I’m getting ready to pour a 6ft x 25ft concrete walkway/slab. The slab will be 4″ thick, although after my last compation it gets 5″ in some areas. I was planning on having a 4000 psi mix delivered. Are fibers worth the small extra cost? What’s your thought on the use of wire mesh, is it nesessary or just an added expense with little benefit?
Discussion Forum
Discussion Forum
Up Next
Video Shorts
Featured Story
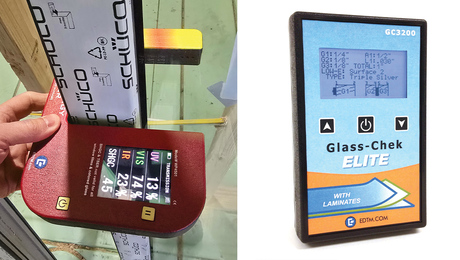
New devices showcased at the Builders' Show make it easy to measure glass performance, u-factor, SHGC, window thickness, and more.
Featured Video
How to Install Cable Rail Around Wood-Post CornersHighlights
"I have learned so much thanks to the searchable articles on the FHB website. I can confidently say that I expect to be a life-long subscriber." - M.K.
Fine Homebuilding Magazine
- Home Group
- Antique Trader
- Arts & Crafts Homes
- Bank Note Reporter
- Cabin Life
- Cuisine at Home
- Fine Gardening
- Fine Woodworking
- Green Building Advisor
- Garden Gate
- Horticulture
- Keep Craft Alive
- Log Home Living
- Military Trader/Vehicles
- Numismatic News
- Numismaster
- Old Cars Weekly
- Old House Journal
- Period Homes
- Popular Woodworking
- Script
- ShopNotes
- Sports Collectors Digest
- Threads
- Timber Home Living
- Traditional Building
- Woodsmith
- World Coin News
- Writer's Digest
Replies
The wwf (welded wire fabric) is what you want for a slab because it provides strength after curing that will be non-existent with the fiber.
Fiber serves to reduce cracking during the curing process, but really doesn't do anything for you after the concrete has cured.
You may see some cracking no matter what you do on a slab of that size, but with the wire and some control joints, the cracking will be isolated mostly to the joints if your base is well compacted.
You can also step up to a rebar mat, but since it sounds as though your slab will get only foot traffic, the wire should suffice.
The only time I've used fiber mesh was when constructing holding tanks for livestock water or industrial chemical holding tanks when, in conjunction with reinforcing steel, the fiber minimizes micro cracks during curing.
I also don't care for fiber in a slab that is to be nicely finished because the fibers provide an annoying surface of fuzz that, while they'll eventually wear away, are a PITA to finish over.
Thanks for the reply. I was leaning toward using the wire welded fabric. In reading the article "Tips for pouring a concrete slab" in April/May 2008 Fine Homebuilding it mentions something to the effect of having a break in the welded wire fabric where there is a control joint so to let the concrete crack along the control joint. This was the first time I have heard of that, is that the correct way of laying the wire fabric? I thought you wanted the welded-wire fabric to be one continous piece.
If I were you, I would purchase the 6" X 6" reinforcing wire in 5' X 10' sheets: Much less troublesome than dealing with a roll, which is heavy and, sometimes a real PITA to get to lay flat.And then you can lay your mats end to end and leave a small gap where they meet, mark the OUTSIDE of your form so you can locate the right spot to strike your control joint after your concrete is in plate and floated (there is a tool for this....kind of like an edging tool, but with a formed "V" on the working surface).You can, instead of a control joint, just place a piece of 2" X or even 1" pressure treated lumber on edge at your joint locations with its top edge on grade with your forms to be a permanent isolator and a kind of basic design element.I personally prefer the tooled joint.As I recall, your width is 6' so I would thicken the edge next to the inside of the perimeter forms a couple inches to provide a bit more strength and stability.I am an Animal
Edited 5/7/2008 4:35 pm by Notchman
Concretes not my thing , but I grew up pouring slabs ( son of a mason). I remember claims that fiber could be used in place of steel. Now I never gave it much credence myself, but that seams to imply it does add tensile strength.
Am I hearing you right in that it adds little or nothing after the initial curing?
That's what I've read: That it's purpose is to "help prevent cracks from forming in the first place, but only while the concrete is settling in it's plastic state."The quote is from a concrete book I've had on a couple jobs and loaned to employees so I can't find the name of it...it's pretty trashed (I'm not sure why I still have it). But I've also seen that description in other concrete reinforcement literature.If you take one of those fibers, you can break it between thumb and fore-finger of each hand without much effort...about like a human hair.Now I'm talking about synthetic "fiber"...there is also shredded steel fiber, but it's spendy and rarely if ever used around residential work.I am an Animal
6' wide, 25' long, and a nominal 4" thick?
Given how thin it is, I'd put an expansion joint every 6.25'
I'd spec that with #3 @ 12"O.C.E.W. too--but I'm a huge pessimist on WWM on any thing but floor slabs over metal pan decks, too (and not so much there, either)
Fibre in the mix will help; you've already gone up to 4000 mix from 3000 (or the 2800 I occassionally see spec'ed). But, as already pointed out, fibre seems best with broom finish (or really, really good finishers).
Now, my actual first question is "on what?"
You could get dam-strength 8000psi concrete, and have that fail on an improperly made-up subgrade. Preperation and compaction are the important things--not 4x4WWM v 6x6WWM or none at all.
>> Given how thin it is, I'd put an expansion joint every 6.25' <<
OH - really....
With those dimensions, it's really more of a sidewalk than a slab. I'd get your finisher to cut it up every 6 ft and forget the reinforcing, just as I would if I poured a 6'x6' slab. Then again we don't get frost heave here.
Use both - the fibermesh is like $6-8 yard last time I looked.
Jeff
fiber doesnt work, nether does welded wire. pout about a eight in slab it be fine, dont waste your money on rebar, it not worth the money
You don't say, but have you removed all vegetation and all top soil?
Have you replaced with a sub-base as needed with CA-6 or similar and compacted it to .95 proctor?
Have you added a base of rock, 3/4" to 1", about as thick as your slab? 4" concrete slab will not support cars unless the base and sub-base are very good. 5" will support light vehicles with no load. 6" will take heavier vehicles with a good base and sub-base. and so on.
Some add sand at this point.
You also don't say but is your concrete outside or in? What is your percent of air entrainment? Probably about 6%? What is your water reducing and/or your super plasticizer?
Broom or trowel? If 4" thick 5' to 8' for your tooled joints.
Fibers work best on early plastic cracking. Either WWF or rebar will reduce later cracking if its keep in the correct location. Get chairs, zig-zags, dobie's etc. and keep the mesh or rebar in the right place. 90% of the wire mesh in sidewalks ends up on the bottom and does NOTHING to help limit cracks. Keep the mesh or rebar at least 2" off the bottom of the slab and at or below the middle of the slab. If your slab is thick enough (6" or thicker) keep the mesh at least 3" off the bottom. Do NOT walk on the mesh, do not use rolled mesh its to hard to keep flat.
Cure it, cure it, cure it. After brooming and a little setting cover with burlap and keep damp to slightly wet NOT flooded. Do not let it freeze or preferably not below 40 deg. If its going to get cool get blankets and cover it. Did I say keep it damp for about 1 month (28 days).
Finally coat with 1 coat Ashford Formula Sealer/Hardener.
There are 100's of different combinations of the above and many not listed that also work. But there as many or more that don't work.
We're bidding on a warehouse/factory with 180,000 Sq. Ft. of 8" and 10" concrete floors so we do floors among other things.
Hope this helps,
Jim
It good advice, but this is a 6 ft wide walkway- presumably from the curb to a front entrance. Do you really do that much prep and reinforcing when you pour the walkways around your houses?
Do you really do that much prep and reinforcing when you pour the walkways around your houses?
Locally, I try (perhaps not quite to that high a Proctor)
But, the soil around here is river silts and sediments which gets about 3" of rain per month (all at once in some months; 1/20 a day every day in others).
Any thing less than 12" of subgrade prep will get you a pretzel-twisted sidewalk in only a couple years.Occupational hazard of my occupation not being around (sorry Bubba)
I have a 6" sub-base of campactable gravel/road base, which I have compacted several times with a jumping jack. The average thickness of the walkway is 4.65". I took about 25 random measurements throughout the area and ranged from 4" to 5.5" with a majority of the measurements at 4.5".
The Ready mix company said all exterior concrete will be air entrained, I'm going to assume they know how much is needed for is climate. Aggreagate size, slump, etc I'm leaving in their hands also. I told them the application and they said they would mix and deliver what I need. All they wanted to know was: how much, the application, what psi mix, and delivery date/time
I was planning on using the welded wire fabric sheets, more economical than purchasing a roll for this small of a project.
The location of this walkway is along my house to provide access between the front and back of the property, foot traffic only.
I'm planning on a broom finish and was going to spray a sealer as soon as all finish work was done. Should I use wet burlap or plastic instead for curing?
Don't forget to support the wire with chairs.
What is wanted is not the will to believe, but the will to find out, which is the exact opposite. --Bertrand Russell
A lot of good advice there... You sound like a commercial concrete guy... A few questions and observations frequent residential concrete customer (had 35 yards placed yesterday - yea - I know - small peanuts....) :
>> Have you replaced with a sub-base as needed with CA-6 or similar and compacted it to .95 proctor? << CA-6 Must be a local designation for... what?? fines mixed with various size crushed stone up to 1.25" stone? Crushed stone grading is highly regional. Here it is all designated by the state DOT. Obviously NC DOT has nothing to do with Illinois - where you live - for example. Attached is a chart showing the stone products as we order them here.... prices are out of date though. I guess I could say he should use ABC....
>> You also don't say but is your concrete outside or in? What is your percent of air entrainment? Probably about 6%? What is your water reducing and/or your super plasticizer? << I've never known super to be used on a residential project... I once asked a concrete guy to use super on a driveway and he walked off the job right then and there, wouldn't't return my calls - he had already done a lot of work for me - I guess that was the last straw. 6% entrainment hu... I've tried to specify entrainment levels in the past and the batch plant operator tells me that they will determine what is appropiate for my project if I want them to warranty it...
Doing a proctor test is a bit of overkill for a sidewalk in front of someone's house IMO. The testing might cost the same as the concrete installation.... - or at the very least as much as the labor anyway... Maybe $175 for the field work and the same for the lab work. Typically, we have soil engineers test bases for structural slabs only... I guess an engineer/tech should be onsite to collect cylinders too... and have them busted later :-)
>> After brooming and a little setting cover with burlap and keep damp to slightly wet NOT flooded. << Why not flooded? Not that I do that anyway... just trying to learn something here.... Do you have trouble with the burlap staining the concrete's surface? Is there a special burlap for this application? I guess you have to keep the whole thing clean too during cure...
>> Did I say keep it damp for about 1 month (28 days). << No doubt - that is best practice, but how does that fit into a construction schedule? In many cases that would require the project to more or less stop for the duration...
I can see how all your points would pertain to a warehouse/factory with a 180,000 Sq. Ft. but a sidewalk in front of someone's house??? He did say he wanted to know how to keep it from cracking though....
Edited 5/8/2008 7:59 am ET by Matt
We used super-p at some of our house slabs - it greatly improves workability of 4,000 psi concrete without having to add water. By the way - NO water added at jobsite ;o)I would not use a sealer on exterior walkways
Jeff
Edited 5/8/2008 9:37 am ET by Jeff_Clarke
The guy I was talking about who walked off on me said "it makes it take off too quick". I think that was the last thing he said to me. That ended up being a 50 yard pour. May not be an issue with smaller pours (say 10 or 20 yards) or say with a 20 man crew... or maybe a crew with those ride-on helicopters (power trowel) - although I haven't seen either on residential. Not saying super-p or other water reducers are not used in residential, I'm just saying it's very uncommon here. Over the last few years I've probably hired out the placement of 4000 yards with several different subs.... No super-P... In some cases I was buying the concrete - I'm sure they would have tried to get me to buy it if they thought it would help... I haven't done any commercial jobs... actually I did one... it was a low-rent low-bid kind-a deal. What a night mare. Concrete was turn-key. Concrete truck drivers refused to tell me what the mix was. Didn't exactly give me the warm and fuzzies... That concrete/site/pavement sub was about the worst experiences of my life.... nasty work.... In the end, imagine a hot headed Irish guy, a grown up biker, an Iranian, and a few lawyers arguing over the job performance and payment... :-) Luckily the long handled tools were left in the trucks... I'll let you guess which one I was... :-)
Lawyer?
Not to slam anyone, but I'll take offence tha to that... I'd think you'd know me at least a little by now.... Maybe you forgot to add the smiley face?
I'm going with the hot-headed mick.
OK - the Mc was lost off the surname a few generations ago but you get the milkbones. :-)
Ahh, well it takes a hot-headed mick to know one!
I'll pass along the milkbones to my copilot if ya don't mind... 30 seconds ago I found my 7mo old. 75lb rottie standing in the middle of my pool table. For a dog that can't make it in and out of my truck without much debate, I was floored.
Shortly therafter, so was she.
So 4in will not support cars? I see that called out all the time. Usually, 4 in crushed stone then 4 in concrete 4,000.
I usally do not do concrete. Just frame but I pouring a barn floor and it is speced 4 and 4 with 4,000.
Thoughts?
So 4in will not support cars?
Sure it will--if the subgrade underneath it will.
1 1/2" of ashphalt on the right subgrade will hold entire parking lots--if you didn't penny-pinch the paving contractor that is.Occupational hazard of my occupation not being around (sorry Bubba)