*
I’ve been on this site a short time,really enjoy the honest and open discussions here.I’ve never seen any talk about flor trusses on the threads here.I’ve used them extensively in the past 2 years,wondering if any of you are or have used them.
Discussion Forum
Discussion Forum
Up Next
Video Shorts
Featured Story
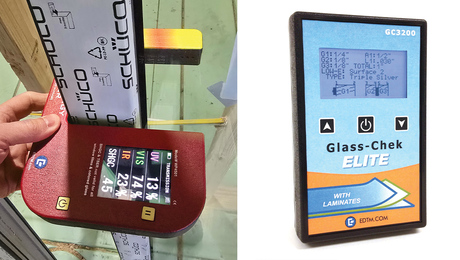
New devices showcased at the Builders' Show make it easy to measure glass performance, u-factor, SHGC, window thickness, and more.
Featured Video
How to Install Cable Rail Around Wood-Post CornersHighlights
"I have learned so much thanks to the searchable articles on the FHB website. I can confidently say that I expect to be a life-long subscriber." - M.K.
Fine Homebuilding Magazine
- Home Group
- Antique Trader
- Arts & Crafts Homes
- Bank Note Reporter
- Cabin Life
- Cuisine at Home
- Fine Gardening
- Fine Woodworking
- Green Building Advisor
- Garden Gate
- Horticulture
- Keep Craft Alive
- Log Home Living
- Military Trader/Vehicles
- Numismatic News
- Numismaster
- Old Cars Weekly
- Old House Journal
- Period Homes
- Popular Woodworking
- Script
- ShopNotes
- Sports Collectors Digest
- Threads
- Timber Home Living
- Traditional Building
- Woodsmith
- World Coin News
- Writer's Digest
Replies
*
A couple of well-written articles have appeared in FHB over the years devoted to open-web floor trusses, and I am fascinated by their many advantages over I-joists or dimensional lumber. Based on your experience, how do the costs compare between I-joists and floor trusses when built to the equivalent deflection ratings (let's say L/480 or better)? Is one method typically "bouncier" than the other (again, same deflection rating)? I've seen advertisements for the TrimJoist system, a combination of open-web floor truss and I-joist. Seems very interesting. Any comments on TrimJoist? Any recommendations on other manufacturers or types (for example, wood vs. metal webbing, etc.)?
*Floor trusses 101 - I really like floor trusses, but I guess /I'm kind of biased, having been in the truss business. First, the good things about trusses. They go down amazingly fast. They can be built deeper than I-joists for longer clear spans. They have plenty of room for wiring, plumbing, and possibly ductwork. Decking goes down easily due to the 3.5" nailing surface. Now, the bad stuff. They are more expensive to purchase than I-joists or conventional lumber. (Labor savings may offset this) You have to plan ahead to get them ordered and on the jobsite when you need them. Problems with getting the bearings and stair openings in the wrong place are common. You can't always get ductwork in the floor system without planning out your duct layout. (truss manufacturers won't automatically do this for you)People tend to want to close up the spacing of the floor system, and get very shallow trusses. This will make the floor bouncy. I can't think of anything else at the moment, and I have to get to work. If you have any specific questions, toss 'em out and we'll kick 'em around.
*Floor trusses suck! But you can achieve longer spans. I've found that the trussed systems are just as bouncy, or bouncier. That's probably due to the designers trying to keep costs down. Kinda like using 2x10's when 2x12's would be more appropriate. Ron Strohbeck says trusses are faster. I wholehearily disagree! The only time saving is the setting of the beam. If the trusses are 24" oc, there will be additional savings. All those savings are lost when the specialty fastners, headers, lacers, and edge treatments are considered. Cantilevers are a another nightmare. Concentrated loads that result in bearing spots are also very troublesome. And don't forget the firestopping headache. Around here, the fire people want to limit the "floor" plenum to be limited to 500 sq ft. On a large home, there will need to be several draftsops installed into the flooor system. Sometimes, it is relatively easy, and other times its a nightmare. And how about having to go back after the other trades hack away at the "unecessary" lacers that are always in their way!?Ok, lets talk about problems. What if you are one truss short (it's been known to happen). We were two trusses short on our last house, and had to wait 6 days for the parts to show up. It was in an area that had to be stood up first!What happens if you accidently get one in the way of a plumbing stool? Try headering a hacked up truss!Oops, the rookie cut the wrong end of the truss? Theres a huge mistake! Oh oh junior, you installed that truss upside down! Another hour added!What? The foundation wasn't perfect? We better re-engineer and re-order the entire section!Trusses are good owl savers, but are best suited to special situations. Unless of course, you don't mind adding 20% to your framing time, and having the builder ask you to reduce your bid because of all the time the lumber man said it would save!It takes 5% more time just to sift though the truss package and make sure you are getting the parts in the right place!I spent two hours on the last truss house, cantilevering the second floor wall 4" for brick. The 30' wall would normally take me 15 minutes to endblock it! You call that savings?Blue, anxious to set the record straight in MIPS I'll bet if the truss manufacturers had to install their own products, they'd re-design them to be more user friendly.
*Deflection ratings vary,depending on span,but most are rated from L/480-L/850.The last set I used was a 30'span,22"depth,with L/553 max live load deflection at center of truss.Lately,we have been using trusses designed and built by Littfin wood truss systems.As far as how they feel?I think they are solid as a rock.After installing them,they seem a little spongy,but when the lateral bracing is fastened tight and properly,this sponginess disappears. We always specify the trusses to be dropped below the top of the foundation by 3"-6",so that the house doesn't seem so high off the ground.In other words, the top of the truss ends up being 16" up from the top of the foundation.We also specify a 1 1/2"X3 1/2" notch in all outside ends of the truss.Here we install a continuous 2X4 ribbon board to tie it all together,and give the wall framing something more substantial to bear on.The initial cash outlay is more than any other floor joist,but the ease of installation,and other sub work after that justifies the expense.All electrical,plumbing,HVAC,etc. is so much easier to run through open webs.This lowers the subcontractors labor considerably.Also, in finished basements,there are no soffits to build to hide ductwork or plumbing.Also no bearing walls(usually),so the basement can be unlimited as far as finishing it off.I do like the idea of the TRIMJOIST system,I will be pursueing that in more detail for next few jobs.Ron, you are correct in placement of stairwell openings.We have had problems in this area,with occasional field adjustments,we have made them all workout.I also find it difficult to attach newel posts for stair railings to the trusses,since the flange is 3 1/2" wide, we have to do some thinking in this area to get the post down in the cavity for a solid anchor.We tend to use alot of adhesive on these trusses for subfloor since there is a 3 1/2" flange,which is alright with me.And if I can't hit 3 1/2" with the nailer then I better have someone else nail it off!!!Here is another advantage for trusses, you don't spend time pounding out and renailing the missed nails.I used the metal webbing once a couple of years ago,found it to be considerably more "bouncy" than wood.Well, gotta go,keep the feedback coming!
*No more coffee for blue. I think if i was building my own home, I would try them in a heart beat. Blue's problems seem valid, but I would think that there would be major advantages in not having subs cutting up dimensional lumber to fit in plumbing, mechanical etc. Sounds more like problems for the design end that got blue's panties in a knot.
*I'm sorry FredL,but you lost me on the decompartmentalize thing!"Every leak to the inside is directly connected to every leak to the outside",please explain. Blue, I agree that trusses are limited to a certain degree.As with roof trusses,there can be some jobsite framing required because of these limitations.However, I find that a well planned design and working with the truss manufacturer,we can usually work in these details before hand.I have had changes made in the plan after the trusses were delivered,Yes,it can be a pain trying to cantilever a bumpout that was not designed into the original plan(been there,done that).In my area,the people are real conservative,thus most our designs are simple 1 & 2 story houses.Not a lot of bumpouts or irregularities associated with high $$ move up units.As far as placement of fixtures,we try to compensate for this problem when it occurs by moving the wall as little as required so as not to have to cut the truss chord.
*Blue, most of the problems you bring up can easily be fixed by planning ahead, or maybe switching truss suppliers. If you were 2 trusses short on a house, and it took 6 days to get replacements, you definitely need to switch. I've made mistaked before - everybody does. But every truss plant I've worked for tried to correct their mistakes in 24 hours. You mentioned having a truss get in the way of a toilet flange. How is that different with trusses than with any other floor system ? Check your layout *before* you start setting the trusses, and you won't have this problem. You mention the foundation not being perfect. There are 2 ways I've dealt with this. Sometimes the contractor would order the floor trusses before the foundation was in, and tell his concrete guy it needed to be right on. Your sill plates may have to be held in or out a touch to get the dimensions you want, but it's doable. The other would be to have the truss company measure the foundation right after it's stripped, and build the trusses accordingly. This is safer, but can hold you up a bit. You also said "trussed systems are just as bouncy, or bouncier. That's probably due to the designers trying to keep costs down." That's simply not true. The cost of increasing the depth of trusses in minimal. Designers don't tend to make floor trusses any deeper than necessary because everyone seems to want a really shallow floor system. Until buyers/contractors start stressing stiffness instead of shallowness, this won't change. Actually, trusses can be cheaper when they're deeper. Let's say you want a 12" deep floor truss to span about 19'. Due to the high tension/compression forces, the top and bottom chord have to be #1 SYP. Increase the depth to 14", and the truss may work with #2 SYP chords, and be about $.10 per foot cheaper, and your floor would be stiffer. (I'm going from memory here, so I may be off a bit) Ask your truss supplier about it. Trusses aren't the answer to all your problems. But they can be beneficial if you plan ahead.
*Ron, you correctly point out several easy fixes to some of the issues, ie. plan ahead, use a different truss company, use deeper etc.Each solution delivers a new set of problems.I have encountered two plumbing problems in the last two years. In each case, the plumber notched into the floor structure. One was 2x10. The fix took 30 minutes. The other was a floor truss. I stil have not done the fix. The engineer required the entire truss to be lined with 3/4 " ply nailed 6" oc. Ok, great. One minor detail. There are two heat ducts running through the truss, one is a large square run, the other an oval. there are countless wires and pipes.The fix should have been the plumber to get the superintendent prior to cutting. We would have pulled all the nails and moved it! Our fix would have been a 2 hour work of art. The layout man did check to make sure the stool didn't land on a joist. Like you said, "Mistakes happen". Somehow he goofed! It happens, but it would hardly matter if 2x10's were used. That was my point.You also give many solutions for getting the foundations perfect. Again, good suggestion. Again, you are missing the point. With joist, there is no problem if the foundation is off by several inches. Usually we are cutting that much, or there is always a longer length at the lumber yard. With trusses, the bearing points are much more critical. A couple of inches either way can cause faliure. Quikly!Our truss company also promises one or two day delivery for problems. Try getting them to honor their promise in the heat of the season when they are already three weeks behind! IN my last case, I told the super, who called the lumber man, who called the truss supplier , who musta droppeed the message into his secretaries lap, who was on vacation, and her replacemnt was out to lunch and I had to wait 6 days!I'm not saying that trusses won't work, I'm just pointing out that I've never had to wait more than a day for joist errors. The last shortage was filled in two hours!You've correctly pointed out that most don't want the extra depth trusses. Thnk you.I did notice that you didn't comment on some of the other bothersome details associated with trusses. I know why too! They are a pain in the pocket book to overcome!I just thought of another detrimental attribute associated with trusses. Changes! Often the clients of the custom homes want to make changes that are often too complicated when trusses are involved. They simply aren't flexible enough in custom build operations. Around here, they (trusses) seem to be a Homeowner thing. Builders stick to the things that they know will make them a profit. It's a tough sell to those in the know, unless there is a real specific need for them.framin with dimension lumber till it runs out,Blue"Conserve toilet paper, use both sides."
*Jd. I'm just relaying some of the problems that I've encountered. Remember, I'm not trying to sell anything, I'm just giving you another side. I've lived the life, and know that 2x10's are easier.I'd also be willing to put my money where my mouth is. I'm not saying "don't use them", cause that's still a matter of opinion. Just don't preach to me how easy they are. I know better!Try to rectify the end bond framing with me. It can't be done! It took me a healty two hours, and I didn't think it was a well engineered deal at that! I followed the specs to the tee though.To point out the sustantial difference, I'll elaborate.In two hours, I can end block one end on a floor system. In two hours I can carry and stand up the entire back section of most houses that I frame (3000 sq ft =/-). I realize that floor trusses have some advantages, but ease in framing is not one of them! I'm putting in 2x 10's in mine. Cause I'm lazy!"Work is for people who don't know how to fish."
*blue,I'm a fan of sticks too, ....and Iwouldn't think of using trusses 80% of the time and the remaining 20% ofthe time I would do everything to avoid their use....Ithink of them as an option to solve real uniqueneeds of a design...so unique that they willbe worth the extra time and money and risk of delay, etc.Stick framing roofs too,Jack : ) )()ps- blue...starting to see into the 80/20 rule?
*FredL,Don't you insulate the perimeter of the floor cavities?With proper insulation and the sheathing overlapping the layers of a house,how can there be gaps for air to infiltrate in these floor cavities? Blue,Please explain the "end bond framing"and "end blocking a floor system"to me.We may be talking about two different things here.BTW,that must be why I work so much,because I hate to fish!!!!!!
*I'm starting to see the 80/20 thing.I agree with your truss usage. We had a need for them on the last house. They spanned 18' in the rear of the house. It was the great room. NO bearing points, no stairwell, no problem areas. They fit in nicely. It'a an isolated case wher not much can go wrong.One weird thing about these trusses. They require lateral bracing a 7' oc. the bracing must be 2x4. The bracing is required to be standing on edge . Why is it so important for lateral bracing to be installed on edge?We had to go back on a house with this particular type trusses and knock all the bracing loose, and re-fasten it standing on edge! We had installed it on the flat, but they wouldn't accept it. There was another 6 hr repair to add to my list of "Why I Hate Floor Trusses!" Blue
*Maj, there are several reasons that a floor would need to be end blocked.In the case that I'm describing, I had to cantilever the second floor out 4" for brick (the first floor is brick, and the second floor is siding: fairly typical around here). The 4" cantilever on the sidewalls (if the joist are running front to back) is a pretty straighforward thing with 2x10's. We simply install blocks between the rim (we call it a bond in Metro Detroit), and the first joist. The blocks are usually approximately 16" +/-, and are installed 16" oc, usually stacked over the studs.I can whack and stack an end bond in five minutes sometimes. It takes me that much time or more to sift through the truss specs to isolate the proper end joists 'cause they usually have several different sizes for specific things. And the spec sheets are horrendously organized. I have to flip through up to 50 pages to find the right item.With floor trusses however, it becomes a major thing. I had to fasten two floor trusses together (how does one join two floor trusses together in a way that makes sense?). I then had to install hangers @24" oc to receive shortened "jack" trusses. They were 36" (guess). I then had to attach the rim joist to the trusses. The trusses aren't perfect, and couldn't be held perfect to the double truss due to variations in the plates. The hanger nails are a hit and miss item, sometimes landing on plates, sometimes landing on air. To compensate, they have huge overkill hanger's spec'd that will guarantee nailing somewhere. The trouble is that inspectors require that every hole be filled. So here I am puttine 15 nails into a truss that is 36 " inches long, and the forces being transmitted is uplift!So, after nailing foolishly for about an hour, I still have to get the rim on and straight. Ever try taking a 1/4" off a 3 1/2" wide member while hanging by your gonads?You see, I'm not opposed to using trusses. Just don't send them to me if there are alot of offsets, floor height variations, any cantilevers, any bearing points, any possibility of changes, any possibility of foundation wall variations, concientious fire code inspections, if the builder uses plumbers who don't use common sense when a member is mistakenly in the way, if the homeowner is the changing type, etc, etc.I/ve used them without trouble on simple rectangular ranches that had clear spanned roof trusses. Although very heavy (we should have used a crane @$320 minimum), we managed to get them installed in a similar timeframe as 2x10's take us. ON second thought, the trusses take a little bit longer, but not enough to squalk (ripping the rim plywood, stairwells, etc.)!My history with these things goes back 23 years, and the problems remain the same!Blue
*Blue,Oh would it be nice if we could get twice theprice for the first time we build one of these architectural wonders...Jack : ) )(