*
I want to build a garage. I don’t know
if i should sub in this cement guy or not.He want’s to make a frost wall out of block instead of pouring one. Is this a common practice or is this just a bad idea?
Discussion Forum
Discussion Forum
Up Next
Video Shorts
Featured Story
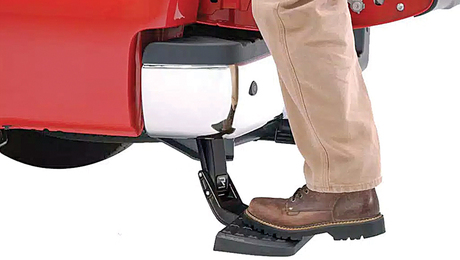
The RealTruck AMP Research Bedsteps give you easy access to your truck-bed storage.
Featured Video
SawStop's Portable Tablesaw is Bigger and Better Than BeforeHighlights
"I have learned so much thanks to the searchable articles on the FHB website. I can confidently say that I expect to be a life-long subscriber." - M.K.
Replies
*
Sounds like you are building your garage on conventional footings (vis a floating or monolithic turn-down slab). Depending on the depth of your footings and the height of your "frost walls" blocks may or may not be a good way to go. Anything less than four feet should be cheeper with blocks. With blocks you save the cost of forms. On a garage sized project block frost walls over four feet in height may still be cheeper than putting up forms. If you use "cut-away" "L" blocks for your top course you will also have the form for your slab. Run #4 rebar around the perimeter and vertically every four feet. Let the verticals run long and bend them over into the slab. If your wall is over three courses high (or two feet) consider laying a course of knock out web blocks in the center with a #4 rebar. When you place the slab let the concrete fill the block cores. As for your concrete man - no one here can tell you if he is any good or not. You can answer this for yourself by chaseing down the following: What is his local reputation? Can he give you references? Have you solicited competitive bids and if so, how does he stand on price and recommended approach? His approach does not sound out of line with practices in my area (NE Ark).
*
Thanks for the advice. I live in Vermont. I have checked with some of his refrences. I have yet to see a block wall frost wall. The garage is going to be directly conected to the main house. Any suggestions? thanks,
Roofer
*
Vermont. How far down do you normally put your footings? At one time, concrete forms were made on site by carpenters. Today, most formed up concrete foundations are placed using modular forms. These forms are rented by the general and set up by his crew or, more commonly, a specialized sub, who owns his own forms. The problem with your job is that it is too small to justify the fixed cost associated with getting and setting up forms. It may also be impossible to find a form sub right now with time to do a small job like yours. From a strength standpoint, blocks on properly reinforced footings will carry the weight of your garage and a second story. Block basement foundations do have a reputation for leaking. This should not be a problem with a backfilled garage. The fact that your new garage will be attached to your old house raises two concerns with me. The first is that all additions tend to settle a bit. The best insurance is adequate footings on well tamped or preferably undisturbed soil combined with fraiming that can float a bit in relationship to the house itself. The second is that your slab should be supported on all four sides by foundation. I would have the block mason lay up a wall or series of pilasters along the existing house foundation to carry this weight. Assuming you are going to pull a permit for this job I suggest a talk with your local building officials. If blocks are a problem they can tell you.
*
There is nothing wrong with block frost walls. I have put in hundreds of them. You will have the same problems with a poured wall if you don't make sure the footings are sitting on solid ground. Most poured walls don't have any support for the slab. With block, you can use 8" and then go to 6" with the last row or two to create a ledge. Unless you dig down and tie support blocks to the house footing, you will have settling of the slab at the house. The best way to handle this is to pour it a bit higher than the other walls and cut a control joint right in the middle. Slope the floor at least 2 1/2" in 12 feet. It will crack in the middle and form a straight drain line to the center of the slab. You should (NOT) tie concrete into the block cores. It will shrink as it dries and pull the blocks (and crack the block joints)
*
Block walls and poured walls are equivalent as a finished product, if both are properly built. The advantage of one over the other is basically one of materials logisitcs. Block walls require no forms and can be built with limited access to the back of the wall. The site must be accessable to a fork lift or other machinery or the blocks will have to be moved by hand. Concrete for poured walls can be pumped, which may be and advantage logistically.
*Roofer,I'm from the Pittsburgh, Pa. region. Most of our homes here have full size basements. These basement walls are composed of 8 inch block which in turn, sits on a concrete foundation ("footer").Homes and garages without basements are most commonly seen with frost walls built from block.They are built from block, not because block is better, but because it is cheeper. What G. LaLonde said about using 8 inch and 6 inch block for ledging is exacting the way it is done here too. Its a 100% acceptable practice here. But, it is not difficult to form a keyway into a concrete form so as to form this ledge either.Block walls must be parged with portland cement and then coated with tar or (better) wrapped with a waterproof membrane (not plastic), to keep groundwater from penetrating through the block's mortar joints. And yes, water will find its way into those joints! Most homes here have leaky basements. Blocks can't take much lateral strain, (only compressive) and so you must be careful when backfilling around the walls or you could lose one (collapse). Concrete is stronger, and I believe is the better way to go, but it certainly does cost more. The fact that you have'nt seen any block walls in your region should be telling you something. Have the job priced out both ways. If concrete frost walls is within your budget, I would opt that way instead.Davo
*
Be careful where the concrete floor rests on the blocks. Use the " L " blocks on top course as Steve mentioned, but consider not tying the floor to the blocks with rebar. Allow 1/2" expansion at this point. We even fill the block cores and lay down plastic so the concrete does not bond to blocks. The problem is sometimes,for whatever reasons, the top course of blocks will crack and lift slightly from the course below. Must be warping, stretching, or expansion of the slab. Don't know why and don't really care , but I've seen it happen many times. There is no reason to attach the slab to the foundation because the load is 100% straight down compression and the weight of the concrete is sufficient to hold it in place. Any comments on this method ?
*Steve and Dave: Steve--Concrete block walls do not leak anymore than poured walls.Both require the same "waterproofing". HOEVER We have used Dri-Blocks for five years with great success. These puppies have a latex additive as well as a mortar which is water repellent (not water proof). The mortar can be tricky. i.e. Grace Lab. If a customer has no intentions of finishing their basement we encourage them to save their money on further water treatment.We have had water standing three feet deep behind these walls with no leakage. Dave--poured walls are not any stronger than blocks walls. Purely "an old wives tale". Both types are unable to take significant lateral strain by themselves.The strength for both types comes from the proper placing, sizing and spacing of rebars. 94.203% of our work is repairing and replacing basement walls in eastern Nebraska where there is a lot of expansive clay soils. When we replace basement walls we install either poured, using ICFs or blocks. We are not partial. Both systems are heavily reinforced. In our area both types of walls that have not been properly reinforced crack.What the heck.
*I agree completely. This poured vs block wall topic has come up before, if someone wants to look back. I use both types of walls and can say that each type has certain advantages and disadvantages. Poured walls certainly aren't the answer to all problems. Personally, I have built 4 homes for myself and used block walls because they were much better for my particular situation. Both types cost about the same here, so it is not a matter of money. Every time I hear somebody say " There's nothing better than a poured wall" I cringe. I find it much easier to waterproof a block wall properly than to waterproof a poured wall. In addition they are much easier to finish because of the nice straight lines in every dimension. I could go on and on about the advantages of using block over poured walls. Maybe this topic will come up again..........
*
I want to build a garage. I don't know
if i should sub in this cement guy or not.He want's to make a frost wall out of block instead of pouring one. Is this a common practice or is this just a bad idea?
*
The method of building with concrete blocks I described in my earlier post is widely used here. I do not know of any problems with slabs pulling the blocks apart. The house I am building now has backfilled block "chain walls" and an integral slab. I looked at the joints yesterday and it all looks good. I note that with steel and concrete in the blocks an open joint will not compromise strength. With reguard to block foundations leaking, well it should not be an issue in a garage.