Does anyone know if modular houses can be expected to retain their value as well as stick-built houses? My guess is “no,” but I’m wondering if it’s an established fact that modulars depreciate more than stick.
Discussion Forum
Discussion Forum
Up Next
Video Shorts
Featured Story
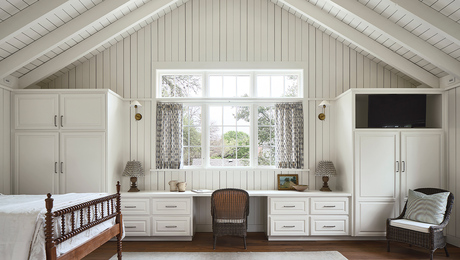
This 654-sq.-ft. ADU combines vaulted ceilings, reclaimed materials, and efficient design, offering a flexible guest suite and home office above a new garage.
Featured Video
SawStop's Portable Tablesaw is Bigger and Better Than BeforeHighlights
"I have learned so much thanks to the searchable articles on the FHB website. I can confidently say that I expect to be a life-long subscriber." - M.K.
Fine Homebuilding Magazine
- Home Group
- Antique Trader
- Arts & Crafts Homes
- Bank Note Reporter
- Cabin Life
- Cuisine at Home
- Fine Gardening
- Fine Woodworking
- Green Building Advisor
- Garden Gate
- Horticulture
- Keep Craft Alive
- Log Home Living
- Military Trader/Vehicles
- Numismatic News
- Numismaster
- Old Cars Weekly
- Old House Journal
- Period Homes
- Popular Woodworking
- Script
- ShopNotes
- Sports Collectors Digest
- Threads
- Timber Home Living
- Traditional Building
- Woodsmith
- World Coin News
- Writer's Digest
Replies
I suspect this varies a lot by location and the type of house you're talking about. You're probably better off asking a realtor from your area.
Around here, a cheap modular home (that's just a glorified mobile home) probably loses half it's value once you've moved into it.
A high quality custom modular is almost indistinguishable from a site built house.
Children need love, especially when they do not deserve it.
Just my experience, but everyone I know that's bought into a 'manufactured home' is stuck. It's easier to get financing, which is why they usually get into them. But, by the time you by the house, land, septic, well, foundation, ect. you've got so much money in it that you're upside down on the loan. Everyone I know that's had a house stick built in the same area could sell for a profit within a year.
We looked at some, but in everycase they weren't nearly as nice as the stickbuilt houses in the same price range.
I do know, that with manufactured homes, people pay close attention to how old it is. Doesn't seem to be much of an issue with stick built.
Just my personal beef: Every one I've ever had any experience with looks great. Everyone also has more corners cut building it then in all but the worst stick built house I've seen. It amazes me how they can squeeze pennies, and quality out of every single piece of the house. My folks just got out of one. I'm very grateful for that, as I don't get dragged into figuring out how to replace non-standard, junk plumbing and other parts anymore.
I wouldn't buy one, even the best built brands (one my folks had). I wouldn't recommend anyone I liked buy one.
In our area, modulars appreciate at about the same rate as stick-built; they're just worth less per sq. ft. We bought five acres w/ million-dollar views and a 1500 sq. ft. modular 8 years ago. The lot justifies a much nicer home. I've drawn the plans, but other projects (paying ones) call. But in those 8 years, it's appreciated close to 40%, 151K to 240K, and I'm not complaining.
I think this issue may totally depend on the area, though. We can look off in the distance and see a yurt on 3 acres, no central water. Saw it in the paper last week for $160K. Go figure.
Formerly BEMW at The High Desert Group LLC
Another issue that impacts modular cost over time is the finish. In the case of ours, which I intend to gut when I do the addition, leaving only the structure, the finish is cheesy as hell, but the structure is amazingly sound. 2x6 ext. walls with OSB glued and nailed inside and out. Likewise with the OSB in areas with vaulted ceilings. This thing doesn't creak the tiniest bit when it blows 60-70 over the ridge. Floors are 3/4" ply over 2x4x12" deep open trusses.
On the other hand, the trim and finish is fairly pathetic. Plastic parts in the door harware, pressed steel kitchen sink, stickum tiles in the bathrooms, etc. Those things alone could certainly drive down resale in some areas.
Formerly BEMW at The High Desert Group LLC
The two types of manufactured houses are:
(1) HUD Code Manufactured homes. They are built to the National HUD Code. Also know as single wides and double wides. They are lower quality than stick built homes and depreciate at a fast rate.
(2) Modular Manufactured homes. They are built to the same building code as site built homes. Often times they are built to higher standards than stick built as they have to withstand the stress of the trip from the factory to the site. Due to maximum section sizes there are some design limitations to modular homes. Other than that they are equal to site built homes. I have even seen modular homes with brick facades.
It gets confusing because doublewide HUD Code homes are often referred to as "Modular" by the public.
Can anyone tell me what the differences is between the HUD code and UBC or BOCA?? WHy would one thing be allowed on one code (like HUD) and not another??
thanks
Prior to 1976 there was no standard for manufactured homes. HUD in order to make singlewides and doublewides conform to minimum quality and safety standards developed a national building code for manufactured homes. Lenders will not lend on Single or doublewides built prior to the HUD Code going into affect in July of 1976.
The HUD code homes typically have cheap paneling on the walls with exposed seams. The HUD code homes typically have very low pitched roofs and no attic space. If you look in the crawlspace and see a metal chasis you have a HUD Code home. If you see wood floor joist the home is likely modular.
Many Manufacturers built both HUD Code homes and modular homes in the same factory. HUD code home cost about $30-$45 per square foot. Modular homes cost much more.
Interesting. Our first house was a modular home. We didn't know that until after we'd lived there a year or so and were told. It was brought in in two pieces, hooked together, then trusses were put on the roof, and a standard roof was framed over it. Never really knew what to call it, but if you didn't know, you'd assume it was site built.
I was thinking of the typical doublewide type house. Floors me how cheaply those things are built. Some friends just got stuck in one. The drawers are already falling apart. Big closets, one 12' long with one 8' wire shelf in it. Lots of problems with cracking. The cheap faucets may outlast the 2 year warrenty, but I wouldn't count on it. Every piece of hardware in that thing is cheap junk.
He realized he was stuck when the loan finally closed about 20% above what they verbally told him it'd be. He wasn't smart enough to get it in writing. Took them about 6 months to get the house set up so he could move in, then they raised the price to the max he could get a loan for. He tried to get out of it with a lawyer, but the papers he signed committed him, w/o locking a price down. Got the lawyer involved months too late to be of any use.
Have a friend that owns a plumbing supply store. Has what he calls his crappy contractor section. Cheapest things available. 100% plastic faucets, and other quality things. Says he sells them to manufactured home builders (usually for warrenty repairs), and contractors who don't care about their customers.