I am looking to install a plain concrete floor in a small kitchen (approx 10’x8′). Ceramic tile ares currently in place. There is a 1/4″ difference between hardwood floors and the tile floor, the hardwood being higher. Is anyone aware of a product that would allow me to just skim coat over the ceramic tile (Any experience with Ardex products). Would I have to remove tile or can I surface right over it. Any suggestions on products and installation information would be appreciated. Also if you do this type of work and are in the Norwalk, CT area, I would love your contact information |
Discussion Forum
Discussion Forum
Up Next
Video Shorts
Featured Story
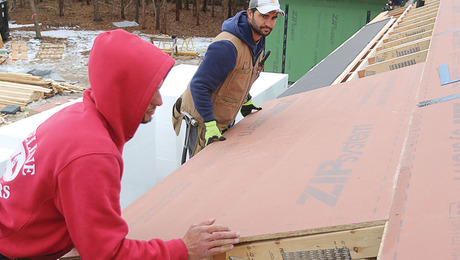
Learn about solutions and fastening methods to prevent truss uplift issues.
Highlights
"I have learned so much thanks to the searchable articles on the FHB website. I can confidently say that I expect to be a life-long subscriber." - M.K.
Replies
Are you asking if there is any way to put 1/4" of concrete over the tile?
What kind of tile?
What is underneath the tile?
Ardex is a product in the catagory of "self-leveling cement topping". In theory, it woiuld be the correect product. The things to be cautios of are flex in thefloor that would crack the ardex, loose tiles or grout, getting a smooth finish. Did you read the mfgr instructions to see if they allow topping of tile?
"When asked if you can do something, tell'em "Why certainly I can", then get busy and find a way to do it." T. Roosevelt
Are you asking if there is any way to put 1/4" of concrete over the tile?
Yes... and if there is a way, what product to use. It won't be stained... I'm looking for the loft feel.
What kind of tile?
12" ceramic tiles with 1/2 grout
What is underneath the tile?
Subfloor... At 220lbs I can give a mild jump and don't feel give.
The things to be cautios of are flex in thefloor that would crack the ardex, loose tiles or grout, getting a smooth finish. Did you read the mfgr instructions to see if they allow topping of tile?Did you read the mfgr instructions to see if they allow topping of tile?
It appears that you are able to install over tile, however, I have no experience with concrete in this application (well, very little experience with concrete in general, short of a curb and for wood decks).
My concern is that it would make an solid bond. Ardex initially sounded like it might be the right material for the job as it appears to have a high PSI rating and will bond to ceramic tile...
The floor appears to be structurally sound with tiles and grout still in good shape. As for getting a smooth finish, any suggestions?
Ardex Info:
Smooth, dense and solid substrates such as burnished concrete, ceramic and quarry tile, natural stone, cementitious and epoxy terrazzo, and solidly bonded epoxy coatings can be smoothed with an ARDEX underlayment prior to the installation of new flooring. The surface of these substrates must be clean and free of all contaminants including oil, grease, wax, etc. Due to the non-porous character of these substrates, sealers, dressing and surface treatments can often be completely removed effectively using professional stripping agents. As an alternative and where stripping is not a sufficient technique, mechanically cleaning of all of the above non-porous substrates can be used to remove all foreign matter.
Please note that all hard surface tile substrates must be thoroughly evaluated for the bond of the individual tiles. All tiles which are not solidly bonded must be completely removed, to include the setting mortar, down to clean, sound, solid concrete.
I'm with Dinosaur on this one. I think you would be pushing your luck.
What's the correct way of approaching it. Remove the tile and lay it over the subfloor? I'd like to keep it level with the hardwood flooring entering the kitch (3/4").... or should I be looking at a different material with a similar look?
I'd definitely remove the tile. I'm with Dino, for sure you need a shear plane. I think you are better off with a double layer of grade-D paper, but that's a pretty minor point.I bet if you let Dino and IMERC hash this out a little longer you will get your answer.
I wanna know what the finish elev to the sub floor measure is... Life is not a journey to the grave with the intention of arriving safely in a pretty and well preserved body, but rather to skid in broadside, thoroughly used up, totally worn out, and loudly proclaiming<!----><!----><!---->
WOW!!! What a Ride!Forget the primal scream, just ROAR!!!
<<I wanna know what the finish elev to the sub floor measure is... >>I'm getting the impression that it's 3/4", the OP should jump in here.I understand your concern about the lathe, and don't necessarily disagree. I've used Finishcrete to successfully fix some pretty bad concrete slab F-ups, but I'm not familiar with any of these products you've desribed, so after this point my opinion isn't worth much. From here on out I'll be learning too.
Ideally it would be 3/4" to be flush with an adjoining hardwood floor… I suppose a 1-1/4” would be ok, but I wouldn’t want to anymore than that.
I'm getting the impression that this is an ill advised idea, even with the removal of the tile. ? .
there is an answer for what you are trying to do....
WTB the tile has to go though...Life is not a journey to the grave with the intention of arriving safely in a pretty and well preserved body, but rather to skid in broadside, thoroughly used up, totally worn out, and loudly proclaiming<!----><!----><!---->
WOW!!! What a Ride!Forget the primal scream, just ROAR!!!
This guy uses polymer (concrete) overlays to so that he can do decorative concrete finishes on it.I don't remember the details, but they some where real thin. Brands where mentioned in the article.http://www.jlconline.com/cgi-bin/jlconline.storefront/45c0163d0016172d27177f0000010534/Product/View/0402deco
.
.
A-holes. Hey every group has to have one. And I have been elected to be the one. I should make that my tagline.
Try: http://www.miracote.com
Check out their Miracote Repair mortar II. Then the Miracote Protective Coating. I'm thinking you could do what you want from these.
This sounds like a bad idea. There is just too much that could go wrong with it. The SLC could crack due to flexing, expansion, or vibration. It could delaminate from the tile surface. The likelihood of you getting a good job out of this strikes me as very, very low.
Bite the bullet, Craig. Strip the tiles and do it right. Although why you'd want a plain concrete floor in a kitchen, I can't quite figure out....
Dinosaur
How now, Mighty Sauron, that thou art not brought
low by this? For thine evil pales before that which
foolish men call Justice....
This is the closest picture I could find. Its a loft style apartment, I built maple cabinets and have a black solid surface counter...
http://www.taunton.com/finehomebuilding/media/h00038_02.jpg
Wouldn't do it in a house, but I think it will look good in an apt. Just don't want to mess it up after all the time in the rest of the project...
Wouldn't do it in a house, but I think it will look good in an apt
Well, chacun à son goût, as we say up here. But it's hard on the dishes when you drop 'em. Which is another thought; if you do manage to get a ¼" of some sort of concrete to stick to your tile floor, dropping a heavy skillet on it (and it happens) could easily crack it badly.
If you really want that look, strip the tiles down to the subfloor, seal the subfloor and perimeter with 15# felt; screw down a screen of diamond lathe on top of that as reinforcement and bonding element; then pour, float, and finish a real concrete floor a full Âľ" thick.
You will be well advised to hire a professional concrete floor finisher to do the pour and float if you want it to come out looking half-decent. Otherwise, it'll likely look like a driveway.Dinosaur
How now, Mighty Sauron, that thou art not broughtlow by this? For thine evil pales before that whichfoolish men call Justice....
why the lath???
just do light weight...Life is not a journey to the grave with the intention of arriving safely in a pretty and well preserved body, but rather to skid in broadside, thoroughly used up, totally worn out, and loudly proclaiming<!----><!----><!---->
WOW!!! What a Ride!Forget the primal scream, just ROAR!!!
The felt will act as a waterproof membrane and bond breaker, kinda like a Kerdi or Ditra, but a lot cheaper. But if you also screw down metal lath over spacers so it floats, say, a quarter inch off the floor before the pour, it'll act like a mini reinforcement grid in the slab and hold the slab in place without bonding it to the floor so unequal expansion of the subfloor-and-slab combination won't crack it.Dinosaur
How now, Mighty Sauron, that thou art not broughtlow by this? For thine evil pales before that whichfoolish men call Justice....
light weight is intended for this type of application and comes fibered...
lath can leave air pockets and after walking it before and during the pour...
so much for floating the lath....
no argument with the felt...Life is not a journey to the grave with the intention of arriving safely in a pretty and well preserved body, but rather to skid in broadside, thoroughly used up, totally worn out, and loudly proclaiming<!----><!----><!---->
WOW!!! What a Ride!Forget the primal scream, just ROAR!!!
I guess you'd have to be real careful to work all the air out of the concrete while floating it. On something that thin, I'd use knee boards, though, instead of walking in it.
I've never used this 'light-weight' stuff you're talking about. Tell me more. Are we talking chopped glass fibre and polystyrene?Dinosaur
How now, Mighty Sauron, that thou art not broughtlow by this? For thine evil pales before that whichfoolish men call Justice....
some times it's called nailable but it is very similar to gypcrete...
lots of use in commercial bldgs for the floors.....
spec yur own fiber.... no poly...
I meant stepping on the lath.. that will turn it into a nightmare.. it will develop high / low spots and voids... Life is not a journey to the grave with the intention of arriving safely in a pretty and well preserved body, but rather to skid in broadside, thoroughly used up, totally worn out, and loudly proclaiming<!----><!----><!---->
WOW!!! What a Ride!Forget the primal scream, just ROAR!!!
What about diamond (expanded metal) lathe? Maybe a low-rib?I've seen some pretty nice surfaces done that way. The low-rib expanded metal stays in palce fairly well. Seems like if a guy used a fairly fat mixture and substituted some acrylic and anti-hydro for some of the water . . .
I think any lath in any type of CC that thin is asking for a redo...
and yes.. pull the tile...Life is not a journey to the grave with the intention of arriving safely in a pretty and well preserved body, but rather to skid in broadside, thoroughly used up, totally worn out, and loudly proclaiming<!----><!----><!---->
WOW!!! What a Ride!Forget the primal scream, just ROAR!!!
Humor me and look at this link.:
http://www.miracote.com/download/Tab%209%20-%20Miracote%20Data%20Sheets/Miraflex%20II%20Decking%20System%20Code%20MIR%20120.pdf
This ends up being about 3/4" thick. Note the testing results in the right hand column. The repair mortar core is troweled into the metal lath and has a similar consistency as a thinset. It must be mixed with it's part B (a milky white liquid) in exact proportions. Same with the MPC. Each has it's own liquid. The MPC is also commonly used for stamping projects.
I'm doing a deck at my kid's with this setup. He's on the west side of Michigan. When the weather breaks in April or May, I'll finish it up and take some pic's.
I just bookmarked that page. Thank you!
Excellent.... thanks
3/4" is all the coating thickness is???
I tried to find the "official" installation instructions but couldn't...
now I gots the need to know more...Life is not a journey to the grave with the intention of arriving safely in a pretty and well preserved body, but rather to skid in broadside, thoroughly used up, totally worn out, and loudly proclaiming<!----><!----><!---->
WOW!!! What a Ride!Forget the primal scream, just ROAR!!!
This is the procedure for wood applications. Another procedure is used for concrete substrates.
1. On a plywood substrate (ext. ply, at least 5/8"), expanded wire lath (ASTM C847) is laid using #16 1" wide crown, 1/2" long leg staples (ASTM F1667) spaced 22 to 28 per sq. ft.
2. Primer (Miracote liquid catalyst, diluted 1:1 with clean H2O) is sprayed (Hudson sprayer) at the rate of 400 sq/ft per gallon.
3. Miracote Repair Mortar III (1 gal of RM III liquid mixed with 40 lbs bag of RM III powder) is hand troweled into the lath 1/4" thick. (58 gallons and bags per 1000 sq ft)
4. (Optional step, depending upon aging of the RMIII.) Membrane A (I believe similar to McDesign's Seal-o-Flex) diluted 1:1 with H2O is dipped and rolled at the rate of 1 gal per 400 sq ft.
5. 1st Membrane coat. Using a notched squeege and backrolled, Membrane A is applied at the rate of 64 sq ft per gal.
6. 2nd Membrane coat. Same as the first.
7. 1st coat of Protective Cementitious Coating. Miracote Protective Coating (1 gal of MPC catalyst mixed well with 50 lbs of MPC powder) is hand troweled at the rate of 225 sq ft, or about 40 to 45 mils thick. This can be colored as desired.
8. 2nd coat of MPC. Same as the first. Hand troweled or screed
(Some examples I've seen can be made to look like ceramic tile - saw cut and back grouted.)
These next two steps are dependent upon the look desired.
9a. 1st coat of pigmented topcoat. Miracote Colorbond (a pigmented or clear epoxy topcoat) is either dip and rolled, or sprayed using a airless type sprayer at 300 sq ft per gal.
10a. 2nd coat of pigmented topcoat. Same as the first.
(Back to the original procedure - included with either method.)
9. 1st coat of Clear Sealer. Either HD II Lacquer (an acrylic resin in a solvent base) or Miraseal (an acrylic copolymer in a aqueous base) is sprayed with the Hudson and backrolled at 400 sq ft per gal. Avoid puddling and don't exceed the recommended thickness.
10. 2nd coat of Clear Sealer. Same as the first.
Basically, these components can be tinted as desired and within the recommended application rates, textured as needed.
Or, consider this to be an art project, using these components as your creativity allows.
Proper flashing is assumed. The underlying substrate MUST be stable and pitched at least 1/4" per foot. Although at least the 5/8" ex. ply is required, one can go thicker, use something like Advantex, or first lay with felt or EDPM. Reseal at least every three years.
Obviously this is a higher end product. My poker buddy's new $2.5MM monstrosity has such surfacing off his 3 decks.
I'm led to believe pricing for this comes in about $2.65 per sq ft. Materials only. I'm also led to believe if installed, it gets billed north of $10 per ft.
thanks again..Life is not a journey to the grave with the intention of arriving safely in a pretty and well preserved body, but rather to skid in broadside, thoroughly used up, totally worn out, and loudly proclaiming<!----><!----><!---->
WOW!!! What a Ride!Forget the primal scream, just ROAR!!!
I was talking about using the diamond ('expanded') metal lathe catskinner mentioned. Same stuff we use for stucco...or wrapping around trees to foil hungry beavers, LOL. Stuff comes in 2' x 8' pieces, and is designed so the rough-coat of stucco can penetrate it without problems. That being the case, I can't see why concrete wouldn't go through nice enough as long as you used a fine aggregate.
And yeah, we agree no walking on the lathe. Knee-boards all the way. I'd use doubled up washers to space the lathe off the floor when screwing it down.
Dinosaur
How now, Mighty Sauron, that thou art not broughtlow by this? For thine evil pales before that whichfoolish men call Justice....