*
I’m afraid it seems to be true. From what I have seen (albeit limited) many customers prefer fast and lower quality rather than having the crew take a little extra time to do it right. The place we’re at now the home owner is there all day, every day and when asked how he wants a particular thing done it is usually the quick and easy fix rather than the “right” way. Too bad. Of course there are those that want it right and only right but they seem in the minority. I don’t like it, but what to do? My 2 cents anyway.
Discussion Forum
Discussion Forum
Up Next
Video Shorts
Featured Story
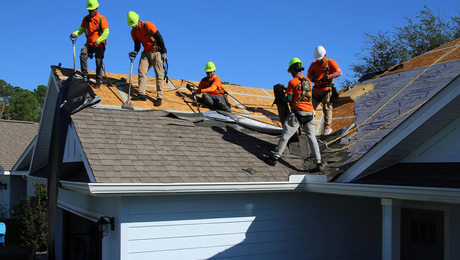
Listeners write in about haunted pipes and building-science tomes, and they ask questions about roof venting and roof leaks.
Featured Video
How to Install Cable Rail Around Wood-Post CornersHighlights
"I have learned so much thanks to the searchable articles on the FHB website. I can confidently say that I expect to be a life-long subscriber." - M.K.
Replies
*
Learn from the master, Henry Ford....Planned obsolecence....don't make it last forever...just until they want something different, then get the repeat business. Laugh WITH me.Keith
*
Tomorrow morning I have to have the tile setter tear out an entire shower side wall of 8x10 tile because the upper half of the back corner is set with 1/2 inch slivers. An error caused by an out of plumb back wall and compounded by not taking extra measurements of the depth of the shower after determining the plumbline for the front bullnose.
*Gacc, I don't trim, but if I was, I'd probably get it closer than 3/16" by eye with my makita framing saw.I'd probably have to start with a new blade.I've seen a lot of carpenters complaining about the others poor workmanship and 1/4" gaps. But when I look at those gaps they miraculously close up to 1/8 or less.Sometimes theres more bs going on in these forums than a dairy farm. But i really don't have any avrsion to puttying a less than perfect joint if it's going to be painted. The gap is no less annoying than nail holes, and I don't see you balancing the trim. Your putting tons of holes in it. Besides, look closely at some of your furniture. You'll be surprised to find out some of the joints are puttied too!sleeping well night after night,blue
*Very astute observation Keithc.! I questioned an old carpenter "Buck" once about a detail that wasn't quite right. He winked at me and said "y'all gotta leave something for your old age, son"!I guess he figured he'd be back repairing it in hiw twilight years.blue
*Ralph, it's not a compuound error. It's a simple basic layout error: no end piece should be less than 1/2 the size of your base unit. That is a very common error that is repeated thousands of times each day, in many different trades.blue
*
Well, back online after about a month or so, glad to be reading the threads again.
Arrived in Az finally to get a gig with a builder here (only until I get my own thing going again) to find out how these "Track Hacks" do things.
F'n pathetic! I've never seen so much pressboard and MDF in my life, it SUCKS! I now call it "MDB", (medium density bullshit). My first day on site was a joke, the foreman asked if I had a coping saw, reply "ahh...yea?, then he goes on to tell me that the base trim is coped in the houses we do, and do I understand the proccess? "ahhhm...Yea?" So he goes on to "show me" how the fine art of coping is done. Better could have been done with a chainsaw! 1/8th to 3/16ths gaps etc., and the answer to those delemas anyone?.....anyone? Riggghhht...CAULK! I just about crapped myself. I could see already what I was in for.
A week in, I found myself in a room where the drywallers had not run board to the floor, and we aint talking an inch short or so, this was a full width of the trim if not more in some places. I was shown that if the pin gun was held away from the wall far enough the nail is left about 1/2" or so out of the wall and will hold the trim out at the bottom and caulking wil fill the rest. I looked at my "instuctor" in total disbelief, and said "You've GOT to be kidding!". He further went on to explain how "Things like this are a test of a TRUE carpenter" and how "If houses were built straight, anyone could do what we do", just as matter of fact as he was standing there, like he accually believed that shit! (sorry folks, I get wound just thinking about how I've been doing things wrong all these years) and the hits just keep on commin'. The thing that is truly sad, is the fact that people are buying these sorry ass excuses for houses and paying good money for them, (min. price on ours are 250 and up).
The ONLY thing that keeps me there is the fact that its a payckeck RIGHT NOW and the minute I can find a good custom builder or get my own licencing/bonding done, I'M GONE!!!!
I know there are some very talented carpenters (real ones!) who read and submit to this site, so that group excluded, NOW HEAR THIS...Any of you folks who fall into the category described above, listen close.. YOU ARE NOT CARPENTERS, AT PRESENT RATE- YOU WILL NEVER BE CARPENTERS, and should UNDER NO CIRCUMSTANCES pass youself off as a carpenter. Go back to doing whatever it was you did before going to "Harrys school of Hack" and let people who know what the F*^# there doing, build sutable housing for people who deserve something done right for there hard earned dollar!!!
I went back to one house for pickup (punchlist stuff)and it looked like it snowed blue tape EVERYWHERE! Dont you people have any pride in what you do?
CSR
*Chris - Jeff Clarke "Quality cost-cutting" 5/26/00 7:19am>here is my response, already posted.Jeff
*Here we go again,This is one of the main reasons why I am in favor of carpenters being required to carry a licence.Any hack with a hammer can call himself a carpenter.Ed. Williams
*Chris, Stayed in a brand new hotel in Tuba City Arizona last month. That's just south of Monument Valley, Grand Canyon tourist area. Hampton Inn I think. Can't be a year old. On first entering the room I noticed the walls and ceiling done with some kind of huge hide everything splatter.I'm sure there was no need to fill the screws, one coat tape job probably hidden under it too. The corners were so out of square it made my eyes hurt. The high tech double pane low-e window had a major air leak from being tweaked into a diamond shaped opening. Joe H
*How the hell did the building industry ever get to this all time low. Don't the fools buying these homes have ANY clue what they are getting. If I were the one sinking 250K into a brand new home, I'd be there every day to make sure that EVERYTHING was done right to order. I feel bad enough leaving a tiny gap in framing let alone a canyon of a gap in finish work. What ever happened to the trade schools too, I sure am glad that I didn't go that route - "okay class today we are going to learn how to use a screwdriver, gaaffaaww". I can understand that they have a hard enough time with the kids that they get, but come on... if they don't want to learn, get the hell rid of them, period ended. It seems to me that the TRUE carpenters amongst us are becoming a rare breed. This is nothing short of a tragedy...
*Well Chris R., I'm certainly not going to be singing the blues because some carpenter showed me a creative and inovative way to "shim" out a piece of production trim. And I can't get too fired up because they caulk a gap closed either. Let's face it, theres a time for perfection and a time for production. If you know that a caulker is coming behind and treating all minor (yes 3/16" is minor) defects with caulking, take advantage of it and don't recut a piece that wouldn't meet a stain standard. It sounds like you have a hard time accepting that there is a different standard for the different types of trim.Well it's time you learned that there is!The idea of shimming with pins is a novel and widespread idea. I used to do it quite regularly with vinyl covered drywall and glue. Remember, glue will shim 3/8" and is a very effective shim if needed.I don't doubt that there might be some serious quality problems if you are working with a wham bam producion outfit but you haven't mentioned anything of substance yet. Wanna try again?Sidebar to Gacc Dallas. Why would you want to get the government involved on your business anymore than they already are? Let the buyer beware, and if shoddy workmanship occurs, the courts will allow damages. Licensing only keeps out hard working tradesmen that are intimidated by reams of paperwork and legal mumble jumble. I'd be in favor of licensing carpenters only if there was no paperwork involved. And that ain't gonna happen in a legal society governed by lawyers. blue
*The reason this quality of work exists is because it's what many (maybe most) homw owner's want.Given the choice between a small, quality built home or a cheap, shoddy McMansion for the same amount of money, the McMansions sell every time.
*The same piece of trash you are building for 250's today will sell for 300 in 5 years. It will look alot worse then than it does now and it will STILL go up in value. Every other market I know things of inferior quality go down in value the minute you buy it.....houses go up. Love this country or what?
*Yeah its sad but true. The most important thing I learned from my first spec house is that they sell these things by the sq.', not by the pound. You can spend more time and money building a better house but it will sell for the same as the pig with lipstick. Time will tell if there is a difference in appreciation.JonC
*I'm afraid it seems to be true. From what I have seen (albeit limited) many customers prefer fast and lower quality rather than having the crew take a little extra time to do it right. The place we're at now the home owner is there all day, every day and when asked how he wants a particular thing done it is usually the quick and easy fix rather than the "right" way. Too bad. Of course there are those that want it right and only right but they seem in the minority. I don't like it, but what to do? My 2 cents anyway.
*F'kn-A Bubba, you sing it! My sister lives in Phoenix and I have some friends in other parts out there, so I've seen what you are talking about. It makes me gag to look at it and I shudder just thinking about it. But, our boy blue down by the stream has a good point. We have become a commidity. Tell me, what's she gonna' do, spend her days in litigation seeking judgement against a builder who can't be found?Then again these guys are too sun-addled--no shit, you ever been to AZ 'tween May and November?--so maybe they deserve some sympathy, eh? b Faster, cheaper means more than you think.
*It is the same everywhere Chris. The consumer will put up with it, so the money rolls and the cycle continues. The real crime is the resources that get pi#sed away. Unfortunately building it right many times means it is not affordable. There are ten companies in my little neck of the woods quoting new construction homes prices at $85/ sq ft. I can't come close to that with the construction standards I have in place.Upshot- my higher quality nets me two or three homes a year while they build twenty.I'm comfortable with that...
*Never ever ever -rely- on the threat of a future lawsuit to keep a builder in line. Litigation costs a fortune, builders are talented at giving you hell and go broke all the time, etc. There are too many of them for class action. Suing doesn't work, don't even think about it unless it's too late to make another choice. That's why it's "caveat emptor" and not "just-sue-em-later". :-)What's a typical new home warranty -- one year? What competent incompetent builder can't string along legally naive owners of junk houses for one year? And those private home warranties are a joke (yes, we got one, and I didn't read it closely until we had a problem, duh -- $75 deductible?? no coverage for "obsolete equipment"??).There is a huge demand for NEW housing ('cause it doesn't have all those problems of old houses!), a mindless desire for more square footage, and little sophistication in an increasing materialistic culture. A great time to be a hack -- it's just a calculated risk to cut corners, and logical to do it unless your standards compel you to give more than you have to (which I commend!). Without pride, who cares whether people call you names? At the same time, don't give away your work -- if you can't get paid for it and can't get a different job, give 'em what they paid for. Fair enough.Now, shouldn't this topic be titled "TracT Hacks." What about pride in spelling?? :-)
*I don't blame the hacks. It's society that is willing to pay the big money for the quantity, and not quality. What I find frustrating is that your average Joe home owner wouldn't know craftsmanship if it hit him in the face. In face the only way the recognize poor work is when it actually falls apart. However, this same guy will spend countless hours researching whether to buy the Mercedes, or the BMW. The sad truth is they just done understand the importance of 'Fine home building' Perhaps this is because todays business world often has folks moving from one house to the next...My solution was to find the minority of folks who want craftsmanship at a fair price. Like I read hear before, if you my name on the work, you pay my price. If you want it cheaper, go find some hatchet to do it.
*My eyebrows really went up at CSR's original post of this thread. I'm not involved with home constuction but I cannot imagine that level of crudity is allowed to exist.I have a father and son team in rebuilding our kitchen and I am happy with their attention to detail and good humor as they work through the usual glitches that are a part of any remodel. I have produced a couple of custom trim pieces for them to solve fit problems. The last piece had to be made from rough white oak and - I kid you not - was within .010 in all dimensions. It would have been closer but the DeWalt planer is new and I need a bit more practice with it.How about a house made of furniture grade wood, dovetails and screws?
*Charles, I'll be happy to build you a house made of dovetails and screws. The problem is, unless you order it up that way, and are willing to pay for it, I'd lose my shirt in the transaction. I must admit, unfortunately, that I agree with everything said on this post. The people I run into are only interested in two things; the commodity price of square feet, and how it looks. They don't care about construction details, energy effeciency, or long-term quality. And the problem is rampant with some of the people I work with. I swear before god that the next coworker who says "it's fine, no one will notice" is going to wear a 25oz. hart framer in their forehead from now on. It's obviously time for me to go out on my own...
*Charles, how about a house carved from redwood? We still have a few good old reds that we can fell, and crve out your residence.It is easy to forget the two seperate functions of the wood that creates a house. The first is the rough. It is called rough because it only needs to be close, kinda like horshoes. The finish, hides the defects that are inherrent in the rough. A good board hanger, combined with a good trimmer can float over all the imperfections of a rough, even an awful rough. All too often idealists want the rough to be the finish. The worry when a rough door jamb is out of plumb by 1/4", or a stud is bowed.All needless worry.I really do feel sorry for all you perfectionists. I was once one too. My stomaches used to wrench at the site of imperfection, even in a rough stage. I still find myself thinking about it sometimes but have managed to learn to look at the total picture, AFTER IT IS FINISHED! I really don't care anymore if the joist are 16.5" o.c. some places and 15.5" oc in others. And I enjoy houses a lot more now.Roughing a house with furniture grade wood, dovetails and screws makes as much sense as finishing a coffee table with 2x4 legs, osb top and 16d cement coated sinkers.It's time to analyze each phase of the house building operation on it's own merits. Confusing the two functions and holding each to improper statards can only result in unhappiness (yours) and your resulting fixes will surely waste precious resources.save the owls.blue
*Blue-]Bravo!!
*Just teasing guys. I know enough about home construction to realise practical limits. In fact, from some of the things I have read here and on other threads I probably know more than some of the people you have worked with.However, I do have a serious question for you guys. Is it really impossible or just extremely difficult to get things right? No insult intended here but I am reading almost nothing but "almost", "fairly close", "1/4 out", "1/2 out", "pretty square", "sloppy", "loose", "caulk", "defect", "hide".Is it possible to do it the way you guys seem to want it? What would it take?
*A serious question deserves a serious reply, so here goes.Getting things right is often a matter of perception. For instance, if you were commissioned to install a window into an existing brick wall, within two inches from the inside corner, and found the entire house to be built on an unlevel foundation, with the resulting corners being square, but not plumb, would you put your window in square and paralell, or make it plumb? The results would be conflicting depending on what the interior drywallers did, and the exterior brickies did. Let's assume the standard m.o. The drywallers just banged the board tight and the brickies dropped a plumb line. If you installed your window plumb, level and square, it would look great from the outside. The lines in the brick would run paralell and everything would be hunky dori. But then compare that to the inside. The lines would be running out of parallel and look like the window was out of whack since the ceiling and corners would be square.It certainly would be a difficult choice, and many similar stiuations arise out there in the real world. We usually don't have the luxury of tearing down the house and starting over with a perfect foundation. And so we compromise.Building a house is not science. You can devise scientific methods, but somewhere, somehow, something will crop up, unless you are jackplaning all your lumber out of 4x material. Even then, you will be forced to use all of your artistic skills to finish your project in a reasonable time. And so, the tradesmen are forced to make on the fly decisions, that reflect the values and relalities that confront them as they try to earn a living. When I was young and idealistic, I often chose the perfectionist route. I was an aspiring artist that was proving that artists must starve to realize their dreams. Somewhere along the way, I woke up and learned to compormise. Indeed one tool maker complimented me as being the most "compromising guy he ever met" (I had just hung his island celing cabinets on a drop that was running at least 1 1/2" out of level in 6 feet.) His entire ceiling and soffit drop had been somehow created in an extremely out-of-level condition. The entire ceiling was t&g cedar and already finished, and I just happeded in there to install his cabinets. A lessor carpenter would have walked, but the master boogerer took over.He payed me that night in cold hard cash and that is a testament that it can be done.I'm still wondering if I was dreaming.Anyways, I'm a big proponent of getting the bearing points suported and making the exterior presentable. Never perfect, but always better looking than what you'd do.oh yeah, I like my new life where I have food on my shelves for my wife and kids.We also wear shoes now.Caulking where required, blue
*Blue:Thanks-the perfectionist in the rough part of me needed that! It's a tough habit to break though.
*I know what your going through Rick G. It is very hard to let some things go, yet imperative in the bigger schemes (remember the shrinking paycheck). I don't know any rougher that thinks "I'll just set this rim joist out of square a little to make it harder for the tile setter", but these things happen. And when you have to make the gut wrenching choice to leave something that you are not proud of, you hope the craftsmen that follow you are skilled enough to hide it and make the final project palatable.Keep your head up Rick. Perfectionists anon is meeting every night right here.blue
*I think what is trying to be said is that there is point of diminishing returns here.Yes, there are an awful lot of folks out there today, that should never have been allowed to buy and use tools, let alone charge people for using them. My thought is that these people are a disgrace to the trade.There are also a lot of tradesmen out there who are doing what needs to be done. By this I mean, provide the best quality work, but also realizing that sometimes the destination is more important than how we get there.Should every other joint be caulked... never by me. Should I spend a huge amount of time on a particular joint correcting for out of plumb or square, when a bit of caulk and paint will have the same outcome? Make the end result look good an move on.I think what is important is have the skill to do it as close to perfect as possible. This way the caulk may come out as infrequently as possible. But, sometimes it makes sense. Someone who uses a little at the right time is much different than someone who uses it every time, because they have not properly mastered the trade.Hopefully I haven't pissed too many people off.
*I have to admit I understand some of the problems you have to face when you follow another "craftsman" into a job. My house is not exactly a masterpiece of geometrical enlightenment.But...if you could start from bare ground, what would you do?
*I think to a certain extent we're also talking about degrees; it's one thing to have to caulk the trim where it meets the wall because the drywall is puffy; it's another when I see 2 cases of caulk being delivered along with the trim. The problem I think is really becoming bad is that I run into people who knowingly are providing shoddy workmanship and short-term quality, and don't care. The case in point is the deck builder I ran into today. He proudly points out that he can build a deck in one day; cut the holes, have them inspected, place the posts with powder concrete around it, backfill and go. Everything looks great this summer, but in five years, I'll be yanking that post out and replacing a deck (I do four or five a year). I know that I'm too new in this business and I'm sure that I'm going the perfectionist route that Blue is talking about. But I also know that in ten years, a large portion of what I do will be replacing OSB around windows under vinyl siding that wasn't protected, replacing decks with crappy posts, and redoing windows that have never worked. I'm just afraid we're doing ourselves a huge disservice, even if the customer doesn't realize it right now.If I were starting from bare ground it's simple; hire professionals. From the start, the excavators will make a level hole, the wall guys will make a square foundation, the framers will make a strong, solid frame, and the rest will continue. It's all in the people.
*just keep in mind that there is an ass for every horse...the tract house builders are delivering exactly what their customers want ... it's not what i want...i started out building homes. but somewhere in the late eighties .. houses became commodities and i was in the wrong market..now we remodel.. and we do additions and we'll build a house every couple of years for the customers who want our brand of quality and attention to detail..if i were building tract.. i'd hire my own version of blue..a guy i trained 15 years ago who went out on his own and now has one of the best framing crews in the state.. he didn't learn the framing business from me.. i'm way too slow for that ..but , here's the deal...bestyacanchagot..b (((you do the best you can with what you got....))))that 's an old portagee fishing term i learned in p'town, and when things went just right, they were b finest kind..and finest kind had a whole lot of different levels of quality..it might even have meant bringing in a stove-in boat... but hey, that better'n not commin back at all..if you got a widow on a budget.. you give her your best work FOR HER BUDGET...but the business comes first.. you got to stay in business to take care of your customers.. so you can take care of your family and yourself..it's a long journey trying to find the right mix that gives you satisfaction and reward... if you don't like the standards of tract home building...do something else..want to be a custom builder .. look twice .. they arn't doing a much better job than the tract builders..if you don't have good design.. a good customer with the appropriate budget.. and a good team of framers and finshers and subs.. it just ain't gonna happen..b but hey , whadda i no ?
*Right, the standards are different on every job.I'm a remodeler, no new construction so I don't get to decide on site conditions, I get what I get. I built a little sun room on a small, 70's rancher. Nice and clean but certainly not fancy. The addition was all paint grade, a little caulk, built partly level and partly parallel to the existing house. Worked fast, kept the price down. The customer's were thrilled. I look around and see some imperfections. Sometimes I really dwell on the two or three things that aren't exactly right. I could have done everything perfect, but the customers couldn't have afforded it and I would not have done the work. By compromising some quality (this was still built well and finished appropriately), We both won. I got the work and they were able to afford the addition.Now, I'm going to be building a sun room on a VERY NICE house this summer. The room will be all exposed timber (look) framing, t&G roof decking, triangular windows in the gables. Everything's going to be just right. This "room" isn't much more than a roof and screen windows. The price is nearly the same as the finished sunroom. Different quality, different prices, different needs but all appropriate.
*Blue,I hope you're not showing your true colors.3/16" gap in trim joinery will get you fired off my crew.Sounds like you got "hack" confused with what you call "production".You can't justify slip-shot work by giving it a fancy name.Give me a break........you don't really believe that do you?I expected more from you. Don't give me that usual crap that there is a time and place for everything; I understand that BUT...........there is never a place for a 3/16" gap in trim work.......unless you're a hack.Say it ain't so......Ed. Williams
*Hey Messi,You and Blue have spoken very wisely. Personally, this is why I like to do both trim work and build cabinetry. I find it very challenging to go into a not so perfectly built house and see what I can do to hide the imperfections with my trim work. Covering up the flaws and makeing things look right by applying my skills gives me great satisfaction. Lets face it; if homes were built perfect, there would be no challenge for me and anyone that could swing a hammer could probably trim one out without much difficulty.On the other hand, I also enjoy building custom cabinetry because this gives me my opportunity to be a perfectionist. Here I find it challenging to test myself as to how square I can make a cabinet carcase or door. Here My goal is to try and make as flawless a product as I possibly can, giving the customer the best craftsmanship and value for his dollar. To sum it up I guess that my situation gives me the best of both worlds.