isn't there greater chance of mis-design with open joist space so that you're more likely to need hotter water to handle the heat loss with an air transfer system??
Or, given the fact he's already set up with a high temp boiler, could he concievably save time and money by eliminating the plates and insulating the air space, and not worring about a mixing valve?
WHW...our messages crossed, but it looks like we're on the same track.
TIA to both you and Mongo.
Edited 9/29/2003 5:04:33 PM ET by johnnyd
I don't know about dated, but it has never been good to simply hang the tubing in the airspace. RFH is best laid in a thermal mass such as concrete or gypcrete.
The foil serves as a convector to transfer heat to the bottom of the subfloor. If not tightly insulated, it will also serve as a radiant surface to send btu's into the air.
I would not think of installing it in a wood frame without the foil and the insulation. I have used both fibreglas and foil faced foam. I prefer the later.
Excellence is its own reward!
Edited 9/29/2003 10:23:21 PM ET by piffin
FWIT, this from
http://www.rpa-info.com/forums/forumdisplay.cgi?action=topics&forum=Public+Bulletin+Board&number=24
In 1999 Kansas State University did an ASHRAE study comparing the output of plates, no plates and insulation.
They found that with a fixed water temperature of 140°F, plates increased the heat transer over no plates by between 160% and 172% depending on where the insulation was placed.
KSU used foam board insulation instead of fiberglass batts so the insulation could not be pushed flush to the underside of the subfloor and resulted in an air gap the thickness of the tubing.
They found that with a 2-inch gap, the plates put out 42 Btu/hr•sqft, while with a 5/8-inch gap, the output increased to 46.3 Btu/hr•sqft.
The opposite was true for no plates. With a 5/8-inch air gap the output was 23.5 Btu/hr•sqft, while with a 2-inch air gap the output increased to 26.2 Btu/hr•sqft.
A report on this study can be found in the July 2002 issue of the Radiant Panel Report